당신은 주제를 찾고 있습니까 “fault isolation manual – RDR-4000 On-Wing Fault Isolation“? 다음 카테고리의 웹사이트 Chewathai27.com/you 에서 귀하의 모든 질문에 답변해 드립니다: Chewathai27.com/you/blog. 바로 아래에서 답을 찾을 수 있습니다. 작성자 Honeywell Help \u0026 Support 이(가) 작성한 기사에는 조회수 93회 및 좋아요 2개 개의 좋아요가 있습니다.
fault isolation manual 주제에 대한 동영상 보기
여기에서 이 주제에 대한 비디오를 시청하십시오. 주의 깊게 살펴보고 읽고 있는 내용에 대한 피드백을 제공하세요!
d여기에서 RDR-4000 On-Wing Fault Isolation – fault isolation manual 주제에 대한 세부정보를 참조하세요
RDR-4000 On-Wing Fault Isolation
fault isolation manual 주제에 대한 자세한 내용은 여기를 참조하세요.
Fault Isolation Manual Definition | Law Insider
Define Fault Isolation Manual. or “FIM” – means the Manual that deals with methods that can isolate the component, device or software module causing the …
Source: www.lawinsider.com
Date Published: 5/20/2022
View: 9347
Fault Isolation Manuals Are Failing – IQPC
Fault Isolation Manuals Are Failing. Troubleshooting is the step-by-step process by which the causes of equipment problems are entified so that proper …
Source: www.iqpc.com
Date Published: 7/7/2021
View: 2031
On Shift
A fault isolation manual (FIM) prescribes a series of steps to be used when troubleshooting a problem. The steps in the FIM involve replacing parts, …
Source: www.faa.gov
Date Published: 11/23/2021
View: 1301
Fault Isolation Manual
Operation and Service/organizational, GS and Depot Maintenance Manual with. Illustrated Parts Breakdown 1968.
Source: m.central.edu
Date Published: 3/28/2022
View: 3453
(PDF) GENERAL SCHEDULED MAINTENANCE AIRCRAFT …
GENERAL SCHEDULED MAINTENANCE AIRCRAFT MAINTENANCE MANUAL FAULT ISOLATION MANUAL ILLUSTRATED PARTS CATALOG STRUCTURAL REPAIR MANUAL (PART 1) ILLUSTRATED …
Source: www.academia.edu
Date Published: 11/30/2022
View: 7486
An Evaluation of Fault Isolation Manuals from the … – DTIC
The purpose of this research was to investigate the F-16 Fault Isolation Manual from the maintenance technicians perspective.
Source: apps.dtic.mil
Date Published: 4/30/2021
View: 2959
Aircraft Troubleshooting Optimization Using Case-based …
The Fault Isolation Manual (FIM) is consered as a specialist … in determined situations to properly isolate a fault. Although.
Source: papers.phmsociety.org
Date Published: 5/14/2021
View: 2943
ps01 – Boeing
Component maintenance and overhaul manuals for all Boeing and Douglas components. … Fault isolation manual. Fault reporting manual.
Source: www.boeing.com
Date Published: 1/22/2021
View: 1281
Fault-Isolation-Manual/b747-JT9D7A-fim.pdf at master – GitHub
Creation of an automatic Boeing 747 Fault Isolation Manual using Prolog – Fault-Isolation-Manual/b747-JT9D7A-fim.pdf at master …
Source: github.com
Date Published: 1/29/2021
View: 1019
주제와 관련된 이미지 fault isolation manual
주제와 관련된 더 많은 사진을 참조하십시오 RDR-4000 On-Wing Fault Isolation. 댓글에서 더 많은 관련 이미지를 보거나 필요한 경우 더 많은 관련 기사를 볼 수 있습니다.
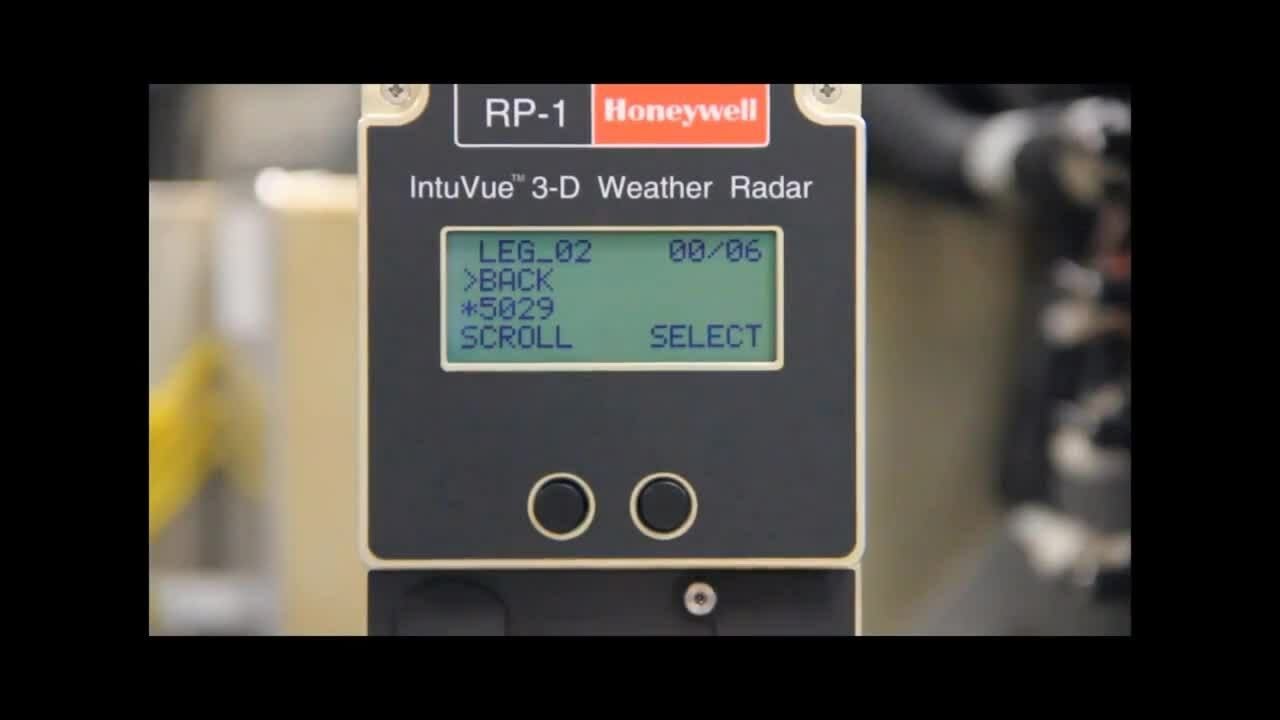
주제에 대한 기사 평가 fault isolation manual
- Author: Honeywell Help \u0026 Support
- Views: 조회수 93회
- Likes: 좋아요 2개
- Date Published: 2021. 1. 5.
- Video Url link: https://www.youtube.com/watch?v=BFHtCNUUo7A
What is fault isolation manual?
A fault isolation manual (FIM) prescribes a series of steps to be used when troubleshooting a problem. The steps in the FIM involve replacing parts, one after another, until a faulty part is found and replaced and the system functions normally again.
What is the difference between AMM and CMM?
The legislation lists what maintenance manuals should be used with reference to aircraft maintenance, and those include mainly the AMM (aircraft maintenance manual) and IPC (illustrated parts catalogue). However, also the CMM (component maintenance manual) is listed as possible aircraft maintenance data.
What is the process of troubleshooting in aircraft?
Troubleshooting is the process of identifying the cause of a malfunction or discrepancy, determining its severity, eliminating the cause, replacing or repairing discrepant components, systems, or structures, and, finally, …
What is the importance of IPC in aviation?
The objectives of the IPC are to: Assess your knowledge of instrument flight (including subjects such as Federal Aviation Regulations, the Airman’s Information Manual, meteorology, flight planning, aircraft performance, aircraft navigation systems, and emergency procedures.
What is problem isolation?
Problem isolation moves you from the general ideas about a problem, to a specific idea of what the problem is, as follows: Before problem isolation: I have no idea, except for some general symptoms.
What is AMM manual?
Definition. The formal document which details the way in which all maintenance tasks carried out on an aircraft shall be accomplished. This includes items such as lubrication system functional checks and servicing of the airplane but usually excludes structural repairs and modifications.
What is IPC in aircraft maintenance?
The IPC is a companion document to the Aircraft Maintenance Manual (AMM). Use The Aircraft Maintenance Manual (AMM) for the Removal and Installation of parts on the aircraft. The document is divided into chapters according to the systems of the aircraft. Each chapter contains figures and tables with a description.
What does SRM mean in aviation?
Safety Enhancement Topic
Single-pilot resource management (SRM) is the art of managing all onboard and outside resources available to a pilot before and during a flight to help ensure a safe and successful outcome. Incorporating SRM into GA pilot training is an important step forward in aviation safety.
What is the difference between troubleshooting and testing?
We could treat testing and troubleshooting as two topics. Troubleshooting almost always involves some type of testing. However, troubleshooting implies that we suspect some “trouble” to exist. Testing can be done for reasons entirely unrelated to finding a suspected problem.
What is a Mel in aviation?
A minimum equipment list (MEL) is a list which provides for the operation of aircraft, subject to specified conditions, with particular equipment inoperative (which is) prepared by an operator in conformity with, or more restrictive than, the MMEL established for the aircraft type.
What are the common engine problems in aircraft?
Reasons that are known to occur include: Preventable fuel problems such as exhaustion, mismanagement, contamination, or misfueling. Structural failures where a broken connecting rod, crank, valve, or camshaft is present account for seventeen percent of engine failures, primarily in Continental engines.
What is fault isolation in aircraft?
Fault Isolation Manual or “FIM” – means the Manual that deals with methods that can isolate the component, device or software module causing the error.
What is fault isolation in networking?
Fault isolation is the identification of the error cause. Typically, software fault isolation is attained by determining the sequence of events (inputs, outputs, software states, etc.) leading up to the error. The sequence of events isolates the software component executing at the time of the error.
What is the software fault isolation?
Software Fault Isolation (SFI) is a security-enhancing program transformation for instrumenting an untrusted binary module so that it runs inside a dedicated isolated address space, called a sandbox.
How do you isolate a fault?
It is accomplished by building in test circuits and/or by dividing operations into multiple regions or components that can be monitored separately. After fault isolation is accomplished, parts can be replaced manually or automatically (see fault tolerant).
Fault Isolation Manual definition
Boeing Aircraft Manuals, including the Fault Isolation Manual , that explain the operation, maintenance, servicing and trouble-shooting of the Engine for the B787.
Before further flight after any movement reported in accordance with paragraph (g) of this AD, determine which servomotor moves the pitch trim control wheel, and do applicable other specified actions in accordance with Airbus A300 TR 22–001, dated April 11, 2003, to Chapter 22– 23–00 of the Airbus A300 Fault Isolation Manual .
A dual engine flame out could result in inaccessibility of the remaining fuel in the center tank due to loss of electrical power to the pumps, consequent unrecoverable dual28–41–00, Section July, of the Boeing 767 Fault Isolation Manual (FIM).
In the course of the interviews, examples were given of poor procedures including poorly conceived Fault Isolation Manual (FIM) documents.
Before further flight after any movement reported in accordance with paragraph (g) of this AD, determine which servomotor moves the pitch trim control wheel, and do applicable other specified actions in accordance with Airbus TR No. 22–001, dated April 11, 2003, of Chapter 22– 23–00 of Airbus A300 Fault Isolation Manual .
FIM Fault Isolation Manual A manual containing technical Data required by the technician to isolate the Fault and identify remedies.
Customer’s claim includes all applicable documentation of such tests with the returned Boeing Product, including but not limited to: Central Maintenance Computer ( CMC), Flight Maintenance Computer System, (FMCS), Fault Isolation Manual (FIM), Engine Indicating and Crew Alerting System (EICAS) or Built In Test Equipment (BITE) messages.
Troubleshooting may involve avionic LRU changes, however, it does not involve multiple avionic LRU changes in pursuit of a system fault, unless the changes are made in accordance with a published approved fault isolation maintenance procedure (e.g. Troubleshooting Manual, Fault Isolation Manual procedure).
Class 2 faults do not affect dispatch and will be listed in the Fault Isolation Manual (FIM).
Project Manual means the volume usually assembled for the Work which may include the bidding requirements, sample forms, and other Contract Documents.
Technical Specifications means the technical specifications set forth in Schedule 1 to the Agreement and to which, the STBs, CAS and SMS must comply with.
technical specification means, with respect to any Software, the document setting forth the technical specifications for such Software and included in the Statement of Work.
User Manual means the user guide, Help Guide, documentation provided with the Software, updated agreements provided on the website of Quick Heal (www.quickheal.com), explanatory or other materials as provided from time to time by Quick Heal.
Isolation means a behavior management technique in which a student is placed alone in an enclosed space from which the student is not prevented from leaving.
Project Implementation Manual means the manual adopted by the Recipient through the PCU on November 30, 2010, for the purposes of defining the detailed implementation arrangements for the Project, and setting forth, inter alia: (i) the detailed Project staffing plan for each stakeholder; (ii) the Project monitoring and evaluation modalities; and (iii) the terms, procedures and conditions for the initial management and operation of the national CARG scheme, as the same may be amended from time to time with the agreement of the Association.
Design Manual means the MOHLTC design manual or manuals in effect and applicable to the development, upgrade, retrofit, renovation or redevelopment of the Home or Beds subject to this Agreement.
Subsystem means a functional grouping of items that combine to perform a major function within an end item, such as electrical power, attitude control, and propulsion.
Customer Specific Training means a private Course organized on demand specifically for Customer.
Backflow Prevention Assembly means any mechanical assembly installed at a water service line or at a plumbing fixture to prevent a backflow contamination event, provided that the mechanical assembly is appropriate for the identified contaminant at the cross connection and is an in-line field-testable assembly.
Technical safeguards means the technology and the policy and procedures for its use that 27 protect electronic PHI and control access to it.
Modules means the Base Modules and Extended Modules.
Web Site Accessibility Standards/Specifications means standards contained in Title 1 Texas Administrative Code Chapter 206.
Web Site Accessibility Standards/Specifications means standards contained in Title 1 Texas Administrative Code Chapter 206.
Diagnostic clinical procedures manual means a collection of written procedures that describes each method (and other instructions and precautions) by which the licensee performs diagnostic clinical procedures; where each diagnostic clinical procedure has been approved by the authorized user and includes the radiopharmaceutical, dosage, and route of administration.
Operations Manual means a manual containing procedures, instructions and guidance for use by operational personnel in the execution of their duties;
Electronic Subcontracting Reporting System (eSRS) means the Governmentwide, electronic, web-based system for small business subcontracting program reporting. The eSRS is located at http://www.esrs.gov.
Procedures Manual means the standards and procedures manual described in Section 8.3.
Automated data acquisition and handling system or “DAHS” means that component of the CEMS, or other emissions monitoring system approved for use under rule 3745-14-08 of the Administrative Code, designed to interpret and convert individual output signals from pollutant concentration monitors, flow monitors, diluent gas monitors, and other component parts of the monitoring system to produce a continuous record of the measured parameters in the measurement units required by rule 3745-14-08 of the Administrative Code.
Electronic Programme Guide or “EPG” means a program guide maintained by the Distributors of Television Channels that lists Television Channels and programmes, and scheduling and programming information therein and includes any enhanced guide that allows subscribers to navigate and select such available channels and programmes;
Provider Manual means the DAVIS Vision Care Plan Provider Manual, as amended from time to time by DAVIS.
Service Specifications means the following documents, as applicable to the Services under Your order:
CAISO Tariff means the California Independent System Operator Corporation Operating Agreement and Tariff, including the rules, protocols, procedures and standards attached thereto, as the same may be amended or modified from time to time and approved by the FERC.
Electronic Payment System means a payment system that generates any transfer of funds, other than a transaction originated by cash, check, or similar paper instrument, which is initiated through an electronic terminal, telephone, mobile phone, computer, or magnetic tape, for the purpose of ordering, instructing or authorizing a financial institution to debit or credit an account. The term includes debit cards, wire transfers, transfers made at automatic teller machines, and point-of-sale terminals.
MERS Procedures Manual The MERS Procedures Manual, as it may be amended, supplemented or otherwise modified from time to time.
Aircraft Component Maintenance
The maintenance of aircraft components is a story of its own, and in this introductory post, I will try to go through some of the basics and the general idea of what an aircraft component actually is and who can do maintenance work on it.
Let’s start with the second question – who can do maintenance on aircraft components? A Part 145 approved maintenance organization, with an A-class approval (for aircraft) can carry out maintenance on aircraft. However, an aircraft is – quite obviously – made up of hundreds or thousands of components. So how can deep can an aircraft maintenance organization go? It’s quite obvious that we can remove an engine from an aircraft. But can we remove a fuel pump from the engine? And if so, are we allowed to replace the driving shaft of that fuel pump, would this still be aircraft maintenance?
Maintaining components as part of the aircraft
The answer, as usual, lies within the aircraft technical documentation and relevant legislation, Part 145 in this case, for our EASA example. The legislation lists what maintenance manuals should be used with reference to aircraft maintenance, and those include mainly the AMM (aircraft maintenance manual) and IPC (illustrated parts catalogue). However, also the CMM (component maintenance manual) is listed as possible aircraft maintenance data. So what can we do?
In fact, this is actually quite simple. The AMM will tell you what you are allowed to do on an aircraft and hence, what technical actions are considered aircraft maintenance rather than component maintenance. It is possible to perform maintenance tasks in accordance with a CMM provided the AMM refers to it and tells you to perform those tasks. The regulation itself allows for component maintenance in accordance with a CMM under A category approval provided the component does not need to be removed from the airframe in order to undergo such maintenance unless it is being removed only for the purpose of obtaining better access. This may sound complex, but it really isn’t – the general idea is that you can do component maintenance under the aircraft category in two cases:
When the AMM tells you to do so by providing appropriate instructions or by pointing to a relevant CMM When the maintenance of the component does not require the unit itself to be removed from the airframe except for the purpose of improving technical access. This means that you cannot perform any component maintenance which requires shelf tests or mechanical finishing, for instance.
Furthermore, the IPC which I mentioned earlier, gives you a list of all aircraft parts and components. This means that all the part numbers which are listed in the IPC can normally be replaced on the aircraft. In other words, if the IPC lists a component as one part number and does not list the specific pieces which make up a given component, it should generally be considered as a standalone unit, which needs to be maintained under a component maintenance approval.
So now we know what component maintenance is not. So how do we go about fixing the components which are being removed from the aircraft?
Maintaining components on their own
The ability to fix components requires a different kind of Part 145 approval – an approval within the C category. There are several of those categories, numbered C1, C2, C3 .. and so on and they are more or less structured by ATA chapters (so you get categories like hydraulics, or landing gear). This approval allows you to do something, that is not allowed when you maintain components in the A category as described above – it allows you to issue a component release certificate in the form of an EASA Form One or equivalent (like the FAA Form 8130).
The components release certificate is a document stating that the component you have just performed maintenance on is ready for release to service within the limits prescribed in relevant documentation or set forth by your limitations (workshop limitations). The EASA Form One is mandatory for operators (your customers) to be able to fit the component to their aircraft.
Typical component maintenance events
There are three main component maintenance events which are generally performed by specialized shops:
Aircraft Component Overhaul
Aircraft Component Repair
Aircraft Component Modification
All of those have their own specifics and require a slightly different approach from both the operator / airworthiness provider and the workshop. Let’s look at them in slightly more detail.
The overhaul of aircraft components
Even though modern aircraft strive away from hard time maintenance, and condition monitoring is becoming the main approach for maintenance steering groups, many components still require regular overhauls once in a while.
An overhaul is sometimes called a major repair, although personally I don’t like this term as it is highly confusing. In most cases, when an overhaul is required, the operator will provide the workshop with a component which is generally serviceable except for the fact that it has reached it’s hard time limit. This means that there will be no defect syndromes to take care off and no defect description as such.
Overhauls are defined either in component maintenance manuals (CMM) or in specific overhaul manuals (OM) although the latter is generated mainly for major components such as engines, propellers or landing gear. Whatever its name, the technical documentation specifies exactly what needs to be accomplished during an overhaul of the given aircraft component. Such tasks generally include:
Dismantling of the component to given detail
Thorough detailed visual inspections and special inspections (such as NDT) of selected parts
The discarding and replacement of parts which have life limits within the components or need to be replaced whenever the component is torn down (such as seals)
Cleaning, fixing of known and detectable defects
Reassembly
Thorough bench testing of the component
As a result, we get a component which is treated as new without additional limits imposed. What’s worth noting, however, is that especially for major components (like landing gear or engines) there are life limited parts within a components, and their life limit is often longer than the TBO (time between overhaul) for the component itself. As a result, we are allowed to place a “used” part into a component during overhaul. In order for this to be possible, the repair shop needs to obtain from the operator or airworthiness provider accurate and properly signed life limit details on the part – this is the workshops only source of information regarding the parts inside the overhauled component. Without this, they will not be able to release the component to service and hence will have to replace all parts with brand new ones, which is generally quite expensive and an unnecessary cost as such.
Aircraft component repair
The repair of aircraft components is slightly different from a complete overhaul, as the workshop needs only to determine what causes a given defect, rectify that defect, run some bench tests and release the component back to service.
The trouble shooting procedures are generally available in the CMM or the CRM (component repair manual). Therefore, in most common scenarios, the procedure is as follows:
Check the documentation for a trouble shooting (T/S) procedure applicable to the given defect symptoms
Carry out all tests in accordance with the procedure
Determine the fault
Eliminate the fault in accordance with an appropriate procedure from the CMM/CRM
Do reassembly tests and release the unit
As simple as this may sound, there is something that every operator or airworthiness provider needs to understand and remember:
Whenever a component is torn down (“opened up”) in a workshop, it is the workshop responsibility to assess its general state (not only with respect to the reported defect, but as a whole). This means, that a simple defect may end up requiring even a complete overhaul if, after the components is opened, it turns out that several parts and subassemblies need replacing due to excessive wear and tear. This always increases costs and is very difficult to plan for because, for parts which are not hard time controlled, it is almost impossible to assess their condition without bench testing them at least.
Aircraft component modification
Quite often, components need to be modified. Sometimes the modification is intended to improve the usability of a given component and is voluntary, at other times a modification is required for instance during every overhaul.
Modifications can have several forms, from introductions of new, modified component sub-assemblies to the replacement of software in modern, electronic aircraft components.
A modification is rarely done on its own – most often it is performed during an overhaul or a repair (generally speaking – during a shop visit) of the component. It is either ordered by the operator or airworthiness provider if it is voluntary, or performed by the workshop automatically if it is mandatory.
The fact that a modification has been applied to a given component must be made clear on the release document (EASA Form One) and recorded in the operator’s airworthiness record system.
I hope that this brief post was somewhat helpful. If you have any ideas, questions or anything you would like to share – please leave a comment below or email me!
Aircraft Maintenance and Repair, Seventh Edition, 7th Edition [Book]
Troubleshooting Theory and Practice 19
INTRODUCTION
Whenever a malfunction or discrepancy is reported or comes to the attention of the technician, no matter how simple or how complex, the process of troubleshooting begins. The technician must determine the discrepancy’s effect upon the airworthiness of the aircraft and the appropriate time and location for the corrective action to be taken.
THE TROUBLESHOOTING PROCESS
Troubleshooting is the process of identifying the cause of a malfunction or discrepancy, determining its severity, eliminating the cause, replacing or repairing discrepant components, systems, or structures, and, finally, …
GENERAL SCHEDULED MAINTENANCE AIRCRAFT MAINTENANCE MANUAL FAULT ISOLATION MANUAL ILLUSTRATED PARTS CATALOG STRUCTURAL REPAIR MANUAL (PART 1) ILLUSTRATED TOOLS AND EQUIPMENT MANUAL CONSUMABLE PRODUCTS
Academia.edu no longer supports Internet Explorer.
To browse Academia.edu and the wider internet faster and more securely, please take a few seconds to upgrade your browser.
An Evaluation of Fault Isolation Manuals from the Maintenance Technician’s Perspective
Accession Number: ADA229536
Title: An Evaluation of Fault Isolation Manuals from the Maintenance Technician’s Perspective
Descriptive Note: Master’s thesis
Corporate Author: AIR FORCE INST OF TECH WRIGHT-PATTERSON AFB OH SCHOOL OF SYSTEMS AND LOGISTICS
Report Date: 1990-09-01
Pagination or Media Count: 323.0
Abstract:
The purpose of this research was to investigate the F-16 Fault Isolation Manual from the maintenance technicians perspective. Evaluation considered the effect of various demographic factors and the maintenance technicians perceptions on the Fault Isolation Manuals usefulness and accuracy. The findings indicate that maintenance technicians who use the manual more perceive the manual to be more useful and accurate than technicians who use the manual less. The findings also determined that technicians have a perception that the manual has several inaccurate areas.
ps01
Boeing continues to expand upon technology-based solutions to support commercial airplane operators with maintenance management. One such solution is to provide operators with digital information through a secure on-line delivery system for hangar maintenance and through portable maintenance computers for time-critical problem-solving at the gate. These digital data products and services help operators improve productivity, reduce technical operational costs, and increase revenue by making additional flying time available. The digital data products and services offered by Boeing are designed to provide operators with the ability to efficiently search and retrieve maintenance and operations information. The chief benefits operators can realize by using these products include the ability to Access technical documents through a single point of entry.
Streamline engineering and maintenance operations.
Minimize technical interruptions such as delays and cancellations.
Boeing has been providing technical information in digital format since 1992 with the creation of the Reference Engineering Data Automated Retrieval System (REDARS) (see April-June 1995 Airliner magazine). Operators’ engineering and maintenance personnel now use high-speed systems with search-and-retrieval capabilities instead of flipping through paper and microfilm documents. The effort required to maintain current and accurate technical libraries is significantly reduced. The time savings allows for more engineering research (for example, developing repair procedures) and more time for mechanics to spend in productive labor. With simplified, rapid access to the most current data available, operators can reduce costs and ultimately increase revenues by returning airplanes to the revenue fleet sooner. Boeing is partnering with its customers and suppliers to assess the long-term value of leading-edge digital information technologies. The goal in this effort is to provide a unified set of applications based on Air Transport Association (ATA) specification 2100. According to Moore’s Law, technology doubles every 18 months and product concepts currently considered feasible may quickly become obsolete. The Boeing approach in recognizing Moore’s Law is to create digital products that will easily evolve into more powerful business applications as technology advances. This process includes transitioning operators (when requested) to cost-effective and more productive versions. The use of both existing and evolving ATA specifications is a key to maintaining the required stability. The company’s long-term strategy is to provide both digital data and systems throughout engineering operations. This includes materiel provisioning management, maintenance training, engineering, planning, heavy maintenance, line maintenance, dispatch, and flight operations. The delivery and use of data across different computing systems form the foundation for the growing Boeing family of digital data products and services. Providing end-to-end support with a single point of contact for all aspects of systems management is the cornerstone of the Boeing philosophy on digital products. The four primary products in the family are Boeing On-Line Data (BOLD). Portable Maintenance Aid (PMA) Portable Document Query System (PDQS). Standard Generalized Markup Language (SGML).
The digital data product Boeing On-Line Data (BOLD) is a secure global on-line delivery system that provides the aviation industry with the most accurate, current information available to operate and maintain the worldwide Boeing fleet. Through a single secure login, users have access to a complete digital reference library of information previously available only in an operator’s central technical library of paper, microfilm, and aperture cards. BOLD makes access to information as close as the nearest networked Windows, Macintosh, or UNIX workstation (fig. 1). As a result, the most current data is available at engineers’ and planners’ desks as well as on the shop floor for mechanics performing an overnight or heavy maintenance check. Operators and maintenance repair organizations around the world have used BOLD since its introduction in March 1995. Since then, system usage has increased to more than 6 million requests per week from both operators and Boeing users, as roughly 8,000 users at over 60 installations in Asia, Europe, and North America have moved away from outdated and hard-to-maintain paper processes. The operators included in this group fly more than 70 percent of the airplanes in the Boeing fleet. Switching to digital on-line data has enabled customers to reduce costs and increase revenue. Quick, easy access to the required data reduces research time during heavy maintenance, allowing airplanes to return to revenue service sooner. Users of BOLD have access to information created by Boeing and its component suppliers. To provide an integrated solution to all the data needed to operate and maintain a fleet, engine manufacturer CFMI has contracted with Boeing to provide select engine maintenance data over BOLD. Discussions and negotiations with other major engine manufacturers are underway. Data currently available on BOLD include: Engineering and tooling drawings for all Boeing-designed commercial airplanes, from the 707 to the 777. Work is underway to scan the approximately 1.5 million aperture cards that represent drawings for all Douglas-designed commercial airplanes. Completion is scheduled for mid-1999. A part-number index that correlates and links airplane parts and their associated installation drawings. Airplane service bulletins issued since August 1993 for Boeing-designed commercial airplanes and those issued since November 1994 for Douglas-designed commercial airplanes. Airplane service bulletin index for all bulletins issued for the combined Boeing and Douglas fleet, with a link to the loaded bulletins. Airplane service bulletin index for all bulletins issued for the combined Boeing and Douglas fleet, with a link to the loaded bulletins. Component maintenance and overhaul manuals for all Boeing and Douglas components. Component maintenance and overhaul manuals for more than 230 suppliers. Boeing part, materiel, and process standards. Information that correlates airplane effectivity for an operator’s Boeing fleet, allowing the user to query information applicable to a particular airplane.
Boeing has involved operators in the evolution of BOLD since its introduction. Direct feedback has resulted in additional content and enhanced functionality. Some of the following have been implemented and others are under development: Lower network costs. Improved system performance. More technical data.
Lower network costs.
Operators told Boeing that network costs to reach the database in Seattle, Washington, were too high. In response, Boeing worked with SITA to reduce costs for customers who use Aeronet, the private SITA network. Boeing established regional hubs around the world to support users of the distributed client-server BOLD application. As a result, these users need only acquire a connection to the hub site nearest their location, and Boeing purchases the network connection back to Seattle. This high-bandwidth connection is monitored and adjusted to grow with the operator’s usage. Current hub sites include Hong Kong, London, Singapore, and Tokyo. As new BOLD installations dictate, new hubs will be created. Planned sites include Bahrain, Moscow, São Paulo, and Sydney. Operators are not limited solely to SITA for network connection; BOLD supports standard TCP/IP access from any network provider, including the public Internet. Improved system performance.
One solution to improve system performance is to implement a local BOLD server at the operator’s site. The commands that create the images on the screen originate from the local server and are transmitted across the operator’s local area network to the user’s display. Printing can also be served locally, further reducing dependence on external communication with the Boeing servers in Seattle or the nearest regional hub, thus allowing for quicker system response. Another significant improvement is local data caching. When a user first requests to view a document in BOLD, the document is retrieved from the central repository in Seattle, sent across the network, and loaded into a local cache on the operator’s server. Navigation within the document is served from the local copy. When the document is requested again, the system will perform a quick currency check with the repository in Seattle to ensure that the local copy is the most recent. If not, the local copy is replaced with the newer version. Two types of caching, dynamic and static, are used. As documents fill the dynamic cache, the least accessed document is pushed out. Documents loaded to the static cache are not pushed out unless deleted or replaced with a newer version. The static cache is configurable and expandable to whatever size hard disk an operator’s system can support (typically 1 terabyte). The dynamic cache is limited to 2 gigabytes. A companion to local caching is a function called “publish and subscribe.” Users can be notified of new or updated documents and request these to be automatically cached in their local server. For instance, an operator’s service bulletin engineer can choose to be notified whenever bulletin activity occurs. Activity can be as broad as all Boeing bulletins or as narrow as bulletins applicable to a particular ATA chapter for a particular airplane model. When a new or revised bulletin is released, the system issues an e-mail notification and automatically downloads the bulletin to the local cache. The operator may designate the time that file transfers should occur to take advantage of off-peak hours, when rates are lowest. More technical data
The greatest value of BOLD as a global on-line delivery solution, however, lies in the technical data offered. As part of an integrated Boeing digital data solution, BOLD will serve as the on-line delivery mechanism for other Boeing products. Examples include the Portable Maintenance Aid (PMA) and Portable Document Query System (PDQS) discussed later in this article. Both will be delivered by BOLD with their associated documents and functionality. This added functionality addresses operators’ requests to Boeing for the additional data they need to support their business processes. This will include the following “big seven” documents: Aircraft maintenance manual. Fault isolation manual. Fault reporting manual. Illustrated parts catalog. Wiring diagram manual. System schematic manual. Structural repair manual.
BOLD will also contain engine manufacturer maintenance data. CFMI has contracted to deliver its service bulletins, engine manual, and illustrated parts catalog (IPC) for the CFM56-7–the sole engine for 737-600/ -700/-800–through BOLD. Negotiations with other major engine manu-facturers are underway to include additional models and documents. Boeing is currently developing functionality that will enable operators to manage their own data through BOLD. For operators who maintain storage of their own engineering drawings on aperture cards, Boeing can digitally convert these and manage them in the BOLD data repository. This allows the user, from a single system, to view Boeing drawings as well as his or her own. Also planned for future enhancement is the ability for an airline to add its own authored pages to the component maintenance and overhaul manuals loaded in BOLD. Lastly, BOLD is migrating to an object-oriented architecture. This will allow Boeing to offer a common object request broker architecture application programming interface to customers who would like to bypass the BOLD interface and access the data directly. As part of this technical migration, BOLD will move from its current X-Window/ Motif interface to a Java application incorporating Web technologies. BOLD is scheduled to become available on the Web in mid-1999. The drawings for heritage Douglas products and the traditional Boeing engineering and tooling drawings will become available on-line at that time, as will service bulletins and the “big seven” documents described in this article. Later, component maintenance and overhaul manuals, engine manufacturers’ data, and Boeing part, materiel, and process standards will also become available through BOLD on the Web.
Boeing has developed the Portable Maintenance Aid (PMA) to streamline the often time-consuming process of troubleshooting modern, complex airplanes. The PMA provides all the necessary line maintenance documentation in digital format along with a powerful search capability. The application includes specialized process-oriented features tailored to how each document is used. References within and between documents are hyperlinked to further minimize cross-referencing time. With an off-the-shelf notebook personal computer (PC) and the PMA, troubleshooting information is now at the mechanic’s fingertips (fig. 2). The PMA interface (fig. 3) is intuitive and requires minimal training, even for users with no computer experience. The PMA currently contains customized versions of the following documents: Fault isolation manual. Aircraft maintenance manual. Illustrated parts catalog. Wiring diagram manual–equipment list.
It also includes the following supporting documents: Combined index. Maintenance tips, service letters, and in-service activity reports. Dispatch deviation procedures guide for the 737-600/-700/-800/-900 and 777.
Future PMA expansion plans include addition of other manuals, such as the structural repair manual, wiring diagram manual, and system schematics manual, and integration with other Boeing digital products. Boeing will also continue to tailor the PMA to provide more efficient troubleshooting by using state-of-the-art diagnostic tools such as intelligent decision aids and intelligent graphics. Intelligent decision aids combine engineering design, mechanic knowledge, and in-service data to help diagnose problems on complex airplane systems. Intelligent graphics technologies provide improved navigation and text searching on illustrations. The PMA is currently available for the 737-300/-400/ -500/-600/-700/-800/-900, 747-400, 757, 767, and 777. It is planned to be available to support introduction of the 717 in 1999 and other Douglas-designed airplanes at a later date. More than 36 customers have ordered or received the PMA for one or more of their Boeing models. The primary requirement behind development of the PMA was the need to incorporate all technical documentation necessary for line maintenance in one application that can be carried to the airplane. Operators can also add to the PMA in-house information that they author. This popular feature allows operators to view their own minimum equipment list and other documents on the PMA. The Year 2000 (Y2K)-compliant PMA version 3.0 will be introduced in third quarter 1999.
Boeing is conducting a pilot program of the Portable Document Query System (PDQS). This system provides an excellent transition to digital technology for operators who wish to implement digital maintenance processes gradually. PDQS maintains the familiar look and feel of paper documents (fig. 4) but eliminates the space and time required to store and update paper documents. The PDQS pilot program began in late 1997 and will be complete by the end of first quarter 1999. More than a dozen customers are participating in the program worldwide and represent a cross-section of small, medium, and large operators. Some operators have networked PCs, while others use standalone PCs. The purpose of the pilot is to collect candid feedback from operators about their requirements, based on fleet type, so Boeing can provide them with the right data at the right place, at the right time. PDQS complements processes and procedures that are optimized for conventional documentation and is the ideal solution for standalone PCs. PDQS takes advantage of the industry-standard Adobe® Acrobat® portable document format (PDF) to provide the convenience of digital information storage. PDQS offers many document navigation and information retrieval features, including View/zoom. Search. Print. Copy/paste. Bookmarks. Thumbnails. Temporary revisions.
PDQS is a CD-ROM-based product compatible with Windows® 95 and is Y2K compliant. It requires a 486/33 or faster processor with 16-MB RAM or higher, a 3.5-in floppy drive, a 2X CD-ROM drive or faster, and a PostScript®-compatible printer. The PDQS pilot includes in-production and legacy data for the following models: 727, 737-100/-200/-300/ -400/-500/-600/-700/-800/ -900, 747-100/-200/-300/ -400, 777, and MD-80. Other models have not yet been included in the pilot program. The following documents will be available: Aircraft maintenance manual. Illustrated parts catalog. Structural repair manual.
Structural repair manuals for the 757, 767, 777, MD-11, and MD-80 are also available. Boeing is currently working to make all models available in PDQS format. Boeing created the PDQS pilot program in response to the customer requirement to provide legacy data on-line and in a single format that is applicable to all Boeing models.
Boeing also offers maintenance and repair documents in digital format for operators who choose to create their own systems for using the data. The data is offered in Standard Generalized Markup Language (SGML) format for the text and computer graphics metafile or consultative committee international telegraph and telephone (CCITT) group IV tag image file format (TIFF) image for the graphics, in conformance with ATA specification 2100 for digital data interchange. Summary
As modern commercial airplanes grow increasingly complex, operators will need faster, more efficient ways to access maintenance and operations information about them. In response, Boeing will continue to refine and enhance its line of existing digital products–including BOLD, PMA, PDQS, and SGML–and develop new products to meet emerging needs. By offering digital technologies that provide long-term value, Boeing can help operators achieve the following: Reduced overhead costs associated with managing technical information. Improved line maintenance and technical operations. Reduced parts inventory and associated management costs. Increased airplane availability.
Details on Boeing digital data products and services are available from Digital Data Customer Support by Phone: 206-544-9990 Email: [email protected] Web: http://www.boeing.com/digitaldata
Ricardo Benavides
Systems Analyst –
Portable Document Query
System Development
Technical Data
Products and Services
Boeing Commercial
Airplanes Roy Bruno
Manager –
Information Strategy
Technical Data
Products and Services
Boeing Commercial
Airplanes Denice Carnahan
Manager
Technical Data
Products and Services
Boeing Commercial
Airplanes Sam Mallos
Product Manager –
Boeing On-Line Data
Technical Data
Products and Services
Boeing Commercial
Airplanes Michael Maple
Senior Manger
Marketing
Boeing Commercial
Airplanes Steve Miller
Product Manager –
Portable Maintenance Aid
Technical Data
Products and Services
Boeing Commercial Airplanes
Fault-Isolation-Manual/b747-JT9D7A-fim.pdf at master · Stefanos423/Fault-Isolation-Manual
This commit does not belong to any branch on this repository, and may belong to a fork outside of the repository.
키워드에 대한 정보 fault isolation manual
다음은 Bing에서 fault isolation manual 주제에 대한 검색 결과입니다. 필요한 경우 더 읽을 수 있습니다.
이 기사는 인터넷의 다양한 출처에서 편집되었습니다. 이 기사가 유용했기를 바랍니다. 이 기사가 유용하다고 생각되면 공유하십시오. 매우 감사합니다!
사람들이 주제에 대해 자주 검색하는 키워드 RDR-4000 On-Wing Fault Isolation
- RDR-4000 On-Wing Fault Isolation
RDR-4000 #On-Wing #Fault #Isolation
YouTube에서 fault isolation manual 주제의 다른 동영상 보기
주제에 대한 기사를 시청해 주셔서 감사합니다 RDR-4000 On-Wing Fault Isolation | fault isolation manual, 이 기사가 유용하다고 생각되면 공유하십시오, 매우 감사합니다.