당신은 주제를 찾고 있습니까 “bs 6364 cryogenic testing – Cryogenic Valve Test – Peach Valve Co., Ltd.“? 다음 카테고리의 웹사이트 https://chewathai27.com/you 에서 귀하의 모든 질문에 답변해 드립니다: https://chewathai27.com/you/blog. 바로 아래에서 답을 찾을 수 있습니다. 작성자 Hana Oh 이(가) 작성한 기사에는 조회수 9,068회 및 좋아요 33개 개의 좋아요가 있습니다.
bs 6364 cryogenic testing 주제에 대한 동영상 보기
여기에서 이 주제에 대한 비디오를 시청하십시오. 주의 깊게 살펴보고 읽고 있는 내용에 대한 피드백을 제공하세요!
d여기에서 Cryogenic Valve Test – Peach Valve Co., Ltd. – bs 6364 cryogenic testing 주제에 대한 세부정보를 참조하세요
Since 1975, Peach Valve has been renowned as high quality Dual Plate Check Valve (API 594) manufacturer whose specialists and stas are dedicated to considering particular circumstance of each customer in the world. From the design to shipping Peach Valve cryogenic valves are tailored to meet the clients’ needs in any severe environments. Especially for LNG industries, Peach Valve makes a contributes with their cryogenic valves as a vendor of many signicant Oil and Gas companies.
bs 6364 cryogenic testing 주제에 대한 자세한 내용은 여기를 참조하세요.
Valves for cryogenic service – Flowtherm
Testing. 8. Pressure testing. 4. 9. Marking. 4. Appendix A Cryogenic test … 2) Marking BS 6364:1984 on or in relation to a product is a claim by the …
Source: www.flowtherm.com.au
Date Published: 4/29/2022
View: 2457
BS 6364: Specifications for Valves for cryogenic service
BS 6364 Standard specifies the requirements for the design, manufacture and testing of valves for cryogenic service. It is a requirement of this standard …
Source: www.reliavalve.com
Date Published: 3/10/2021
View: 2466
Cryogenic Ball Valve, Extended Bonnet with BS 6364 Test
The cryogenic ball valve is used for low-temperature working conditions, especially for some hazardous media, such as liquized natural gas.
Source: www.raysvalve.com
Date Published: 2/10/2022
View: 495
BS 6364 Cryogenic certified Ball, Globe and Gate Valves for …
Anson’s AF-36C & AF-51C Cryogenic Ball Valve passes BS 6364 Cryogenic Testing This testing requires immersion in liqu nitrogen @-321F for …
Source: www.valveworldexpo.com
Date Published: 10/15/2022
View: 6758
BS 6364 : Valves for Cryogenic Service
Specifies requirements supplementary to those in the applicable valve product standards when the valves are used for cryogenic service. Applies to the size …
Source: global.ihs.com
Date Published: 9/25/2021
View: 626
Comparison of Contemporary Cryogenic Valve Standards
in cryogenic service include LNG (Liquefied Natural Gas) processing, … BS 6364: 1984: Valves for Cryogenic … ISO 28921-2: 2015: Part 2 -Type testing.
Source: www.lntvalves.com
Date Published: 10/25/2022
View: 5780
BS 6364: Specification for Valves for cryogenic service
BS6364 Standard specifies the requirements for the design, manufacture and testing of valves for cryogenic service. It is a requirement of this standard …
Source: www.reliavalves.com
Date Published: 7/15/2022
View: 257
주제와 관련된 이미지 bs 6364 cryogenic testing
주제와 관련된 더 많은 사진을 참조하십시오 Cryogenic Valve Test – Peach Valve Co., Ltd.. 댓글에서 더 많은 관련 이미지를 보거나 필요한 경우 더 많은 관련 기사를 볼 수 있습니다.
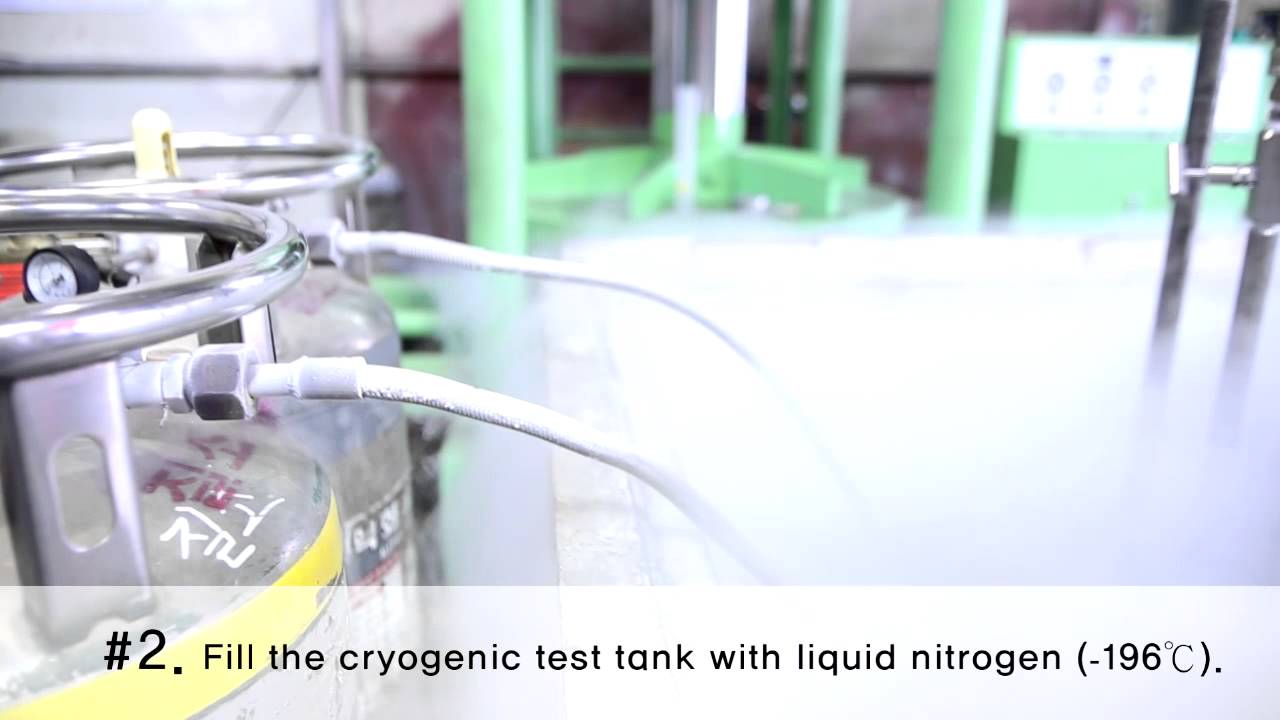
주제에 대한 기사 평가 bs 6364 cryogenic testing
- Author: Hana Oh
- Views: 조회수 9,068회
- Likes: 좋아요 33개
- Date Published: 2014. 6. 19.
- Video Url link: https://www.youtube.com/watch?v=qbDQ9SuwhLk
What is cryogenic testing?
During cryogenic testing components are enclosed in an insulated tank and immersed in liquid nitrogen with 100% Helium as the search gas in order to simulate operating conditions. Our state-of-the-art computer systems monitor for seat leakage, temperature and pressurisation.
What is cryogenic testing of valves?
The cryogenic testing is a special testing monitoring any leakage of the valves (for both floating and trunnion mounted ball valves) at any temperature down to -196 ° C (boiling point of liquid nitrogen). The cryogenic valve is tested according to the operating pressure specified for its class.
What is bs6364?
BS 6364 Standard specifies the requirements for the design, manufacture and testing of valves for cryogenic service. It is a requirement of this standard that the valves comply with the appropriate valve product British Standards, i.e.: steel wedge gate valves: BS 1414; Steel check valves: BS 1868.
What do you mean by cryogenic?
Definition of cryogenic
1a : of or relating to the production of very low temperatures. b : being or relating to very low temperatures. 2a : requiring or involving the use of a cryogenic temperature. b : requiring cryogenic storage.
Are cryogenics cold?
cryogenics, production and application of low-temperature phenomena. The cryogenic temperature range has been defined as from −150 °C (−238 °F) to absolute zero (−273 °C or −460 °F), the temperature at which molecular motion comes as close as theoretically possible to ceasing completely.
BS 6364: Specifications for Valves for cryogenic service
BS 6364: Specifications for Valves for cryogenic service
BS 6364: Specifications for Valves for cryogenic service
BS 6364 Standard specifies the requirements for the design, manufacture and testing of valves for cryogenic service. It is a requirement of this standard that the valves comply with the appropriate valve product British Standards, i.e.:
steel wedge gate valves: BS 1414;
Steel check valves: BS 1868
steel globe and globe stop and check valves: BS 1873;
steel ball valves: BS 5351;
steel wedge gate, globe valve and check valves DN 50 and smaller: BS 5352;
copper alloy globe, globe stop and check, check and gate valves: BS 5154;
testing of valves: BS 6755;
butterfly valves for general purposes: BS 5155.
The size range covered by this standard is DN 15 to a maximum nominal size appropriate to the above product standards, in the temperature range – 50 °C to – 196 °C, yet capable of operation at ambient conditions to allow for start-up and run-down.
NOTE 1 For marine applications where design temperatures are below – 165 °C attention is drawn to the need to check requirements with the relevant Statutory Authority.
Appendix C lists the information to be supplied by the purchaser.
NOTE 2 The titles of the publications referred to in this standard are listed on the inside back cover.
Requirements
4.1 Valves shall be supplied with extended bonnets/glands (see Figure 1). The length of the extension shall be sufficient to maintain the stem packing at a temperature high enough to permit operation within the normal temperature range of the packing material.
4.2 Valves on gas service shall be capable of operation with the valve stem at or above the horizontal position.
4.3 Valves in liquid service other than cold box applications shall be capable of operation with the
valve stem at or above 45° above the horizontal position.
4.4 For cold box applications, valves shall be suitable for use with the valve stem at or above 15° above the horizontal position and in addition the minimum gland extension length as shown in Figure 1 shall be as given in Table 1.
NOTE If any special length of gland extension is required by the purchaser he should state this (see Appendix C).
4.5 For applications other than cold box applications the minimum gland extension length shall be 250 mm (see Figure 1).
4.6 Valves shall be designed to relieve pressures above normal working pressure that may build up in trapped cavities due to thermal expansion or evaporation of liquid.
NOTE For ball valve and gate valves this requirement can be met by the provision of a pressure relief hole or passage or other means, e.g. pressure relieving seats, to relieve pressure in the bonnet and body cavities to the upstream side of the valve. The means adopted will be determined by the manufacturer unless the purchaser exercises his option in accordance with Appendix C.
4.7 Where valves, by design, are unidirectional in operation, the flow direction shall be clearly indicated either on and integral with the body of the valve or on a plate securely attached to the body of the valve.
In the design of such valves, measures shall be taken to prevent incorrect assembly.
4.8 Valve bonnets shall be bolted, welded or union type. Union type bonnets shall only be used on valves DN 50 and below, or for marine applications DN 40 and below, and the union nut shall be locked to the body. The use of screwed bonnets shall not be permitted.
NOTE Gasket materials for bolted bonnets are outside the scope of this standard (see Appendix C).
4.9 For steel valves, fabricated gland extensions shall be constructed from a single length of seamless tube butt-welded to the bonnet and gland housing.
4.10 For high pressure bronze or copper alloy valves of PN 100 rating or greater, the extension tube shall be screwed into the bonnet prior to silver soldering.
4.11 The clearance between the valve stem and gland extension bore shall be designed to minimize convection heat losses. The wall thickness of the extension shall be minimized, compatible with the rating of the valve and mechanical strength requirements in order to reduce conduction heat losses.
4.12 Valve stems shall be of one-piece construction except for end entry ball valves, in which case the valve design shall be such that the valve stem cannot be blown out of the body in the event of the gland being removed while the valve is under pressure. Rising stem valves with renewable gland packing that incorporate a back seat shall have the back seat located in the region of the gland. Gland designs incorporating lantern rings and screwed plugs in the gland body shall not be used.
4.13 Globe valves shall have tapered or conical discs. The use of flat seated discs shall not be permitted.
4.14 The maximum force required to operate the valves manually under service conditions, when applied at the rim of the handwheel or lever, shall not exceed 350 N, except for valve seating and unseating only, when it shall be permissible for this value to be increased to 500 N. Where reduction gearing is provided, it shall be suitable for operation at ambient temperature.
4.15 Valves for flammable service shall be designed to ensure electrical continuity to prevent build-up of static electricity.
Cryogenic Testing – Vaseco
With critical components expected to function in environments as diverse as the North Sea or Arabian Gulf, more regular testing is now required to ensure they perform in these extreme conditions.
During cryogenic testing components are enclosed in an insulated tank and immersed in liquid nitrogen with 100% Helium as the search gas in order to simulate operating conditions. Our state-of-the-art computer systems monitor for seat leakage, temperature and pressurisation.
The emission testing is carried out by a Helium Mass Spectrometer which can detect <5ppm of the trace gas, with all emissions data recorded. Due to the potentially hazardous nature of cryogenic testing operations, safety is of paramount importance at all times and our specialist testing area is equipped with a dedicated control room and the latest in safety protection. Cryogenic Testing Capabilities: Full cryogenic testing down to -196⁰C (-320.8⁰F) Pressure ratings from ANSI Class 150 to API 20,000 Valves ranging in size from ½” to 36” Typical Components for Cryogenic Testing: Valves (including ball, gate, globe, check, choke, butterfly, relief), Actuators and Sensors.
BS 6364: Specifications for Valves for cryogenic service
BS 6364: Specifications for Valves for cryogenic service
BS 6364: Specifications for Valves for cryogenic service
BS 6364 Standard specifies the requirements for the design, manufacture and testing of valves for cryogenic service. It is a requirement of this standard that the valves comply with the appropriate valve product British Standards, i.e.:
steel wedge gate valves: BS 1414;
Steel check valves: BS 1868
steel globe and globe stop and check valves: BS 1873;
steel ball valves: BS 5351;
steel wedge gate, globe valve and check valves DN 50 and smaller: BS 5352;
copper alloy globe, globe stop and check, check and gate valves: BS 5154;
testing of valves: BS 6755;
butterfly valves for general purposes: BS 5155.
The size range covered by this standard is DN 15 to a maximum nominal size appropriate to the above product standards, in the temperature range – 50 °C to – 196 °C, yet capable of operation at ambient conditions to allow for start-up and run-down.
NOTE 1 For marine applications where design temperatures are below – 165 °C attention is drawn to the need to check requirements with the relevant Statutory Authority.
Appendix C lists the information to be supplied by the purchaser.
NOTE 2 The titles of the publications referred to in this standard are listed on the inside back cover.
Requirements
4.1 Valves shall be supplied with extended bonnets/glands (see Figure 1). The length of the extension shall be sufficient to maintain the stem packing at a temperature high enough to permit operation within the normal temperature range of the packing material.
4.2 Valves on gas service shall be capable of operation with the valve stem at or above the horizontal position.
4.3 Valves in liquid service other than cold box applications shall be capable of operation with the
valve stem at or above 45° above the horizontal position.
4.4 For cold box applications, valves shall be suitable for use with the valve stem at or above 15° above the horizontal position and in addition the minimum gland extension length as shown in Figure 1 shall be as given in Table 1.
NOTE If any special length of gland extension is required by the purchaser he should state this (see Appendix C).
4.5 For applications other than cold box applications the minimum gland extension length shall be 250 mm (see Figure 1).
4.6 Valves shall be designed to relieve pressures above normal working pressure that may build up in trapped cavities due to thermal expansion or evaporation of liquid.
NOTE For ball valve and gate valves this requirement can be met by the provision of a pressure relief hole or passage or other means, e.g. pressure relieving seats, to relieve pressure in the bonnet and body cavities to the upstream side of the valve. The means adopted will be determined by the manufacturer unless the purchaser exercises his option in accordance with Appendix C.
4.7 Where valves, by design, are unidirectional in operation, the flow direction shall be clearly indicated either on and integral with the body of the valve or on a plate securely attached to the body of the valve.
In the design of such valves, measures shall be taken to prevent incorrect assembly.
4.8 Valve bonnets shall be bolted, welded or union type. Union type bonnets shall only be used on valves DN 50 and below, or for marine applications DN 40 and below, and the union nut shall be locked to the body. The use of screwed bonnets shall not be permitted.
NOTE Gasket materials for bolted bonnets are outside the scope of this standard (see Appendix C).
4.9 For steel valves, fabricated gland extensions shall be constructed from a single length of seamless tube butt-welded to the bonnet and gland housing.
4.10 For high pressure bronze or copper alloy valves of PN 100 rating or greater, the extension tube shall be screwed into the bonnet prior to silver soldering.
4.11 The clearance between the valve stem and gland extension bore shall be designed to minimize convection heat losses. The wall thickness of the extension shall be minimized, compatible with the rating of the valve and mechanical strength requirements in order to reduce conduction heat losses.
4.12 Valve stems shall be of one-piece construction except for end entry ball valves, in which case the valve design shall be such that the valve stem cannot be blown out of the body in the event of the gland being removed while the valve is under pressure. Rising stem valves with renewable gland packing that incorporate a back seat shall have the back seat located in the region of the gland. Gland designs incorporating lantern rings and screwed plugs in the gland body shall not be used.
4.13 Globe valves shall have tapered or conical discs. The use of flat seated discs shall not be permitted.
4.14 The maximum force required to operate the valves manually under service conditions, when applied at the rim of the handwheel or lever, shall not exceed 350 N, except for valve seating and unseating only, when it shall be permissible for this value to be increased to 500 N. Where reduction gearing is provided, it shall be suitable for operation at ambient temperature.
4.15 Valves for flammable service shall be designed to ensure electrical continuity to prevent build-up of static electricity.
Cryogenic Ball Valve, Extended Bonnet with BS 6364 Test
Do you want to know what the cryogenic ball valve with extended bonnet is and the tips of material choice and inspection? After reading this article, I believe that you will have a huge gain in the field of cryogenic ball valve design.
When Natural Gas has to be separated into fractions or treated to protect equipment from contaminants (acids), sweetening and acid removal at -51° to -196°C (-59,8° to -320,8°F), are the final stage to do that, starting from liquefaction to sub-cooling stages, with pure or mixed refrigerants (methane, nitrogen) as cooling elements.
RAYS FLOW CONTROL is the manufacturer of cryogenic ball valves with an extended bonnet design.
The cryogenic ball valve specific in LNG valve application.
Our production program offers special valve solutions engineered to suit cryogenic processes with specific constructions and duly selected materials.
Base on the cryogenic service, RAYS design base on API 6D and API 607 Fire Safe with extended bonnet ball valve and complete tested refer BS 6364 standard.
Product Description
Name: Cryogenic Ball Valve
Other names: API 6D Ball, API 607 Ball Valve, Trunnion Ball Valve, Motorized Ball Valve
Standard: API 6D, API 608, ASME B16.34, GOST and EN / DIN
Material: Austenitic Stainless Steel, Forged Steel, and Cast Steel
Application
The cryogenic ball valve is applicable to the different pipelines of Class 150~Class1500, PN16~PN100, JIS10K~JIS20K. By adopting different materials, it is applicable to different working temperatures and mediums. The minimum temperature for the ball valve is -196℃. The operation of the ball valve can be manually operated, gear operated, pneumatically operated, and motor operated. The end connection usually is flanged ends. However, the welded ends are also optional.
Product range
The cryogenic ball valve design has two types: Floating ball valve and trunnion mounted ball valve. For their range, face to face dimension, and flange dimension, please refer to the corresponding data of common floating ball valve and trunnion mounted ball valve. For valves with the working temperature above -50℃, a long neck design is seldom adopted. For valves with working temperature below-50℃, the neck length T shall be 250mm or shall be decided as per our own design and calculation.
The cryogenic ball valve is used for low-temperature working conditions, especially for some hazardous media, such as liquidized natural gas. Our company has been experienced in the design, manufacturing, inspection, and test of the cryogenic ball valve.
Choose for material
Common steels are brittle in the cryogenic condition. So, the key point for the design and production of the cryogenic ball is to select proper body material according to the minimum working temperature. To ensure the material suitability under the low-temperature condition, the material adopted shall be impact tested according to the standard requirement. The packing, gasket, bolt, and nut shall also adopt the materials suitable for low-temperature conditions.
Inspection and Testing
The RAYS Cryogenic Ball Valve can be base on a floating cryogenic ball valve and trunnion cryogenic ball valve, also top entry cryogenic ball valve.
All of the types are based on fire safe API 607 design, and cryogenic testing & inspection are based on BS 6364.
The cryogenic ball valve should be cleaning process without oil grease, and valve shell/body testing by high-pressure air (nitrogen) on design class.
The Cryogenic ball valve can be a motorized ball valve, electric ball valve, actuated ball valve, and also suitable for high-pressure ball valve. If you want to find a reliable cryogenic ball vale manufacturer or supplier, welcome to visit RAYS FLOW CONTROL.
BS 6364 Cryogenic certified Ball, Globe and Gate Valves for LNG
Anson’s AF-36C & AF-51C Cryogenic Ball Valve passes BS 6364 Cryogenic Testing This testing requires immersion in liquid nitrogen @-321F for one hour, then (20) cycles at full rated pressure (2000 psig) with helium as a test gas, then valve is tested for both external & across-valve leakage with helium.
http://www.ansonflow.com/products/af36c.htm
AF-36C Class 800 3-pc Cryogenic Direct Mount Ball Valve
http://www.ansonflow.com/products/af51c.htm
AF-51C Class 150 2-pc Cryogenic Flanged Direct Mount Ball Valve
http://www.ansonflow.com/products/af51c.htm
AF-53C DIN PN16 2-pc Cryogenic Flanged Direct Mount Ball Valve
Please contact Anson for details.
BS 6364: Specification for Valves for cryogenic service
1 – Scope
BS6364 Standard specifies the requirements for the design, manufacture and testing of valves for cryogenic service. It is a requirement of this standard that the valves comply with the appropriate valve product British Standards, i.e.:
steel wedge gate valves: BS 1414;
steel check valves: BS 1868;
steel globe and globe stop and check valves: BS 1873;
steel ball valves: BS 5351;
steel wedge gate, globe and check valves DN 50 and smaller: BS 5352;
copper alloy globe, globe stop and check, check and gate valves: BS 5154;
testing of valves: BS 6755;
butterfly valves for general purposes: BS 5155.
The size range covered by this standard is DN 15 to a maximum nominal size appropriate to the above product standards, in the temperature range – 50 °C to – 196 °C, yet capable ofoperation at ambient conditions to allow for start-up and run-down.
NOTE 1 – For marine applications where design temperatures are below – 165 °C attention is drawn to the need to check
requirements with the relevant Statutory Authority. Appendix C lists the information to be supplied by the purchaser.
NOTE 2 – The titles of the publications referred to in this standard are listed on the inside back cover.
3 – General requirements
Valves shall comply with the appropriate standards listed in clause 1 in addition to clauses 4 to 9 of this standard.
4 – Requirements
4.1 Valves shall be supplied with extended bonnets/glands (see Figure 1). The length of the extension shall be sufficient to maintain the stem packing at a temperature high enough to permit operation within the normal temperature range of the packing material.
4.2 Valves on gas service shall be capable of operation with the valve stem at or above the horizontal position.
4.3 Valves in liquid service other than cold box applications shall be capable of operation with the valve stem at or above 45° above the horizontal position.
4.4 For cold box applications, valves shall be suitable for use with the valve stem at or above 15° above the horizontal position and in addition the minimum gland extension length as shown in Figure 1 shall be as given in Table 1.
NOTE – If any special length of gland extension is required by the purchaser he should state this (see Appendix C).
4.5 For applications other than cold box applications the minimum gland extension length shall be 250 mm (see Figure 1).
4.6 Valves shall be designed to relieve pressures above normal workingpressure that may build up in trapped cavities due to thermal expansion or evaporation of liquid.
NOTE – For ball and gate valves this requirement can be met by the provision ofa pressure reliefhole or passage or other means, e.g. pressure relieving seats, to relieve pressure in the bonnet and body cavities to the upstream side of the valve. The means adopted will be determined by the manufacturer unless the purchaser exercises his option in accordance with Appendix C.
Valve with extended bonnet
Table 1 — Minimum gland extension length for cold box applications
Type Minimum Gland extension length ( in mm) for nominal size DN: 15 20 25 38 50 80 100 150 200 250 300 350 400 450 500 Globe 500 500 500 600 600 700 700 700 750 850 850 — — — — Gate 500 500 500 600 600 700 700 700 900 1000 1100 1200 1300 1400 1500 Ball 500 500 500 600 600 700 700 — — — — — — — — Butterfly — — — — — — 700 700 700 750 800 850 850 900 950
4.7 Where valves, by design, are unidirectional in operation, the flow direction shall be clearly indicated either on and integral with the body of the valve or on a plate securely attached to the body of the valve.
In the design of such valves, measures shall be taken to prevent incorrect assembly.
4.8 Valve bonnets shall be bolted, welded or union type. Union type bonnets shall only be used on valves DN 50 and below, or for marine applications DN 40 and below, and the union nut shall be locked to the body. The use of screwed bonnets shall not be permitted.
NOTE – Gasket materials for bolted bonnets are outside the scope of this standard (see Appendix C).
4.9 For steel valves, fabricated gland extensions shall be constructed from a single length of seamless tube butt-welded to the bonnet and gland housing.
4.10 For high pressure bronze or copper alloy valves of PN 100 rating or greater, the extension tube shall be screwed into the bonnet prior to silver soldering.
4.11 The clearance between the valve stem and gland extension bore shall be designed to minimize convection heat losses. The wall thickness of the extension shall be minimized, compatible with the rating of the valve and mechanical strength
requirements in order to reduce conduction heat losses.
4.12 Valve stems shall be of one-piece construction except for end entry ball valves, in which case the valve design shall be such that the valve stem cannot be blown out of the body in the event of the gland being removed while the valve is under
pressure. Rising stem valves with renewable gland packing that incorporate a back seat shall have the back seat located in the region of the gland.
Gland designs incorporating lantern rings and screwed plugs in the gland body shall not be used.
4.13 Globe valves shall have tapered or conical discs. The use of flat seated discs shall not be permitted.
4.14 The maximum force required to operate the valves manually under service conditions, when applied at the rim of the handwheel or lever, shall not exceed 350 N, except for valve seating and unseating only, when it shall be permissible for this
value to be increased to 500 N. Where reduction gearing is provided, it shall be suitable for operation at ambient temperature.
4.15 Valves for flammable service shall be designed to ensure electrical continuity to prevent build-up of static electricity.
5 Materials
NOTE – The specification of materials and gland packing is outside the scope of this standard owing to the variety of materials for the temperature range of operation, but Appendix B gives the preferred austenitic steels and non-ferrous materials that may be used.
5.1 Bolting materials shall be selected from those listed in BS 4882.
NOTE – Note that on first cooling below ambient temperature and down to – 196 °C, some austenitic steels increase slightly in size owing to a permanent metallurgical change. This may result, for example, in bolts relaxing their pre-load the first time they are cooled. The manufacturer/user should take account of this in selecting the steels used.
5.2 Valves shall have metal/metal or soft seats (see Appendix C). Soft seats shall be backed by a secondary metal seat. Virgin PTFE shall be supported in such a way as to prevent cold flow.
5.3 The valve trim materials selected shall be such as to avoid the effects ofgalling (seizure or binding) caused by frequent operation at cryogenic temperatures.
8 Pressure testing
8.1 Shell strength test
8.1.1 The valve body and bonnet shall be subjected to a hydrostatic or pneumatic test. Hydrostatic testing shall be carried out as described in the appropriate standard(s) given in clause 1. For stainless steel valves, the chloride content of the water for hydrostatic tests shall not exceed 30 p.p.m. Pneumatic tests shall be at the full test pressure specified in the appropriate valve product standard.
WARNING. – Attention is drawn to the hazardous nature of pneumatic testing.
8.1.2 For shell tests, discs and wedges, iffitted, shall be in the open position and ball valves shall be in the half-open position.
8.1.3 After hydrostatic shell testing, the component parts of the valve shall be thoroughly cleaned and degreased.
8.2 Shell leak test. After the hydrostatic or pneumatic strength test, body and bonnet joints and glands of valves shall be soap or immersion-under-water tested using dry oil-free air or nitrogen at the full seat rating of the valve.
The stem shall be free to turn at this pressure.
During the test duration specified in Appendix B of BS 6755-1:1986, there shall be no visible leakage.
8.3 Seat leak test
8.3.1 Valve seats shall be tested with dry oil-free air or inert gas at the full seat rating or for ball valves at 6.9 bar 1) Valve shut-off shall be achieved by the normal methods of operation and duration of tests shall be in accordance with BS 6755-1.
8.3.2 For valves having metal-to-metal seats, the maximum permitted leakage rate shall be 0.3 mm 3 /s ° DN.
8.3.3 For valves having soft seats there shall be no visible leakage for the duration of the test. 8.4 Cryogenic prototype testing. When tested as described in Appendix A, valves shall satisfy all the requirements of the test as given in that appendix.
Valves intended for marine applications shall be subjected to the tests described in Appendix A.
NOTE – For all other applications, cryogenic testing is normally carried out only when requested by the purchaser and it is
essential, therefore, for the purchaser to state he requires this testing to be done end also, whether he wishes to be present
(see Appendix C).
Appendix A – Cryogenic test
A.1 Temperature. The cryogenic test temperature shall be – 196 °C.
A.2 Prior to testing
A.2.1 Degrease the valve components, dry them and assemble the valve in a clean and dust- and grease-free environment.
A.2.2 Tighten bolts to a pre-determined torque or tension and record the value.
A.2.3 Make suitable thermocouple connections to the valve to enable valve body and bonnet temperature to be monitored throughout the test.
A.3 Testing
A.3.1 Handwheel operated valves: gate, globe, ball and butterfly valves
A.3.1.1 A suitable test apparatus is shown diagrammatically in Figure 2. Set up the valve as shown in Figure 2 in the test tank and make all connections. Take care to ensure that the valve gland is positioned clear of the cold boil-offgas in the top of the tank.
A.3.1.2 Make an initial system proving test at the maximum seat test pressure [see A.3.1.4 d)] at ambient temperature using helium gas to ensure that the valve is in a suitable condition for the test to proceed.
A.3.1.3 Cool down the valve by immersing it in liquid nitrogen to a depth such that the level of the liquid covers at least the top of the valve body/bonnet joint. Maintain a purge of helium gas throughout the cooling operation.
A.3.1.4 When the valve body and bonnet are at a temperature of – 196 °C carry out the following operations a) to e).
a) Soak the valve at the test temperature for at least 1 h until all temperatures have stabilized. Take temperature measurements by means of the thermocouples to ensure uniform temperature of the valve.
b) Repeat the initial proving test described in A.3.1.2 at the test temperature.
c) Open the valve and close it 20 times.
Measure the open and close forces for at least the first and last operation.
Figure 2 — Typical arrangement oflow temperature type test rig
NOTE 1 – Value spindle gland positioned above the tank top level.
NOTE 2 – Check valves — the test apparatus shall be capable of interchanging the gas supply system and the flow measuring system
d) Subject the valve to a seat pressure test in the normal flow direction for the valve. For valves which are capable of sealing in both directions, test each seat separately. Raise the pressure in increments, as given in the tabulated data below, up to the maximum permissible working pressure at 20 °C as specified in the appropriate product standard. (See 1 Scope for list of product standards.)
Nominal pressure Increment PN bar 20 3.5 50 7.5 64 10 100 20
Where the valve seat rating has been downrated by the manufacturer, use this value as the seat test pressure.
Measure and record leakage rate at each pressure stage.
The leakage rate measured at the flowmeter shall not exceed 100 mm 3 /s ×° DN.
e) With the valve in the open position, close the needle valve (see Figure 2) on the outlet side of the valve and pressurize the valve body to the seat test pressure. Maintain this pressure for a period of 15 min and check the valve gland and body/bonnet joint for leak tightness. There shall be no visible leakages.
A.3.2 Check valve
A.3.2.1 A suitable test apparatus is shown diagrammatically in Figure 2 and the test apparatus shall be capable of interchanging the gas supply and the measuring system. Set up the valve in the normal flow direction as shown in Figure 2 in
the test tank and make all connections.
A.3.2.2 Make an initial system proving test at ambient temperature using helium gas at the maximum seat test pressure [see A.3.1.4 d)].
Interchange the test apparatus and subject the valve to a seat pressure in the reverse flow direction [see A.3.1.4 d)] to ensure the valve is in a suitable condition for the test to proceed.
A.3.2.3 Carry out requirements described in A.3.1.3, the purge of helium gas to be in the normal direction of flow.
During cool-down monitor the temperature of the valve body and bonnet by means of suitably placed thermocouples.
A.3.2.4 When the valve body and bonnet are at a temperature of – 196 °C carry out the following operations a) to e).
a) Soak the valve at the test temperature for at least 1 h until all temperatures have stabilized.
Take temperature measurements by means of the thermocouples to ensure uniform temperature of the valve.
b) Repeat the initial proving test described in A.3.2.2 at the test temperature.
c) Subject the valve to flow in the normal flow direction to unseat the valve and then flow in the reverse flow direction to close the valve. Repeat three times.
d) Subject the valve to a seat pressure test in the reverse flow direction for the valve. Raise the pressure in increments, as given in the tabulated data below, up to the maximum permissible working pressure at 20 °C as specified in the appropriate product standard (see 1 Scope for list of products).
Where the valve seat rating has been down rated by the manufacturer, use this value as the rated seat test pressure.
Measure and record leakage rate at each pressure stage.
The leakage rate measured at the flow meter shall not exceed 200 mm 3 /s ° DN.
e) With the valve in the normal flow direction, close the needle valve (see Figure 2) on the outlet side of the valve and pressurize the valve body to the maximum seat test pressure. Maintain this pressure for a period of 15 min and check the
valve gland and body/bonnet joint for leak tightness. There shall be no visible leakage.
A.3.3 Return the valve to ambient temperature, then repeat the helium gas proving test detailed in
A.3.2.2. Measure any leakage through the valve and record it and compare the result with the reading taken under A.3.2.4.
A.3.4 After completion of the test, dismantle the valve and in a clean, dust-free environment. Check for ease of dismantling and examine all component parts for wear and damage.
A.4 Test report. The test report shall include the following information:
a) conditions of valve parts after the test (see A.3.4);
b) torque applied to valve body, bonnet and gland bolts (see A.2.2);
c) leakage rates;
d) results of proving tests at ambient temperature (see A.3.1.2 or A.3.2.2) and at test temperature (see A.3.1.4 b) or A.3.2.4 b)].
e) record of valve body temperature measurements [see A.3.1.4 a) or A.3.2.4 a);
f) record that the valve unseated and seated [see A.3.2.4 c)].
g) record any other measurements or
observations made during the course of the test.
Appendix B – Preferred materials
Table 2 and Table 3 list the preferred materials for construction of valves for cryogenic service.
Table 2 — Austenitic steels
Type of valve body ASTM Standard and grade British Standard and grade Castings a) Flanged valves only b) Flanged or weld end valves ASTM A351, CF8 ASTM A351, CF8M ASTM A351, CF3 ASTM A351, CF3M ASTM A351, CF8C BS 1504, 304C15
BS 3100, 304C15 BS 1504, 316C16
BS 3100, 316C16 BS 1504, 304C12
BS 3100, 304C12 BS 1504, 316C12
BS 3100, 316C12 BS 1504, 347C17
BS 3100, 347C17 Forgings a) Flanged valves only b) Flanged or weld end valves ASTM A182, F304 ASTM A182, F316 ASTM A182, F304L ASTM A182, F316L ASTM A182, F321 ASTM A182, F347 BS 970, 304S15
BS 1503, 304S31 BS 970, 316S16
BS 1503, 316S31 BS 970, 304S12
BS 1503, 304S11 BS 970, 316S12
BS 1503, 316S11
BS 1503, 316S13 BS 970, 321S12
BS 1503, 321S31 BS 970, 347S17
BS 1503, 347S31
NOTE – When specified in the order, cast steels should be Charpy V-notch impact tested in accordance with BS 131-2. British
Standard cast steels should have the impact properties specified in BS 1504 and BS 3100. Steels to ASTM A351 should have impact properties equal to the equivalent British Standard grades.
키워드에 대한 정보 bs 6364 cryogenic testing
다음은 Bing에서 bs 6364 cryogenic testing 주제에 대한 검색 결과입니다. 필요한 경우 더 읽을 수 있습니다.
이 기사는 인터넷의 다양한 출처에서 편집되었습니다. 이 기사가 유용했기를 바랍니다. 이 기사가 유용하다고 생각되면 공유하십시오. 매우 감사합니다!
사람들이 주제에 대해 자주 검색하는 키워드 Cryogenic Valve Test – Peach Valve Co., Ltd.
- Valve Cryogenic Test
Cryogenic #Valve #Test #- #Peach #Valve #Co., #Ltd.
YouTube에서 bs 6364 cryogenic testing 주제의 다른 동영상 보기
주제에 대한 기사를 시청해 주셔서 감사합니다 Cryogenic Valve Test – Peach Valve Co., Ltd. | bs 6364 cryogenic testing, 이 기사가 유용하다고 생각되면 공유하십시오, 매우 감사합니다.