당신은 주제를 찾고 있습니까 “a320 outflow valve – Airbus A320 Out Flow Valve Stuck Part 1“? 다음 카테고리의 웹사이트 https://chewathai27.com/you 에서 귀하의 모든 질문에 답변해 드립니다: https://chewathai27.com/you/blog. 바로 아래에서 답을 찾을 수 있습니다. 작성자 A320 Mentor Channel. 이(가) 작성한 기사에는 조회수 612회 및 좋아요 16개 개의 좋아요가 있습니다.
a320 outflow valve 주제에 대한 동영상 보기
여기에서 이 주제에 대한 비디오를 시청하십시오. 주의 깊게 살펴보고 읽고 있는 내용에 대한 피드백을 제공하세요!
d여기에서 Airbus A320 Out Flow Valve Stuck Part 1 – a320 outflow valve 주제에 대한 세부정보를 참조하세요
Airbus A320 Out Flow Valve Stuck Part 1
a320 outflow valve 주제에 대한 자세한 내용은 여기를 참조하세요.
Residual Cabin Pressure | Safety First | Airbus
pressurization, it is possible to refer to the cabin overpressure procedure. (Only on the A320 family, due to single outflow valve configuration – paper.
Source: safetyfirst.airbus.com
Date Published: 1/21/2022
View: 7296
4. Pressurisation
Pressurisation control is proved by an outflow valve and two safety valves, one to prevent over-pressurisation (>8.6 psi), the other to prevent …
Source: hursts.org.uk
Date Published: 3/16/2022
View: 8861
A320: Manual control of cabin – PPRuNe Forums
i just had a simulator event where we discussed the manual operation of the outflow valve. To be honest, i had some difficulties to …
Source: www.pprune.org
Date Published: 5/22/2022
View: 5023
A320 OUTFLOW VALVES – Hayward and Green
A320 OUTFLOW VALVES. H&G offer a full integrated support package on the A320 aircraft Cabin Outflow Valve system including guaranteed stock availability of the …
Source: www.haywardandgreen.com
Date Published: 6/4/2022
View: 6705
A320 TECHNICAL QUESTIONS (910) – TheAirlinePilots.com
Only after outflow valve is fully opened. Q 58: What is the function of the Pack Flow selector? A: Allows the pilot to increase pack flow but will not allow …
Source: www.theairlinepilots.com
Date Published: 4/26/2021
View: 6319
A320-Air_Conditioning_and_Pressurization.pdf – SmartCockpit
A320. SIMULATOR. FLIGHT CREW OPERATING MANUAL. CONTENTS … When the RAM AIR pushbutton is ON: The outflow valve opens about 50 %, proved …
Source: www.smartcockpit.com
Date Published: 7/18/2021
View: 4259
AIRCON/PRESSURIZATION/VENTILATION
There are Three modes of Pressurization on the A320. (a) AUTOMATIC … RAM AIR, the OutFlow Valve opens about 50% proved that Delta P is less than 1 Psi.
Source: theflyingengineer.com
Date Published: 9/4/2022
View: 862
주제와 관련된 이미지 a320 outflow valve
주제와 관련된 더 많은 사진을 참조하십시오 Airbus A320 Out Flow Valve Stuck Part 1. 댓글에서 더 많은 관련 이미지를 보거나 필요한 경우 더 많은 관련 기사를 볼 수 있습니다.
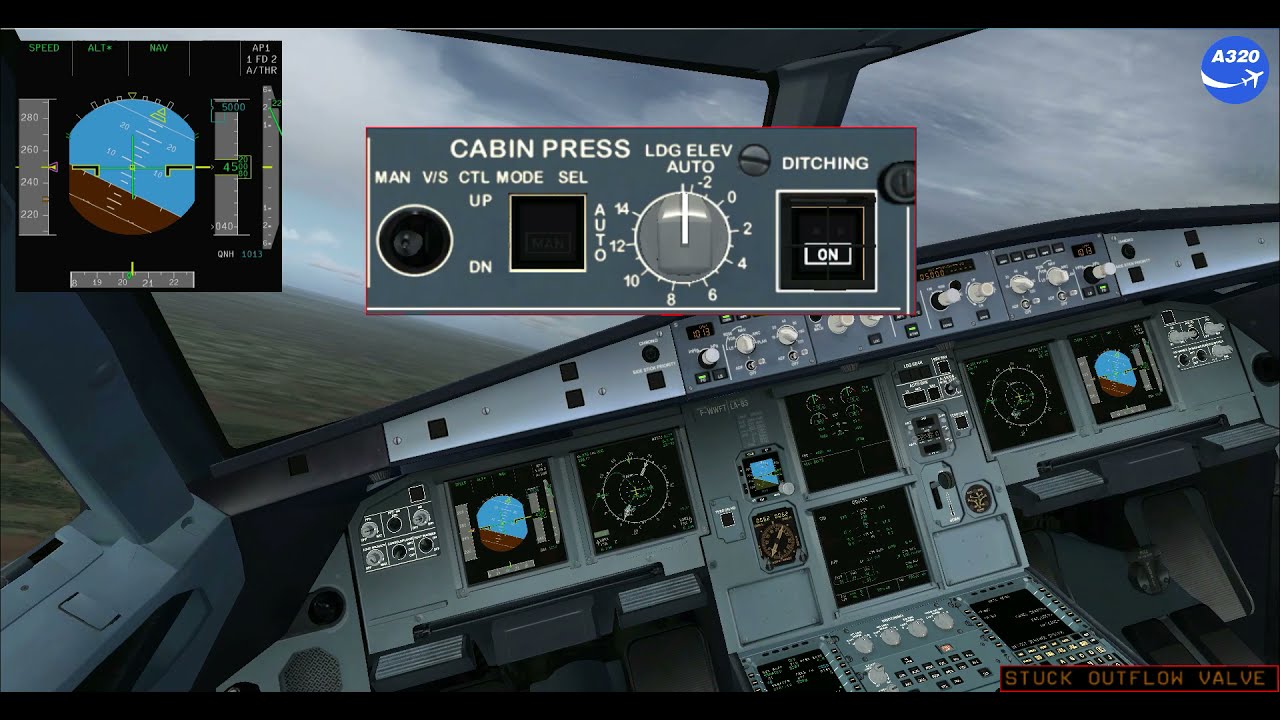
주제에 대한 기사 평가 a320 outflow valve
- Author: A320 Mentor Channel.
- Views: 조회수 612회
- Likes: 좋아요 16개
- Date Published: 2021. 7. 2.
- Video Url link: https://www.youtube.com/watch?v=SuzMnOmDANw
What is an outflow valve?
Outflow valve: Allows for air to exit the cabin at a controlled rate which results in the cabin becoming pressurized. Safety/Dump Valve: If the outflow valve fails, the dump valve will release excess pressure (can be manually activated) by a squat switch to prevent pressurization on the ground.
What is the cabin outflow valve?
To keep the aircraft cabin pressure at a safe level, any incoming air is held within the cabin through the use of an automatic outflow valve. This valve opens and closes on a regular basis to release the incoming air at the rate regulated by pressure sensors.
Why do we need two outflow valves?
Larger aircraft often have two outflow valves. The valves are automatically controlled by the aircraft’s pressurization system. If higher pressure is needed inside the cabin, the door closes. To reduce cabin pressure, the door slowly opens, allowing more air to escape.
What is the function of the cabin outflow valve on a pressurized aircraft?
All exhaust air is dumped to atmosphere via an outflow valve, usually at the rear of the fuselage. This valve controls the cabin pressure and also acts as a safety relief valve, in addition to other safety relief valves.
What is an outflow valve and what is its function?
A valve in the aircraft pressurization system that controls the pressure inside the cabin by controlling the amount of air allowed to flow out of the cabin. It is a type of pressure maintenance valve.
Where is the location of out flow valve?
Location – The outflow valves are located in the aft cabin at the bottom of the aft pressure bulkhead. Operation – The primary outflow valve is electrically controlled by the cabin pressurization controller and pneumatically driven.
Can a pilot depressurize the cabin?
Padfield said depressurization can happen quickly or slowly. If quickly, there is little time to react, although pilots are trained to keep an eye on cabin pressure and adjust the plane’s oxygen levels accordingly.
What control changes the position of the outflow valve?
Cabin Pressure Controller
The regulator controls the position of the outflow valve(s) normally located at the rear of the aircraft pressure vessel.
What are the purposes of positive and negative cabin pressure relief valves?
The spring-loaded relief valve opens inward to allow ambient air to enter the cabin. Too much negative pressure can cause difficulty when opening the cabin door. If high enough, it could cause structural damage since the pressure vessel is designed for cabin pressure to be greater than ambient.
Why are planes pressurized to 8000 feet?
The higher the altitude, the less oxygen there is in the air and the lower the overall air pressure is. If flights were not pressurized, passengers would be at risk of various physiological aliments. Because of this, federal regulations require that all commercial flights over 8,000 feet be pressurized.
How high can you fly without oxygen?
For Part 91 General Aviation operations the required flight crew must use supplemental oxygen for any portion of the flight that exceeds 30 minutes above a cabin pressure altitude of 12,500 feet mean sea level (MSL) up to and including 14,000 feet (MSL).
How high can you fly without pressurization?
Federal Aviation Regulations say that without pressurization, pilots begin to need oxygen when they fly above 12,500 feet for more than 30 minutes, and passengers have to use it continuously above 15,000.
What is the function of negative pressure relief valve?
The negative pressure relief valve prevents the generation of subatmospheric pressures in the circuit as a result of a discrepancy between the fresh gas flow and the gas evacuation rate. The ideal valve will open at a small negative pressure, and immediately permit a high gas inflow.
How is cabin pressurization controlled?
Operation – The pressurization controller automatically controls the cabin altitude (pressure) and cabin altitude rate of change by varying the position of the outflow valves based on the following inputs: Landing field altitude, Cabin pressure, Airplane altitude, Squat switch position and Throttle position.
What is SRV valve?
Safety relief valve (SRV): an automatic system that relieves by static pressure on both gas and liquid. Pilot-operated safety relief valve (POSRV): an automatic system that relieves on remote command from a pilot, to which the static pressure (from equipment to protect) is connected.
How is cabin pressurization controlled?
Operation – The pressurization controller automatically controls the cabin altitude (pressure) and cabin altitude rate of change by varying the position of the outflow valves based on the following inputs: Landing field altitude, Cabin pressure, Airplane altitude, Squat switch position and Throttle position.
How does cabin pressurization work?
How airplanes are pressurized. All airplane cabins are pressurized to simulate the amount of pressure felt at 8,000 feet. Pressurization happens via the engines, which compress incoming air, heat it up, and then divert some of that hot compressed air to the cabin.
What is cabin pressurization system?
Put simply, cabin pressurization is a process in which conditioned air is pumped into and exhausted out of the cabin of an aircraft to keep the pressure in the cabin between sea level and 8000 feet.
Aircraft Pressurization
Pilot Handbook of Aeronautical Knowledge,
Airplane Pressurization System Pilot Handbook of Aeronautical Knowledge,
Airplane Pressurization System The pressurization of an aircraft to allow high altitude operations due to loss in pressure and protecting occupants against the effects of hypoxia In a typical pressurization system, the cabin, flight compartment, and baggage compartments are incorporated into a sealed unit capable of containing air under a pressure higher than outside atmospheric pressure High altitude operations allow for lower fuel consumption for a given airspeed (efficiency) and avoidance of weather and turbulence above storms Oxygen masks prevent hypoxia but they do not help with sinus and ear blocks or decompression sickness, also oxygen masks can be uncomfortable Pressurized air is generally obtained from an aircrafts turbocharger or compressor section of turbine aircraft Piston-powered aircraft may use air supplied from each engine turbocharger through a sonic venturi (flow limiter)
Gas-turbine-powered aircraft use air supplied from the compressor stage of the engine which is conditioned for the cabin A cabin pressurization system typically maintains a cabin pressure altitude of ~8,000′ at the maximum designed cruising altitude of an aircraft [ Figure 1: ] This prevents rapid changes of cabin altitude that may be uncomfortable or cause injury to passengers and crew
It does however, mean pressure inside the body exceeds that outside the body causing bloating and being overall uncomfortable
Lower cabin altitudes reduce this effect, but are only available to aircraft manufacturered to withstand the stresses, like the 787 composite bodied aircraft The pressurization system permits a reasonably fast exchange of air from the inside to the outside of the cabin to eliminate odors and to remove stale air Definitions: Aircraft altitude: the actual height above sea level at which the aircraft is flying
the actual height above sea level at which the aircraft is flying Ambient temperature: the temperature in the area immediately surrounding the aircraft
the temperature in the area immediately surrounding the aircraft Ambient pressure: the pressure in the area immediately surrounding the aircraft
the pressure in the area immediately surrounding the aircraft Cabin altitude: cabin pressure in terms of equivalent altitude above sea level
cabin pressure in terms of equivalent altitude above sea level Differential pressure: the difference in pressure between the pressure acting on one side of a wall and the pressure acting on the other side of the wall. In aircraft air-conditioning and pressurizing systems, it is the difference between cabin pressure and atmospheric pressure Pilot Handbook of Aeronautical Knowledge,
Standard Pressure Chart Pilot Handbook of Aeronautical Knowledge,
Standard Pressure Chart The cabin pressure control system provides cabin pressure regulation, pressure relief, vacuum relief, and the means for selecting the desired cabin altitude in the isobaric and differential range In addition, dumping of the cabin pressure is a function of the pressure control system A cabin pressure regulator, an outflow valve, and a safety valve are used to accomplish these functions The cabin pressure regulator controls cabin pressure to a selected value in the isobaric range and limits cabin pressure to a preset differential value in the differential range [ Figure 2 ] When an aircraft reaches the altitude at which the difference between the pressure inside and outside the cabin is equal to the highest differential pressure for which the fuselage structure is designed, a further increase in aircraft altitude will result in a corresponding increase in cabin altitude Differential control is used to prevent the maximum differential pressure, for which the fuselage was designed, from being exceeded This differential pressure is determined by the structural strength of the cabin and often by the relationship of the cabin size to the probable areas of rupture, such as window areas and doors The cabin air pressure safety valve is a combination pressure relief, vacuum relief, and dump valve The pressure relief valve prevents cabin pressure from exceeding a predetermined differential pressure above ambient pressure The vacuum relief prevents ambient pressure from exceeding cabin pressure by allowing external air to enter the cabin when ambient pressure exceeds cabin pressure The flight deck control switch actuates the dump valve When this switch is positioned to ram, a solenoid valve opens, causing the valve to dump cabin air to atmosphere The degree of pressurization and the operating altitude of the aircraft are limited by several critical design factors Primarily, the fuselage is designed to withstand a particular maximum cabin differential pressure Several instruments are used in conjunction with the pressurization controller The cabin differential pressure gauge indicates the difference between inside and outside pressure This gauge should be monitored to assure that the cabin does not exceed the maximum allowable differential pressure A cabin altimeter is also provided as a check on the performance of the system In some cases, these two instruments are combined into one A third instrument indicates the cabin rate of climb or descent A cabin rate-of-climb instrument and a cabin altimeter are illustrated in [ Figure 3 ] Cabin Pressure Altitude: Cabin pressure altitude is the equivalent altitude inside of the cabin
Maintianing cabin pressure inside of the cabin reduces physical strain on the pilot and passenger’s bodies Cabin Differential Pressure: The difference in pressure between the cabin and the outside air
Sonic Venturi: Limits the amount of air taken from turbo by accelerating air to sonic speeds creating a shock wave which acts as a barrier
This air is very hot and must be run through a heat exchanger to cool it
After being cooled, air is sent to the cabin via heating and ventilation outlets
Regulation: Outflow valve: Allows for air to exit the cabin at a controlled rate which results in the cabin becoming pressurized
Allows for air to exit the cabin at a controlled rate which results in the cabin becoming pressurized Safety/Dump Valve: If the outflow valve fails, the dump valve will release excess pressure (can be manually activated) by a squat switch to prevent pressurization on the ground
If the outflow valve fails, the dump valve will release excess pressure (can be manually activated) by a squat switch to prevent pressurization on the ground Vacuum Relief Valve: Allows ambient air into the cabin
Instrumentation: Cabin/differential Pressure Indicator: Works like an altimeter but has two references, outside air pressure and cabin pressure
Works like an altimeter but has two references, outside air pressure and cabin pressure Cabin Rate of Climb Indicator: Indicates the rate of change in cabin pressure
Indicates the rate of change in cabin pressure Pilot Handbook of Aeronautical Knowledge,
Pressurization Instruments Cabin Pressurization Controls: Basic Preset: When cabin pressure reaches a preset value (about 8,000′)
When cabin pressure reaches a preset value (about 8,000′) The Outflow Valve begins closing until max cabin differential pressure is reached and then cabin altitude begins to climb
Cabin rate of climb will be slightly less than airplane rate of climb due to higher air density in the cabin
Cabin Pressure Control: Pilot selects altitude pressurization begins and can preset the rate at which the cabin pressurizes
Pilot selects altitude pressurization begins and can preset the rate at which the cabin pressurizes Differential Range System: Works to prevent exceeding differential pressure limits
Works to prevent exceeding differential pressure limits Isobaric Range: Works to maintain a preset cabin pressure Cabin Decompression: Decompression: the inability of the aircraft’s pressurization system to maintain its designed pressure differential
the inability of the aircraft’s pressurization system to maintain its designed pressure differential Problems can be caused by a malfunction in the pressurization system or structural damage to the aircraft
The primary danger of decompression is hypoxia
Quick, proper utilization of oxygen equipment is necessary to avoid unconsciousness
Another potential danger that pilots, crew, and passengers face during high altitude decompressions is evolved gas decompression sickness
This occurs when the pressure on the body drops sufficiently, nitrogen comes out of solution, and forms bubbles that can have adverse effects on some body tissues
Decompression caused by structural damage to the aircraft presents another type of danger to pilots, crew, and passengers being tossed or blown out of the aircraft if they are located near openings
Individuals near openings should wear safety harnesses or seat-belts at all times when the aircraft is pressurized and they are seated
Structural damage also has the potential to expose them to wind blasts and extremely cold temperatures
Rapid descent from altitude is necessary if these problems are to be minimized
Automatic visual and aural warning systems are included in the equipment of all pressurized aircraft
Gradual Decompression: Slow decompression is dangerous because it may be hard to detect until after you are already experiencing the effects of hypoxia. Annunciation lights are installed to aid in detection
Rapid Decompression: A change in cabin pressure in which the lungs decompress faster than the cabin, resulting in no likelihood of lung damage Decompression in 1-10 seconds usually associated with major structural damage Cabin will fill with fog because of immediate condensation of water vapor The cabin will become extremely cold because of immediate loss of heated air Also at high altitudes you will only have up to 12 seconds of useful consciousness Rapid decompression decreases the period of useful consciousness because oxygen in the lungs is exhaled rapidly, reducing pressure on the body This decreases the partial pressure of oxygen in the blood and reduces the pilot’s effective performance time by one-third to one-fourth its normal time For this reason, an oxygen mask should be worn when flying at very high altitudes (35,000′ or higher) It is recommended that the crew-members select the 100% oxygen setting on the oxygen regulator at high altitude if the aircraft is equipped with a demand or pressure demand oxygen system
Explosive Decompression: Refers to a sudden marked drop in the pressure of a system that occurs faster than the lungs can decompress Generally it results from some sort of material fatigue or engineering failure, causing a contained system to suddenly vent into the external atmosphere Lungs take about 0.2 seconds to decompress without restriction (masks) Anything less than 0.5 seconds is considered explosive decompression Associated with explosive violence and is potentially dangerous During an explosive decompression, there may be noise, and one may feel dazed for a moment The rapid loss in pressure may cause a cloud to form due to the rapid drop in temperature and change in relative humidity Dust or loose objects may become airborne and move around the cabin
If faced with a decompression event, take care of yourself, the airplane, and your passengers, in that order Decompression Sickness: When an occupant of any aircraft is observed or suspected to be suffering from the effects of DCS, 100% oxygen or available aircraft oxygen will be started and the pilot shall immediately descend to the lowest possible altitude and land at the nearest civilian or military installation suitable for safe landing and obtain qualified medical assistance
Consideration shall be given to whether the installation is in proximity to a medical re-compression chamber
It is extremely important to be able to recognize symptoms and convey this and the altitude profile to medical support
Pressurization System Errors: Cabin does not decompress:
Outflow valve is blocked, a safety valve should decompress the aircraft, triggered with WOW (Weight on Wheels)
Cabin does not pressurize:
Outflow valve is stuck open
Conclusion: Despite the 8,000 cabin pressure altitude standard, manufacturers like Gulfstream have lowered cabin pressure altitude further as material science advancements withstand increased physical stresses See: Gulfstream G700 to Offer Lower Cabin Altitude
Still looking for something? Continue searching:
References: Federal Aviation Administration – Pilot/Controller Glossary
CFI Notebook.net – Pilot Information Manual
Pilot Handbook of Aeronautical Knowledge (6-32) Pressurized Aircraft Copyright © 2022 CFI Notebook, All rights reserved. | Privacy Policy | Terms of Service | Sitemap | Patreon | Contact Facebook
YouTube
Aircraft Pressurization: A Beginner’s Guide to How Aircraft Cabin Pressure Works
How Does Aircraft Pressurization Work?
We often take flying for granted and never pay a second thought as to how we’re able to function so high up in the air. This article will delve into how an aircraft’s cabin pressurization system makes it possible to breathe oxygen comfortably while flying and why testing equipment is a necessary part of your ground support equipment fleet.
Keeping passengers safe and comfortable at over 30,000 feet is an accomplishment airplane manufacturers have spent decades trying to master. As humans, we function best at sea level. But airplanes are at their best when at great heights with thin and smooth air.
As you can see, this creates quite the quandary. So, airplane manufacturers created a cabin pressurization system to keep passengers and employees safe and comfortable while in the air. But how aircraft cabin pressure works can be a little confusing. So, we’re answering a few of the most common questions that arise when discussing the ins and outs of aircraft pressurization.
Where Does Pressurized Air Come From?
The answer to this first question is a little complex as it can vary across aircraft manufacturers, so let’s dive in.
Older piston-powered airliners used to use electric air compressors to pump outside air into the cabin of the airplane. However, this tended to add a lot of extra weight to the aircraft. Jetliners then began to use bleed air from the engines to spin the turbo compressors, which then pumped outside air into the cabin. Today, most modern airplanes use bleed air from the engines’ compressors to properly pressurize the cabin.
But How Does Aircraft Cabin Pressure Work?
So, we’ve answered where pressurized air comes from, but how does it actually work? Buckle up.
The engine’s compressor contains a series of spinning blades that draw in fresh air from outside the plane. The air becomes extremely hot as it’s compressed. It then enters the engine’s combustion chamber where it combines with fuel and is burned. Then, the expanded gasses flow through the engine’s turbine blades (powering the compressor blades) and exit the engine, creating thrust.
The bleed air, which is clean, hot air, is taken from the compressor prior to mixing with any fuel or exhaust gasses. Bleed air can help with the following:
– Cabin pressurization
– Wing and engine ice protection
– Air-driven hydraulic pumps
– Engine starter motors
While some of the already-hot bleed air is used for things like wing deicing, cabin-bound bleed air must be cooled first. The cooling is conducted within an intercooler, which is a device similar to that of a car radiator. The intercooler works by shedding the heat to ambient air. The air then travels to the belly of the plane where it is cooled even further through the use of air packs, which use an air cycle machine (a refrigeration unit). This surprisingly simple air conditioner utilizes air packs to compress incoming air to heat it before sending it to an additional intercooler to dump the heat outside of the plane. This air then expands through the expansion turbine, resulting in cool air.
At this point, the cooled air is ready to mix with the recirculated cabin air through the use of fans. Automatic systems work throughout the flight to regulate the mixture of the engine’s heat and the cold from the air packs. To keep the aircraft cabin pressure at a safe level, any incoming air is held within the cabin through the use of an automatic outflow valve. This valve opens and closes on a regular basis to release the incoming air at the rate regulated by pressure sensors. The outflow valve also acts as an exit hatch for old, smelly air to vacate the plane.
How Do Pilots Control Pressurization?
This is a semi-trick question. During preflight checks, the pilot should turn on a display that will show the altitude of the landing airport. But after this, pilots won’t typically do anything related to cabin pressurization for the remainder of the flight. All planes, as we’ve already mentioned, have an automatic mode that controls the outflow valve.
Keep in mind that pilots can override the automatic modes in the case of a malfunction. The manual mode will allow the pilot to then adjust the position of the outflow valve.
Are There Any Side Effects?
While there are no long-term risks to being inside a pressurized aircraft cabin, there are some odd side effects you may notice while on the plane. As the pressurized air has low humidity, you will become dehydrated very quickly. So, you’ll want to stay hydrated by drinking plenty of water.
Dehydration can increase when drinking alcohol. So, if passengers decide to drink on a fight, they should be sure to drink water and have something to eat as well.
Aircraft pressurization also reduces your sense of taste and smell. A Lufthansa commissioned study found it can decrease these senses by as much as 30%. This is why extra spices or flavorings are often added to food on airplanes.
Why Can’t The Plane Simply Fly Lower?
You may ask yourself, why can’t the plane simply fly lower to avoid the hassle of creating perfect aircraft cabin pressure ? While airplanes can certainly fly below 10,000 feet where the atmospheric pressure is ideal, there are some operational drawbacks to doing this for an entire flight. For one, there are many mountain ranges that are higher than 10,000 feet. In addition to this, most bad weather can be found at lower altitudes, so pilots typically want to avoid this. And in terms of efficiency, turbofan engines are extremely inefficient when used at lower altitudes and ground speeds.
How Can Aircraft Pressurization Be Tested?
To ensure an airplane is safely pressurized prior to a flight, you’ll need to test the pressure. To do this, make sure to use the proper airplane cabin pressure testing equipment. These pieces of equipment are vital players in your GSE fleet and help to maintain the safety standards for any airplane coming to or leaving your airport. The following are just a few of the cabin pressure testing equipment options available from Tronair.
– A leak fluid dispenser can detect if air is escaping when the cabin is pressurized.
– A cabin pressure test unit (also available as a portable unit), in addition to checking for leaks, can test the pressurization components of the airplane, such as the outflow valves, gauges and door seals.
Let Tronair Help Find the Aircraft Cabin Pressure Testing Equipment for Your Needs
At Tronair, we work tirelessly to offer our customers a diverse and unparalleled selection of GSE products. We understand how important safety is when it comes to aircraft pressurization and air travel overall — it’s why we create testing equipment you can count on. Shop our high-quality selection of cabin pressure testing equipment, leak fluid dispensers and more. Have a question or need a quote? Our customer service department and sales team are here to help with any questions you may have regarding our extensive range of products. Contact us today.
Aircraft Pressurization Beginner’s Guide
How and why are airplanes pressurized?
It’s easy to take flying for granted. We hop on-board a comfy airliner and fly high in the stratosphere without giving breathing a second thought. The aircraft’s pressurization system makes it possible. Here’s how the magic works…
Hypothetical experiment: If you place a scale in a vacuum chamber and compare the weight of a filled balloon with an empty one, you’ll see that air has mass.
Earth’s atmosphere is about 300 miles thick. At sea level, our bodies are subjected to about 14.7 pounds of pressure from this tall column of air. I’ll bet you don’t even notice! For animals roaming the earth’s surface, a 14.7 psi atmosphere provides the perfect amount of oxygen.
As we climb in altitude, the amount of air pressure acting on us decreases rapidly. You notice the decrease when your ears pop while driving up a mountain or riding a fast elevator. Although the atmosphere is 300 miles thick, most of the air molecules are squashed down to within a few thousand feet of the earth’s surface.
Denver is fine. Going higher spells trouble.
As we climb higher, air molecules are spread farther apart. When we breathe, our lungs take in less air, and less oxygen. Folks living in Denver, Colorado (5600 ft) are quite happy breathing the lower, 12 psi atmosphere. Climbing to a higher altitude, though, and the pressure drops really fast.
At 18,000 feet, the atmospheric pressure is down to 7.3 psi, about half the sea-level pressure. There just isn’t enough oxygen in a breath of air to adequately supply the brain. At this pressure, a healthy adult has only 20-30 minutes of useful consciousness.
Airliners fly between 30,000 and 43,000 feet. At those altitudes the atmosphere provides less than 4 psi of pressure. If you tried breathing at that altitude, your useful consciousness would be less than a minute (followed soon after by death).
To survive high altitudes, occupants of an aircraft need help breathing. The solution is to pump air into the airplane so the interior pressure is high enough to keep the humans happy.
Why bother with pressurization? Why not fly down low?
Airplanes can certainly fly below 10,000 feet where the atmospheric pressure is a comfy 10 psi or higher, but it has some drawbacks:
It’s tough to cross a 14,000 foot mountain range at 10,000 ft.
Most bad weather is at lower altitudes.
Turbofan engines are very inefficient down low.
Aircraft ground speeds are slower at lower altitudes.
If you want a fast, smooth ride in a fuel efficient airplane that can fly over a mountain range, we need to pressurize!
How does a pressurization system work?
The airplane body (fuselage) is a long tube capable of withstanding a fair amount of differential air pressure; think of it like a big plastic soda bottle. In theory, we could seal the bottle so, as the airplane climbs, the interior air pressure would stay the same. We can’t do that because it’s hard to perfectly seal a huge airplane fuselage. Even if we could, the passengers would quickly use up the available oxygen. And just imagine the smell inside a perfectly sealed tube on a long flight! Clearly, a big sealed soda bottle won’t work for us without some modification.
To solve the problems, pressurization systems constantly pump fresh, outside air into the fuselage. To control the interior pressure, and allow old, stinky air to exit, there is a motorized door called an outflow valve located near the tail of the aircraft. It’s about the size of a briefcase and located on the side or bottom of the fuselage. Larger aircraft often have two outflow valves. The valves are automatically controlled by the aircraft’s pressurization system. If higher pressure is needed inside the cabin, the door closes. To reduce cabin pressure, the door slowly opens, allowing more air to escape. It’s one of the simplest systems on an aircraft.
One of the benefits of a pressurization system is the constant flow of clean, fresh air moving through the aircraft. The air inside the airplane is completely changed every two or three minutes making it far cleaner than the air in your home or office.
Pressurization systems are designed to keep the interior cabin pressure between 12 and 11 psi at cruise altitude. On a typical flight, as the aircraft climbs to 36,000 feet, the interior of the plane “climbs” to between 6000-8000 feet.
Why not keep the cabin at 14.7 psi to simulate sea-level pressure and maximize comfort? The aircraft must be designed to withstand differential pressure, that’s the difference between the air pressure inside and outside the aircraft. Exceeding the differential pressure limit is what makes a balloon pop when it’s over inflated. The greater the differential pressure, the stronger (and heavier) the airplane must be built. It’s possible to build an aircraft that can withstand sea-level pressure during cruise, but it would require a significant increase in strength and weight. A 12 psi cabin is a good trade-off.
Outflow Valve Trivia: If you look at pictures of airliners taken prior to 1990, you might see brown stains around the outflow valve. The stains are from tobacco smoke. Airlines were thrilled when the industry banned smoking. Tar and nicotine gummed up valves, instruments, and sensors causing thousands of dollars a year in damage. Tobacco is really nasty stuff.
Protecting the Fuselage from Pressurization Problems
Two types of mechanical devices are installed on the fuselage to protect the pressurized section of the aircraft against excessive pressure differential.
Positive Pressure Relief Valves
Every pressurized aircraft has a maximum pressure differential limit. Exceeding this limit (pumping too much air pressure into the fuselage) can cause damage – even blow out doors and windows. To protect the aircraft from over pressurizing, positive pressure relief valves are installed. The devices (sometimes called butterfly valves) are spring-loaded to vent excess air pressure when cabin pressure exceeds the maximum limit.
Negative Pressure Differential Relief Doors
Negative pressure differential means the pressure outside the cabin is greater than the pressure inside the cabin. This situation could occur during a rapid descent. Negative pressure is bad because it pushes inward on doors and windows. These components are not designed for this type of force.
Again, spring-loaded devices are used to protect the fuselage from damage. Air pressure of less than 1.0 psi against the outside of the doors causes them to open inward against the spring load, venting air into the fuselage to equalize the pressure.
Where does pressurized air come from?
Electric Compressors
Old piston powered airliners, like the Boeing Stratocruiser, used electric air compressors to pump fresh, outside air into the cabin. This system worked well, but the compressors added a lot of weight to the aircraft.
Turbocompressors
Early jetliners, like the Douglas DC-8 and Boeing 707 used bleed air from the engines to spin turbocompressors. The turbocompressors then pumped fresh outside air into the cabin.
Engine Bleed Air
Most modern airliners use bleed air from the compressor section of the engines to pressurize the cabin. This very hot air must be cooled to a comfortable temperature before it’s directed into the cabin.
Electric Compressors (Again!)
The new Boeing 787 Dreamliner brings back the electric compressor. The 787’s electrical system powers compressors, just like on the old Stratocruiser. Advances in technology make this system far more efficient than it’s predecessor from the 1950’s.
What is bleed air? A jet engine has three main sections: compressor, combustion, and turbine/exhaust. The compressor is at the front of the engine. A series of spinning blades draws in fresh, outside air. As the air is compressed, it becomes very hot. Remember high school physics? As a gas is compressed, its temperature rises. The hot, compressed air then enters the combustion chamber where it is mixed with fuel and burned. The expanded gasses continue through turbine blades which power the compressor blades before exiting the engine producing thrust. Bleed air is fresh, clean, hot air taken from the compressor section of the engine before it is mixed with fuel or exhaust gasses. Common uses for hot bleed air are wing and engine ice protection, cabin pressurization, engine starter motors, and air driven hydraulic pumps.
How do pilots control the pressurization?
It’s really, really easy. The cabin altitude control panel on the 757 and 767 is super simple. During preflight checks, pilots turn the “LDG ALT” knob to display the altitude of the landing airport. That’s it! We don’t touch it for the remainder of the flight. The automatic mode takes care of the outflow valve for us.
The remaining indicators and knobs are for redundancy in case of a malfunction. There are two separate automatic modes. A manual mode allows us to adjust the position of the outflow valve should both auto systems fail. Pressurization systems work great and rarely cause any trouble.
Effects Of Flying In A Pressurized Cabin
The air inside an aircraft cabin is very low in humidity. On a long flight it’s important to drink plenty of water to stay hydrated. When the flight attendant offers you a bottle of water, drink it. You may not notice that you’re dehydrated.
Alcohol consumption: Dehydration increases the effects of alcohol on your body. To make matters worse, alcohol increases dehydration; it’s a double-whammy. If you choose to drink alcohol on a flight, be sure to drink plenty of water and have something to eat while enjoying your cocktail. Don’t be that guy. Drink extra-responsibly when flying.
Does this food taste bland? Yes! There’s a good chance your in-flight meal really does taste bland. The aircraft cabin’s low humidity and lower air pressure reduce your sense of taste and smell by as much as 30% according to a Lufthansa commissioned study. Airline food kitchens often add extra spices and flavoring to meals to compensate for your crippled taste buds!
Special thanks to my Twitter friend (and fellow blogger) @Jen_Niffer for tipping me off to the Lufthansa study!
Further Reading About Pressurization:
What happens if there is a problem with the pressurization system?
Your Oxygen Mask vs My Oxygen Mask
Share this: Facebook
Cabin pressurization
Process to maintain internal air pressure in aircraft
Cabin pressurization is a process in which conditioned air is pumped into the cabin of an aircraft or spacecraft in order to create a safe and comfortable environment for passengers and crew flying at high altitudes. For aircraft, this air is usually bled off from the gas turbine engines at the compressor stage, and for spacecraft, it is carried in high-pressure, often cryogenic tanks. The air is cooled, humidified, and mixed with recirculated air if necessary before it is distributed to the cabin by one or more environmental control systems.[1] The cabin pressure is regulated by the outflow valve.
While the first experimental pressurization systems saw use during the 1920s and 1930s, it was not until 1940 that a commercial aircraft would enter service with a pressurized cabin, when the Boeing 307 Stratoliner joined the Transcontinental & Western Air and Pan American Airways fleets. The practice would become widespread a decade later, particularly with the introduction of the British de Havilland Comet jetliner in 1949. While initially a success, two catastrophic failures in 1954 temporarily grounded the worldwide fleet. The cause was found to be a combination of progressive metal fatigue and aircraft skin stresses, both of which aeronautical engineers had limited understanding at the time. The key engineering principles learned from the Comet were applied directly to the design of all subsequent jet airliners, such as the Boeing 707.
Certain aircraft have presented unusual pressurization scenarios. The supersonic airliner Concorde had a particularly high pressure differential due to flying at unusually high altitude: up to 60,000 ft (18,000 m) while maintaining a cabin altitude of 6,000 ft (1,800 m). This not only increased airframe weight, but also saw the use of smaller cabin windows than most other commercial passenger aircraft, intended to slow the decompression rate if a depressurization event occurred. The Aloha Airlines Flight 243 incident, involving a Boeing 737-200 that suffered catastrophic cabin failure mid-flight, was primarily caused by its continued operation despite having accumulated more than twice the number of flight cycles that the airframe was designed to endure. For increased passenger comfort, several modern airliners, such as the Boeing 787 Dreamliner and the Airbus A350 XWB, feature reduced operating cabin altitudes as well as greater humidity levels; the use of composite airframes has aided the adoption of such comfort-maximising practices.
Need for cabin pressurization [ edit ]
Pressurization becomes increasingly necessary at altitudes above 10,000 ft (3,000 m) above sea level to protect crew and passengers from the risk of a number of physiological problems caused by the low outside air pressure above that altitude. For private aircraft operating in the US, crew members are required to use oxygen masks if the cabin altitude (a representation of the air pressure, see below) stays above 12,500 ft (3,800 m) for more than 30 minutes, or if the cabin altitude reaches 14,000 ft (4,300 m) at any time. At altitudes above 15,000 ft (4,600 m), passengers are required to be provided oxygen masks as well. On commercial aircraft, the cabin altitude must be maintained at 8,000 ft (2,400 m) or less. Pressurization of the cargo hold is also required to prevent damage to pressure-sensitive goods that might leak, expand, burst or be crushed on re-pressurization.[citation needed] The principal physiological problems are listed below.
Hypoxia The lower partial pressure of oxygen at high altitude reduces the alveolar oxygen tension in the lungs and subsequently in the brain, leading to sluggish thinking, dimmed vision, loss of consciousness, and ultimately death. In some individuals, particularly those with heart or lung disease, symptoms may begin as low as 5,000 ft (1,500 m), although most passengers can tolerate altitudes of 8,000 ft (2,400 m) without ill effect. At this altitude, there is about 25% less oxygen than there is at sea level.[2] Hypoxia may be addressed by the administration of supplemental oxygen, either through an oxygen mask or through a nasal cannula. Without pressurization, sufficient oxygen can be delivered up to an altitude of about 40,000 ft (12,000 m). This is because a person who is used to living at sea level needs about 0.20 bar (20 kPa) partial oxygen pressure to function normally and that pressure can be maintained up to about 40,000 ft (12,000 m) by increasing the mole fraction of oxygen in the air that is being breathed. At 40,000 ft (12,000 m), the ambient air pressure falls to about 0.2 bar, at which maintaining a minimum partial pressure of oxygen of 0.2 bar requires breathing 100% oxygen using an oxygen mask. Emergency oxygen supply masks in the passenger compartment of airliners do not need to be pressure-demand masks because most flights stay below 40,000 ft (12,000 m). Above that altitude the partial pressure of oxygen will fall below 0.2 bar even at 100% oxygen and some degree of cabin pressurization or rapid descent will be essential to avoid the risk of hypoxia. Altitude sickness Hyperventilation, the body’s most common response to hypoxia, does help to partially restore the partial pressure of oxygen in the blood, but it also causes carbon dioxide (CO 2 ) to out-gas, raising the blood pH and inducing alkalosis. Passengers may experience fatigue, nausea, headaches, sleeplessness, and (on extended flights) even pulmonary oedema. These are the same symptoms that mountain climbers experience, but the limited duration of powered flight makes the development of pulmonary oedema unlikely. Altitude sickness may be controlled by a full pressure suit with helmet and faceplate, which completely envelops the body in a pressurized environment; however, this is impractical for commercial passengers. Decompression sickness The low partial pressure of gases, principally nitrogen (N 2 ) but including all other gases, may cause dissolved gases in the bloodstream to precipitate out, resulting in gas embolism, or bubbles in the bloodstream. The mechanism is the same as that of compressed-air divers on ascent from depth. Symptoms may include the early symptoms of “the bends”—tiredness, forgetfulness, headache, stroke, thrombosis, and subcutaneous itching—but rarely the full symptoms thereof. Decompression sickness may also be controlled by a full-pressure suit as for altitude sickness. Barotrauma As the aircraft climbs or descends, passengers may experience discomfort or acute pain as gases trapped within their bodies expand or contract. The most common problems occur with air trapped in the middle ear (aerotitis) or paranasal sinuses by a blocked Eustachian tube or sinuses. Pain may also be experienced in the gastrointestinal tract or even the teeth (barodontalgia). Usually these are not severe enough to cause actual trauma but can result in soreness in the ear that persists after the flight[3] and can exacerbate or precipitate pre-existing medical conditions, such as pneumothorax.
Cabin altitude [ edit ]
An empty bottle, sealed at 11,000 m (37,000 ft), is crushed on descent to sea level, compared with one in its original state.
The pressure inside the cabin is technically referred to as the equivalent effective cabin altitude or more commonly as the cabin altitude. This is defined as the equivalent altitude above mean sea level having the same atmospheric pressure according to a standard atmospheric model such as the International Standard Atmosphere. Thus a cabin altitude of zero would have the pressure found at mean sea level, which is taken to be 101.325 kPa (14.696 psi).[4]
Aircraft [ edit ]
In airliners, cabin altitude during flight is kept above sea level in order to reduce stress on the pressurized part of the fuselage; this stress is proportional to the difference in pressure inside and outside the cabin. In a typical commercial passenger flight, the cabin altitude is programmed to rise gradually from the altitude of the airport of origin to a regulatory maximum of 8,000 ft (2,400 m). This cabin altitude is maintained while the aircraft is cruising at its maximum altitude and then reduced gradually during descent until the cabin pressure matches the ambient air pressure at the destination.[citation needed]
Keeping the cabin altitude below 8,000 ft (2,400 m) generally prevents significant hypoxia, altitude sickness, decompression sickness, and barotrauma.[5] Federal Aviation Administration (FAA) regulations in the U.S. mandate that under normal operating conditions, the cabin altitude may not exceed this limit at the maximum operating altitude of the aircraft.[6] This mandatory maximum cabin altitude does not eliminate all physiological problems; passengers with conditions such as pneumothorax are advised not to fly until fully healed, and people suffering from a cold or other infection may still experience pain in the ears and sinuses.[citation needed] The rate of change of cabin altitude strongly affects comfort as humans are sensitive to pressure changes in the inner ear and sinuses and this has to be managed carefully. Scuba divers flying within the “no fly” period after a dive are at risk of decompression sickness because the accumulated nitrogen in their bodies can form bubbles when exposed to reduced cabin pressure.
The cabin altitude of the Boeing 767 is typically about 7,000 ft (2,100 m) when cruising at 37,000 ft (11,000 m).[7] This is typical for older jet airliners. A design goal for many, but not all, newer aircraft is to provide a lower cabin altitude than older designs. This can be beneficial for passenger comfort.[8] For example, the Bombardier Global Express business jet can provide a cabin altitude of 4,500 ft (1,400 m) when cruising at 41,000 ft (12,000 m).[9][10][11] The Emivest SJ30 business jet can provide a sea-level cabin altitude when cruising at 41,000 ft (12,000 m).[12][13][unreliable source?] One study of eight flights in Airbus A380 aircraft found a median cabin pressure altitude of 6,128 ft (1,868 m), and 65 flights in Boeing 747-400 aircraft found a median cabin pressure altitude of 5,159 ft (1,572 m).[14]
Before 1996, approximately 6,000 large commercial transport airplanes were assigned a type certificate to fly up to 45,000 ft (14,000 m) without having to meet high-altitude special conditions.[15] In 1996, the FAA adopted Amendment 25-87, which imposed additional high-altitude cabin pressure specifications for new-type aircraft designs. Aircraft certified to operate above 25,000 ft (7,600 m) “must be designed so that occupants will not be exposed to cabin pressure altitudes in excess of 15,000 ft (4,600 m) after any probable failure condition in the pressurization system”.[16] In the event of a decompression that results from “any failure condition not shown to be extremely improbable”, the plane must be designed such that occupants will not be exposed to a cabin altitude exceeding 25,000 ft (7,600 m) for more than 2 minutes, nor to an altitude exceeding 40,000 ft (12,000 m) at any time.[16] In practice, that new Federal Aviation Regulations amendment imposes an operational ceiling of 40,000 ft (12,000 m) on the majority of newly designed commercial aircraft.[17][18] Aircraft manufacturers can apply for a relaxation of this rule if the circumstances warrant it. In 2004, Airbus acquired an FAA exemption to allow the cabin altitude of the A380 to reach 43,000 ft (13,000 m) in the event of a decompression incident and to exceed 40,000 ft (12,000 m) for one minute. This allows the A380 to operate at a higher altitude than other newly designed civilian aircraft.[17]
Spacecraft [ edit ]
Russian engineers used an air-like nitrogen/oxygen mixture, kept at a cabin altitude near zero at all times, in their 1961 Vostok, 1964 Voskhod, and 1967 to present Soyuz spacecraft.[19] This requires a heavier space vehicle design, because the spacecraft cabin structure must withstand the stress of 14.7 pounds per square inch (1 atm, 1.01 bar) against the vacuum of space, and also because an inert nitrogen mass must be carried. Care must also be taken to avoid decompression sickness when cosmonauts perform extravehicular activity, as current soft space suits are pressurized with pure oxygen at relatively low pressure in order to provide reasonable flexibility.[20]
By contrast, the United States used a pure oxygen atmosphere for its 1961 Mercury, 1965 Gemini, and 1967 Apollo spacecraft, mainly in order to avoid decompression sickness.[21][22] Mercury used a cabin altitude of 24,800 ft (7,600 m) (5.5 psi (0.38 bar));[23] Gemini used an altitude of 25,700 ft (7,800 m) (5.3 psi (0.37 bar));[24] and Apollo used 27,000 ft (8,200 m) (5.0 psi (0.34 bar))[25] in space. This allowed for a lighter space vehicle design. This is possible because at 100% oxygen, enough oxygen gets to the bloodstream to allow astronauts to operate normally. Before launch, the pressure was kept at slightly higher than sea level at a constant 5.3 psi (0.37 bar) above ambient for Gemini, and 2 psi (0.14 bar) above sea level at launch for Apollo), and transitioned to the space cabin altitude during ascent. However, the high pressure pure oxygen atmosphere proved to be a factor in a fatal fire hazard in Apollo, contributing to the deaths of the entire crew of Apollo 1 during a 1967 ground test. After this, NASA revised its procedure to use a nitrogen/oxygen mix at zero cabin altitude at launch, but kept the low-pressure pure oxygen atmosphere at 5 psi (0.34 bar) in space.[26]
After the Apollo program, the United States used standard air-like[vague] cabin atmospheres for Skylab,[27] the Space Shuttle orbiter, and the International Space Station.[28]
Mechanics [ edit ]
Pressurization is achieved by the design of an airtight fuselage engineered to be pressurized with a source of compressed air and controlled by an environmental control system (ECS). The most common source of compressed air for pressurization is bleed air extracted from the compressor stage of a gas turbine engine, from a low or intermediate stage and also from an additional high stage; the exact stage can vary depending on engine type. By the time the cold outside air has reached the bleed air valves, it is at a very high pressure and has been heated to around 200 °C (392 °F). The control and selection of high or low bleed sources is fully automatic and is governed by the needs of various pneumatic systems at various stages of flight.[29]
The part of the bleed air that is directed to the ECS is then expanded to bring it to cabin pressure, which cools it. A final, suitable temperature is then achieved by adding back heat from the hot compressed air via a heat exchanger and air cycle machine known as a PAC (Pressurization and Air Conditioning) system. In some larger airliners, hot trim air can be added downstream of air conditioned air coming from the packs if it is needed to warm a section of the cabin that is colder than others.
At least two engines provide compressed bleed air for all the plane’s pneumatic systems, to provide full redundancy. Compressed air is also obtained from the auxiliary power unit (APU), if fitted, in the event of an emergency and for cabin air supply on the ground before the main engines are started. Most modern commercial aircraft today have fully redundant, duplicated electronic controllers for maintaining pressurization along with a manual back-up control system.
All exhaust air is dumped to atmosphere via an outflow valve, usually at the rear of the fuselage. This valve controls the cabin pressure and also acts as a safety relief valve, in addition to other safety relief valves. If the automatic pressure controllers fail, the pilot can manually control the cabin pressure valve, according to the backup emergency procedure checklist. The automatic controller normally maintains the proper cabin pressure altitude by constantly adjusting the outflow valve position so that the cabin altitude is as low as practical without exceeding the maximum pressure differential limit on the fuselage. The pressure differential varies between aircraft types, typical values are between 540 hPa (7.8 psi) and 650 hPa (9.4 psi).[30] At 39,000 ft (12,000 m), the cabin pressure would be automatically maintained at about 6,900 ft (2,100 m), (450 ft (140 m) lower than Mexico City), which is about 790 hPa (11.5 psi) of atmosphere pressure.[29]
Some aircraft, such as the Boeing 787 Dreamliner, have re-introduced electric compressors previously used on piston-engined airliners to provide pressurization.[31][32] The use of electric compressors increases the electrical generation load on the engines and introduces a number of stages of energy transfer;[33] therefore, it is unclear whether this increases the overall efficiency of the aircraft air handling system. It does, however, remove the danger of chemical contamination of the cabin, simplify engine design, avert the need to run high pressure pipework around the aircraft, and provide greater design flexibility.
Unplanned decompression [ edit ]
Passenger oxygen mask deployment
Unplanned loss of cabin pressure at altitude/in space is rare but has resulted in a number of fatal accidents. Failures range from sudden, catastrophic loss of airframe integrity (explosive decompression) to slow leaks or equipment malfunctions that allow cabin pressure to drop.
Any failure of cabin pressurization above 10,000 ft (3,000 m) requires an emergency descent to 8,000 ft (2,400 m) or the closest to that while maintaining the Minimum Sector Altitude (MSA), and the deployment of an oxygen mask for each seat. The oxygen systems have sufficient oxygen for all on board and give the pilots adequate time to descend to below 8,000 ft (2,400 m). Without emergency oxygen, hypoxia may lead to loss of consciousness and a subsequent loss of control of the aircraft. Modern airliners include a pressurized pure oxygen tank in the cockpit, giving the pilots more time to bring the aircraft to a safe altitude. The time of useful consciousness varies according to altitude. As the pressure falls the cabin air temperature may also plummet to the ambient outside temperature with a danger of hypothermia or frostbite.
For airliners that need to fly over terrain that does not allow reaching the safe altitude within a maximum of 30 minutes, pressurized oxygen bottles are mandatory since the chemical oxygen generators fitted to most planes cannot supply sufficient oxygen.
In jet fighter aircraft, the small size of the cockpit means that any decompression will be very rapid and would not allow the pilot time to put on an oxygen mask. Therefore, fighter jet pilots and aircrew are required to wear oxygen masks at all times.[34]
On June 30, 1971, the crew of Soyuz 11, Soviet cosmonauts Georgy Dobrovolsky, Vladislav Volkov, and Viktor Patsayev were killed after the cabin vent valve accidentally opened before atmospheric re-entry.[35][36]
History [ edit ]
Cessna P210 – First commercially successful pressurized single-engine aircraft
The aircraft that pioneered pressurized cabin systems include:
In the late 1910s, attempts were being made to achieve higher and higher altitudes. In 1920, flights well over 37,000 ft (11,000 m) were first achieved by test pilot Lt. John A. Macready in a Packard-Le Père LUSAC-11 biplane at McCook Field in Dayton, Ohio.[39] The flight was possible by releasing stored oxygen into the cockpit, which was released directly into an enclosed cabin and not to an oxygen mask, which was developed later.[39] With this system flights nearing 40,000 ft (12,000 m) were possible, but the lack of atmospheric pressure at that altitude caused the pilot’s heart to enlarge visibly, and many pilots reported health problems from such high altitude flights.[39] Some early airliners had oxygen masks for the passengers for routine flights.
In 1921, a Wright-Dayton USD-9A reconnaissance biplane was modified with the addition of a completely enclosed air-tight chamber that could be pressurized with air forced into it by small external turbines.[39] The chamber had a hatch only 22 in (560 mm) in diameter that would be sealed by the pilot at 3,000 ft (910 m).[39] The chamber contained only one instrument, an altimeter, while the conventional cockpit instruments were all mounted outside the chamber, visible through five small portholes.[39] The first attempt to operate the aircraft was again made by Lt. John A. McCready, who discovered that the turbine was forcing air into the chamber faster than the small release valve provided could release it.[39] As a result, the chamber quickly over pressurized, and the flight was abandoned.[39] A second attempt had to be abandoned when the pilot discovered at 3,000 ft (910 m) that he was too short to close the chamber hatch.[39] The first successful flight was finally made by test pilot Lt. Harrold Harris, making it the world’s first flight by a pressurized aircraft.[39]
The first airliner to enter commercial service with a pressurized cabin was the Boeing 307 Stratoliner, built in 1938, prior to World War II, though only ten were produced before the war interrupted production. The 307’s “pressure compartment was from the nose of the aircraft to a pressure bulkhead in the aft just forward of the horizontal stabilizer.”[40]
World War II era flying helmet and oxygen mask
World War II was a catalyst for aircraft development. Initially, the piston aircraft of World War II, though they often flew at very high altitudes, were not pressurized and relied on oxygen masks.[41] This became impractical with the development of larger bombers where crew were required to move about the cabin and this led to the first bomber with cabin pressurization (though restricted to crew areas), the Boeing B-29 Superfortress. The control system for this was designed by Garrett AiResearch Manufacturing Company, drawing in part on licensing of patents held by Boeing for the Stratoliner.[42]
Post-war piston airliners such as the Lockheed Constellation (1943) made the technology more common in civilian service. The piston-engined airliners generally relied on electrical compressors to provide pressurized cabin air. Engine supercharging and cabin pressurization enabled aircraft like the Douglas DC-6, the Douglas DC-7, and the Constellation to have certified service ceilings from 24,000 to 28,400 ft (7,300 to 8,700 m). Designing a pressurized fuselage to cope with that altitude range was within the engineering and metallurgical knowledge of that time. The introduction of jet airliners required a significant increase in cruise altitudes to the 30,000–41,000 ft (9,100–12,500 m) range, where jet engines are more fuel efficient. That increase in cruise altitudes required far more rigorous engineering of the fuselage, and in the beginning not all the engineering problems were fully understood.
The world’s first commercial jet airliner was the British de Havilland Comet (1949) designed with a service ceiling of 36,000 ft (11,000 m). It was the first time that a large diameter, pressurized fuselage with windows had been built and flown at this altitude. Initially, the design was very successful but two catastrophic airframe failures in 1954 resulting in the total loss of the aircraft, passengers and crew grounded what was then the entire world jet airliner fleet. Extensive investigation and groundbreaking engineering analysis of the wreckage led to a number of very significant engineering advances that solved the basic problems of pressurized fuselage design at altitude. The critical problem proved to be a combination of an inadequate understanding of the effect of progressive metal fatigue as the fuselage undergoes repeated stress cycles coupled with a misunderstanding of how aircraft skin stresses are redistributed around openings in the fuselage such as windows and rivet holes.
The critical engineering principles concerning metal fatigue learned from the Comet 1 program[43] were applied directly to the design of the Boeing 707 (1957) and all subsequent jet airliners. For example, detailed routine inspection processes were introduced, in addition to thorough visual inspections of the outer skin, mandatory structural sampling was routinely conducted by operators; the need to inspect areas not easily viewable by the naked eye led to the introduction of widespread radiography examination in aviation; this also had the advantage of detecting cracks and flaws too small to be seen otherwise.[44] Another visibly noticeable legacy of the Comet disasters is the oval windows on every jet airliner; the metal fatigue cracks that destroyed the Comets were initiated by the small radius corners on the Comet 1’s almost square windows.[45][46] The Comet fuselage was redesigned and the Comet 4 (1958) went on to become a successful airliner, pioneering the first transatlantic jet service, but the program never really recovered from these disasters and was overtaken by the Boeing 707.[47][48]
Even following the Comet disasters, there were several subsequent catastrophic fatigue failures attributed to cabin pressurisation. Perhaps the most prominent example was Aloha Airlines Flight 243, involving a Boeing 737-200.[49] In this case, the principal cause was the continued operation of the specific aircraft despite having accumulated 35,496 flight hours prior to the accident, those hours included over 89,680 flight cycles (takeoffs and landings), owing to its use on short flights;[50] this amounted to more than twice the number of flight cycles that the airframe was designed to endure.[51] Aloha 243 was able to land despite the substantial damage inflicted by the decompression, which had resulted in the loss of one member of the cabin crew; the incident had far-reaching effects on aviation safety policies and led to changes in operating procedures.[51]
The supersonic airliner Concorde had to deal with particularly high pressure differentials because it flew at unusually high altitude (up to 60,000 ft (18,000 m)) and maintained a cabin altitude of 6,000 ft (1,800 m).[52] Despite this, its cabin altitude was intentionally maintained at 6,000 ft (1,800 m).[53] This combination, while providing for increasing comfort, necessitated making Concorde a significantly heavier aircraft, which in turn contributed to the relatively high cost of a flight. Unusually, Concorde was provisioned with smaller cabin windows than most other commercial passenger aircraft in order to slow the rate of decompression in the event of a window seal failing.[54] The high cruising altitude also required the use of high pressure oxygen and demand valves at the emergency masks unlike the continuous-flow masks used in conventional airliners. The FAA, which enforces minimum emergency descent rates for aircraft, determined that, in relation to Concorde’s higher operating altitude, the best response to a pressure loss incident would be to perform a rapid descent.[56]
The designed operating cabin altitude for new aircraft is falling and this is expected to reduce any remaining physiological problems. Both the Boeing 787 Dreamliner and the Airbus A350 XWB airliners have made such modifications for increased passenger comfort. The 787’s internal cabin pressure is the equivalent of 6,000 ft (1,800 m) altitude resulting in a higher pressure than for the 8,000 ft (2,400 m) altitude of older conventional aircraft;[57] according to a joint study performed by Boeing and Oklahoma State University, such a level significantly improves comfort levels.[58][59] Airbus has stated that the A350 XWB provides for a typical cabin altitude at or below 6,000 ft (1,800 m), along with a cabin atmosphere of 20% humidity and an airflow management system that adapts cabin airflow to passenger load with draught-free air circulation.[60] The adoption of composite fuselages eliminates the threat posed by metal fatigue that would have been exacerbated by the higher cabin pressures being adopted by modern airliners, it also eliminates the risk of corrosion from the use of greater humidity levels.[57]
See also [ edit ]
4. Pressurisation
4. Pressurisation
Figure 4. Pressurisation controls
Pressurisation control is provided by an outflow valve and two safety valves, one to prevent over-pressurisation (>8.6 psi), the other to prevent under-pressurisation (>1 psi below ambient).
Two identical cabin pressure controllers, one acting as master, the other as a reserve, provide automated control of pressurisation. Each controller has an associated motor with which to modulate the outflow valve. A third motor provides for manual control. The pressure controllers exchange roles 70 seconds after each landing.
The LDG ELEV selector (Figure 4, “Pressurisation controls” (1)) can be set to AUTO or to an altitude. In AUTO the controller uses the landing elevation from the FMGC. If using a manually selected landing elevation, the CAB ALT on the ECAM PRESS page should be used rather than the coarse scale.
The landing QNH is usually sourced from the FMGC. If this is not available, the captain’s baro reference from the ADIRS is used.
The automatic pressurisation control operates in 6 modes:
Ground(GN) Before takeoff and 55 seconds after landing, the outflow valve is fully opened. At touchdown any residual cabin pressure is released at a cabin vertical speed of 500 fpm. Takeoff(TO) The aircraft is pre-pressurised to 0.1 psi diff at a rate of 400 fpm. Climb(CL) Cabin altitude if a function of actual rate of climb. Cruise(CR) The higher of cabin altitude at level-off or landing field elevation is maintained. Descent(DE) Cabin rate of descent maintained so that cabin pressure equals landing field pressure, with a maximum R.O.D. of 750fpm. Abort(AB) Cabin pressure set to take-off altitude + 0.1 psi.
If a single pressure controller fails, the other automatically takes over. If both pressure controllers fail, an amber FAULT light appears on the MODE SEL push button (Figure 4, “Pressurisation controls” (2)). Pressing this button puts the pressurisation in manual mode, and the spring loaded MAN V/S CTL toggle switch (Figure 4, “Pressurisation controls” (3)) must be used to control the pressurisation. When in MAN mode, the CAB V/S display on the ECAM CRUISE page changes to a gauge format to assist with manual control. Changing to manual mode for 10 seconds and then back to auto mode will cause the pressure controllers to swap roles.
The outflow valve is below the ditching water line. Pressing the ditching button (Figure 4, “Pressurisation controls” (4)) closes the outflow valve unless it is under manual control. Note that use of the ditching button and low pressure ground air will cause a build up of differential pressure.
A320: Manual control of cabin
The question is whether or not the TOD should be readjusted to meet a cabin alt of 0 when below FL200 or keep the TOD of the profile and let the cabin rate descent progressively. For the latter, a cabin alt of zero , « the target » will not be achieved.
Also , when will the cabin altitude meet the aircraft altitude ? If at 4000 feet the cabin alt is still at 4000 feet there is no point of making the cabin descent further to zero and then make the cabin alt rise with the « full up » procedure.
It states on a separate note :
V/S CTL FULL UPWhen on intermediate approach (below airfield pressure altitude +2 500 ft), adjust ΔP = 0. »
So in one hand you target a cabin alt of zero and then target a Delta P of zero?
1 st case ) you descended earlier and took into consideration the 300 ft/ min cabin rate so you started your descent let’s say 40 min before ETA. The target cabin alt of zero was met when below FL200.
For an airfield of 3000 feet elevation , if before approach the cabin was at zero I will probably enter a hold and make the cabin rise progressively to meet aircraft altitude ( and that is to meet the delta P of zero small note)
When applying the « full up » and rising the cabin from zero to aircraft altitude and releasing the delta P in few seconds will certainly be beyond the acceptable limits of comfort.
2 nd case) you descent normally as per the profile and as you target a cabin alt of zero , the target is never met before approach. That is to say that the aircraft altitude will meet the cabin altitude somewhere before approach hence you have a delta P of zero because you are at 4000 feet and cabin alt of 4000 feet.
when applying the « full up » procedure little to no residual pressure will be released. You then meet the requirement of having a delta of zero ( small note in FCOM).
In one hand a cabin alt of zero requirement along with a second requirement of Delta P of zero seems contradictory.
Would you target a cabin alt of zero ( 1st requirement)or a delta P of zero ( second requirement)?
I would rather go for case 2 .
More inputs will be appreciated.
A320 OUTFLOW VALVES
We use cookies on our website to give you the most relevant experience by remembering your preferences and repeat visits. By clicking “Accept All”, you consent to the use of ALL the cookies. However, you may visit “Cookie Settings” to provide a controlled consent.
AIRCON/PRESSURIZATION/VENTILATION
AIRCONDITIONING
If there is any conflicting information, your FCOM shall be the overriding reference.
Q1. Under what conditions, Pack Flow Control Valve will close automatically?
A1. Pack Flow Control Valve [Pneumatically Operated/Electrically Controlled] closes automatically under the following conditions :-
(a) Pack Overheating
(b) Engine Starting
(c) Operation of Fire or Ditching P/b.
The Pack Flow Control Valve remains closed in absence of air pressure.
Q2. What is the RAM AIR P/B for? When is it used?
A2. Emergency Ram Air inlet ventilates cockpit/cabin to remove smoke or if both packs fail.
The Emerg. Ram Air Inlet Valve is controlled by RAM AIR P/b on AIR COND panel. It opens the Ram Air Valve, provided that Ditching is not selected.
Q3. What is the limitation for opening the RAM AIR inlet?
A3. Ram Air Inlet will only open if Ditching is not selected. Also, during T/O, RAM AIR Inlet/Outlet flaps close when T/O PWR set and MLG struts are compressed.
During LDG, they close as soon as MLG struts are compressed and speed at or above 70 knots. They open 20 seconds after speed drops below 70 knots.
Also, if Delta P > 1 Psi, check valve located downstream the Ram Air door will not open even if Ram Air Door has been selected open. No airflow will then be supplied.
Q4. What are the conditions in which Hot Air Fault light comes?
A4. HOT AIR Fault light (Amber) comes on when :-
(a) Duct Overheat is detected [Overheat is sensed when Duct temp. reaches 88 degree Celsius]
*Goes off when temp. drops below 70 degree Celsius and flight crew select OFF.
(b) HOT AIR pressure regulating valve disagrees with selected position.
Q5. If Hot Air Press Reg. valve fails in open condition, what happens? What you are supposed to do, if in flight?
A5. There is no effect if the Hot Air Press. Regulating Valve fails in open condition.
Q6. If Hot Air Press Reg. valve fails in closed condition, what happens? What you are supposed to do, if in flight?
A6. Optimized regulation is lost. Trim Air Valves are driven to the full closed position. PACK 1 controls the cockpit temperature and PACK 2 controls the cabin temperature (FWD and AFT) to mean value of selected temperatures.
Q7. How many trim air valves are fitted and what do they do?
A7. There are 3 Trim Air Valves o the A320. One for each zone :-
(a) COCKPIT
(b) FORWARD CABIN
(c) AFT CABIN
The Trim Air Valve, associated with each zone adjusts the temperature by adding hot air tapped upstream of the packs to the Mixing Unit Air.
Q8. If cockpit trims air valve has failed in open position, which of the warnings will be generated?
A8. TRIM AIR VALVE failed in open position, the following warning is generated :-
TRIM AIR SYS FAULT
And on ECAM COND page, “ZONE TRIM AIR VALVE” position indication will become amber.
Q9. What are the three supply zones for conditioned air?
A9. The Three Supply Zones for Conditioned AIR are :-
(a) COCKPIT
(b) FWD CABIN
(c) AFT CABIN
Q10. What happens when a temperature selector rotary knob is adjusted in the cockpit?
A10. A signal is sent to the Zone Controller requesting a different temperature [Rotary Knobs to select reference temperature which are fine tuned through the Forward Attendant Panel (FAP) for cabin zones ] . The ACSC’s compute a temperature demand from the selected temp. and the actual temp. A signal corresponding to the lowest demanded zone temp. goes to Air Conditioning System controllers which then make both Packs produce the required Outlet Temperature.
Q11. What is ACSC and what does it do?
A11. ACSC is short for Air Conditioning System Controller. It does the following :-
(a) PACK Operation Control
(b) Controlling the PACK flow control Valve
(c) Controlling the HOT AIR PRESS Regulating Valve
(d) TRIM AIR Valve CONTROL.
(e) Temperature and flow regulation.
Each ACSC regulates the temperature of its associated PACK by modulating the bypass valve and the Ram Air Inlet flap.
Q12. On which of the ECAM pages, the packs’ parameters are shown? What are they?
A12. On the ECAM BLEED page :-
(a) PACK Outlet temp.
(b) PACK Bypass Valve position
(c) PACK Compressor Outlet temp
(d) PACK flow
Q13. On ECAM COND page, two temperature values are shown. What is the meaning of it?
A13. The two temperature Indications are :-
(a) Zone Temp Indication : The Zone Temp indication for the three zones, indicates the temp. in the zones.
(b) Zone Duct Temp Indication : The temperature of the air in the three main supply ducts to the Cocpit, The Forward Cabin and the Aft Cabin.
Q14. The ram air inlet flaps, {for the ACM heat exchangers}, automatically close under two conditions regardless of heat exchanger requirements. What are those two conditions? Where can you see them during walk-around inspection?
A14. RAM AIR Inlet/Outlet flaps close automatically under the following two indications :-
(a) TAKEOFF – T/O PWR set and MLG struts compressed.
(b) LANDING – As soon as MLG struts compressed and speed greater than or equal to 70 knots.
Q15. Is cargo heat provided to the forward cargo compartment?
A15. No.
Q16. Name the important components of the Air conditioning system?
A16. The following are the important components of the A320 Air Conditioning System
(a) Air Conditioning Pack
(b) Air Cycle Machine
(c) Heat Exchanger
(e) Mixing Unit
(f) Water Separator
And the Controller
(a) Air Conditioning System Controller
PRESSURIZATION
If there is any conflicting information, your FCOM shall be the overriding reference.
Q1. How many modes of pressurization exist on A320?
A1. There are Three modes of Pressurization on the A320
(a) AUTOMATIC
(b) SEMI-AUTOMATIC
(c) MANUAL
Q2. In auto mode of operation, what will be the max cabin altitude if system is functioning normal?
A2. 8000 ft is the Max Cabin Altitude in AUTO mode of operation.
Q3. If pilot suspects that the selected controller is malfunctioning, how can he change the controller {CPC}, while operating pressurization in AUTO?
A3. If the pilot suspects that the operating pressurization system is not performing properly, he can attempt to select to other system by switching the MODE SEL P/b to MAN for at least 10 seconds, then returning it to AUTO.
Q4. When will CPC changeover take place automatically?
A4. Automatic CPC Changeover happens automatically :-
(a) 70 seconds after each Landing.
(b) If the Operating System fails.
Q5. If one cabin pressure controller fails, how is pressurization maintained? What ECAM Caution will be generated?
A5. Pressurization System consists of 2 CPC’s , one of which operates the OutFlow Valve by means of its associated Automatic Motor. In case of a single CPC failure, the remaining CPC takes over automatic control of pressurization. The following ECAM Caution will be generated :-
SYS 1 (or 2) FAULT
and correspondingly the PRESS PAGE on the SD will be automatically displayed.
Q6. If Cabin Pressurization is in Auto, and if you have to push open Emer. RAM AIR, what happens to the Out Flow Valve?
A6. When the Cabin Pressurization is in AUTO and you push open EMER. RAM AIR, the OutFlow Valve opens about 50% provided that Delta P is less than 1 Psi.
Q7. What happens to the outflow valve if the MODE SEL switch is in MAN?
A7. If the MODE SEL s/w is in MAN, the OutFlow Valve won’t open even if Delta P is less than 1 Psi.
Q8. If you increase Cabin V/S {when pressurization in MAN Mode}, what happens to the Out-Flow Valve?
A8. The MAN V/S CTL toggle S/w is used to increase/decrease the Cabin V/s. The following happens to the OutFlow Valve on operation of the MAN V/S CTL Toggle s/w :-
UP : The Valve moves towards the open position.
DOWN: The Valve moves towards the closed position.
The OutFlow Valve operates slowly in MAN mode, so the pilot must hold the toggle switch in the UP or DOWN position until reaching the target V/s.
Q9. While in MAN Mode, how do you increase the cabin ALT?
A9. In MAN mode, you can increase the Cabin Altitude by operation on the MAN V/S CTL toggle s/w. By moving the s/w towards UP, the OutFlow valve moves towards the OPEN position, this increases the Cabin ALT.
Q10. By increasing cabin altitude in flight, what happens to Cabin Diff Pressure? Will it increase or decrease?
A10. The Cabin Differential Pressure will decrease when the Cabin Altitude is increased in flight.
Q11. What is the role of Safety Valves?
A11. The two independent pneumatic safety valves prevent Cabin Pressure from going too high (8.6 Psi above ambient ) or too low ( 1Psi below ambient ).
Q12. How many safety valves are fitted on A320?
A12. There are 2 independent pneumatic Safety Valves fitted on the A320, located on the rear pressure bulkhead above the floatation line.
Q13. What do you understand by negative differential pressure?
A13. Differential Pressure is the difference between the Cabin Pressure and the Ambient Pressure.
Delta P = Cabin Press. – Ambient Press.
Thus a Negative Differential Pressure means lesser Cabin Pressure than the Ambient Pressure.
Q14. With the LDG ELEV selector in AUTO, which reference altitude is used for landing field pressurization?
A14. The Controller normally uses the landing elevation and the QNH from the FMGC, and the pressure altitude from ADIRS. If FMGC data are not available, the controller uses the CAPT BARO Reference from the ADIRS and the LDG ELEV selection.
Q15. With the LDG ELEV selector at 1, what would be the landing elevation?
A15. With the LDG ELEV selector at 1, the Landing elevation would be +1000 feet.
Q16. What is RPCU? What are the logic conditions for RPCU to open the Out Flow Valve?
A16. RPCU is short for Residual Pressure Control Unit. It automatically depressurizes the aircraft in case of abnormal residual pressure on ground. It automatically open OutFlow valve if :-
(a) The OutFlow Valve is not fully open and,
(b) Both CPC’s are failed, or manual mode is selected, and
(c) The A/C is o the ground and
(d) All engines are ShutDown, or all ADIRS indicate airspeed < 100 knots. Q17. What happens when the DITCHING pushbutton is selected ON? A17. When the DITCHING P/b is selected ON, the operating system sends a “close” signal to the OutFlow valve, Emergency Ram Air Inlet, Avionics Ventilation Inlet and Extract Valves and the PACK Flow Control Valves close. Q18. “Cabin V/S” info is displayed on three ECAM pages. Which are those? A18. CABIN V/S info is on the following ECAM pages :- (a) ECAM PRESS page (b) ECAM CRUISE page (c) ECAM DOOR page ( Only in Flight phases 5/6/7 ) *Flight Phase 5- Lift Off to 1500 ft. *Flight Phase 6- 1500 ft – 800 ft *Flight Phase 7- 800 ft to TouchDown. Q19. When will V/S pulse in green? A19. The V/S pulses in green when V/S > 1750 ft/min. It resets at 1650 ft/min.
Q20. When will Diff press pulse in green?
A20. The digital presentation of Differential Pressure will pulse green when Delta P > 1.5 Psi ( Resets at 1 Psi ) during Flight Phase 7.
*Flight Phase 7 : 800 ft to Touchdown
Q21. When will Diff press become amber?
A21. Delta P becomes Amber when Delta P less than or equal to -0.4 Psi or greater than or equal to 8.5 Psi.
Q22. When does CAB ALT become red?
A22. The Cabin Alt Presentation appears in red when the Cabin Altitude goes above 9550 feet.
Q23. Can Out flow valve indication become amber? When?
A23. The OutFlow Valve indication becomes amber when the valve opens more than 95% during flight.
Q24. Name the important components of Pressurization?
A24. Following are the important components of Pressurization :-
(a) CPC : Cabin Pressure Controller
(b) RPCU : Residual Pressure Control Unit
(c) OutFlow Valve with its three motors
(d) Safety Valve
VENTILATION
If there is any conflicting information, your FCOM shall be the overriding reference.
Q1. What happens when you press Blower P/B to OVRD?
A1. When the BLOWER or the EXTRACT P/b switch is set at the OVRD (Override) position, the system is in closed circuit configuration and adds air from the Air Conditioning system to the ventilation air.
When the BLOWER P/b s/w is set at OVRD. , the Blower fan is stopped and the Extract fan continues to run.
Q2. What happens when you press Extract P/B to OVRD?
A2. When the BLOWER or the EXTRACT P/b s/w is set at the OVRD (Override) position, the system is in closed circuit configuration and adds air from the air conditioning system to the ventilation air.
When the EXTRACT P/b s/w is set at OVRD. , the Extract fan is controlled directly from the p/b. Both fans continue to run.
Q3. What will happen when you press both Blower & Extract P/B to OVRD? Name some situations when you have to push both Blower & Extract p/b to OVRD?
A3. When both BLOWER and EXTRACT P/b’s are set at OVRD position, the Air Conditioning system supplies cooling air, which is then exhausted overboard. The Blower fan stops and the Extract fan continues to run.
In case of smoke detection in the avionics ventilation air, the BLOWER and the EXTRACT FAULT lights come on, in this case both the BLOWER and the EXTRACT fan switches are selected to OVRD.
In case of SKIN VALVE FAULT, with the Extract valve affected, the BLOWER and the EXTRACT fan switches are selected to OVRD. (These actions send additional closure signals to the inlet and extract valves. The weather radar image on both ND’s may be lost in case of insufficient ventilation. )
Q4. What happens when Blower Fan stops on ground with engines shut down?
A4. When the Blower fan stops on the ground with the engines stopped :-
FAULT Lt on the BLOWER P/b lights up.
ECAM activates.
The External horn sounds while on the ground.
Q5. What indications are given on the ventilation panel, if smoke is detected in the avionics ventilation duct?
A5. On the Ventilation Panel, the FAULT Lt. on both the BLOWER and the EXTRACT P/b’s lights up Amber. ECAM activates.
Q6. What is the Avionics Ventilation System configuration once you apply take-off power?
A6. On the Ground after the application of T/O power, the Ventilation system is in closed circuit configuration.
Footnote: Tremendous efforts have gone into making this page. People involved with Project Airbus Tech (PAT) have spent countless sleepless nights to make this page possible for you. The least you can do is to support us by giving us our due credit.
No part of this page may be copied, or distributed, or used for any commercial purposes. For any uses, please CONTACT THE FLYING ENGINEER.
Thank you for supporting us, and thank you for giving us our due credit.
키워드에 대한 정보 a320 outflow valve
다음은 Bing에서 a320 outflow valve 주제에 대한 검색 결과입니다. 필요한 경우 더 읽을 수 있습니다.
이 기사는 인터넷의 다양한 출처에서 편집되었습니다. 이 기사가 유용했기를 바랍니다. 이 기사가 유용하다고 생각되면 공유하십시오. 매우 감사합니다!
사람들이 주제에 대해 자주 검색하는 키워드 Airbus A320 Out Flow Valve Stuck Part 1
- airbus a320
- a320 systems
- A320 OUTFLOW VALVE
- a320
- airbus
- airbus a320 family
Airbus #A320 #Out #Flow #Valve #Stuck #Part #1
YouTube에서 a320 outflow valve 주제의 다른 동영상 보기
주제에 대한 기사를 시청해 주셔서 감사합니다 Airbus A320 Out Flow Valve Stuck Part 1 | a320 outflow valve, 이 기사가 유용하다고 생각되면 공유하십시오, 매우 감사합니다.