You are looking for information, articles, knowledge about the topic nail salons open on sunday near me how to get water out of hydraulic fluid on Google, you do not find the information you need! Here are the best content compiled and compiled by the Chewathai27.com team, along with other related topics such as: how to get water out of hydraulic fluid how to get water out of tractor hydraulic system, hydraulic fluid dryer, how to get water out of hydraulic systems, water in hydraulic fluid, water in hydraulic system tractor, milky hydraulic fluid in tractor, does hydraulic fluid absorb water, symptoms of water in hydraulic fluid
For emulsified or dissolved water, vacuum dehydration is the best option. These online or offline machines use heat (within a critical range as too high a heat will break down the oil) and vacuum technologies to remove water from oil.Water not only affects the components of a hydraulic or lubrication system, it can also change the fluid itself, physically and chemically. The physical properties most affected by the presence of water include: viscosity. lubricity and load-carrying characteristics.If saturation is still high (if the oil still looks cloudy), the oil will have to be changed once again. A second option to remove water is to use water-absorbing filter elements. Most standard return line filter assemblies are available with media to remove free water.
Contents
What happens when water gets in hydraulic fluid?
Water not only affects the components of a hydraulic or lubrication system, it can also change the fluid itself, physically and chemically. The physical properties most affected by the presence of water include: viscosity. lubricity and load-carrying characteristics.
Can you filter water out of hydraulic oil?
If saturation is still high (if the oil still looks cloudy), the oil will have to be changed once again. A second option to remove water is to use water-absorbing filter elements. Most standard return line filter assemblies are available with media to remove free water.
Does water sink in hydraulic fluid?
Zoller said that because water generally has a higher specific gravity than hydraulic fluid (exceptions do exist e.g. HFD-R), it tends to settle at the bottom of the reservoir when given sufficient resident time in a still environment.
How does water get into hydraulic oil?
Water contamination in hydraulic oil usually occurs when assembling a component, storing or transporting new oil. Also during maintenance, during machine operation, due to atmospheric humidity, or also due to internal chemical reactions, such as condensation.
How much water is acceptable in hydraulic oil?
The saturation level is the amount of water that can dissolve in the oil’s molecular chemistry and is typically 200-300 ppm for mineral hydraulic oil. Many references cite 1000 ppm (0.1%) as an acceptable water concentration for hydraulic oil.
How do I know if my hydraulic fluid has water in it?
Put a small amount of oil on a piece of tin foil, in a spoon or in a small metal container. Hold a small flame under the foil/spoon/container containing the fluid. If moisture is present then the fluid will crackle and pop as soon as it is heated up.
Why is my hydraulic fluid milky white?
Response: Oil turning milky white generally means that water is entering the reservoir. There are three primary causes of water entering a reservoir: If the unit is located outside and not protected by a shelter, the water can enter the system externally through worn O-rings, the breather cap, or a worn gasket.
What makes hydraulic oil milky?
Oil becomes cloudy when it’s contaminated with water above its saturation level. If you’ve worked with hydraulic equipment for any length of time, it’s likely that you’ve come across a hydraulic system with cloudy oil. Oil becomes cloudy when it’s contaminated with water above its saturation level.
Does hydraulic oil and water mix?
Most hydraulic fluid is oil-based, so we cannot forget the adage that oil and water do not mix well.
How do you know if your hydraulic fluid is bad?
- Abnormal Noise. Abnormal noise in hydraulic systems is often caused by aeration or cavitation. …
- High Fluid Temperature. …
- Slow Operation.
Does hydraulic fluid evaporate?
As temperatures increase, hydraulic fluid can begin to evaporate. As temperatures decrease, the fluid can freeze. This is one of the major concerns when we consider hydraulic fluid and climatic changes.
How do I know if my hydraulic fluid has water in it?
Put a small amount of oil on a piece of tin foil, in a spoon or in a small metal container. Hold a small flame under the foil/spoon/container containing the fluid. If moisture is present then the fluid will crackle and pop as soon as it is heated up.
Why does my hydraulic fluid look milky?
Oil becomes cloudy when it’s contaminated with water above its saturation level. If you’ve worked with hydraulic equipment for any length of time, it’s likely that you’ve come across a hydraulic system with cloudy oil. Oil becomes cloudy when it’s contaminated with water above its saturation level.
Water Contamination in Hydraulic and Lube Systems
- Article author: www.machinerylubrication.com
- Reviews from users: 47878
Ratings
- Top rated: 3.2
- Lowest rated: 1
- Summary of article content: Articles about Water Contamination in Hydraulic and Lube Systems Updating …
- Most searched keywords: Whether you are looking for Water Contamination in Hydraulic and Lube Systems Updating Water and oil don’t mix – it’s a well-known adage in the lubrication business. But what exactly does that mean? Yes, water contamination can be problematic, but how can water be measured? Can it be…
- Table of Contents:

Water in hydraulic oil: do you face this problem? – Poc Filtros
- Article author: www.pocfiltros.com.br
- Reviews from users: 11672
Ratings
- Top rated: 3.6
- Lowest rated: 1
- Summary of article content: Articles about Water in hydraulic oil: do you face this problem? – Poc Filtros Updating …
- Most searched keywords: Whether you are looking for Water in hydraulic oil: do you face this problem? – Poc Filtros Updating Responsible for lubricating and ensuring the movement of equipment and machinery parts, hydraulic oil (also called fluid) is considered essential in industry,
- Table of Contents:
Publicações recentes
ASSINE NOSSA NEWSLETTER
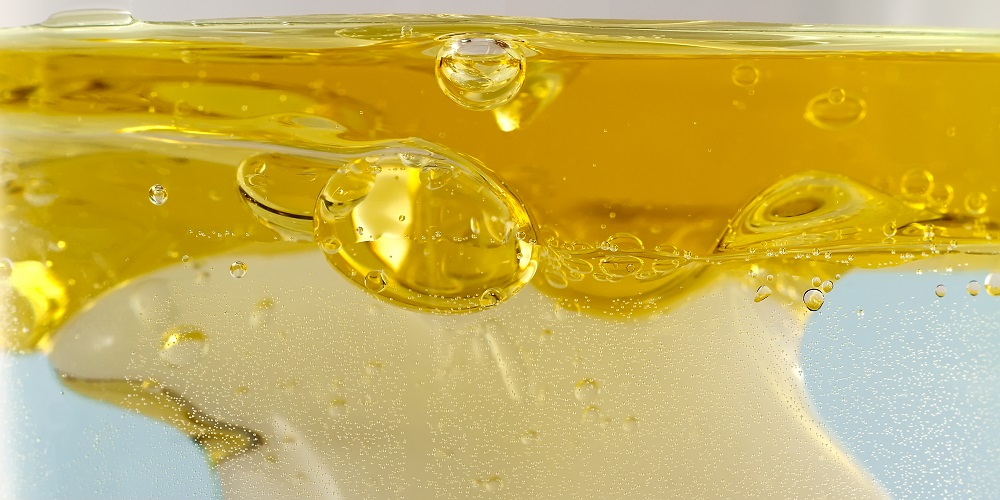
StackPath
- Article author: www.powermotiontech.com
- Reviews from users: 32097
Ratings
- Top rated: 4.3
- Lowest rated: 1
- Summary of article content: Articles about StackPath A simple but effective way to dry the oil is pass a small quantity (~4 SCFM) of desiccant dry air (-40°F dew point) through the reservoir continuously.This … …
- Most searched keywords: Whether you are looking for StackPath A simple but effective way to dry the oil is pass a small quantity (~4 SCFM) of desiccant dry air (-40°F dew point) through the reservoir continuously.This …
- Table of Contents:

How to Get Water Out of a Hydraulic System – White House Products, Ltd
- Article author: www.whitehouseproductsltd.com
- Reviews from users: 20088
Ratings
- Top rated: 3.6
- Lowest rated: 1
- Summary of article content: Articles about
How to Get Water Out of a Hydraulic System – White House Products, Ltd
Drain the oil from the system. · Clean out the reservoir and remove all deposits and sludge. · Replace the filters. · Flush the system with a lower viscosity oil. … - Most searched keywords: Whether you are looking for
How to Get Water Out of a Hydraulic System – White House Products, Ltd
Drain the oil from the system. · Clean out the reservoir and remove all deposits and sludge. · Replace the filters. · Flush the system with a lower viscosity oil. White House Products, Ltd. explains how to get water out of a hydraulic system after the water has contaminated the hydraulic oil, and the steps to follow. - Table of Contents:
Blog
How to Flush Water from a Hydraulic System

How to remove water from hydraulic oil
- Article author: www.hydraulicsupermarket.com
- Reviews from users: 14768
Ratings
- Top rated: 4.9
- Lowest rated: 1
- Summary of article content: Articles about How to remove water from hydraulic oil Water removal methods … Methods for removing free (unstable suspension) and emulsified (stable suspension) water include: … Vacuum distillation and headspace … …
- Most searched keywords: Whether you are looking for How to remove water from hydraulic oil Water removal methods … Methods for removing free (unstable suspension) and emulsified (stable suspension) water include: … Vacuum distillation and headspace … content article about removing water from hydraulic oilhydraulics technical information
- Table of Contents:

Error 403 (Forbidden)
- Article author: www.quora.com
- Reviews from users: 28538
Ratings
- Top rated: 4.4
- Lowest rated: 1
- Summary of article content: Articles about Error 403 (Forbidden) For industrial dehydration of oil , to separate water from Low vacuum dehydration unit are used. They give instant ROI ,else you have to sell your water mixed … …
- Most searched keywords: Whether you are looking for Error 403 (Forbidden) For industrial dehydration of oil , to separate water from Low vacuum dehydration unit are used. They give instant ROI ,else you have to sell your water mixed …
- Table of Contents:

See more articles in the same category here: Chewathai27.com/toplist.
How do you remove water from your hydraulic system?
It’s common knowledge that particulate contamination is unwanted in hydraulic systems. Contamination in hydraulic oil can damage mobile and industrial machinery. Of as much concern should be water in oil, as it too can lead to component failure.
Water in hydraulic fluid can be seen as free, dissolved or emulsified and can reduce hydraulic fluid lubricity, cause pitting against metal surfaces, degrade additives and accelerate oil aging. As a result, it is necessary to mitigate the presence of water in hydraulic systems. But before you can do that, first you must understand what types of water exist in a hydraulic system.
Free water is easily identifiable, as it can be visually seen if you pull oil from a system. This water separates clearly from the oil and can easily be decanted out of the reservoir because the specific gravity of most oils is less than 1.00.
Emulsified water is that which has blended with the oil so it can’t be decanted. Think of a bottle of salad dressing, in which the oil and vinegar/water are mixed upon shaking.
Dissolved water is the most difficult to identify and remove. This usually forms as the oil temperature increases — just as it is easier to dissolve salt in boiling water, so it is easier for hydraulic fluid to absorb water in hotter temperatures.
For emulsified or dissolved water, vacuum dehydration is the best option. These online or offline machines use heat (within a critical range as too high a heat will break down the oil) and vacuum technologies to remove water from oil. These systems will also remove particulates in the final stage.
Water Contamination in Hydraulic and Lube Systems
Water and oil don’t mix – it’s a well-known adage in the lubrication business. But what exactly does that mean? Yes, water contamination can be problematic, but how can water be measured? Can it be controlled? What are the best options for removing it? This article reviews the detrimental effects water contamination can have on hydraulic and other lubrication systems and explains ways to measure, control and remove water.
Figure 1. Saturation Curve for a Typical Turbine Lube Oil
States of Water
Water can be present in hydraulic fluids and other lubricants as either dissolved, emulsified or free water. The point at which the fluid cannot hold any more dissolved water is called the saturation level. If more dissolved water is present than the fluid can hold, the excess water (or free water) can be present either as a separate bulk water phase or as an emulsion.
Typically, oversaturated fluids appear cloudy. How much water a fluid can hold at saturation strongly depends on the fluid base stock type, the additive package, temperature and pressure. For instance, highly refined mineral oils with few additives hold little water before becoming saturated, about 100 parts per million (ppm) at 70°F.
At the other extreme, ester-based hydraulic fluids, such as those used in rolling mill applications, can have saturation levels of more than 3,000 ppm at 70°F and higher still at higher temperatures.
A saturation curve for a typical turbine lube oil (Figure 1), illustrates the relationship between temperature and saturation levels: If a system operates at 100°F and the fluid contains only dissolved water (100 ppm), then a drop to ambient temperature (70°F), as during a shutdown, would lead to the presence of free water in the system, because the saturation level at ambient conditions is less than 100 ppm.
On the other hand, ingression of water at operating temperature can also lead to the presence of free water, if the saturation level is reached or exceeded (at 100°F, this would be 200 ppm).
Figure 2. Relative Bearing Fatigue Life1
Sources of Water
Water can originate from a variety of sources. Examples of environmental ingression are rain leakage into external reservoirs, seepage through reservoir covers, access panels, breathers or worn seals, and condensation from air in reservoirs and other system areas. Water can also enter the fluid system from the process side, from leaky heat exchangers or coolers, or direct ingression of process water, such as cooling water, washdown water or steam.
Water ingression can be minimized with clever system design and good housekeeping, but it is difficult (and costly) to eliminate all sources of water entirely .
The Effects of Water
The presence of water in hydraulic fluids and lubricants can have wide-ranging effects on system components. Surface corrosion, probably the most obvious effect, is directly linked to the presence of free bulk water. Accelerated metal surface fatigue, such as in bearings, can be promoted even if all the water present in the fluid is dissolved. This was studied by Cantley in 19771, who investigated the effect of dissolved water on the fatigue life of tapered roller bearings.
Cantley developed an equation linking the relative bearing life and the water content of the lubricant used in the tests, an SAE 20 fluid containing rust- and oxidation-inhibiting additives. He showed that the bearing life could be extended by a factor of five, if the bearing lubricant contained only 25 ppm dissolved water compared to 400 ppm, close to the saturation level at the test temperature of 150°F. Figure 2 shows an adaptation of Cantley’s findings and illustrates the strong correlation between water content and relative bearing life.
Figure 3. Capacitive Water Sensor Technology
Other effects of water on fluid systems include reduced lubricating characteristics (lubricant film thickness, load-carrying ability, etc.), caused by the presence of water, which can lead to increased component wear2, and jamming of components due to ice crystals formed at low temperatures.
Water not only affects the components of a hydraulic or lubrication system, it can also change the fluid itself, physically and chemically. The physical properties most affected by the presence of water include:
viscosity
lubricity and load-carrying characteristics
power transfer characteristics (compressibility), especially in hydraulic systems
The chemical properties on which even small amounts of water can have a measurable effect are:
Thermo-oxidative stability. The reaction of oxygen with fluid basestock forms oxygenated compounds and is accelerated by heat and the presence of water. Metals, in the form of wear debris, often act as a catalyst. 3 Oxidation ultimately leads to higher viscosity and deposits, such as polymeric compounds or sludges.
Oxidation ultimately leads to higher viscosity and deposits, such as polymeric compounds or sludges. Hydrolysis, the decomposition of ester-based fluids as a result of heat and water, results in acids and alcohols, leading to increased corrosivity.
Deposition characteristics (soot, coking)
Premature additive depletion and additive precipitation, impacting fluid performance
Table 1. Vacuum Dehydration Process Comparison
Measuring Water Content in Fluids
There are two methods commonly used to express water content in hydraulic and lubrication fluids: The absolute content in ppm expresses the water content in parts per million (ppm) either by weight or volume. This method is typically used for water content specifications. Relative content expressed as percent of saturation indicates the fluid water content relative to its saturation level at a given temperature. It gives a clearer warning of impending formation of free water.
There are a variety of techniques to measure the quantity of water in hydraulic fluids and lubricants. The ultimate choice depends upon whether a quick assessment or a precise measurement is required. Some of the techniques that are typically applied include the following:
Of these, only Karl Fischer titration and the use of capacitive water sensors are useful for monitoring the water content, as these are more accurate quantitative methods.
The classic way of monitoring water content involves taking a representative sample and sending it to a laboratory for analysis, usually Karl Fischer titration. While this is a reliable and accurate method, the major drawback is the time lag between sampling and analysis results.
Capacitive Water Sensor
A capacitive water sensor, on the other hand, offers real-time monitoring and can be used as a control device. This instrument is a development of the air moisture sensor. It consists of a capacitive cell formed by sandwiching a dielectric polymer between electrodes (Figure 3). The lower electrode is deposited upon a ceramic substrate, which is impervious to moisture while the upper capacitor plate – a dielectric polymer – allows the transmission of water molecules.
Water molecules migrate into or out of this layer depending on the humidity of the polymer relative to the fluid. This alters its dielectric constant and thus the capacitance of the capacitor. This change in capacitance is then converted into a signal proportional to the saturation level of the fluid, in a percent range of zero to 100, where 100 percent saturation corresponds to the solubility limit of water in the fluid at the given temperature.
The water saturation levels can be related to the absolute water concentration (ppm) via an algorithm that uses fluid parameters determined for the specific fluid brand in conjunction with the fluid temperature via a calibration curve.
Karl Fischer Titration
The Karl Fischer method is used for the determination of the absolute water content in fluids as the reference for this conversion.4 This conversion requires the measurement of the fluid temperature at the water sensor, which is achieved with an integral resistance temperature detector (RTD) sensor. Note that the white dots in Figure 3 represent the porosity of the gold layer.
Figure 4. Selecting Proper Control Level
Setting Water Control Levels
For most industrial hydraulic and lubrication systems, a properly set control level, typically recommended at 50 percent saturation or less, minimizes the detrimental effects of water contamination. The control level should be selected, where possible, at the lowest anticipated system temperature, such as cold ambient during a shutdown.
As shown above, most fluids can hold less water at lower temperatures. To prevent the formation of free water at any given system condition, the control level should be set at least to the saturation level at the lowest expected temperature. This however does not account for ingression of water, which is why it is recommended to set the control level to 50 percent saturation, as this provides a safeguard against surface corrosion or loss of fluid characteristics (for example, lubricity, compressibility) due to the presence of free water.
In addition, this also keeps the absolute water content reasonably low, which slows all chemical reactions that depend on water as one of the reactants (for example, fluid hydrolysis and component surface degradation). Figure 4 illustrates this methodology.
Figure 5. Spray Nozzle Mass Transfer Purifier
Methods for Water Removal
An integral part of effective water control is the ability to efficiently remove water from the hydraulic or lubrication system. Some of the methods for water removal are discussed below.
Draining: Most hydraulic and lubrication systems have reservoirs sized to promote separation of contaminants; air rising to the free surface and water falling to the base. Regular draining of the reservoir is an inexpensive way to remove free water and automatic drain valves are available to reduce maintenance time.
Centrifuges separate water from fluids by centrifugal force and utilize differences in specific gravity between the fluid and the water for the separation. They remove free and some of the emulsified water (depending on the relative stability of the emulsion), but do not remove dissolved water. Centrifugal separation is suited for continuous decontamination of fluids, but requires excellent water demulsibility (oil/water separation). High capital and maintenance costs, as well as high power demand, are some of the drawbacks of this technology.
Coalescers separate water droplets from the fluid stream by arresting them on or near the surface of a filter or screen so that the droplets fuse together (coalesce) and grow to a size that allows them to fall to the bottom of the vessel where they can be extracted. Coalescers cannot separate dissolved water. Because coalescers rely on the interfacial tension between the water and the fluid phase, they tend to become ineffective in the presence of surface-active agents in the fluid. They also require fine upstream filtration to remove any particulate contamination, which could block and render the coalescer ineffective.
Absorbent filters remove free and emulsified water by super absorbent polymers impregnated in the filter matrix. Absorptive water removal is not well-suited when large amounts of water are present in the fluid and do not remove dissolved water or strongly emulsified water.
Vacuum dehydration purifiers are used to dry hydraulic fluids and lubricants by exposing them to a partial vacuum. Two technologies are available, flash distillation vacuum dehydration and mass transfer vacuum dehydration. While both processes utilize the concentration gradient between the fluid and the evacuated air to evaporate the water from the fluid, the flash distillation technology also applies heat to further boil off more water and operates at a higher vacuum. This makes flash distillation more efficient, as it removes more water from the fluid than a mass transfer device. Table 1 highlights the main differences between the two technologies.
The high temperature and vacuum employed in flash distillation devices can lead to loss of lower boiling base stock fractions and volatile additives, and can result in thermo-oxidative fluid degradation – serious drawbacks if fluid integrity needs to be preserved.
Mass transfer purifiers are recommended due to their minimal impact on fluid chemical and physical properties. A typical unit is shown in Figure 5. The fluid is fed into the vacuum chamber where it is spread into a thin film to reduce the path length for the water to reach the free surface and so be transferred to the air. This can be done in a number of ways.
n Figure 5, an aerosol mist is generated by pumping the fluid through spray nozzles. Alternative technologies commonly used are discharging the fluid over stacked rings, or onto a spinning disc. The vacuum in the vessel is about 20 percent atmospheric pressure and the air expands to about five times its original volume.
Therefore, if the air is at 100 percent relative humidity (100 percent saturation) then the evacuated air passing through the fluid mist is at 20 percent relative humidity and will pick up the water vapor from the fluid, until fluid and air water content are in equilibrium. Thus, depending on the vacuum, mass transfer purifiers, can remove all free water and up to 80 percent of dissolved water from the fluid.
When combined with a water sensor, mass transfer purifiers can be utilized to control water in hydraulic and lubrication systems continuously; however, not to the low percent saturation levels obtained with purifiers. (Vacuum) pressure is the main factor.
Conclusions
Water is a significant contaminant in hydraulic and lubrication fluid systems, resulting in degradation of system components and fluid.
Substantial cost savings can be gained from operating with dry fluids. Recommended saturation level: 50 percent or less for typical mineral oil-based fluids.
Water monitoring techniques must be accurate, repeatable and in real time so that increases in water content can be promptly rectified. On-line monitoring of water via a capacitive water sensor offers an optimal and cost-effective solution to monitoring.
Mass transfer vacuum dehydration purifiers are recommended for water removal from hydraulic fluids and lubricants because of the minimal impact on fluid properties.
Read more on water-in-oil contamination:
How to Measure Water In Oil
Options for Removing Water in Oil
Removing Water Contamination from Oil
Best Ways to Test for Water in Oil
References
R.E. Cantley. “The Effect of Water in Lubricating Oil on Bearing Fatigue Life.” ASLE Transactions, American Society of Lubrication Engineers, Volume 20, No. 3, p. 244-248, 1977; from a presentation at the 31st Annual ASLE Meeting, Philadelphia, Penn. J. Fitch and S. Jaggernauth. “Moisture, the Second Most Destructive Lubricant Contaminant and its Effect on Bearing Life.” P/PM Technology, p. 50-53, 1994. M. Weinschelbaum. “A Study of the Invisible but Measurable Particulate Contaminants in Hydraulic Systems.” Proceedings of the National Conference on Fluid Power, Volume XXIII, p. 265-277, 1969. K . Farooq and R. Fowler. “Comparison of Water Measurement Results in Polyol Ester-based Lubricant Fluids by the Coulometric Karl Fischer Method and a Thin Film Polymer Capacitive Water Sensor.” JOAP International Condition Monitoring Conference, April 3-6, 2000.
About the Author
About the Author
Remove water from hydraulic oil
Rain falls on mobile machinery, and unless you clean and garage your front-end loader like you do your hot-rod, your loader will get wet. When your loader gets wet, the opportunity for water to make its way into your hydraulic system exists. Water, especially “free” water not dissolved in the oil, can cause corrosion, modify viscosity, reduce lubrication and increase oxidation. If water is making its way into your hydraulic oil, you should address both the cause and the solution as quickly as possible.
Water can be ingested through cracked or missing seals, through breather caps or even through exposure to extended periods of excessive humidity. Removing water from the oil might be fruitless if you cannot first find its access point and repair the leak. First check the filler/breather assembly, especially the flange-mounted gasketed type. A cracked or broken gasket will allow pooled water to drip directly into the reservoir. You may want to consider adding a filler riser, which prevents pooled water from collecting around the gasket.
Another possible location of water entry is through a broken rod seal on a cylinder. If the seal and/or wiper are cracked, worn or missing, and if the cylinder is in a “cavitation” condition where the cylinder is being pulled out, a vacuum can suck in water. This effect is exacerbated on machines operating in heavy rain or even under water. It should go without saying, proper maintenance practices, such as regular inspections, will help prevent this type of ingression.
So you have water in your oil; now what? You have three options in removing water from oil. The first option is to just change the oil. Although you will miss some of the water-contaminated oil resting within the valves, motors, lines and cylinders outside the reservoir, changing the bulk of the oil will often reduce the overall water saturation once the machine has run for a while. If saturation is still high (if the oil still looks cloudy), the oil will have to be changed once again.
A second option to remove water is to use water-absorbing filter elements. Most standard return line filter assemblies are available with media to remove free water. By changing the standard element with a water-removing element, you can slowly trap the free water as the machine is running. If water content is excessive, it may take an impractical amount of time to remove free water, and a number of filter elements might also be required. It should be noted, these elements only trap free water, and do nothing to “dry” the humid oil.
Oil has humidity, just like air, and as long as saturation is less than 100%, water remains unseen and dissolved within the oil. Oil with 99% humidity is still a bad thing, as even a small drop in temperature can cause the water to “rain” out of the oil. Highly humid oil also promotes oxidation. The problem with humid oil is that it cannot be removed with filter elements such as with free water. Special machines that heat the oil while under vacuum, called vacuum dehydrators, are available at fluid power distributors and filtration companies. They can be rented, but often for the cost of changing your machine’s oil. They can also be purchased, but are very expensive and only make sense if you have a large fleet of machines being serviced regularly.
The best method to keep oil dry is through prevention. Well-maintained oil will last indefinitely, so ensure you inspect your machine often and make repairs when required.
So you have finished reading the how to get water out of hydraulic fluid topic article, if you find this article useful, please share it. Thank you very much. See more: how to get water out of tractor hydraulic system, hydraulic fluid dryer, how to get water out of hydraulic systems, water in hydraulic fluid, water in hydraulic system tractor, milky hydraulic fluid in tractor, does hydraulic fluid absorb water, symptoms of water in hydraulic fluid