당신은 주제를 찾고 있습니까 “astm d4169 pdf – ASTM D4169 Transit Testing | Packaging Compliance Labs“? 다음 카테고리의 웹사이트 Chewathai27.com/you 에서 귀하의 모든 질문에 답변해 드립니다: Chewathai27.com/you/blog. 바로 아래에서 답을 찾을 수 있습니다. 작성자 Packaging Compliance Labs 이(가) 작성한 기사에는 조회수 1,105회 및 좋아요 7개 개의 좋아요가 있습니다.
astm d4169 pdf 주제에 대한 동영상 보기
여기에서 이 주제에 대한 비디오를 시청하십시오. 주의 깊게 살펴보고 읽고 있는 내용에 대한 피드백을 제공하세요!
d여기에서 ASTM D4169 Transit Testing | Packaging Compliance Labs – astm d4169 pdf 주제에 대한 세부정보를 참조하세요
At Packaging Compliance Labs, the two standards we use most frequently for transit testing, distribution testing, is ASTM D4169 and the ISTA Series. In this video, we go over the most common tests that are performed during transit testing studies.
astm d4169 pdf 주제에 대한 자세한 내용은 여기를 참조하세요.
ASTM D4169-16.pdf – PDFCOFFEE.COM
Designation: D4169 − 16Standard Practice forPerformance Testing of Shipping Containers and Systems1 This standard is…
Source: pdfcoffee.com
Date Published: 4/19/2022
View: 9705
Astm D4169-16 | PDF | Cargo | Consumer Goods – Scribd
ASTM D4169-16.pdf – Free download as PDF File (.pdf), Text File (.txt) or read online for free.
Source: www.scribd.com
Date Published: 10/21/2021
View: 9638
ASTM-D4169-14.pdf
‘ This practice is under the jurisdiction of ASTM Committee 010 on Packaging and is the direct responsibility of Subcommittee D10.21 on Shipping Containers and.
Source: indico.fnal.gov
Date Published: 10/9/2021
View: 3003
pdf Download ASTM D4169: Standard Practice for … – CivilNode
ASTM D4169: Standard Practice for Performance Testing of Shipping Containers and Systems pdf Download. File Size 212.14 KB. Year 2016. Number of Pages
Source: civilnode.com
Date Published: 9/3/2021
View: 4243
Standard Practice for Performance Testing of Shipping …
Do you already have an ASTM Compass® Subscription? Access your content now. Go to ASTM Compass®. Standard Active Last Updated: Feb 18, 2022. ASTM D4169-22 …
Source: www.astm.org
Date Published: 5/22/2022
View: 5527
ASTM D4169-16 PDF Standard EN Preview – NormStream
Significance and Use 4.1 This practice proves a gue for the evaluation of shipping units in accordance with a uniform system, using established test …
Source: www.normstream.com
Date Published: 5/16/2022
View: 510
ASTM D 4169 – 04 pdf free download
A superscript epsilon (e) indicates an editorial change since the last revision or reapproval. ASTM D 4169 – 04 pdf free download. This standard …
Source: worldwidestandard.net
Date Published: 10/24/2022
View: 938
Astm D4169-16 Pdf – Wakelet
Astm D4169-16 Pdf. Performance Testing Of Shipping Containers And Systems1 This Standard Is Issued Under The Fixed Designation D4169; The Number Immediately …
Source: wakelet.com
Date Published: 3/15/2021
View: 785
주제와 관련된 이미지 astm d4169 pdf
주제와 관련된 더 많은 사진을 참조하십시오 ASTM D4169 Transit Testing | Packaging Compliance Labs. 댓글에서 더 많은 관련 이미지를 보거나 필요한 경우 더 많은 관련 기사를 볼 수 있습니다.
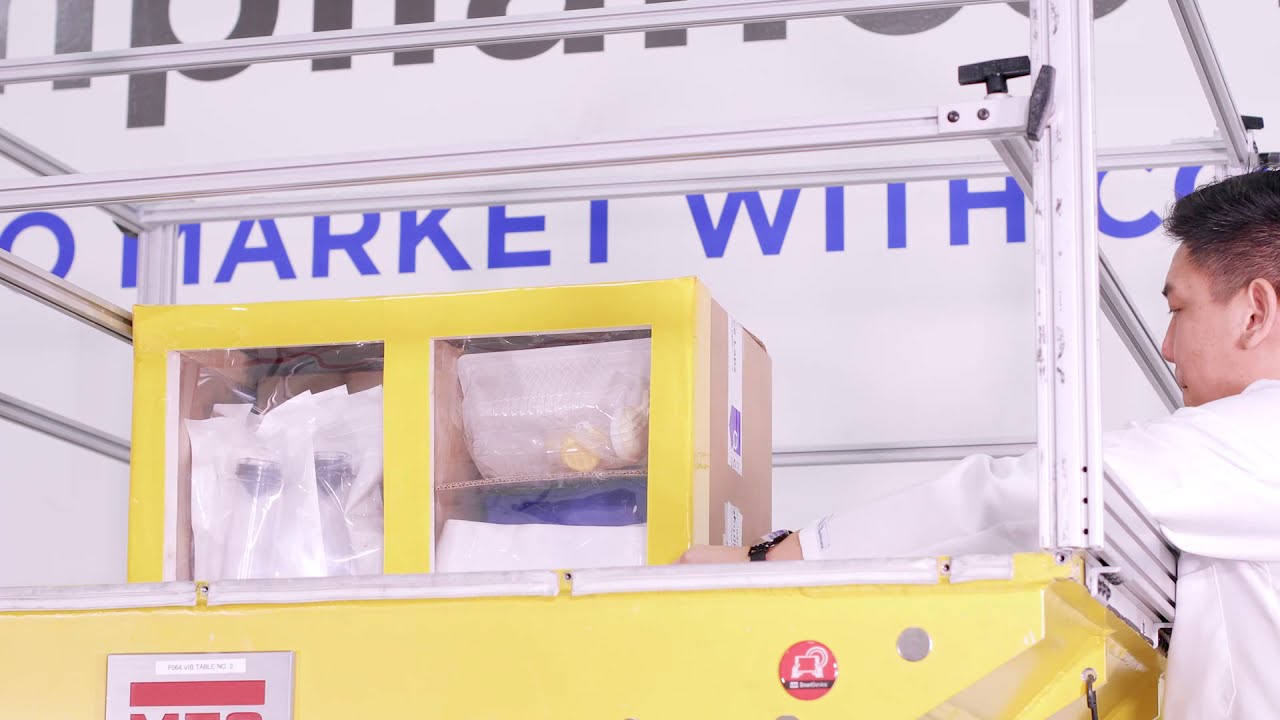
주제에 대한 기사 평가 astm d4169 pdf
- Author: Packaging Compliance Labs
- Views: 조회수 1,105회
- Likes: 좋아요 7개
- Date Published: 2020. 10. 27.
- Video Url link: https://www.youtube.com/watch?v=8Nmy6boy1LY
ASTM D4169-16.pdf
Citation preview
Designation: D4169 − 16
Standard Practice for
Performance Testing of Shipping Containers and Systems1 This standard is issued under the fixed designation D4169; the number immediately following the designation indicates the year of original adoption or, in the case of revision, the year of last revision. A number in parentheses indicates the year of last reapproval. A superscript epsilon (´) indicates an editorial change since the last revision or reapproval. This standard has been approved for use by agencies of the U.S. Department of Defense.
D999 Test Methods for Vibration Testing of Shipping Containers D4003 Test Methods for Programmable Horizontal Impact Test for Shipping Containers and Systems D4332 Practice for Conditioning Containers, Packages, or Packaging Components for Testing D4728 Test Method for Random Vibration Testing of Shipping Containers D5265 Test Method for Bridge Impact Testing D5276 Test Method for Drop Test of Loaded Containers by Free Fall D5277 Test Method for Performing Programmed Horizontal Impacts Using an Inclined Impact Tester D5487 Test Method for Simulated Drop of Loaded Containers by Shock Machines D6055 Test Methods for Mechanical Handling of Unitized Loads and Large Shipping Cases and Crates D6179 Test Methods for Rough Handling of Unitized Loads and Large Shipping Cases and Crates D6344 Test Method for Concentrated Impacts to Transport Packages D6653 Test Methods for Determining the Effects of High Altitude on Packaging Systems by Vacuum Method D7386 Practice for Performance Testing of Packages for Single Parcel Delivery Systems F1327 Terminology Relating to Barrier Materials for Medical Packaging (Withdrawn 2007)3 2.2 Military Standards:4 MIL-STD-810F Environmental Test Methods MIL-STD-2073–1 DOD Standard Practice for Military Packaging 2.3 Association of American Railroads Standards:5 General Information Bulletin No. 2 Rules and Procedures for Testing of New Loading and Bracing Methods or Materials
1. Scope* 1.1 This practice provides a uniform basis of evaluating, in a laboratory, the ability of shipping units to withstand the distribution environment. This is accomplished by subjecting them to a test plan consisting of a sequence of anticipated hazard elements encountered in various distribution cycles. This practice is not intended to supplant material specifications or existing preshipment test procedures. 1.2 Consider the use of Practice D7386 for testing of packages for single parcel shipments. 1.3 The suitability of this practice for use with hazardous materials has not been determined. 1.4 The values stated in inch-pound units are to be regarded as standard. The values given in parentheses are mathematical conversions to SI units that are provided for information only and are not considered standard. 1.5 This standard does not purport to address all of the safety concerns, if any, associated with its use. It is the responsibility of the user of this standard to establish appropriate safety and health practices and determine the applicability of regulatory limitations prior to use. 2. Referenced Documents 2.1 ASTM Standards:2 D642 Test Method for Determining Compressive Resistance of Shipping Containers, Components, and Unit Loads D880 Test Method for Impact Testing for Shipping Containers and Systems D951 Test Method for Water Resistance of Shipping Containers by Spray Method D996 Terminology of Packaging and Distribution Environments 1 This practice is under the jurisdiction of ASTM Committee D10 on Packaging and is the direct responsibility of Subcommittee D10.21 on Shipping Containers and Systems – Application of Performance Test Methods. Current edition approved April 1, 2016. Published June 2016. Originally approved in 2004. Last previous edition approved in 2014 as D4169 – 14. DOI: 10.1520/D4169-16. 2 For referenced ASTM standards, visit the ASTM website, www.astm.org, or contact ASTM Customer Service at [email protected] For Annual Book of ASTM Standards volume information, refer to the standard’s Document Summary page on the ASTM website.
3 The last approved version of this historical standard is referenced on www.astm.org. 4 Available from Standardization Documents Order Desk, DODSSP, Bldg. 4, Section D, 700 Robbins Ave., Philadelphia, PA 19111-5098, http:// dodssp.daps.dla.mil. 5 Available from Association of American Railroads (AAR), 425 Third St., SW, Washington, DC 20024, http://www.aar.org.
*A Summary of Changes section appears at the end of this standard Copyright © ASTM International, 100 Barr Harbor Drive, PO Box C700, West Conshohocken, PA 19428-2959. United States
1
D4169 − 16 3.3.1 3.3.2 3.3.3 3.3.4 3.3.5
3. Terminology 3.1 Definitions—General definitions for the packaging and distribution environments are found in Terminology D996. 3.2 Definitions of Terms Specific to This Standard: 3.2.1 acceptance criteria—the acceptable quality level that must be met after the shipping unit has been subjected to the test plan. See Section 7.
TOFC—trailer on flatcar. COFC—container on flatcar. TL—truckload. CL—carload. LTL—less than truckload.
4. Significance and Use
3.2.2 assurance level—the level of test intensity based on its probability of occurring in a typical distribution cycle. 3.2.2.1 Discussion—Level I is a high level of test intensity and has a low probability of occurrence. Level III is a low level of test intensity, but has a correspondingly high probability of occurrence. Level II is between these extremes. For Distribution Cycle 18 (DC–18), see MIL-STD-2073–1 for definitions of military levels of protection.
4.1 This practice provides a guide for the evaluation of shipping units in accordance with a uniform system, using established test methods at levels representative of those occurring in actual distribution. The recommended test levels are based on available information on the shipping and handling environment, and current industry/government practice and experience (1-13).6 The tests should be performed sequentially on the same containers in the order given. For use as a performance test, this practice requires that the shipping unit tested remain unopened until the sequence of tests are completed. If used for other purposes, such as package development, it may be useful to open and inspect shipping units at various times throughout the sequence. This may, however, prohibit evaluating the influence of the container closure on container performance.
3.2.3 coeffıcient of restitution—the ratio of the rebound velocity to the impact velocity. 3.2.4 distribution cycle (DC)—the sequential listing of the test schedules employed to simulate the hazard elements expected to occur for a specific routing of a shipping unit from production to consumption. See Table 1. 3.2.5 feeder aircraft—small, potentially non-pressurized aircraft used to transport express packages.
4.2 For Distribution Cycle 18, as referred to in MIL-STD2073–1, the use of this practice is defined in subsequent sections identified as DC-18.
3.2.6 hazard element—a specific event that occurs in a distribution cycle that may pose a hazard to a shipping unit. The element will usually be simulated by a single test schedule. See Section 9.
5. Test Specimen 5.1 Test specimens consist of representative samples of complete shipping units, including actual contents. Products with blemishes or minor defects may be used if the defective component is not to be studied by the test and if the defect is documented in the report. Dummy test loads are acceptable if testing the actual product might be hazardous. If a dummy load is used, it should be instrumented to determine if the fragility level of the actual product has been exceeded. Take care to duplicate the load characteristics of the actual product, and avoid unnecessary prehandling.
3.2.7 shipping unit—the smallest complete unit that will be subjected to the distribution environment, for example, a shipping container and its contents. 3.2.7.1 small shipping unit—for DC-18, a small shipping unit is defined as one having no edge dimension or diameter over 60 in. (1.52 m) and a gross weight of 100 lb (45 kg) or less. 3.2.7.2 large shipping unit—for DC-18, a large shipping unit is defined as one having at least one edge dimension or diameter over 60 in. (1.52 m) or a gross weight in excess of 100 lb (45 kg), or it is one that has a gross weight exceeding 100 lb (45 kg) and is secured to a base or to the base of a shipping unit.
5.2 Care must be taken to ensure that no degradation has occurred to either the product or the package if the test packages have been shipped to the test site. If any doubt exists as to the condition of the package, repack the product in new packaging material before testing.
3.2.8 test plan—a specific listing of the test sequence to be followed to simulate the hazards anticipated during the distribution cycle of a shipping unit. Included will be the test intensity and number of sequential tests to be conducted. See 8.5.
5.3 The number of test replications depends on the desired objectives of the testing and the availability of duplicate products and shipping containers. Replicate testing is recommended to improve the reliability of the test results.
3.2.9 test schedule—the specific procedure to be used, including the three assurance level intensities, and a reference to the test method that is the basis of the schedule. 3.2.9.1 Discussion—The purpose of the schedule is to simulate the forces occurring during any hazard element of the distribution cycle. See Section 9.
6. Conditioning 6.1 If the distribution cycle contains climatic conditions that have an effect on the performance characteristics of the product, shipping container, or components such as cushioning, use one of the following procedures. (It should be noted that different atmospheric conditions are likely to exist between the
3.2.10 total velocity change, (∆V)—the sum of the impact and rebound velocities.
6 The boldface numbers in parentheses refer to a list of references at the end of this practice.
3.3 Abbreviations: 2
D4169 − 16 TABLE 1 Distribution Cycles
DC
Distribution Cycle
Performance Test Schedule Sequence (see Section 9 for Test Schedule definition) Third Fourth Fifth
First
Second
Schedule A Handling
Schedule D Stacked Vibration
1
General Cycle—undefined distribution system
Schedule F Loose-Load Vibration
2
Specially defined distribution system, user specified (see Appendix X2)
3
Single package without pallet or skid, LTL motor freight
4
Single package with pallet or skid, LTL motor freight
5
Motor freight, TL, not unitized
Schedule A Handling
Schedule D Stacked Vibration
6
Motor freight, TL, or LTL—unitized
Schedule A Handling
Schedule D Stacked Schedule J Vibration OR Concentrated Schedule C Vehicle Impact Stacking plus Schedule E Vehicle Vibration
7
Rail only, bulk loaded
Schedule A Handling
Schedule D Stacked Vibration
8
Rail only, unitized
Schedule A Handling
9
Rail and motor freight, not unitized
10
Schedule G Schedule J Rail Concentrated Switching Impact
Sixth
Seventh
Schedule A Handling
select from Schedules A through I
Schedule Schedule D Stacked A Vibration OR Handling Schedule C Vehicle —Manual Stacking plus Schedule E Vehicle Vibration
Schedule F Schedule J Loose-Load Concentrated Vibration Impact
Schedule A Handling— Manual
…
Schedule Schedule D Stacked A Vibration OR Handling Schedule C Vehicle —Mechanical Stacking plus Schedule E Vehicle Vibration
Schedule F Schedule J Loose-Load Concentrated Vibration Impact
Schedule A Handling— Mechanical
…
Schedule E Schedule J Vehicle Concentrated Vibration Impact
Schedule A Handling
…
Schedule A Handling
Schedule B Warehouse Stacking
…
Schedule G Rail Switching
Schedule A Handling
…
…
Schedule D Stacked Vibration
Schedule G Rail Switching
Schedule A Handling
Schedule B Warehouse Stacking
…
Schedule A Handling
Schedule C Vehicle Stacking
Schedule E Vehicle Vibration
Schedule G Rail Switching
Schedule F Schedule J Loose-Load Concentrated Vibration Impact
Rail and motor freight, unitized
Schedule A Handling
Schedule D Stacked Vibration
Schedule G Schedule J Rail Concentrated Switching Impact
Schedule A Handling
Schedule B Warehouse Stacking
11
Rail, TOFC and COFC
Schedule A Handling
Schedule G Rail Switching
Schedule D Stacked Vibration
Schedule F Loose-Load Vibration
Schedule A Handling
…
12
Air (intercity) and motor freight (local), over 150 lb (68.1 kg), or unitized
Schedule A Handling
Schedule D Stacked Vibration
Schedule I Low PressureA
Schedule E Schedule J Vehicle Concentrated Vibration Impact
Schedule A Handling
13
Air (intercity) and motor freight (local, single package up to 150 lb (61.8 kg). Consider using Practice D7386 for single parcel carrier shipments.
Schedule A Handling
Schedule C Vehicle Stacking
Schedule F Loose-Load Vibration
Schedule I Low PressureA
Schedule E Vehicle Vibration
Schedule J Concentrated Impact
14
Warehousing (partial cycle to be added to other cycles as needed)
Schedule A Handling
Schedule B Warehouse Stacking
…
…
…
…
15
Export/Import shipment for intermodal container or roll on/roll off trailer (partial cycle to be added to other cycles as needed)
Schedule A Handling
Schedule C Vehicle Stacking
Schedule A Handling
…
…
…
3
Schedule A Handling
Schedule A Handling
D4169 − 16 TABLE 1
DC
Distribution Cycle
Continued
First
Second
Performance Test Schedule Sequence (see Section 9 for Test Schedule definition) Third Fourth Fifth
Sixth
16
Export/Import shipment for palletized cargo ship (partial cycle to be added to other cycles as needed)
Schedule A Handling
Schedule C Vehicle Stacking
Schedule A Handling
…
…
…
17
Export/Import shipment for break bulk cargo ship (partial cycle to be added to other cycles as needed)
Schedule A Handling
Schedule C Vehicle Stacking
Schedule A Handling
…
…
…
18
Non-Commercial Government shipments per MIL-STD-2073-1
Seventh
Refer to Annex A1 for Test Schedules applying to DC-18.
A
This high altitude, non-pressurized transport simulation test may be deleted from this distribution cycle when testing shipping units that contain primary packages that have a porous material.
7.2 In many cases, the acceptance criteria can be the following: Criterion 1—Product is damage-free. Criterion 2—Package is intact. Criterion 3—Both criteria 1 and 2. Often, this means that the shipping container and its contents are suitable for normal sale and use at the completion of the test cycle. Detailed acceptance criteria may allow for accepting specified damage to a product or its package. The form and content of acceptance criteria may vary widely, in accordance with the particular situation. Methods may range from simple pass-fail judgments to highly quantitative scoring or analysis systems.
origin and destination points of a distribution cycle, particularly for export/import cycles.) 6.1.1 Conduct the test at standard conditions and compensate for the effects of any climatic condition. Condition the shipping units to a standard atmosphere of 73.4 6 2°F (23 6 1°C) and 50 6 2 % relative humidity. Condition fiberboard containers in accordance with Practice D4332. The same atmospheric condition should be used for any assurance level. A conditioning period of 72 h, or sufficient time to reach equilibrium of all parts of the package and product is recommended. Tests should be conducted in the conditioned atmosphere whenever possible. If not possible, conduct the tests as soon after removal from the conditioning atmosphere as practicable. Recondition the shipping units to the standard atmosphere as necessary during the test plan. 6.1.2 In some circumstances, it may be necessary to conduct some or all of the tests at special climatic conditions, such as those given in Practice D4332, or Test Method D951, or others (salt, spray, water immersion, humidity, or temperature). The same climatic condition should be used for any assurance level. A conditioning period should be provided which will allow sufficient time to reach equilibrium of all parts of the package and product. Tests should be conducted in the conditioned atmosphere whenever possible. If not possible, conduct the tests as soon after removal from the conditioning atmosphere as practicable. Recondition the shipping units as necessary during the test plan. For atmospheres other than the standard conditioning atmosphere, the user must determine the appropriate compressive load factor for warehouse and vehicle stacking, as the factors given in 11.2 are based on testing under the standard test atmosphere.
8. Procedure 8.1 Define Shipping Unit—Describe shipping unit in terms of size, weight, and form of construction. See 3.2.7. Determine whether the container will be manually or mechanically handled. 8.2 Establish Assurance Level—Specify a level of test intensity. The level should be one of three pre-established assurance levels. This must be pre-established based on the product value, the desired level of anticipated damage that can be tolerated, the number of units to be shipped, knowledge of the shipping environment, or other criteria. Assurance Level II is suggested unless conditions dictate otherwise. Assurance Level I provides a more severe test than II. Assurance Level III provides a less severe test than II. The assurance level may be varied between schedules (see Sections 10 – 15) if such variations are known to occur. The test levels used should be reported. See Section 18.
7. Acceptance Criteria
8.3 Determine Acceptance Criteria—Acceptance criteria are related to the desired condition of the product and package at the end of the distribution cycle. See Section 7.
7.1 Acceptance criteria must be established prior to testing and should consider the required condition of the product at receipt. The organizations conducting the test may choose any acceptance criteria suitable for their purpose. It is advisable to compare the type and quantity of damage that occurred to the test specimens with the damage that occurs during actual distribution and handling or with test results of similar containers whose shipping history is known.
8.4 Select Distribution Cycle—Select a Distribution Cycle from the available standard distribution cycles compiled in Table 1. Use the DC that most closely correlates with the projected distribution. When the distribution is undefined, the general distribution cycle DC-1 should be selected. When the 4
D4169 − 16 system that will be handled by mechanical means. Manual and mechanical handling are described further in 10.2 and 10.3.
anticipated distribution is well understood, a special distribution cycle DC-2 may be specified. In using DC-2, the user selects test schedules from Section 9 and specifies the test sequence (see Appendix X2 for more details). For purposes of DC-3 and DC-13, the bottom of a single package is the surface on which the package rests in its most stable orientation. The identified bottom should be utilized for purposes of determining the starting orientation of each test schedule within the above stated distribution cycles.
10.2 Manual Handling—The test levels and the test method for this schedule of the distribution cycle are intended to determine the ability of the shipping unit to withstand the hazards occurring during manual handlings, such as loading, unloading, stacking, sorting, or palletizing. The main hazards from these operations are the impacts caused by dropping or throwing. Size, weight, and shape of the shipping unit will affect the intensity of these hazards. Several test method options are permitted, including free fall and simulated drop test using shock machines. While these test methods produce similar results, the shock machine method produces more control of orientations of impact; see Test Method D5487 for limitations of the shock machine method. 10.2.1 For long narrow packages that are mechanically sorted, another hazard to be simulated is bridge impact (10.2.4). 10.2.2 Mechanical handling (10.3) may be used when it is anticipated that handling will be by mechanical means only. 10.2.3 For the free-fall and shock machine tests, recommended drop heights, the number of drops, the sequence of drops, and the shipping unit orientation at impact are as follows: Test Method D5276, D5487. Conditioning—See Section 6.
8.5 Write Test Plan—Prepare a test plan by using the sequence presented in Table 1 for the distribution cycle selected. Obtain the test intensities from the referenced schedules. The test plan intensity details must take into account the assurance levels selected as well as the physical description of the shipping unit. Table 1 thus leads to a detailed test plan consisting of the exact sequence in which the shipping unit will be subjected to the test inputs. The test schedules associated with each element reference the existing ASTM test methods for clarification of the equipment and techniques to be used to conduct the test. 8.5.1 Sample test plans are provided in Appendix X1. 8.6 Select Samples for Test—See Section 5. 8.7 Condition Samples—See Section 6. 8.8 Perform Tests—Perform tests as directed in reference ASTM standards and as further modified in the special instructions for each test schedule. 8.9 Evaluate Results—Evaluate results to determine if the shipping units meet the acceptance criteria. See Section 7.
Shipping Weight, lb (kg) 0 to 20 (0 to 9.1) 20 to 40 (9.1 to 18.1) 40 to 60 (18.1 to 27.2) 60 to 80 (27.2 to 36.3) 80 to 100 (36.3 to 45.4) 100 to 200 (45.4 to 90.7)
8.10 Document Test Results—Document test results by reporting each step. See Section 18. 8.11 Monitor Shipments—When possible, obtain feedback by monitoring shipments of the container that was tested to ensure that the type and quantity of damage obtained by the laboratory testing correlates with the damage that occurs in the distribution cycle. This information is very useful for the planning of subsequent tests of similar shipping containers.
Number of Impacts at Specified Height
9. Hazard Elements and Test Schedules
One Two Two
9.1 Hazard Elements and Test Schedules are categorized as follows: Schedule A B C D E F G H I J
Hazard Element Handling—manual and mechanical Warehouse Stacking Vehicle Stacking Stacked Vibration Vehicle Vibration Loose Load Vibration Rail Switching Environmental Hazard Low Pressure Hazard Concentrated Impact
One
Test Section 10 drop, impact, stability compression 11 compression 11 vibration 12 vibration 12 repetitive shock 13 longitudinal shock 14 cyclic exposure 15 vacuum 16 impact 17
Number of Impacts at Specified Height One Two Two
10. Schedule A—Handling—Manual and Mechanical:
One
10.1 There are two types of handling hazard element, manual and mechanical. The manual handling test should be used for single containers, smaller packages, and any shipping container that can be handled manually, up to a weight of 200 lb (90.7 kg). Mechanical handling should be used for unitized loads, large cases and crates, and any shipping container or
24 21 18 15 12 10
Drop Height, in. (mm) Assurance Level I II III (610) 15 (381) 9 (229) (533) 13 (330) 8 (203) (457) 12 (305) 7 (178) (381) 10 (254) 6 (152) (305) 9 (229) 5 (127) (254) 7 (178) 4 (102)
Impact Orientation First Sequence of Distribution Cycle Box top adjacent bottom edges diagonally opposite bottom corners bottom
Bag or Sack face two sides both ends
Cylindrical Container top two sides 90° apart bottom edges 90° apart
opposite face
bottom
Impact Orientation Second Sequence of Distribution Cycle Box vertical edge adjacent side faces one top corner and one adjacent top edge see Note 1
Bag or Sack face two sides both ends
Cylindrical Container top two sides 90° apart bottom edges 90° apart
see Note 1
see Note 1
NOTE 1—On the last impact of the last manual handling sequence in a distribution cycle, the impact should be made at twice the specified height or equivalent velocity change. (This is the final (sixth) drop in the sequence, not an additional drop.) The drop should be in the impact orientation most likely for a drop to occur, usually the largest face or the bottom. For distribution cycles where any drop orientation is possible (that is, shipments via carriers that mechanically sort packages), this drop
5
D4169 − 16 Test Method—D880, D4003, D6055, D6179. Conditioning—See Section 6. 10.3.2.1 All Methods of Truck Handling—Pick up, transport around test course, and set down in accordance with Test Methods D6055, Method A for fork lift, Method B for spade lift, Method C for clamp, and Method D for pull pack.
should be in the most critical or damage-prone orientation, as defined in Test Method D5276. NOTE 2—The equivalent velocity change corresponding to the specified drop height used for the shock machine method shall be calculated as specified in Test Method D5487.
10.2.4 Bridge Impact Test: Test Method—D5265. Conditioning—See Section 6. 10.2.4.1 Conduct bridge impacts on long, narrow shipping units which have a length of at least 36 in. (915 mm) and each of the other two dimensions are 20 % or less of the longest dimension. 10.2.4.2 These tests are required only once in any test schedule sequence.
Assurance Level I II III
(1) For shipments via less-than-truckload (LTL), simulate transfer terminal handling by performing fork lift truck transport over a floor hazard described as follows: a modified nominal 2 by 6 in. board with one edge beveled full height at 45° (see Fig. 1) shall be placed on the course in a position where both lift truck wheels on one side must pass over it during each handling sequence, and a second modified nominal 2 by 6 in. board shall be placed on the course after the 90° turn in such a position that both lift truck wheels on the opposite side must pass over it during each handling sequence.
10.3 Mechanical Handling—The test levels and the test method for this schedule of the distribution cycle are intended to determine the ability of large and heavy shipping units, single packages with pallet or skid, and unitized loads to withstand the mechanical handling hazards that occur during loading, unloading, sorting, or stacking. For large shipping cases and crates and any single package with pallet or skid, different test methods are used versus unit loads. For various types of unit loads, test methods also vary, depending on the method of truck handling: fork, clamp, spade, or pull/pack. 10.3.1 Large Shipping Cases and Crates and Single Packages with Pallet or Skid—Perform the following test sequences: Test Method—D6179, D880, D4003. Conditioning—See Section 6. 10.3.1.1 Fork Lift Truck Handling—One rotational flat drop from each opposite base edge in accordance with Method C of Test Methods D6179 and one rotational drop on each of two diagonally opposite base corners in accordance with Method B of Test Methods D6179. Gross Weight, lb (kg) 0 to 500 (0 to 226.8) Over 500 (226.8)
10.3.2.2 All Methods of Truck Handling—Impact all four sides of the shipping unit in accordance with Test Method D880 Procedure B. Alternately, use Test Method D4003, Method B using a short duration programmer, assuming the coefficient of restitution is 0.0 and the total velocity change is equivalent to the specified impact velocity. Assurance Level I II III
Impact Velocity ft/s(m/s) 5.75 (1.75) 4.0 (1.22) 3.0 (0.91)
10.3.2.3 Fork Lift Truck Handling—One rotational flat drop from each opposite base edge in accordance with Method C of Test Methods D6179. Gross Weight, lb (kg) 0 to 500 (0 to 226.8) Over 500 (226.8)
Drop Height, in. (mm) Assurance Level I II III 12 (305) 9 (229) 6 (152) 9 (229) 6 (152) 3 (076)
Drop Height, in. (mm) Assurance Level I II III 12 (305) 9 (229) 6 (152) 9 (229) 6 (152) 3 (76)
11. Schedule B—Warehouse Stacking and Schedule C—Vehicle Stacking:
10.3.1.2 Crane Handling—(Conduct this test only if cranes are used for handling in the distribution process.) One drop flat on bottom and one drop on base edge in accordance with Method D of Test Methods D6179. Use the same drop heights versus shipping unit weight as in 10.3.1.1. 10.3.1.3 Side Impact Test—Impact all four sides of the shipping unit in accordance with Test Method D880, Procedure B. Alternately, use Test Method D4003 Method B using a short duration programmer, assuming the coefficient of restitution is 0.0 and the total velocity change is equivalent to the specified impact velocity. Assurance Level I II III
Cycles (Round Trips) 8 5 3
11.1 The test levels and the test methods for these schedules of a distribution cycle are intended to determine the ability of the shipping unit to withstand the compressive loads that occur during warehouse storage or vehicle transport. The required loading must consider the effects of length of time in storage, the alignment or stacking pattern of the container, variability in container strength, moisture content, temperature, previous handling and transportation, method of load support, and vibration. The minimum required loads for typical shipping
Impact Velocity ft/s(m/s) 5.75(1.75) 4.0(1.22) 3.0(0.91)
10.3.1.4 Tip Test—In accordance with Method F of Test Methods D6179. 10.3.1.5 Tipover Test—In accordance with Method G of Test Methods D6179 if shipping unit fails Tip Test above. 10.3.2 Unitized Loads—Perform the following tests sequences as appropriate for the method of truck handling:
FIG. 1 Floor Hazard
6
D4169 − 16 load the shipping unit to the computed load value, as calculated below. Remove the load within 3 s after reaching the specified value. If the average shipping density factor (Mf) for the specific distribution system is not known, use a value of 10 3 lb/ft (160 kg/m3).
units which include the combined effects of the above factors are recommended below for Schedule B—Warehouse Stacking and Schedule C—Vehicle Stacking (select test levels for either warehouse or vehicle stacking as defined in the distribution cycle): Test Method D642. Conditioning—73.4 6 2°F (23 6 1°C), 50 6 2 % relative humidity in accordance with Practice D4332.
L 5 Mf 3 J
where: L = Mf = J = H =
11.2 Use the following test levels: F Factors Assurance Level Schedule Schedule B—Warehouse C—Vehicle Shipping Unit Construction I II III I II III 1. Corrugated, fiberboard, or plastic container 8.0 4.5 3.0 10.0 7.0 5.0 that may or may not have stress–bearing interior packaging using these materials, and where the product does not support any of the load. 2. Corrugated, fiberboard, or plastic container 4.5 3.0 2.0 6.0 4.5 3.0 that has stress-bearing interior packaging with rigid inserts such as wood. 3. Containers constructed of materials other 3.0 2.0 1.5 4.0 3.0 2.0 than corrugated, fiberboard, or plastic that are not temperature or humidity sensitive or where the product supports the load directly, for example, compression package. 4. If the product supports a known portion of the load, the F factor is calculated in the following manner:
F 5 P ~ F p ! 1C ~ F
c
!
(1)
l
=
w K F
= = =
computed load, lbf or N, shipping density factor, lb/ft3 or kg/m3, 1 lbf/lb or 9.8 N/kg, maximum height of stack in transit vehicle (if vehicle stack height is unknown, use 108 in.(2.7 m)), in. or m, see Note 3, height of shipping unit or individual container, in. or m, length of shipping unit or individual container, in. or m, width of shipping unit or individual container, in. or m, 1728 in.3/ft3 or 1 m3/m3, and a factor to account for the combined effect of the individual factors described above.
12. Schedule D—Stacked Vibration and Schedule E—Vehicle Vibration: 12.1 The test levels and test methods for these distribution cycles are intended to determine the shipping units ability to withstand the vertical vibration environment during transport and the dynamic compression forces resulting from vehicle stacking. The test levels and methods account for the magnitude, frequency range, duration and direction of vibration. Select the Schedule D—Stacked Vibration or Schedule E—Vehicle Vibration (no stacking) test as defined by the distribution cycle. Test methods for sine and random vibration are permitted testing options. The two methods are not equivalent and will not necessarily produce the same results. The random test method results in a better simulation of actual transport vibration environments, and is the preferred method for qualification. The sine test method is often used as a means of determining and observing system resonances and can be used in conjunction with the random method.
If a full pallet load is tested, F factors may be reduced by 30 %. 11.3 For warehouse stacking and vehicle stacking made up of identical shipping units, load the shipping unit to the computed load value, as calculated below. Remove the load within 3 s after reaching the specified value. H2h 3F h
=
(3)
NOTE 3—The value for H, when unknown, is reduced to 54 in. (1.4 m) from 108 in. (2.7 m) for packages under 30 lb (13.6 kg) and 2.0 ft3 (0.056 m3) or less in size when applied to a vehicle stacking hazard element in LTL shipments.
where: Fp = factor given above for compression package (construction Type 3), P = fraction of load supported by product, Fc = factor given above for appropriate container construction, and C = fraction of load supported by container.
L 5 M 3J
h
l 3w 3h H 2 h 3 3F K h
(2)
where: L = computed load, lbf or N, M = mass of one shipping unit or individual container, lb or kg, J = 1 lbf/lb or 9.8 N/kg, H = maximum height of stack in storage or transit vehicle (if vehicle stack height is unknown, use 108 in.(2.7 m)), in. or m, h = height of shipping unit or individual container, in. or m, and F = a factor to account for the combined effect of the individual factors described above.
12.2 Schedule D—Stacked Vibration—Perform the test along the vertical axis with the load in the normal shipping orientation or with the predetermined bottom orientation (as specified in DC-3) facing down. It is permissible to use a concentrated dead load to simulate an upper unit load or mixed commodities. The concentrated load may be calculated from the formulas in 11.3 and 11.4, with the F factor set equal to 1. Recommended intensities and durations for the random tests are given in 12.4, and those for sine tests are given in 12.5. 12.3 Schedule E—Vehicle Vibration—Perform the test for each possible shipping orientation (up to three axes). Recommended intensities and durations for the random tests are given in 12.4, and those for sine tests are given in 12.5.
11.4 For vehicle stacking made up of mixed commodities and shipped in an LTL or small package delivery environment, 7
D4169 − 16 12.4.2.1 For the Truck Profile test, it is recommended to use a combination of all three Test Levels (low, medium, and high) for a better simulation of actual truck vibration environments. The Truck test should be performed in a 1 h (60 min) loop that can be repeated for longer duration simulations. The recommended test durations for the random vibration truck profile are as follows: (1) Low Level for 40 minutes. (2) Medium Level for 15 minutes. (3) High Level for 5 minutes. 12.4.2.2 For vehicle vibration tests when more than one shipping orientation is possible, the total duration should be distributed evenly between the orientations tested.
12.4 Random Test Option: Test Method D4728. Conditioning—See Section 6. 12.4.1 The power spectral densities in Tables 2-4, as defined by their mode of transport, frequency and amplitude breakpoints, and test durations are recommended. 12.4.1.1 Conducting the Truck Profile test is recommended for Distribution Cycles 1, 3, 4, 5 and 6. 12.4.1.2 Conducting the Rail Profile test is recommended for Distribution Cycles 7, 8 and 11. 12.4.1.3 A 60 min test using the Truck Profile followed by a 120 min test using the Rail Profile is recommended for Distribution Cycles 9 and 10. 12.4.1.4 A 60 min test using the Truck Profile followed by a 120 min test using the Air Profile is recommended for Distribution Cycles 12 and 13. 12.4.2 If more detailed information is available on the transport vibration environment or the shipping unit damage history, it is recommended that the procedure be modified to use such information. The test time required to reproduce shipping damage is dependent on the mode of failure, as well as the vibration level. Test durations ranging from 30 min to 6 h have been used successfully for different product or package types. A 3 h (180 min) duration is reasonable to use in the absence of specific shipping or testing experience.
NOTE 4—When conducting the Truck Profile, Assurance Levels I, II, and III are not used.
12.5 Sine Test Option: Test Methods D999, Method B or C. Conditioning—See Section 6. Special Instructions—Dwell time is for each noted product or package resonance up to four discrete resonances. If more than four resonances are noted, test at the four frequencies where the greatest response is noted. In frequency sweeps it is advisable to consider the frequency ranges normally encountered in the type of transportation being considered. The
TABLE 2 TRUCK—Power Spectral Density Levels Frequency 1 3 4 6 12 16 25 30 40 80 100 200 Overall Grms
Power Spectral Density Level, G2/Hz Medium Level 0.00072 0.018 0.018 0.00072 0.00072 0.0036 0.0036 0.00072 0.0036 0.0036 0.00036 0.000018 0.54
High Level 0.00072 0.030 0.030 0.0012 0.0012 0.0060 0.0060 0.0012 0.0060 0.0060 0.00060 0.000030 0.70
8
Low Level 0.0004 0.010 0.010 0.00040 0.00040 0.0020 0.0020 0.00040 0.0020 0.0020 0.00020 0.000010 0.40
D4169 − 16 TABLE 3 RAIL—Power Spectral Density Levels Frequency 1 2 50 90 200 Overall Grms
I 0.00002 0.002 0.002 0.0008 0.00002 0.41
Power Spectral Density Level G2/Hz Assurance Level II 0.00001 0.001 0.001 0.0004 0.00001 0.29
III 0.000005 0.0005 0.0005 0.0002 0.000005 0.2
TABLE 4 AIR—Power Spectral Density Levels Power Spectral Density Level G2/Hz Assurance Level II 0.0002 0.01 0.01 0.00001 1.05
Frequency 2 12 100 300 Overall Grms
I 0.0004 0.02 0.02 0.00002 1.49
resonant frequency(ies) may shift during test due to changing characteristics of the container system. It is suggested that the dwell frequency be varied slightly during the test to detect any
III 0.0001 0.005 0.005 0.000005 0.74
shift and to continue testing at the frequency of maximum response. Use the following test levels:
9
D4169 − 16 Assurance Level I II III
Frequency Range, Hz 3 to 100 3 to 100 3 to 100
Amplitude (O-Peak), g Rail Truck 0.25 0.5 0.25 0.5 0.25 0.5
deemed to be most sensitive to damage. For the fourth impact, rotate the specimen 180° on the carriage.
Dwell Time, min 15 10 5
Assurance Level I
Impact Number 1 2 3 4 (rotate 180°)
II
1 2 3 4 (rotate 180°)
13. Schedule F—Loose Load Vibration: 13.1 The test levels and the test method for this schedule of the distribution cycle are intended to determine the ability of the shipping unit to withstand the repetitive shocks occurring during transportation of bulk or loose loads. The test levels and test method account for amplitude, direction, and duration of the repetitive shocks.
4 6 8 8
(m/s) 1.79 (± 0.22) 2.68 (± 0.22) 3.58 (± 0.22) 3.58 (± 0.22)
4 6 6 6
(± (± (± (±
1.79 2.68 2.68 2.68
0.5) 0.5) 0.5) 0.5)
(± (± (± (±
0.22) 0.22) 0.22) 0.22)
14.4 Procedure Modification—If more detailed information is available on backload or shock characteristics it is recommended that the above procedure be modified to use such information.
13.2 Use the following test levels: Test Method—D999, Method A1 or A2. Conditioning—See Section 6. Special Instructions—Dwell time distributed 50 % along normal vertical shipping axis or with the predetermined bottom orientation (as specified in DC-3 and DC-13) facing down and remaining 50 % evenly along all other possible shipping orientations Assurance Level I II III
Velocity mph (± 0.5) (± 0.5) (± 0.5) (± 0.5)
15. Schedule H—Environmental Hazard: 15.1 This schedule is intended to provide for the anticipated and often rapid changes in ambient conditions associated with the military distribution of material. This schedule determines the susceptibility of the total pack to the effects of moisture, temperature shock, or the combined effects of cyclic exposure. The result of conditioning may involve the observation/ measurement of moisture or water within packs, evidence of corrosion on packaged items, or compromise of the enclosure’s structural integrity such that physical protection can no longer be ensured. Testing shall be in accordance with Test Method D951, where spray intensities of 4 6 0.5 in./h (100 6 10 mm/h) are used for Assurance Level I and 2 6 0.5 in./h (50 6 10 mm/h) for Level II. Water spray temperature is as listed in the table below. During spray segments the air temperature is uncontrolled at ambient conditions. 15.2 Test levels shall be as follows:
Dwell Time, min 60 40 30
14. Schedule G—Simulated Rail Switching: 14.1 The test levels and test methods for this schedule are intended to determine the ability of the shipping unit to withstand the acceleration levels and compressive forces that might occur during rail switching operations. Test Method D4003, Test Method A or Test Method D5277. Conditioning—See Section 6. Special Instructions—Four impacts shall be performed. For railcars with standard draft gear, shock durations of 40 6 10 ms shall be used, as measured on the floor of the carriage. For railcars with long–travel draft gear, shock durations of 300 6 50 ms shall be used. Reference Association of American Railroads, General Information Bulletin No. 2. Note that Test Method D5277 is used for standard draft gear only. Refer to Test Methods D4003 or D5277 for specific instructions on how to instrument and conduct the test.
Assurance Level Temperature, °F (°C) I 160 ± 5 (71 ± 2) 55 ± 5 (13 ± 2) –5 ± 5 (–21 ± 2) 125 ± 5 (52 ± 2) 55 ± 5 (13 ± 2) 32 ± 5 (0 ± 2) 160 ± 5 (71 ± 2) 55 ± 5 (13 ± 2) –65 ± 5 (–54 ± 2) 160 ± 5 (71 ± 2) 55 ± 5 (13 ± 2) –65 ± 5 (–54 ± 2) 40 ± 5 (4 ± 2) 160 ± 5 (71 ± 2)
14.2 Procedure—Load shipping unit on carriage against bulkhead. Use a backload equivalent to a minimum of 3 ft lineal (0.9 m) of cargo. The package used as backload in contact with the test package must be identical to the test package.
II
14.3 Test Levels—Allow the carriage to impact a cushioned barrier in accordance with the following table. Assurance Level I shall be used for open-top rail car load tests. Assurance Level II shall be used for boxcar load tests for non-hazardous materials and for TOFC/COFC load tests for non-hazardous materials. There is no Assurance Level III for this Test Schedule. 14.3.1 If known, container impact surfaces should be the same as occur in actual shipment. If the shipping orientation is not known, or if more than one orientation is possible, the first three impacts should be on that test specimen surface which is
III
Water Spray X X X
X
X
Duration, h 16 2 2 2 2 16 4 2 2 16 2 2 3 16
160 ± 5 (71 ± 2) 14 55 ± 5 (13 ± 2) X 2 160 ± 5 (71 ± 2) 4 32 ± 5 (0 ± 2) 2 55 ± 5 (13 ± 2) X 2 The cyclic sequence shall be repeated on three consecutive days. At the end of the three day period, the unit pack being tested shall then set overnight 160 ± 5 (71 ± 2) 16 Not applicable
15.3 Duration time shall be measured starting the moment at which temperature setting is changed to next condition. 15.4 When specified in the contract, this test should be performed as part of the complete distribution cycle for the smallest complete shipping unit, as part of the contract. 10
D4169 − 16 18. Report 18.1 Report fully all the steps taken. At a minimum, the report should include: 18.1.1 Reference to this practice, 18.1.2 Description of product and shipping unit, including orientation of the product within the shipping unit, 18.1.3 Distribution cycle (DC) and test plan, 18.1.4 Assurance levels and rationale, 18.1.5 Number of samples tested, 18.1.6 Conditioning used, 18.1.7 Acceptance criteria, 18.1.8 Vibration option used, random or sine, 18.1.9 Random vibration power spectral density plot, if used, 18.1.10 Pressure levels and duration for high altitude exposure, if used, 18.1.11 Type of lift truck handling tests used, if any, 18.1.12 Variation from recommended procedures, and 18.1.13 Condition of specimens after test. 18.2 Government Shipments—In addition to 18.1.2 – 18.1.13, the complete report includes: 18.2.1 Party, other than contractor, performing testing, 18.2.2 Testing facility used, other than contractor’s, 18.2.3 Government representative witnessing testing, and 18.2.4 When environmental hazard is performed for other than smallest complete shipping unit (see 15.4).
16. Schedule I—Low Pressure (High Altitude) Hazard 16.1 This schedule is intended to provide for the anticipated reduction in pressure when packaged products are transported via certain modes of transport, such as feeder aircraft or by ground over mountain passes. This test shall be conducted in accordance with levels described in Test Method D6653. This test should be included for products and packages that could be sensitive to a low pressure environment, for example, sealed flexible non-porous packages, liquid containers, or porous packages that may be packed in such a manner as to be adversely affected by low pressure environments. This test may be deleted from DC 12 and 13 when shipping units contain primary packages that have a porous material (porous packaging material is defined in Terminology F1327). 16.2 Test the packages to the expected altitude levels encountered during shipment. If these are not known precisely, use levels recommended by Test Method D6653 of pressure equivalent to 4267 m (14 000 ft.) for a period of 60 min. The test duration and pressure levels may be modified based on knowledge of the shipping environment, product value, desired damage level acceptances, or other criteria as described in Test Method D6653. 17. Schedule J—Concentrated Impact 17.1 This schedule provides a simulation of anticipated low level concentrated impacts as received by packages during sorting operations and in transit. The test is only applicable to lightweight singlewall corrugated shipping containers (under 275 Burst or 44 ECT) and plastic film wrapped packages and unitized loads. Test the appropriate packages or unit loads according to Test Method D6344.
19. Precision and Bias 19.1 The precision and bias of this practice are dependent on those of the various test methods used, and cannot be expressly determined. 20. Keywords 20.1 compression test; distribution cycle; distribution environment; drop test; mechanical handling; package; packaging; random vibration; shipping container; shipping unit; vacuum; vibration
17.2 The impact energy for this test shall be 4.0 ft-lbf (5.4 J) as imposed by the cylindrical mass falling a vertical drop distance of 32 in. (0.8 m).
ANNEX (Mandatory Information) A1. DISTRIBUTION CYCLE DC-18 FOR NON-COMMERCIAL GOVERNMENT SHIPMENTS PER MIL-STD-2073–1
the last manual handling sequence is the same as all other impacts. Use the first sequence impact orientations for the third handling schedule. Test small shipping units using the following test levels:
A1.1 Performance Test Schedule SequenceA1.1 1 2 3 4 5 6 7 8
Handling (A1.2) Warehouse or Vehicle Stacking (A1.3) Handling (A1.2) Low Pressure Hazard (A1.4) Environmental Hazard (A1.5) Loose Load Vibration (A1.6) Vehicle Vibration (A1.7) Handling (A1.2)
Shipping Weight, lb (kg) 0 to 30 (0 to 13.6) over 30 to 75 (over 13.6 to 34) over 75 to 150 (over 34 to 68)
A1.2 Handling—Manual and Mechanical
Drop Height, in. (mm) Assurance Level I II 30 (762) 24 (610) 24 (610) 18 (457) 18 (457) 15 (381)
A1.2.2 Mechanical Handling:
A1.2.1 Manual Handling—This test schedule applies to small shipping units. Description of this schedule is in accordance with 10.2.3, except that the height of the last impact of 11
D4169 − 16 top and bottom rims at diagonally opposite quadrants. Care must be taken to prevent the container from rolling on the support. Additional impacts shall be made in the same manner in different quadrants separated by an approximate 90°, for a total of four drops. For corner drops, use Method B of Test Methods D6179, except that one corner of the shipping unit base shall be supported on a 6 in. (150 mm) height block while the other corner on the same end or side rests on a 12 in. (300 mm) height block. Each corner will be impacted, for a total of four drops. Both edgewise and cornerwise drops shall be performed on large rectangular shipping units. For all rotational drops, test with the lowest drop height indicated by either gross weight or maximum dimension, using the following test levels.
A1.2.2.1 For large shipping units, this schedule is intended to provide a number of testing variations describing specific mechanical handling hazards that occur in government distribution for shipping cases, crates, unitized loads, and cylindrical containers. Required tests for rectangular shipping units include: tip/tipover; fork lift truck transport; rotational drops, both edgewise and cornerwise; and lateral impacts. For Assurance Level I, shipping cases and crates and unitized loads shall also be subjected to sling handling. For cylindrical shipping units, only rotational edgewise drop tests shall apply. Table A1.1 shall be used as a guide in determining both the required tests and the sequence to be followed. A1.2.2.2 Specific tests required: (1) Shipping Cases, Crates, and Unitized Loads–Tip/ Tipover—Shipping cases and crates shall be subjected to both tip and tipover tests for Assurance Level I, following the requirements of Test Method D6179, Methods F and G. For unitized loads, only the tip test will be required. The tip test shall be performed for Assurance Level II for all rectangular shipping units. Tip/tipover requirements shall only be required during the first handling sequence of DC-18. The tip test is useful for determining acceptable shipping unit dimension and center of gravity. For tipover, one impact is required on each of two opposite sides, as determined by the initial side having the lowest height–to–width ratio. (2) Shipping Cases, Crates, and Unitized Loads—Fork Lift Truck Transport—Pick up, transport around test course as defined in Test Methods D6055, Method A, for a total of two cycles (round trips) in the case of Assurance Level I, and one cycle for Assurance Level II. Within the minimum 100 ft (30.5 m) obstacle zone, parallel pairs of 1 by 6 in. (25 by 150 mm) boards, of a length to extend completely across the aisle and spaced 54 in. (1.37 m) apart, are laid flat at intervals of 30, 60, and 90 ft (9.1, 18.3, and 27.4 m). Board angles to the truck’s path shall be 90, 60, and 75 degrees respectively, with the left wheel striking first over the second obstacle (board pairs) and the right wheel first over the third (3) Shipping Cases, Crates, Unitized Loads and Cylindrical Containers—Rotational Drops—For edge drops, use Method A of Test Methods D6179 with a 6 in. (150 mm) height timber edge support. In the case of rectangular shipping units, drops are made on each opposite edge of the unit’s base, for a total of four impacts. For cylindrical shipping units, drops shall be made with the unit on its side, such that impacts occur on
Gross Weight, lb (kg) or Maximum Dimension, in (mm) over 100 to 250 (45 to 113) or over 60 to 66 (1524 to 1676) over 250 to 500 (to 227) or over 66 to 78 (to 1981) over 500 to 1000 (to 454) or over 78 to 90 (to 2286) over 1000 (over 454) or over 90 (2286)
Drop Height, in. (mm) Assurance Level I II 30 (762) 24 (610) 24 (610)
18 (457)
18 (457)
12 (305)
12 (305)
9 (229)
NOTE—For smaller dimension containers, where it is not possible to reach the desired drop height on corner or edge drops, raise the corner or edge until the container is at its balance point and then release the container to fall on the intended corner or edge.
(4) Shipping Cases, Crates, and Unitized Loads–Lateral Impacts—Note that this test is to be performed only during the second handling sequence of Distribution Cycle 18. Testing shall be in accordance with Test Method D880, Procedure B. Alternatively, testing may be in accordance with Test Method D4003, Method B, using a short duration programmer, assuming the coefficient of restitution is 0.0 and the total velocity change is equivalent to the specified impact velocity. Selection of apparatus, as defined within these test methods, shall also be at the option of the package designer/contractor. As a requirement for Assurance Level I, the impact velocity shall be 7.3 ft/s(2.23 m/s). One lateral impact shall be performed on each side (including ends) surface having a dimension less than 9.5 ft (2.9 m). A4 by 4 in. (100 by 100 mm) timber, placed so as to contact the lower edge of the shipping unit, shall be used as an impacting hazard when evaluating unitized loads and demountable shipping cases.
TABLE A1.1 Mechanical Handling for DC-18, Required Tests and Sequence Assurance LevelA
TipB
TipoverB
Forklift Transport
I II
X X
X –
2 cycles 1 cycle
Unitized Loads
I II
X X
–
2 cycles 1 cycle
X X
Cylindrical
I II
–
–
–
X X
Large Shipping Unit Shipping Cases & Crates
A
Rotational Drops Edge Corner X X X X
As referenced in 3.2.2, Assurance Levels I and II equate to military levels of protection A and B, respectively. Test to be performed only during the first handling sequence of DC-18. C Test to be performed only during the second handling sequence of DC-18. D Test to be performed only during the third handling sequence of DC-18. B
12
Lateral ImpactsC
Sling HandlingD
X –
X –
X X
X –
X –
–
–
–
D4169 − 16 (1) For Assurance Levels I and II, the dwell time shall be 2 hours on the base for unitized loads and shipping containers with skid bases, and 1 hour in each of three mutually perpendicular axes for all other shipping containers which may be transported in any orientation. (2) For Assurance Level III, dwell time shall be 15 minutes on the shipping container base plus 7.5 minutes on each of two adjacent sides.
(5) Shipping Cases, Crates, and Unitized Loads—Sling Handling—Test shipping cases, crates, and unitized loads for sling handling, in accordance with Method F of Test Methods D6055, only for Assurance Level I. Note that this test is performed only during the third handling sequence. A1.3 Warehouse or Vehicle Stacking—Refer to Section 11, Schedule B—Warehouse Stacking and Schedule C—Vehicle Stacking.
A1.7 Vehicle Vibration:
A1.4 Low Pressure (High Altitude) Hazard:
A1.7.1 The test method and levels for this schedule are intended to determine the ability of shipping units to withstand random vibration during transport. Test Method—Refer to MIL-STD-810F. Conditioning —See Section 6.
A1.4.1 This schedule is intended to provide for the anticipated reduction in pressure when packaged products are transported via certain modes of transport, such as by aircraft or by ground over mountain passes. This test should be included for products and packages that could be sensitive to a low pressure environment, for example, sealed flexible nonporous packages, liquid containers, or porous packages that may be packed in such a manner as to be adversely affected by low pressure environments.
A1.7.2 Conduct a random vibration test for a total of 9 h using the PSD (power spectral densities) shown below. For the vertical vibration, conduct the test for 3 h on a vertical motion vibration machine. For transverse and longitudinal vibration, conduct the test on a horizontal motion vibration machine for 3 h in each axis.
A1.4.2 For pressurized aircraft transport, test the packages to pressures recommended in Test Method D6653. For nonpressurized aircraft transport, use 4572 km (15 000 ft) as expected altitude (corresponding pressure in a standard atmosphere: 57.2 kPa or 8.3 psia) and maintain for a period of 60 min.
Vertical Frequency, PSD, Hz g2/Hz 10 0.01500 40 0.01500 500 0.00015 1.04 g rms
A1.5 Environmental Hazard: A1.5.1 Refer to Section 16, Schedule H—Environmental Hazard. A1.6 Loose Load Vibration: A1.6.1 The test levels and the test method for this schedule of the distribution cycle are intended to determine the ability of the shipping unit to withstand the repetitive shocks occurring during transportation of bulk or loose loads. The test levels and test method account for amplitude, direction, and duration of the repetitive shocks.
Transverse Frequency, PSD, Hz g2/Hz 10 0.00013 20 0.00065 30 0.00065 78 0.00002 79 0.00019 120 0.00019 500 0.00001 0.204 g rms
Longitudinal Frequency, PSD, Hz g2/Hz 10 0.00650 20 0.00650 120 0.00020 121 0.00300 200 0.00300 240 0.00150 340 0.00003 500 0.00015 0.740 g rms
A1.7.3 For the vertical motion test, mount test specimen to the vibration machine surface in a manner dynamically representative of the life cycle event simulated. For the transverse and longitudinal motion tests, fasten the test specimen to the vibration machine surface by the use of two or more straps over the specimen at right angle to the vibratory motion, tightened down to the machine surface to prevent movement. I-bolts with ratcheting straps are suggested restraining devices.
A1.6.2 Use the following test method and levels: Test Method D999, Method A1 or A2. Conditioning—See Section 6. Special Instruction—Dwell time shall be distributed as follows:
13
D4169 − 16 APPENDIXES (Nonmandatory Information) X1. EXAMPLE TEST PLANS
X1.2.8 Step 8, Perform Tests—Perform tests in accordance with the test plan in Step 5, as directed in the referenced ASTM standards and in the special instructions for each test schedule.
X1.1 The following examples will serve to illustrate the use of this practice: X1.2 Example A—Test a packaged commercial product. The moderate value and volume of shipment are typical of other products in the shipper’s line. No damage is acceptable and the package must be in good condition after the test. The fiberboard packaged product weighs 160 lb (73 kg), is 48 in. (1.2 m) long, 20 in. (0.5 m) wide, 24 in. (0.6 m) high, and stacked 2 high on pallets for storage and truckload shipment. The corrugated fiberboard container is 275 psi (1900 kPa) burst grade material. The customer stores palletized loads 2 high on the floor. The product does not support any of the load.
X1.2.9 Step 9, Evaluate Results—Examine products and packages to determine if the acceptance criteria have been met. X1.2.10 Step 10, Document Test Results—Write a report to cover all steps in detail, in accordance with Section 18. X1.3 Example B—Product to be tested is identical to the product from Example A, except that it will be shipped individually through an LTL distribution system, and there is no storage of more than one container high. Additional information is that the package has unsupported interior spans exceeding 12 in. (0.3 m) on all four sides, and has no pallet or skid.
X1.2.1 Step 1, Define Shipping Unit—Shipping unit to be tested is a typical pallet load. X1.2.2 Step 2, Establish Assurance Level—Assurance Level II will be used, based on value and volume of shipment.
X1.3.1 Step 1, Define Shipping Unit—Shipping unit to be tested is a single package.
X1.2.3 Step 3, Determine Acceptance Criteria at Assurance Level II: Criterion 1—No product damage. Criterion 2—All packages in saleable condition.
X1.3.2 Step 2, Establish Assurance Level—Assurance Level II will be used, based on value and volume of shipment. X1.3.3 Step 3, Determine Acceptance Criteria at Assurance Level II: Criterion 1—No product damage. Criterion 2—All packages in saleable condition.
X1.2.4 Step 4, Select Test Schedules—DC–6 will be used for this palletized, truckload shipment. X1.2.5 Step 5, Write Test Plan: Sequence Test Schedule Test Methods 1 A Handling— D6055 Method A Mechanical D880 Procedure B D6179 Method C
Level Pick up, transport around test course, set down, 5 cycles. Horizontal impact all four sides, 4.0 ft/s (1.22 m/s) Rotational drop, one impact on two opposite base edges from 6 in. (0.152 m).
2
D Stacked Vibration
D4728
“Truck” PSD profile, 0.52 g rms, duration 180 min, with load stacked on top.A
3
A Handling— Mechanical
D6055 Method A
Pick up, transport around test course, set down, 5 cycles. Horizontal impact all four sides, 4.0 ft/s (1.22 m/s) Rotational drop, one impact on two opposite base edges from 6 in. (0.152 m).
D880 Procedure B D6179 Method C
4
B Warehouse Stacking
D642
X1.3.4 Step 4, Select Test Schedules—DC-3 will be used for this single package shipment via LTL motor freight. X1.3.5 Step 5, Write Test Plan: Sequence Test Schedule Test Method D5276 1 A Handling— Manual
Compression of palletload to 2880 lbf (12 800 N) on F=4.5.
A
Alternative vibration test configurations, 1: test 2 full pallet loads high, or use a dead weight load to simulate the upper pallet load, 2: test a single individual container with 480 lb dead weight load to simulate the load stacked on top of bottom container.
X1.2.6 Step 6, Select Samples for Test—Select representative samples. X1.2.7 Step 7, Condition Samples—Condition to 23 6 1°C, 50 6 2 % relative humidity, in accordance with Practice D4332.
Level One drop on top, two drops on adjacent bottom edges, two drops on diagonally opposite bottom corners, one drop on bottom, drop height 7in. (178 mm).
2
D Stacked Vibration
D4728
Truck PSD profile, 0.52 g rms, 60 min on each of two adjacent sides and bottom with concentrated dead load on top, load weighing amount as calculated per D4169, 12.2
3
F Loose Load Vibration
D999, Method A1 or A2
20 min on bottom, 10 min on each of two adjacent sides.
4
A Handling— Manual
D5276
One drop on vertical edge, two drops on adjacent side faces, one drop on top corner, one drop on adjacent top edge, drop height 7 in. (178 mm). One drop on bottom, drop height 14 in. (355 mm).
X1.3.6 Step 6, Select Samples for Test—Select representative samples. 14
D4169 − 16 X1.3.9 Step 9, Evaluate Results—Examine products and packages to determine if the acceptance criteria have been met.
X1.3.7 Step 7, Condition Samples—Condition to 23 6 1°C, 50 6 2 % relative humidity, in accordance with Practice D4332.
X1.3.10 Step 10, Document Test Results—Write a report to cover all steps in detail, in accordance with Section 18.
X1.3.8 Step 8, Perform Tests—Perform tests in accordance with the test plan in Step 5, as directed in the referenced ASTM standards and in the special instructions for each test schedule.
X2. USING THE DC-2 DISTRIBUTION CYCLE
X2.1 The DC-2 distribution cycle is used when an anticipated distribution is well understood and other cycles, DC-3 through DC-18, are not sufficiently descriptive. The understanding of distribution may be developed in several ways, including: measurement of the environment with appropriate instrumentation; careful observation of the various hazard elements in distribution; reference to published authoritative information; product damage reports; or a combination thereof. X2.2 The user of DC-2 is allowed complete flexibility in developing a test plan that accurately reflects the anticipated distribution. This includes the ability to vary Assurance Levels between test schedules for each hazard element, as presently stated in 8.2 for application to any Distribution Cycle. The ability to modify test levels or other details within a test schedule is also permitted in DC-2 when experience has shown it more accurately correlates with actual experience.
1
Schedule
modified A-handling by the manufacturer
Test Method
Pick up, transport around test course, set down 3 times
D880 Procedure B
Incline impact on each end of the palletized load at 4 ft/s
2
D-transport stacked vibration
D4728 Method A
Truck PSD profile, 0.52 g rms, duration 3 h, two loads high
3
modified A-handling by customer
D6055 Method A
Pick up, transport around test course, set down 5 times
D880 Procedure B
Incline impact on each end of the palletized load at 4 ft/s Rotational drop, impact on other end base edge from 6 in.
(2) Comparing this test plan to X1.2, Example A, where DC-6 was used, the number of tests and intensities are somewhat less. X2.2.1.2 Example 2—Following reports of an unacceptable amount of corner damage in shipments of a consumer product direct from the manufacturer to the consumer via small parcel carriers, a thorough study of handling and transport has been made. Subsequent corner drop tests revealed that a drop of 42 in. high is needed to produce the type of damage reported and instrumented shipments have verified some drops at that height. The packaged product weighs 43 lb, and outside dimensions of the container are 24 in. length by 10 in. width by 42 in. depth (end-opening 32 ECT grade box). The container and interior corrugated packaging pieces provide all of the support in compression, and the container is marked with “ This Way Up” arrows in normal depth direction. There is no reported damage to the corrugated containers due to excessive compressive loads, and instrumented shipments verify that the container is almost always in a normal depth orientation (42 in. dimension upright) during transportation. The user of DC-2 develops a test plan that simulates the anticipated distribution, as follows:
Details of Test and Levels
D6055 Method A
Rotational drop, imipact one end base edge from 6 in.
D6179 Method C
X2.2.1 The following hypothetical examples illustrate instances where such flexibility is useful. X2.2.1.1 Example 1—For truckload shipments of palletized loads stacked two-high on trailers from a manufacturer to a customer, a thorough study of handling at both ends of the shipping cycle (manufacturer and customer) has shown the following: no significant impacts against the sides of the loads, only against the ends; seldom any more than one rotational drop of the load on a base edge; small amount of lift truck handling by the manufacturer but a moderate amount by the customer; and no warehousing/stacking of loads in storage by either manufacturer or customer. (1) The user of DC-2 develops a test plan that includes a modified Schedule A Mechanical Handling at the beginning and at the end of the distribution cycle but does not include a compression test, as follows: Sequence
D6179 Method C
15
D4169 − 16 Sequence
Schedule
Test Method
Details of Test and Levels
1
modified A-handling by shipper and carrier
D5276
Drop test from 21 in. high in six orientations as described in table of 10.2.3 First Sequence of Distribution Cycles
2
C-stacking in truck
D642
Compression test to 642 lb (M=10.0 lb/ft3, H=108 in., F=7.0
3
F-loose load vibration
D999 A2
40 min on bottom
4
E-truck vibration
D4728
180 min on bottom, 0.52 g rms
5
modified A-handling by carrier and receiver
D5276
Drop test from 21 in high in five orientations as described in table of 10.2.3 Second Sequence of Distribution Cycles. Drop once from 42 in. high on the most damage-prone corner.
(1) Comparing to X1.3 Example B where DC-3 was used, this test plan’s Assurance Levels vary between test schedules in the sequence, drop test heights are higher than any listed in the table of 10.2.3 for the shipping weight involved, compression strength is checked for full trailer height of 108 in. (rather than 54 in. height), and vibration tests are conducted in only one orientation rather than three.
REFERENCES (14) Singh, S. P., Saha, K., Singh, J. and Sandhu, A. P. S., “Measurement and Analysis of Vibration and Temperature Levels in Global Intermodal Container Shipments on Truck, Rail and Ship,” Journal of Packaging Technology & Science, Accepted for publication. (15) Singh, S. P., Joneson, E., Singh, J., Grewal, G., “Dynamic Analysis of Less-Than-Truckload Shipments and Test Method to Simulate This Environment,” Journal of Packaging Technology and Science Special Issue: Environmental Data Recording, Analysis and Simulation of Transport Vibrations, Vol. 21, Issue 8, pp. 453 – 466, December 2008. (16) Singh, S. P., Singh, J., Gaur, P., Saha, K., “Measurement and Analysis of Vibration Levels on Warehouse and Retail Store Material Handling Equipment,” Journal of Applied Packaging Research, Vol. 2, No. 2, December 2007. (17) Singh, J., Singh, P., Joneson, E., “Measurement and Analysis of U.S. Truck Vibration for Leaf Spring and Air Ride Suspensions and Development of Tests to Simulate these Conditions,” Journal of Packaging Technology and Science, Vol. 19, Issue 6, pp. 309 – 323, November/December 2006. (18) Frank, B., M. Gilgenbach, and M. Maltenfort, “Compression Testing to Simulate real-World Stresses,” Packaging Technology and Science, 23: 275-282, June, 2010. (19) Singh, J., Singh, S. P. and Saha, K., “Effect of Horizontal Offset on Vertical Compression Strength of Stacked Corrugated Fiberboard Boxes,” Journal of Applied Packaging Research, Vol. 5, No. 3, pp. 131-144, July 2011. (20) Ievans, U., “The Effect of Warehouse Mishandling and Stacking Patterns on the Compression Strength of Corrugated Boxes,” TAPPI Journal, August, 1975. (21) Singh, S. P., Singh, J. and Saha, K., “Effect of Palletized Box Offset on Compression Strength of Unitized and Stacked Empty Corrugated Fiberboard Boxes,” Journal of Applied Packaging Research, Vol. 5, No. 3, pp. 157-168, July 2011.
(1) Ostrem, F. E., and Libovicz, B. A., “A Survey of Environmental Conditions Incident to the Transportation of Materials,” General American Research Division, October 1971, pp. 204–442. (2) Henzi, A. N., “A Survey of Test Methods Currently Used for Simulating the Transportation Environment,” General American Research Division, April 1971, pp.202–728, Prepared for Department of Transportation, Office of Hazardous Materials. (3) Ostrem, F. E., and Rumerman, M. L., “Shock and Vibration Transportation Design Criteria Manual,” General American Research Division, September 1965. N 66 34681. Prepared for National Aeronautics and Space Administration. (4) International Safe Transit Association, “Preshipment Test Procedures,” Procedure 1 and 1A, April 1996. (5) EIA Standard RS–414–A, “Simulated Shipping Tests for Consumer Electronic Products and Electronic Components.” Electronic Industries Assoc., February 1975. (6) Preshipment Test Standard for Packaged Major Appliances, ANSI/ AHAM MA–1–PS–1980. (7) Federal Test Method Standard No. 101C. Preservation, Packaging, and Packaging Materials: Test Procedures, March 1980. (8) “The Railroad Environment, A Guide for Shipper and Railroad Personnel,” New York Central Railroad Co., 1966. (9) Packaging for Parcel Post, U.S. Postal Service, November 1974. (10) Ostrem, F. E., and Godshall, W. D., “An Assessment of the Common Carrier Shipping Environment,” General Technical Report FPL 22, U.S. Forest Product Laboratory, 1979 . (11) “Transportability Criteria, Shock and Vibration,” Department of Army Technical Bulletin TB 55–100 Hq., Department of Army, April 1964. (12) Environmental Test Methods, Military Standard 810C, Department of Defense, March 1975. (13) National Motor Freight Classification Item 180, Performance Testing of Shipping Containers, American Trucking Association, Inc., 2011.
16
D4169 − 16 SUMMARY OF CHANGES Committee D10 has identified the location of selected changes to this standard since the last issue (D4169–14) that may impact the use of this standard. (Approved April 1, 2016.) (3) Added Table 2, Table 3, and Table 4. (4) Added Note 4.
(1) Revised 12.1, 12.3, 12.4, and 12.4.1. (2) Added 12.4.1.1, 12.4.1.2, 12.4.1.3, 12.4.1.4, 12.4.2, 12.4.2.1, 12.4.2.1(1), 12.4.2.1(2), 12.4.2.1(3), and 12.4.2.2.
ASTM International takes no position respecting the validity of any patent rights asserted in connection with any item mentioned in this standard. Users of this standard are expressly advised that determination of the validity of any such patent rights, and the risk of infringement of such rights, are entirely their own responsibility. This standard is subject to revision at any time by the responsible technical committee and must be reviewed every five years and if not revised, either reapproved or withdrawn. Your comments are invited either for revision of this standard or for additional standards and should be addressed to ASTM International Headquarters. Your comments will receive careful consideration at a meeting of the responsible technical committee, which you may attend. If you feel that your comments have not received a fair hearing you should make your views known to the ASTM Committee on Standards, at the address shown below. This standard is copyrighted by ASTM International, 100 Barr Harbor Drive, PO Box C700, West Conshohocken, PA 19428-2959, United States. Individual reprints (single or multiple copies) of this standard may be obtained by contacting ASTM at the above address or at 610-832-9585 (phone), 610-832-9555 (fax), or [email protected] (e-mail); or through the ASTM website (www.astm.org). Permission rights to photocopy the standard may also be secured from the Copyright Clearance Center, 222 Rosewood Drive, Danvers, MA 01923, Tel: (978) 646-2600; http://www.copyright.com/
17
Consumer Goods
67% 67% found this document useful, Mark this document as useful
33% 33% found this document not useful, Mark this document as not useful
pdf Download ASTM D4169: Standard Practice for Performance Testing of Shipping Containers and Systems
This practice provides a uniform basis of evaluating, in a laboratory, the ability of shipping units to withstand the distribution environment. This is accomplished by subjecting them to a test plan consisting of a sequence of anticipated hazard elements encountered in various distribution cycles. This practice is not intended to supplant material specifications or existing preshipment test procedures.
Consider the use of Practice D7386 for testing of packages for single parcel shipments.
The suitability of this practice for use with hazardous materials has not been determined.
The values stated in inch-pound units are to be regarded as standard. The values given in parentheses are mathematical conversions to SI units that are provided for information only and are not considered standard.
This standard does not purport to address all of the safety concerns, if any, associated with its use. It is the responsibility of the user of this standard to establish appropriate safety and health practices and determine the applicability of regulatory limitations prior to use.
*A Summary of Changes section appears at the end of this standard
Standard Practice for Performance Testing of Shipping Containers and Systems
ASTM License Agreement
IMPORTANT- READ THESE TERMS CAREFULLY BEFORE ENTERING THIS ASTM PRODUCT.
By purchasing a subscription and clicking through this agreement, you are entering into a contract, and acknowledge that you have read this License Agreement, that you understand it and agree to be bound by its terms. If you do not agree to the terms of this License Agreement, promptly exit this page without entering the ASTM Product.
1. Ownership:
This Product is copyrighted, both as a compilation and as individual standards, articles and/or documents (“Documents”) by ASTM (“ASTM”), 100 Barr Harbor Drive, West Conshohocken, PA 19428-2959 USA, except as may be explicitly noted in the text of the individual Documents. All rights reserved. You (Licensee) have no ownership or other rights in the ASTM Product or in the Documents. This is not a sale; all right, title and interest in the ASTM Product or Documents (in both electronic file and hard copy) belong to ASTM. You may not remove or obscure the copyright notice or other notice contained in the ASTM Product or Documents.
2. Definitions.
A. Types of Licensees:
(i) Individual User:
a single unique computer, with an individual IP address;
(ii) Single-Site:
one geographic location or to multiple sites within one city that are part of a single organization unit administered centrally; for example, different campuses of the same university within the same city administered centrally.
(iii) Multi-Site:
an organization or company with independently administered multiple locations within one city; or an organization or company located in more than one city, state or country, with central administration for all locations.
B. Authorized Users:
any individual who has subscribed to this Product; if a Site License, also includes registered students, faculty or staff member, or employee of the Licensee, at the Single or Multiple Site.
3. Limited License.
ASTM grants Licensee a limited, revocable, nonexclusive, non-transferable license to access, by means of one or more authorized IP addresses, and according to the terms of this Agreement, to make the uses permitted and described below, each ASTM Product to which Licensee has subscribed.
A. Specific Licenses:
(i) Individual User:
(a) the right to browse, search, retrieve, display and view the Product;
(b) the right to download, store or print single copies of individual Documents, or portions of such Documents, solely for Licensee’s own use. That is, Licensee may access and download an electronic file of a Document (or portion of a Document) for temporary storage on one computer for purposes of viewing, and/or printing one copy of a Document for individual use. Neither the electronic file nor the single hard copy print may be reproduced in anyway. In addition, the electronic file may not be distributed elsewhere over computer networks or otherwise. That is, the electronic file cannot be emailed, downloaded to disk, copied to another hard drive or otherwise shared. The single hard copy print may only be distributed to others for their internal use within your organization; it may not be copied. The individual Document downloaded may not otherwise be sold or resold, rented, leased, lent or sub-licensed.
(ii) Single-Site and Multi-Site Licenses:
(a) the right to browse, search, retrieve, display and view the Product;
(b) the right to download, store or print single copies of individual Documents, or portions of such Documents for the Authorized User’s personal use, and to share such copies with other Authorized Users of Licensee within Licensee’s computer network;
(c) if an educational institution, Licensee is permitted to provide a hard copy of individual Documents to individual students (Authorized Users) in a class at Licensee’s location;
(d) the right to display, download and distribute hard copies of Documents for training Authorized Users or groups of Authorized Users.
(e) Licensee will undertake all necessary authentication and verification processes to ensure only Authorized Users can access the ASTM Product.
(f) Licensee will provide ASTM with a list of authorized IP (numeric IP domain addresses) addresses and, if Multi-Site, a list of authorized sites.
B. Prohibited Uses.
(i) This License describes all permitted uses. Any other use is prohibited, is a violation of this Agreement and can result in immediate termination of this License.
(ii) An Authorized User may not make this Product, or Documents, available to anyone other than another Authorized User, whether by Internet link, or by permitting access through his or her terminal or computer; or by other similar or dissimilar means or arrangements.
(iii) Specifically, no one is authorized to transmit, copy, or distribute any Document in any manner or for any purpose except as described in Section 3 of this License, without ASTM’s prior express written permission. In particular, except as described in Section 3, no one may, without the prior express written permission of ASTM: (a) distribute or forward a copy (electronic or otherwise) of any article, file, or material obtained from any ASTM Product or Document; (b) reproduce or photocopy any standard, article, file, or material from any ASTM Product; (c) alter, modify, adapt, or translate any standard, article, file, or material obtained from any ASTM Product; (d) include any standard, article, file, or material obtained from any ASTM Product or Document in other works or otherwise create any derivative work based on any materials obtained from any ASTM Product or Document; (e) impose any charge for a copy (electronic or otherwise) of any standard,article, file, or material obtained from any ASTM Product or Document, except for normal printing/copying costs where such reproduction is authorized under Section 3; or (f) systematically download, archive, or centrally store substantial portions of standards, articles, files, or material obtained from any ASTM Product or Document. Inclusion of print or electronic copies in coursepacks or electronic reserves, or for distance learning use, is not authorized by this License and is prohibited without ASTM’s prior written permission.
(iv) Licensee may not utilize the Product, or access to the Product, for commercial purposes, including but not limited to the sale of Documents, materials, fee-for-service use of the Product or bulk reproduction or distribution of Documents in any form; nor may Licensee impose special charges on Authorized Users for use of the Product beyond reasonable printing or administrative costs.
C. Copyright Notice. All copies of material from an ASTM Product must bear proper copyright notice in ASTM’s name, as shown in the initial page of each standard, article, file or material. Obscuring, deletion or modification of the copyright notice is not permitted.
4. Detection of Prohibited Uses.
A. Licensee is responsible for taking reasonable measures to prevent prohibited uses, and promptly notify ASTM of any infringements of copyright or prohibited use of which Licensee becomes aware. Licensee will cooperate with ASTM in investigating any such prohibited uses and will take reasonable steps to ensure the cessation of such activity and to prevent any reoccurrence.
B. Licensee shall use all reasonable efforts to protect the Product from any use that is not permitted under this Agreement, and shall notify ASTM of any use of which it learns or is notified.
5. Continued Access to Product.
ASTM reserves the right to terminate this License, upon written notice, if Licensee materially breaches the terms of this Agreement. If Licensee fails to pay ASTM any license or subscription fees when due, ASTM will provide the Licensee with a 30-day period within which to cure such breach. No cure period will be provided for material breaches relating to violations of Section 3 or any other breach likely to cause ASTM irreparable harm. If Licensee’s subscription to an ASTM Product terminates, further access to the online database will be denied. If Licensee or Authorized Users materially breach this License or make prohibited uses of material in any ASTM Product, ASTM reserves the right to deny Licensee any access to the ASTM Product, in ASTM’s sole discretion.
6. Delivery Formats and Service.
A. Some ASTM Products use standard Internet HTML format. ASTM reserves the right to change such format upon three [3] months’ notice to Licensee, although ASTM will make reasonable efforts to use commonly available formats. The Licensee and the Authorized Users are responsible for obtaining at their expense suitable Internet connections, Web browsers, and licenses for any software necessary to view the ASTM Products.
B. The ASTM Products are also available in Adobe Acrobat (PDF) format to Licensee and its Authorized Users, who are solely responsible for installing and configuring the appropriate Adobe Acrobat Reader software.
C. ASTM shall use reasonable efforts to make online access available on a continuous basis. Availability will be subject to periodic interruption and downtime for server maintenance, software installation or testing, loading new files, and reasons beyond the control of ASTM. ASTM does not guarantee access, and will not be liable for damages or refunds if the Product becomes unavailable temporarily, or if access becomes slow or incomplete due to system back-up procedures, Internet traffic volume, upgrades, overload of requests to servers, general network failures or delays, or any other cause that may from time to time make the Product unavailable for the Licensee or Licensee’s Authorized Users.
7. Terms and Fees.
A. The term of this Agreement is _____________ (“Subscription Period”). Access to the Product is for the Subscription Period only. This Agreement will remain in effect thereafter for successive Subscription Periods so long as annual subscription fees, as such may change from time to time, are paid. Licensee and/or ASTM have the right to terminate this Agreement at the end of a Subscription Period by written notice given at least 30 days in advance.
B. Fees:
8. Verification.
ASTM has the right to verify compliance with this Agreement, at its expense, and at any time during the course of normal business hours. To do so, ASTM will engage an independent consultant, subject to a confidentiality agreement, to review Licensee’s use of ASTM Product and/or Documents. Licensee agrees to permit access to its information and computer systems for this purpose. Verification will take place upon no less than 15 days notice, during normal business hours and in a manner that does not interfere unreasonably with Licensee’s operations. If verification reveals unlicensed or prohibited use of the ASTM Products or Documents, Licensee agrees to reimburse ASTM for the costs incurred in verification and reimburse ASTM for any unlicensed/prohibited uses. By invoking this procedure, ASTM does not waive any of its rights to enforce this Agreement or to protect its intellectual property by any other means permitted by law. Licensee acknowledges and agrees that ASTM may imbed certain identifying or tracking information in the ASTM Products available on the Portal.
9. Passwords:
Licensee must immediately notify ASTM of any known or suspected unauthorized use(s) of its password(s), or any known or suspected breach of security, including the loss, theft unauthorized disclosure of such password or any unauthorized access to or use of the ASTM Product. Licensee is solely responsible for maintaining the confidentiality of its password(s) and for ensuring the authorized access and use of the ASTM Product. Personal accounts/passwords may not be shared.
10. Disclaimer of Warranty:
Unless specified in this Agreement, all express or implied conditions, representations and warranties, including any implied warranty of merchantability, fitness for a particular purpose or non-infringement are disclaimed, except to the extent that these disclaimers are held to be legally invalid.
11. Limitation of Liability:
To the extent not prohibited by law, in no event will ASTM be liable for any loss, damage, lost data or for special, indirect, consequential or punitive damages, however caused regardless of the theory of liability, arising out of or related to the use of the ASTM Product or downloading of the ASTM Documents. In no event will ASTM’s liability exceed the amount paid by Licensee under this License Agreement.
12. General.
A. Termination:
This Agreement is effective until terminated. Licensee may terminate this Agreement at any time by destroying all copies (hard, digital or in any media)of the ASTM Documents and terminating all access to the ASTM Product.
B. Governing Law, Venue, and Jurisdiction:
This Agreement shall be interpreted and construed in accordance with the laws of the Commonwealth of Pennsylvania. Licensee agrees to submit to jurisdiction and venue in the state and federal courts of Pennsylvania for any dispute which may arise under this Agreement. Licensee also agrees to waive any claim of immunity it may possess.
C. Integration:
This Agreement is the entire agreement between Licensee and ASTM relating to its subject matter. It supersedes all prior or contemporaneous oral or written communications, proposals, representations and warranties and prevails over any conflicting or additional terms of any quote, order, acknowledgment, or other communication between the parties relating to its subject matter during the term of this Agreement. No modification of this Agreement will be binding, unless in writing and signed by an authorized representative of each party.
D. Assignment:
Licensee may not assign or transfer its rights under this Agreement without the prior written permission of ASTM.
E. Taxes.
Licensee must pay any applicable taxes, other than taxes on ASTM’s net income, arising out of Licensee’s use of the ASTM Product and/or rights granted under this Agreement.
ASTM D4169-16 PDF Download
Purchase Standard
Right after completing the purchase process, you can immediately download a digital copy of this standard which is:
Right after completing the purchase process, you can immediately download a digital copy of this standard which is:
Now you can download a digital copy of this standard which is:
Not Locked
Printable PDF
Multi-User
$ 13. 50
Add to Basket
View Basket
ASTM D 4169 – 04 pdf free download
ASTM E 2057 – 00 pdf free download Standard Specifications for Preparation of Laboratory Analysis Requests in Sexual Assault Investigations1 This standard is issued under the fixed designation E 2057; the number immediately following the designation indicates the year of original adoption or, in the case of revision, the year of last revision. A number in parentheses indicates the year of last reapproval. A superscript epsilon (e) indicates an editorial change since the last revision or reapproval. Click below to download ASTM E 2057 – 00 pdf free Download Now! ASTM E 2056 – 00 pdf free download
ASTM D 4239 – 04 pdf free download Standard Test Methods for Sulfur in the Analysis Sample of Coal and Coke Using HighTemperature Tube Furnace Combustion Methods1 This standard is issued under the fixed designation D 4239; the number immediately following the designation indicates the year of original adoption or, in the case of revision, the year of last revision. A number in parentheses indicates the year of last reapproval. A superscript epsilon (e) indicates an editorial change since the last revision or reapproval. Click below to download ASTM D 4239 – 04 pdf free Download Now! ASTM D 4236 – 94 pdf free download
ASTM D 4236 – 94 pdf free download Standard Practice for Labeling Art Materials for Chronic Health Hazards1 This standard is issued under the fixed designation D 4236; the number immediately following the designation indicates the year of original adoption or, in the case of revision, the year of last revision. A number in parentheses indicates the year of last reapproval. A superscript epsilon (e) indicates an editorial change since the last revision or reapproval. Click below to download ASTM D 4236 – 94 pdf free Download Now! ASTM D 4235 – 01 pdf free download
ASTM D 4235 – 01 pdf free download Standard Performance Specification for Women’s and Girls’ Knitted Blouse and Dress Fabrics1 This standard is issued under the fixed designation D 4235; the number immediately following the designation indicates the year of original adoption or, in the case of revision, the year of last revision. A number in parentheses indicates the year of last reapproval. A superscript epsilon (e) indicates an editorial change since the last revision or reapproval. Click below to download ASTM D 4235 – 01 pdf free Download Now! ASTM D 4234 – 01 pdf free download
ASTM D 4234 – 01 pdf free download Standard Performance Specification for Women’s and Girls’ Knitted Robe, Negligee, Nightgown, Pajama, Slip, and Lingerie Fabrics1 This standard is issued under the fixed designation D 4234; the number immediately following the designation indicates the year of original adoption or, in the case of revision, the year of last revision. A number in parentheses indicates the year of last reapproval. A superscript epsilon (e) indicates an editorial change since the last revision or reapproval. Click below to download ASTM D 4234 – 01 pdf free Download Now! ASTM D 4233 – 01 pdf free download
ASTM D 4233 – 01 pdf free download Standard Performance Specification for Women’s and Girls’ Knitted and Woven Brassiere Fabrics1 This standard is issued under the fixed designation D 4233; the number immediately following the designation indicates the year of original adoption or, in the case of revision, the year of last revision. A number in parentheses indicates the year of last reapproval. A superscript epsilon (e) indicates an editorial change since the last revision or reapproval. Click below to download ASTM D 4233 – 01 pdf free Download Now! ASTM D 4232 – 01 pdf free download
ASTM D 4232 – 01 pdf free download Standard Performance Specification for Men’s and Women’s Dress and Vocational Career Apparel Fabrics1 This standard is issued under the fixed designation D 4232; the number immediately following the designation indicates the year of original adoption or, in the case of revision, the year of last revision. A number in parentheses indicates the year of last reapproval. A superscript epsilon (e) indicates an editorial change since the last revision or reapproval. Click below to download ASTM D 4232 – 01 pdf free Download Now! ASTM D 4231 – 01 pdf free download
ASTM D 4231 – 01 pdf free download Standard Practice for Evaluation of Launderable Woven Dress Shirts and Sports Shirts1 This standard is issued under the fixed designation D 4231; the number immediately following the designation indicates the year of original adoption or, in the case of revision, the year of last revision. A number in parentheses indicates the year of last reapproval. A superscript epsilon (e) indicates an editorial change since the last revision or reapproval. Click below to download ASTM D 4231 – 01 pdf free Download Now! ASTM D 4230 – 02e1 pdf free download
ASTM D 4230 – 02e1 pdf free download Standard Test Method of Measuring Humidity with Cooled-Surface Condensation (Dew-Point) Hygrometer1 This standard is issued under the fixed designation D 4230; the number immediately following the designation indicates the year of original adoption or, in the case of revision, the year of last revision. A number in parentheses indicates the year of last reapproval. A superscript epsilon (e) indicates an editorial change since the last revision or reapproval. Click below to download ASTM D 4230 – 02e1 pdf free Download Now! ASTM D 4228 – 99 pdf free download
Astm D4169-16 Pdf
Astm D4169-16 Pdf
Performance Testing Of Shipping Containers And Systems1 This Standard Is Issued Under The Fixed Designation D4169; The Number Immediately Following The …
키워드에 대한 정보 astm d4169 pdf
다음은 Bing에서 astm d4169 pdf 주제에 대한 검색 결과입니다. 필요한 경우 더 읽을 수 있습니다.
이 기사는 인터넷의 다양한 출처에서 편집되었습니다. 이 기사가 유용했기를 바랍니다. 이 기사가 유용하다고 생각되면 공유하십시오. 매우 감사합니다!
사람들이 주제에 대해 자주 검색하는 키워드 ASTM D4169 Transit Testing | Packaging Compliance Labs
- 동영상
- 공유
- 카메라폰
- 동영상폰
- 무료
- 올리기
ASTM #D4169 #Transit #Testing #| #Packaging #Compliance #Labs
YouTube에서 astm d4169 pdf 주제의 다른 동영상 보기
주제에 대한 기사를 시청해 주셔서 감사합니다 ASTM D4169 Transit Testing | Packaging Compliance Labs | astm d4169 pdf, 이 기사가 유용하다고 생각되면 공유하십시오, 매우 감사합니다.