You are looking for information, articles, knowledge about the topic nail salons open on sunday near me how to removing broken exhaust manifold bolt from aluminum head on Google, you do not find the information you need! Here are the best content compiled and compiled by the Chewathai27.com team, along with other related topics such as: how to removing broken exhaust manifold bolt from aluminum head removing exhaust studs from aluminum head, cost to remove broken exhaust manifold bolt, welding broken exhaust manifold bolts, how to remove broken exhaust manifold bolts, 5.3 broken exhaust manifold bolts, how to remove ls exhaust manifold bolts, broken exhaust manifold bolt removal tool, driving with broken exhaust manifold bolts
Contents
Can you heat an aluminum head to remove bolt?
Heat the corroded bolt by placing the neutral flame of the oxy-acetylene torch 3 to 4 inches away from the head of the bolt. Aluminum will draw heat from the bolt, so you will need to heat the bolt longer than a standard carbon bolt.
How do you loosen seized aluminum threads?
While the bolt is in tension, sharply tap the head of the bolt once or twice with a small 4-oz ball-peen hammer. Then stop, and apply tension in the opposite direction and sharply tap with the hammer again. Reverse this procedure several times until the bolt begins to thread out.
At what temperature does aluminum soften?
Just like steel, aluminum alloys become weaker as the service temperature rises. But aluminum melts at only about 1,260 degrees, so it loses about half of its strength by the time it reaches 600 degrees.
How To Remove Broken & Rusted Stud Stuck In Aluminum (Thread Saver!) – YouTube
- Article author: www.youtube.com
- Reviews from users: 39520
Ratings
- Top rated: 3.4
- Lowest rated: 1
- Summary of article content: Articles about How To Remove Broken & Rusted Stud Stuck In Aluminum (Thread Saver!) – YouTube Updating …
- Most searched keywords: Whether you are looking for How To Remove Broken & Rusted Stud Stuck In Aluminum (Thread Saver!) – YouTube Updating Manifold studs break, and most extraction methods include drilling it out, and ruining the aluminum threads. Here’s a neat way to use a battery and a welder …broken bolt, broken stud, manifold stud, stud removal, stud extraction, easy out, head bolts, aluminum, stud in aluminum, broken manifold studs, broken steel bolt, engine stud, stud stuck in engine, exhaust stud, intake manifold, manifold bolt, stuck bolt, rusted bolts
- Table of Contents:
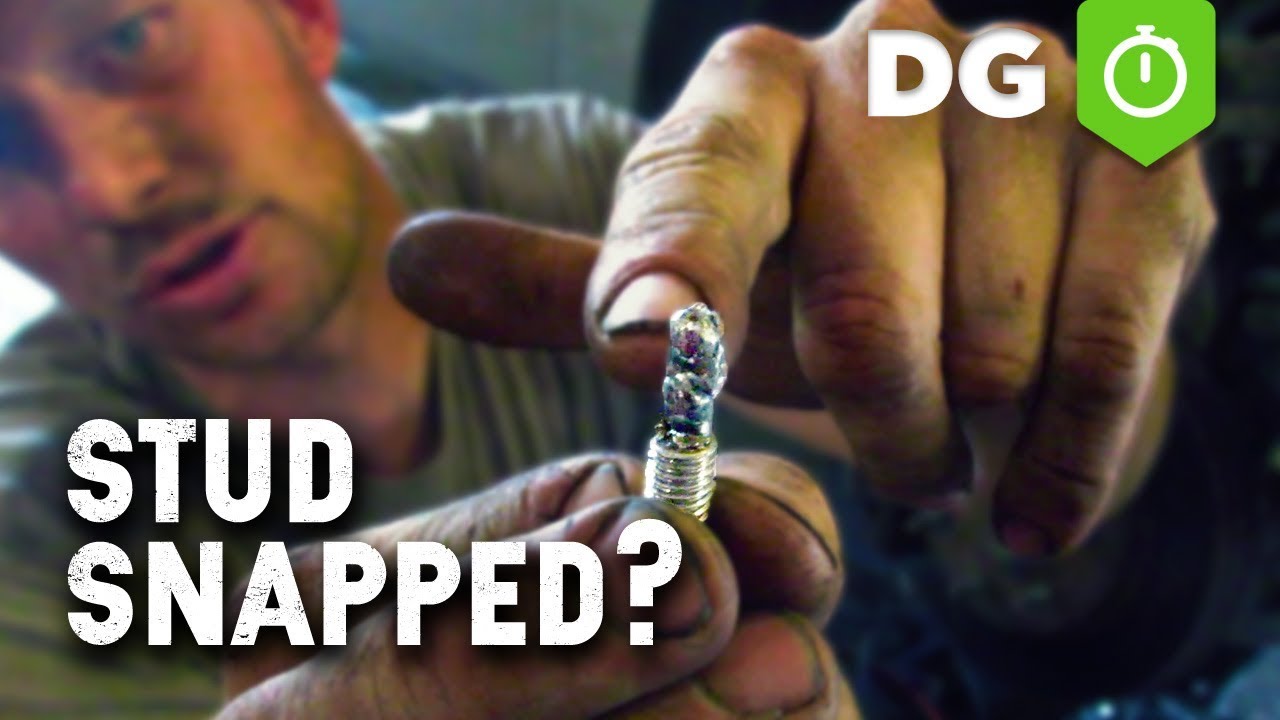
Remove a Broken Exhaust Manifold Bolt – EASY in 15 Minutes! No Disassembly! – YouTube
- Article author: www.youtube.com
- Reviews from users: 7910
Ratings
- Top rated: 4.8
- Lowest rated: 1
- Summary of article content: Articles about Remove a Broken Exhaust Manifold Bolt – EASY in 15 Minutes! No Disassembly! – YouTube Updating …
- Most searched keywords: Whether you are looking for Remove a Broken Exhaust Manifold Bolt – EASY in 15 Minutes! No Disassembly! – YouTube Updating This is a tutorial on how to remove a broken off exhaust bolt in a cylinder head without taking it off the engine! You do need to take the exhaust manifold o…Car, Repair, Tutorial, How, To, diy, 2carpros.com, Do, It, Yourself, broken stud out, not take head off
- Table of Contents:
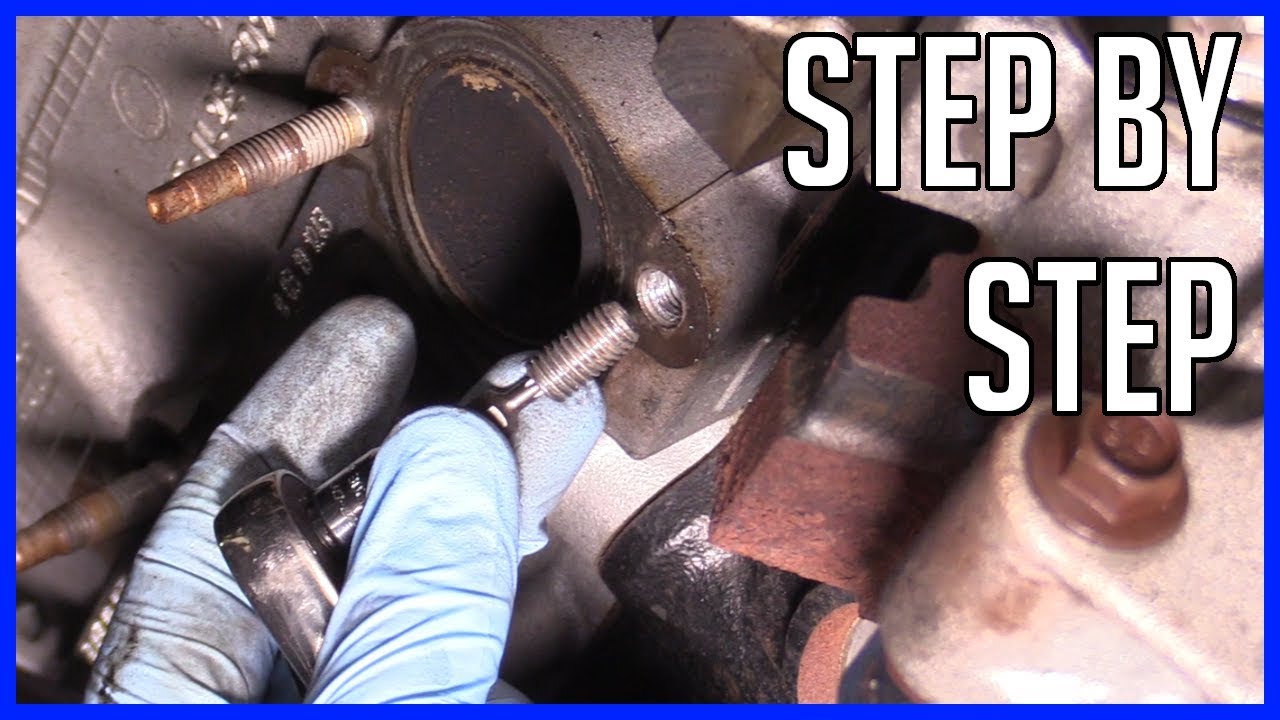
Horribly Stuck Bolt In Aluminum. – YouTube
- Article author: www.youtube.com
- Reviews from users: 36881
Ratings
- Top rated: 4.6
- Lowest rated: 1
- Summary of article content: Articles about Horribly Stuck Bolt In Aluminum. – YouTube Updating …
- Most searched keywords: Whether you are looking for Horribly Stuck Bolt In Aluminum. – YouTube Updating This was part of a suspension Job I did on this G6 where a bolt got stuck in aluminum and much worst than I thought it would be. I made this part a separate …bolt stuck in aluminum, steel bolt stuck in aluminum, stuck bolt removal, stuck bolt, crazed performance repair, automotive technician, mechanic, stuck bolts removal, stuck bolts on car, stuck bolt heat, stuck bolt removal tool, stuck nut, stuck nut on bolt, stuck nuts removal, stuck nut removal tool, stuck lug nut removal, stuck nut removal, how to, how to remove a broken bolt, automotive technician training
- Table of Contents:

How to Remove Corroded Bolts From Aluminum | eHow
- Article author: www.ehow.com
- Reviews from users: 26655
Ratings
- Top rated: 3.9
- Lowest rated: 1
- Summary of article content: Articles about How to Remove Corroded Bolts From Aluminum | eHow Updating …
- Most searched keywords: Whether you are looking for How to Remove Corroded Bolts From Aluminum | eHow Updating Even though aluminum does not rust, corrosion can still form between aluminum and a non-aluminum bolt. This is especially true of aluminum parts and stainless steel bolts subjected to saltwater. The saltwater causes electrolysis between the metals.
- Table of Contents:
Step 1
Step 2
Step 3
Step 4
Step 5
Step 6
Step 7
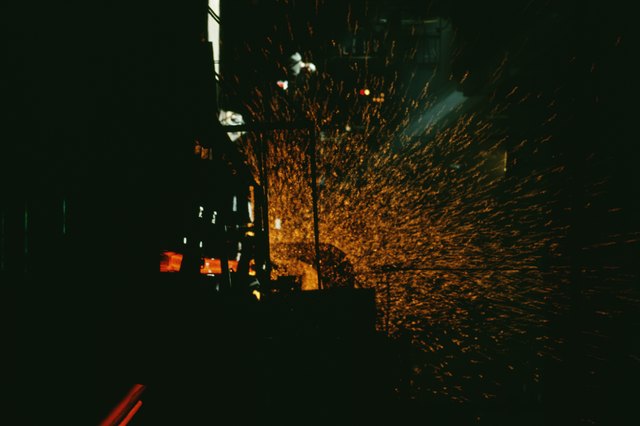
How would you remove a broken exhaust manifold from an aluminium cylinder head? | The Garage Journal
- Article author: www.garagejournal.com
- Reviews from users: 8855
Ratings
- Top rated: 4.6
- Lowest rated: 1
- Summary of article content: Articles about How would you remove a broken exhaust manifold from an aluminium cylinder head? | The Garage Journal Any part of it sticking out? Weld a nut onto it. The heat from welding will help to loosen it as the steel heats slower than the aluminum. …
- Most searched keywords: Whether you are looking for How would you remove a broken exhaust manifold from an aluminium cylinder head? | The Garage Journal Any part of it sticking out? Weld a nut onto it. The heat from welding will help to loosen it as the steel heats slower than the aluminum. Without removing the head, if possible. Broken bolt is not visible; nothing sticks out.
PLEASE READ THIS!! AN EXHAUST MANIFOLD BOLT SHOULD BE IN TITLE…
- Table of Contents:

Fixing Exhaust Leak from Broken Manifold Bolts
- Article author: www.motortrend.com
- Reviews from users: 32669
Ratings
- Top rated: 4.1
- Lowest rated: 1
- Summary of article content: Articles about Fixing Exhaust Leak from Broken Manifold Bolts Ideally, the stud or bolt will break with a bunch of shaft exposed that you can get a set of pliers on to spin it free. If not and it’s broken … …
- Most searched keywords: Whether you are looking for Fixing Exhaust Leak from Broken Manifold Bolts Ideally, the stud or bolt will break with a bunch of shaft exposed that you can get a set of pliers on to spin it free. If not and it’s broken … Exploring different ways to remove a broken exhaust manifold bolt and fix a leaking gasket on a Dodge, Ram, or Jeep Hemi.
- Table of Contents:
Why You Should Fix an Exhaust Leak
Getting Access to the Engine
Removing the Manifold
Extracting a Broken Bolt from Cylinder Head
New Exhaust Gaskets and Studs and Reassembly

Broken exhaust manifold bolt in aluminum head – LS1TECH – Camaro and Firebird Forum Discussion
- Article author: ls1tech.com
- Reviews from users: 34907
Ratings
- Top rated: 4.4
- Lowest rated: 1
- Summary of article content: Articles about Broken exhaust manifold bolt in aluminum head – LS1TECH – Camaro and Firebird Forum Discussion Since the motor is already out it should be pretty easy to remove the broken bolts from the heads. What I do is grind the portion of the bolt … …
- Most searched keywords: Whether you are looking for Broken exhaust manifold bolt in aluminum head – LS1TECH – Camaro and Firebird Forum Discussion Since the motor is already out it should be pretty easy to remove the broken bolts from the heads. What I do is grind the portion of the bolt … Broken,exhaust,manifold,bolt,aluminum,head,53, aluminum, bolt, broke, broken, exhaust, head, ls1, ls1tech, manifold, Broken exhaust manifold bolt in aluminum head, LS1Tech – Forum and Community for GM Performance Vehicles – LS1Generation III External Engine – Broken exhaust manifold bolt in aluminum head – I just bought a 5.3l with aluminum heads and it has the 2 outside bolts in one head ar broken off in head. My question is are they worth saving or are there better heads for the swap to buy relatively cheap?
- Table of Contents:

Broken off exhaust bolt in Aluminum LS heads: “RUST” them out?| Grassroots Motorsports forum |
- Article author: grassrootsmotorsports.com
- Reviews from users: 2604
Ratings
- Top rated: 4.1
- Lowest rated: 1
- Summary of article content: Articles about Broken off exhaust bolt in Aluminum LS heads: “RUST” them out?| Grassroots Motorsports forum | Weld a nut to the cracked stud, quench that weld with a spray of PB Blaster and start to turn it while it’s still hot. If the nut keeps shearing … …
- Most searched keywords: Whether you are looking for Broken off exhaust bolt in Aluminum LS heads: “RUST” them out?| Grassroots Motorsports forum | Weld a nut to the cracked stud, quench that weld with a spray of PB Blaster and start to turn it while it’s still hot. If the nut keeps shearing … Broken off exhaust bolt in Aluminum LS heads: “RUST” them out?
- Table of Contents:

Access Denied
- Article author: shop.advanceautoparts.com
- Reviews from users: 21400
Ratings
- Top rated: 3.6
- Lowest rated: 1
- Summary of article content: Articles about Access Denied The worst of these were the exhaust manifold and header studs that were … and usually required the removal of the head to get it out. …
- Most searched keywords: Whether you are looking for Access Denied The worst of these were the exhaust manifold and header studs that were … and usually required the removal of the head to get it out.
- Table of Contents:

See more articles in the same category here: Top 122 tips update new.
How to Remove Corroded Bolts From Aluminum
Even though aluminum does not rust, corrosion can still form between aluminum and a non-aluminum bolt. This is especially true of aluminum parts and stainless steel bolts subjected to saltwater. The saltwater causes electrolysis between the metals. This will corrode the two unlike metals and create a bond nearly as strong as welding the pieces together. To break this bond, you need to expand the aluminum with heat. Since aluminum is an excellent heat sink, you need a lot of heat to free the corroded bolt.
How would you remove a broken exhaust manifold from an aluminium cylinder head?
Generally speaking its a lot easier to pull the head than it is to remove a broken exhaust stud.
Yes its best if everything goes back where it came from, just lay them out in the order they are removed. If you want to get fancy get some old chunks of 2x something, drill holes for the pushrods and screw in some drywall screws and wrap with electrical tape to hold rocker assemblies.
If you want to get even fancier, they sell trays to hold these parts in order, I’m sure either jegs or summit has them.
If you somehow get them mixed up, its not the end of the world. I’ve worked in several shops where they don’t even bother to pay attention, just slap them back in where ever. In theory I’m sure the engines done this way have somewhat accelerated wear, but I’ve yet to see it cause an issue.
If this is your $20k race engine then yes its more important, in a plain stock engine then I still put them back where they go because that’s how I was taught, but it probably doesn’t make enough difference to worry about.
If you drill crooked on the other hand that can cause some more serious issues, like drilling into the water jacket, destroying the hole you are trying to save, etc….
Depending on how it looks, I might drill it out, but I’m done this a lot and know what I need for access and I have a good drill and bits. I might try an easy out, but in my experience if a left handed bit doesn’t pull the broken piece out, the easy out isn’t going to either.
Easy outs like to break, and then you have an easy out stuck in there and they are harder to get out than the original bolt is. If you try an easy out and it doesn’t come right out, stop.
If your hole is dead center you can increase drill bit size until you are almost at the threads and then take a small chisel ground round on one side, or they sell ‘shearing chisels’ and tap one side in and whats left in the hole will peel right out.
You can also get the right size helicoil ahead of time and just drill the hole out to that size, tap it and insert the helicoil, but I prefer not to do that, and almost never have to.
I haven’t done a lot of the welding a nut on to remove broken bolts, mainly because my welder is a crappy one and I’m not especially good with it. I have tried it a couple times when the bolt is broken off flush and I have plenty of room and the welder is handy. It worked fine then, but being used to drilling them I normally just do that.
Without any previous experience doing any of these methods, and with nobody handy to help you do it, I would just pull the head and send it to a machine shop as suggested above.
How many miles does this engine have on it?
If the engine has less than say, 180k or so, then I would pull both heads and have the machine shop go through them. A good machine shop isn’t generally that expensive, I would say less than $300 for both heads and to remove the broken stud, but will vary by shop and area.
If the engine has higher mileage, anything over 200k for sure, I would just have them pull the broken stud and checked for warping if the head looks good otherwise.
By that I mean no visible cracks, and all the exhaust valves look the same color as each other, and all the intakes look the same each other as well. With the spark plugs in turn the head so the flat side is up and pour gasoline into each combustion area, if the gas stays there for a few minutes the valves are sealing ok.
You can check to make sure the heads aren’t warped yourself if you have a good straight edge and a set of feeler gauges, process and specs are easy to find on the internet I imagine.
While the heads are at the machine shop I would have them install new valve seals. Get your headset (all, or most anyway, of the gaskets needed to do this job are sold as a set, don’t need any fancy gaskets, common felpro work fine.) and take the seals to the machine shop with the head/heads.
The reason I don’t suggest having the heads completely done on a higher mileage engine is that what tends to happen if you do. If you take a higher mileage engine, over 200k and put new heads on it, within a year the bottom end will likely go out.
I’ve seen it happen many times.
But if you can just replace the head gaskets and valve seals (providing the head is in ok shape as mentioned above) they tend to last fine.
Make sure to mark the heads, some can be switched from one bank to the other, some can’t, I just mark them all to be sure. If you are having the heads done completely then it doesn’t matter which head goes where generally speaking. (if they can physically be switched in the first place of course.)
I advise customers to not do heads on a higher mileage engine at all, but many don’t listen to the mechanic, they just look at the dollar amount.
If the heads need more work on a higher mileage engine, I go out of my way to explain what will likely happen, sometimes they listen, sometimes not. If they have me go ahead and get the heads done and reinstall them, most of the time they are back with a bottom end knock within a year.
Note: by having the heads done, I mainly mean having the valves reground, and/or having them surfaced more than a clean up pass.
What happens, or so I believe, is that the valves, rings, and bearing all wear together. This isn’t ideal, but every body gets along ok. If you have a cylinder with a little valve wear and it has been there for years, the rings and bearings have worn themselves accordingly. If you suddenly put a head with perfect valves on that cylinder, and maybe even with higher compression due to surfacing, the associated rings and bearings aren’t used to that pressure and they are loaded differently besides. It works for a time, but eventually they can’t take the extra wear and they get too loose. Push the engine moderately hard and you get a knock.
Fixing Exhaust Leak from Broken Manifold Bolts
If you use a gasoline-powered V-8 pickup or SUV to tow a trailer, chances are you’re going to eventually have an exhaust leak caused by broken manifold bolts or studs. We have a 2004 Dodge Durango with the aluminum-head 5.7L Hemi that we purchased brand new. In addition to regular commuting duties we frequently use the little workhorse SUV to tow a 6,500-pound wakeboard boat or a Jeep/trailer combo of similar weight. The passenger and driver exhaust manifold bolts let go at roughly 70,000 miles and we had them replaced by the dealership under warranty. Then, at about 188,000 miles the driver-side exhaust studs snapped. We got really lucky and those particular studs snapped off with about 1-inch of exposed stud shaft sticking out of the cylinder head. Furthermore, the broken studs were only in finger-tight, so we were able to just spin them out and replace the gasket and bolts with little drama. Most recently at 262,000 miles the passenger side started the telltale “tick, tick tick” when the engine was cold. Once the vehicle was driven a short distance, the manifolds swelled up and the tick was mitigated, but we figured we’d highlight the fix before it got too severe.
Why You Should Fix an Exhaust Leak
Under extreme use like towing heavy loads, the exhaust manifolds can go from normal operating temperature to cherry red in a matter of seconds. That rapid heat causes the exhaust manifold material to expand, which puts a tremendous strain on the bolts and/or studs holding the manifolds to the cylinder heads. After hundreds of expansion and contraction cycles, the studs or bolts finally fail. It’s not too dissimilar from bending a paper clip back and forth. Eventually it’s gonna come apart in your hands. With only part of the manifold cinched tightly to the engine cylinder head, the exhaust gasket will blow out, not only allowing exhaust gases to escape, but possibly allowing air to enter the exhaust stream, throwing off the O2 sensor’s readings. If the O2 sensor thinks the engine is running leaner than it should, it will trigger more fuel to be dumped into the engine, potentially causing harm to the catalytic converter(s). Also, the exhaust manifolds can expand and contract unevenly, which could cause the cast iron to crack, compounding the incorrect O2 sensor readings, not to mention making the annoying exhaust leak sound worse.
Getting Access to the Engine
Every vehicle is different, but on this Dodge Durango it’s easiest to gain access to the exhaust manifolds by jacking up the vehicle, removing the front tire, and then taking out the inner fender liner. We put a jackstand securely under the framerail and then got to work. Once we had access to the manifold we soaked the bolts with penetrating oil to help them come out without snapping. If you live in an area that uses road salt or you experience a lot of rain, snow, or ocean spray, you’ll probably want to devote a couple days to soaking the bolts repeatedly with penetrating lube. This vehicle has been in SoCal its entire life so we just let them soak for a couple hours before proceeding.
See all 21 photos See all 21 photos Remove the wheel and tire and then the inner fender liner to gain access to the exhaust manifolds.
See all 21 photos See all 21 photos Inspect the bolts and exhaust system for obvious damage before proceeding. If you need more parts, it’s best to order before you tear your vehicle down.
See all 21 photos See all 21 photos Our manifold collectors use captured nuts that had rusted apart.
See all 21 photos See all 21 photos Use a quality penetrating spray to soak all of the exhaust bolts before you try to remove them. It will help prevent further snapping and more work.
Removing the Manifold
In our case, the Hemi exhaust manifolds use four studs and five bolts. The studs hold the heat shield in place. All of our bolts came out in one piece, but two of our studs had snapped. Furthermore, two of the nuts that held the heat shield on had seized to the studs and wouldn’t spin. Normally, you can’t just spin the studs out with the heat shield in place, but in our case one of the seized stud nuts was on one of the snapped studs and the other loosened just enough before refusing to budge that it created enough slack to allow the stud to spin out without destroying the heat shield. We were able to pull the heat shield free and then remove the studs on the ground without hurting anything. All of the exhaust manifold bolts came out without issue, but the collector nuts that had rotted away were a problem. Miraculously, we were able to get a pair of vise-grip pliers on the nut and hold it tight enough to remove the manifold collector bolts. With all the bolts removed, the manifold and gasket were removed, exposing the broken studs in the cylinder head.
See all 21 photos See all 21 photos The snapped stud (foreground) obviously pulled right out of the manifold. The rear stud spun out after we managed to loosen the heat shield, retaining nut enough to allow it to spin on the heat shield.
See all 21 photos See all 21 photos With the heat shield removed we took all but one manifold bolt out before tackling the collector-to-downpipe bolts.
See all 21 photos See all 21 photos The collector bolt originally featured a captured nut that wouldn’t spin, but the material had rotted away. Thankfully we were able to get a pair of regular vise-grip pliers on the outer nut. A pair of needle-nose vise-grip pliers fit between the collector and engine block on the inside bolt. We used regular nuts when reassembling.
Extracting a Broken Bolt from Cylinder Head
Depending on where the stud or nut breaks determines how lucky you are. Ideally, the stud or bolt will break with a bunch of shaft exposed that you can get a set of pliers on to spin it free. If not and it’s broken off flush, we’ve had success in some cases of carefully using a sharp punch or chisel to carefully spin the stud out. However, chances are the bolt or stud will either be snapped off deep in the threads or will be seized and won’t want to come out. In those cases you have two options: drill it out or weld a nut onto the broken portion and spin it out.
See all 21 photos See all 21 photos This stud had snapped off about inch below the surface of the cylinder head and wouldn’t spin with a sharp punch.
Drilling can be a dangerous and unsuccessful endeavor. The idea is you start drilling in the direct center of the bolt and then step up the drill size in increasingly larger increments until you’re almost at the threads. Then, you can use an extractor to spin the remaining bolt out. We’ve done this in the past, but it’s nerve-racking because if you break off a drill bit or hardened extractor inside the head there’s virtually no getting it out. We contemplated drilling our stud out, but the fact that we have aluminum cylinder heads and this vehicle had a control arm smack in the way of the drill, we opted for the welding route.
See all 21 photos See all 21 photos Even with a tight 90-degree drill, an upper control arm prevented us from getting a clean angle with the drill extractor on the broken stud.
Your other option when all else fails is welding a nut onto the end of the broken bolt or stud and spinning it out. Not only will the welding give you a secure purchase with which to wrench or spin the broken shank out, but the heat from the welding will help loosen any rust, antiseize, or other material that’s helping prevent the broken shank from coming out. If you’re working with iron cylinder heads you need to be extremely careful to avoid actually welding the nut to the cylinder head or damaging the threads. For this reason, it’s usually best to use a TIG welder. TIG welding is much more precise than MIG welding, but not everybody can do or has a TIG welding setup. Worst case scenario there is you’re removing your cylinder heads and taking them to a machine shop to have the stud extracted. However, most modern engines like the 5.7L Hemi we’re dealing with have aluminum cylinder heads. With standard MIG or TIG welding, the steel welding wire won’t stick to or even damage the aluminum of the cylinder head, allowing you relative safety while attempting to weld on a nut. We used a pair of needle nose pliers to hold a 3/8-inch nut over the hole containing our broken stud. Because the shank was roughly inch down in the hole, we used a relatively high wire speed to help fill the gap and let ‘er rip. With a nut securely welded to the broken stud, the remaining portion spun right out with no damage.
See all 21 photos See all 21 photos We attached our welding ground to the engine and used needle nose pliers to hold a 3/8-inch nut against the head over the hold containing the broken stud shank.
See all 21 photos See all 21 photos With a relatively high wire speed, we welded the nut onto the broken shank and spun it out of the head.
See all 21 photos See all 21 photos You can see the gap between the portion of the broken stud and the nut.
See all 21 photos See all 21 photos Using a relatively low welding heat, the aluminum of the cylinder head remains completely undamaged form the welding procedure.
New Exhaust Gaskets and Studs and Reassembly
Thankfully, after a careful inspection we found no cracks in our factory exhaust manifold. You don’t want to cheap out and get inferior parts when it’s time to reassemble. For our 2004 Hemi we went with a factory Mopar exhaust manifold gasket and a set of new FelPro studs that we purchased from Summit Racing. The FelPro studs came with a blue coating for corrosion resistance and included thread locker on the threads. It seems the gasket design has changed over time, so after verifying the port sizes on the gasket were the same as the original, we applied some antiseize to the bolt threads and got ready to reinstall the manifold. Two of the manifold bolt holes are notched to allow the manifold to slide on. This allows you to keep the manifold gasket on the head while you manipulate the heavy manifold into place. In our case, we had enough access where this wasn’t really an issue, so we assembled both gasket and manifold together, making sure to put studs in the correct holes to accept the heat shield. After getting the bolts finger-tight we broke out the torque wrench and over three passes torqued the manifold bolts and studs in the correct pattern (we found ours online) to the correct 18-lb-ft value for our engine. After the manifold was torqued to the head, we installed some new Grade 8 bolts, lock washers, and nuts and tightened down the downtube collectors to the manifold. After a test fire to verify there were no leaks we buttoned up the inner liner, reinstalled the wheel, and enjoyed the relative sound of silence when firing this engine up when cold.
See all 21 photos See all 21 photos We cleaned and wiped the gasket surfaces of both the cylinder head and exhaust manifold to ensure a leak-free seal.
See all 21 photos See all 21 photos A factory Mopar gasket and FelPro hardware kit from Summit Racing were the only parts we needed. Grand total for this job came in at $75.39.
See all 21 photos See all 21 photos The FelPro hardware kit is $30.99 through Summit Racing, but its high quality with a corrosion-resistant coating fits perfectly.
See all 21 photos See all 21 photos We threaded one bolt through the gasket into the head to hold the gasket in place while we got the manifold ready.
See all 21 photos See all 21 photos Make sure the bolt hole you use corresponds with the slotted hole in the manifold so you can just slide it into place.
See all 21 photos See all 21 photos We torqued the exhaust bolts to 18 lb-ft per the manufacturer’s pattern, which we found through an online service manual. If you can’t find yours, just start in the center and alternate crisscross—bottom, top, side, side—until you’ve done all of them.
So you have finished reading the how to removing broken exhaust manifold bolt from aluminum head topic article, if you find this article useful, please share it. Thank you very much. See more: removing exhaust studs from aluminum head, cost to remove broken exhaust manifold bolt, welding broken exhaust manifold bolts, how to remove broken exhaust manifold bolts, 5.3 broken exhaust manifold bolts, how to remove ls exhaust manifold bolts, broken exhaust manifold bolt removal tool, driving with broken exhaust manifold bolts