당신은 주제를 찾고 있습니까 “saftronics fp5 manual – Repair Saftronics DG2 Plus DC Drive“? 다음 카테고리의 웹사이트 https://chewathai27.com/you 에서 귀하의 모든 질문에 답변해 드립니다: https://chewathai27.com/you/blog. 바로 아래에서 답을 찾을 수 있습니다. 작성자 GalcoTV 이(가) 작성한 기사에는 조회수 497회 및 좋아요 1개 개의 좋아요가 있습니다.
saftronics fp5 manual 주제에 대한 동영상 보기
여기에서 이 주제에 대한 비디오를 시청하십시오. 주의 깊게 살펴보고 읽고 있는 내용에 대한 피드백을 제공하세요!
d여기에서 Repair Saftronics DG2 Plus DC Drive – saftronics fp5 manual 주제에 대한 세부정보를 참조하세요
Saftronics DG2 Plus DC Drive repaired by experienced technicians. Katie Nyberg presents Galco’s repair capabilities. Contact Galco at 800-514-8230 or visit http://www.galco.com/scripts/cgiip.exe/wa/wcat/catalog.htm?searchbox=Saftronics%20DG2%20Plus\u0026source=YouTubeRepair to get your item repaired.
Save — Repair costs are often a significant savings versus the OEM
Cleaned — Every repair is cleaned and dried when possible
Refurbished, Not Just Repaired — Technicians replace commonly failed components when applicable.
Verified Repair — Most repairs are verified on a simulator to ensure long-term proper working order.
Quality — 3 Levels of quality control to make sure your equipment is repaired correctly.
18-Month ‘Bumper-to-Bumper’ Warranty — The entire unit you send to us for service is covered under warranty, not just the portion repaired.
Quick Turnaround — Fast, Faster and Fastest turnaround options, which can be as soon as next business day.
Pre-Priced Repair — In most cases you will know your repair cost before sending us your repair. Otherwise, we offer free evaluations and estimates.
To find all of Galco’s repair capabilities go to: http://www.galco.com/scripts/cgiip.exe/wa/wcat/r_browse.htm?division=IR\u0026source=YouTubeRepair
Galco is a Factory Authorized Stocking Distributor for Over 150 Brands of Industrial Electrical \u0026 Electronic Automation, Controls and Component Products; On-Site and Send-In Repair Services for Industrial Control \u0026 Automation Products for Over 2,000 Brands; Engineered Systems Integration, Retrofits \u0026 Upgrades for Variable Speed Drives, CNC, PLC Systems, Dynamometers \u0026 Test Stand Applications. Visit us online at http://www.galco.com or call us at 800-337-1720.
http://www.galco.com/safety
With respect to the usage, installation or assembly of any products described in this video, Galco Industrial Electronics, Inc., a Michigan corporation, encourages you to follow the requirements and/or guidelines of: i) the Occupational Safety and Health Act of 1970, Public Law 91-596, as amended, and all laws, rules and regulations implemented in relation thereto; ii) the National Electric Code®; and iii) NFPA 70E®. Any installation, assembly or work described in this video should be performed by a qualified licensed electrician.
GTV, Galco, galco.com, Galco Industrial Electronics, and Galco Industrial Electronics, Inc. are registered and/or pending registered trademarks under the U.S. Patent and Trademark Office, assumed names, registered domain names, and/or trade names of Galco Industrial Electronics, Inc., a Michigan corporation.
LEGAL DISCLAIMER:
While we have made every attempt to ensure that the information provided is accurate and has been obtained from reliable sources, Galco is not responsible for any errors or omissions, or for the results obtained from the use of this information. All information is provided \”as is\
saftronics fp5 manual 주제에 대한 자세한 내용은 여기를 참조하세요.
Saftronics FP5 Series User Manual
Fp5/gp5 series user’s manual variable torque inverter (with software version 5110/5120 and newer) efesotomasyon.Com – control techniques,emerson,saftronics -ac …
Source: www.dlmanuals.com
Date Published: 6/21/2021
View: 2581
Saftronics FP5 Series Inverter Operation & user’s manual PDF View …
Saftronics FP5 Series User Manual. Download Operation & user’s manual of Saftronics FP5 Series Inverter for Free or View it Online on All-Gues.com.
Source: all-guidesbox.com
Date Published: 4/2/2021
View: 2245
Saftronics GP5 Series Instruction manual – Manualzz
For more detailed configurations and applications refer to the GP5/FP5 instruction manual (Part # 027-2005F) available at www.saftronics.com.
Source: manualzz.com
Date Published: 3/11/2021
View: 6363
FP5 / GP5, Point Map – Data Sheet for Product
FP5 / GP5, Point Map – Data Sheet for Product. A6V10306121_en.pdf. Assortment_custom; Product_Group_Custom: 3rd party integration; Content_language_custom …
Source: sid.siemens.com
Date Published: 8/4/2021
View: 7443
FP5/GP5 TECHNICAL MANUAL – PDF Free Download
3 PREFACE Saftronics FP5/GP5 is the world s first optimized Inverter specifically designed for general-purpose applications. This manual describes installation, …
Source: docplayer.net
Date Published: 5/1/2021
View: 459
Saftronics FP5/GP5 Series User Manuals PDF Download
ℹ️ Download Saftronics FP5/GP5 Series Manuals (Total Manuals: 1) for free in PDF. Find more compatible user manuals for FP5/GP5 Series Inverter device.
Source: guidessimo.com
Date Published: 12/28/2022
View: 9539
주제와 관련된 이미지 saftronics fp5 manual
주제와 관련된 더 많은 사진을 참조하십시오 Repair Saftronics DG2 Plus DC Drive. 댓글에서 더 많은 관련 이미지를 보거나 필요한 경우 더 많은 관련 기사를 볼 수 있습니다.
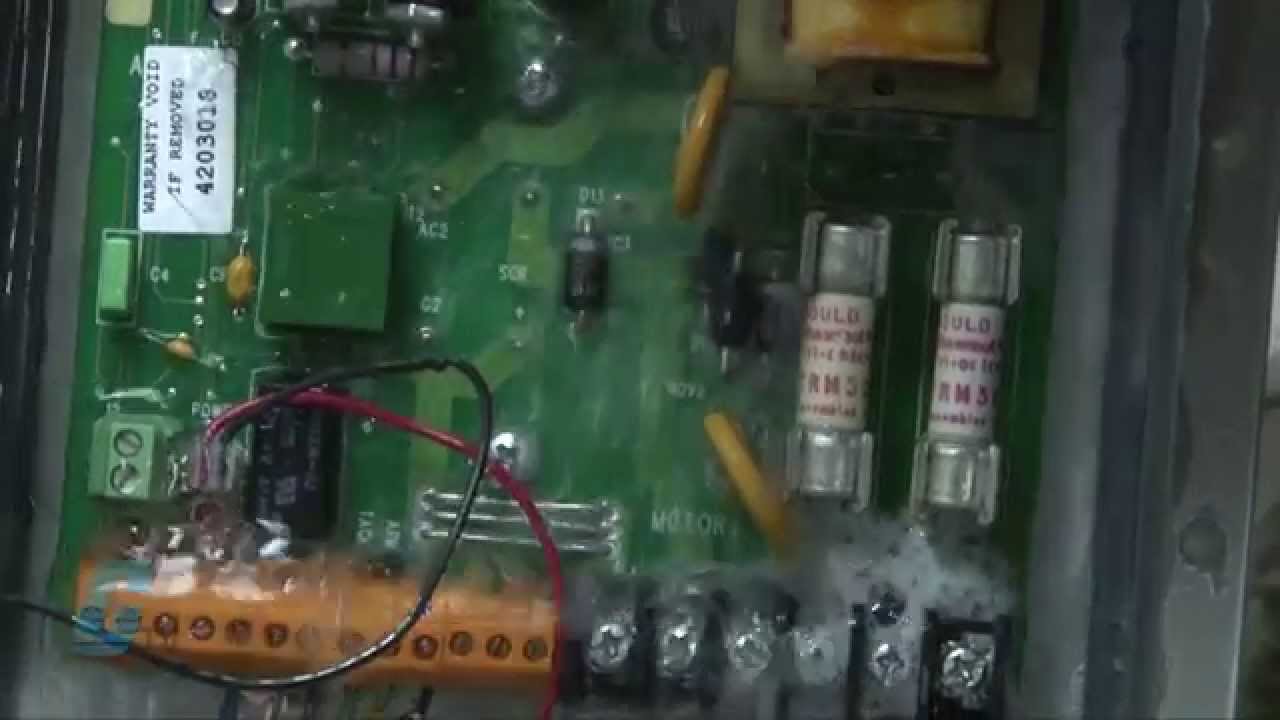
주제에 대한 기사 평가 saftronics fp5 manual
- Author: GalcoTV
- Views: 조회수 497회
- Likes: 좋아요 1개
- Date Published: 2015. 1. 23.
- Video Url link: https://www.youtube.com/watch?v=i9XebTH94_g
Saftronics FP5 Series User Manual
Page 1 Fp5/gp5 series user’s manual variable torque inverter (with software version 5110/5120 and newer) efesotomasyon.Com – control techniques,emerson,saftronics -ac drive-servo motor.
Page 2: Warning 2 fp5/gp5user’s manual precautions 1) read this manual in its entirety before installing or operating the fp5/gp5 inverter. This manual applies to inverters with software versions 5110 and 5120 only and is not intended to be used in con- junction with any other software. 2) do not connect or disconn…
Page 3 Fp5/gp5 user’s manual 3 contents section description page 1 receiving & installation 1.1 i ntroduction . . . . . . . . . . . . . . . . . . . . . . . . . . . . . . . . . . . 6 1.2 s pecifications . . . . . . . . . . . . . . . . . . . . . . . . . . . . . . . . . . . 7 gp5/fp5 . . . . . . . . . . . . ….
Page 4 4 fp5/gp5 user’s manual current limit (stall prevention). . . . . . . . . . . . . . . . . . . . 52 dc injection braking . . . . . . . . . . . . . . . . . . . . . . . . . . . . 54 energy savings control . . . . . . . . . . . . . . . . . . . . . . . . . . 55 frequency agree set point . . . . . . . . ….
Page 5: – Chapter 1 – Fp5/gp5 user’s manual 5 – chapter 1 – receiving & installation section description page 1 receiving & installation 1.1 i ntroduction . . . . . . . . . . . . . . . . . . . . . . . . . . . . . . . . . . . 6 1.2 s pecifications . . . . . . . . . . . . . . . . . . . . . . . . . . . . . . . . . . . 7 fp5…
Page 6 6 fp5/gp5 user’s manual 1.1 introduction the fp5/gp5 is a series of high quality, full featured inverters. With a power range of 5 to 500 hp, it provides all the functionality of prior series, in a compact, low cost package. This functionality includes proprietary features like full-range automatic …
Page 7 Fp5/gp5 user’s manual 7 1.2 specifications fp5/gp5 inverter model cimr-p5u 20p4 20p7 21p5 22p2 23p7 25p5 27p5 2011 2015 – o ut pu t c ha ra ct er ist ics motor output (hp) * 0.5 1 2 3 5 7.5 10 20 25 – capacity (kva) 1.2 2.3 3.0 4.2 6.7 9.5 13 19 24 – rated output current (a)-vt** 3.2 6 8 11 17.5 27 …
Page 8 8 fp5/gp5 user’s manual co nt ro l c ha ra ct er ist ics control method sine wave pwm with full-range, automatic torque boost frequency control range 0.1 to 400 hz frequency accuracy digital command: 0.01%, analog command: 0.1% frequency setting reso- lution digital operator reference: 0.1hz, analog…
Page 9 Fp5/gp5 user’s manual 9 fp5/gp5 inverter model cimr-p5u 2018 2022 2030 2037 2045 2055 2075 — o ut pu t c ha ra ct er ist ics motor output (hp) * 30 40 50 60 75 100 125 capacity (kva) 30 37 50 61 70 85 110 rated output current (a) – vt ** 80 104 130 160 192 248 312 rated output current (a) – ct ** 64…
Page 10 10 fp5/gp5 user’s manual co nt ro l c ha ra ct er ist ics control method sine wave pwm with full-range, automatic torque boost frequency control range 0.1 to 400 hz frequency accuracy digital command: 0.01%, analog command: 0.1% frequency setting resolution digital operator reference: 0.1hz, analog …
Page 11 Fp5/gp5 user’s manual 11 1.3 preliminary inspection receiving after unpacking the fp5/gp5: · verify that the part numbers on the drive nameplate match the num- bers on your purchase order or packing slip. · check the unit for physical damage which may have occurred during shipping. If any part of th…
Page 12 12 fp5/gp5 user’s manual identifying the parts figure 3 parts identification – model p5u43p7 protective cover (top/bottom) front cover 4 mounting holes digital operator jvop-130p heatsink nameplate ventilation slots 0 p drive fwd rev chapter 1 – receiving & installation preliminary inspection efesot…
Page 13: Caution Fp5/gp5user’s manual 13 1.4 mounting precautions 1) when preparing to mount the fp5/gp5, lift it by its base. Never lift it by the front cover. 2) mount the inverter onto nonflammable material. 3) the fp5/gp5 generates heat. For the most effective cooling possible, mount it vertically. For more deta…
Page 14 14 fp5/gp5 user’s manual removing and replacing the digital operator to remove the digital operator from the front cover, push the operator lever in the direction shown by arrow 1 and lift the digital operator in the direction shown by arrow 2 (see figure 4). To replace the digital operator, engage …
Page 15 Fp5/gp5user’s manual 15 dimensions/heat loss open chassis type (ip00) voltage model cimr -p5u open chassis dimensions in inches (mm) mass lbs (kg) heat loss (w) w h d w1 h1 h2 heat sink inside unit total 230v 20p4 5.51 (140) 11.02 (280) 6.30 (160) 4.96 (126) 10.47 (266) 0.28 (7) 6.5 (3) 15 50 65 20p…
Page 16 16 fp5/gp5 user’s manual enclosed type (nema 1, ip20) voltage model (cimr- p5u) nema 1 dimensions in inches (mm) mass lbs (kg) w h d w1 h1 h2 230v 20p4 5.51 (140) 11.02 (280) 6.30 (160) 4.96 (126) 10.47 (266) 0.28 (7) 6.5 (3) 20p7 21p5 22p2 5.51 (140) 11.02 (280) 7.09 (180) 4.96 (126) 10.47 (266) 0….
Page 17 Fp5/gp5 user’s manual 17 clearances when mounting the fp5/gp5, allow sufficient clearances for effec- tive cooling as shown below: notes: 1) the required clearances at the top, bottom, and both sides of the inverter are the same for both open chassis and nema 1 enclosures. 2) for inverter models 25h…
Page 18: Caution 18 fp5/gp5 user’s manual 1.5 wiring precautions 1) do not connect or disconnect wiring, or perform signal checks while the power supply is turned on. 2) connect the power supply wiring to terminals l1, l2 and l3 on the main circuit input section. Do not connect the power supply wiring to output term…
Page 19 Fp5/gp5 user’s manual 19 fp5/gp5 standard connection diagram figure 9 fp5/gp5 terminal diagram digital rs-232 serial port analog inputs (250 Ω ) operator input fi selectable 4~20ma or 0~10v (10-pin) im ⊕ 1 ⊕ 2 b1 b2 230v: models 20p4 through 27p5 460v: models 40p4 through 4015 s1 – fixed s2 s3 sc (c…
Page 20 20 fp5/gp5user’s manual fp5/gp5 standard connection diagram figure 10 fp5/gp5 terminal diagram digital rs-232 serial port analog inputs (250 Ω ) operator input fi selectable 4~20ma or 0~10v (10-pin) s1 – fixed s2 s3 sc (com) s4 s5 s6 fs fv fi fc pwm 8 bit multi-function inputs g (+15v) (20k Ω ) (0v)…
Page 21 Fp5/gp5 user’s manual 21 main circuit wiring input wiring · molded-case circuit breaker (mccb) be sure to connect mccbs or fuses between the ac main circuit power supply and fp5/gp5 input terminals l1, l2 and l3, to protect the power supply wiring. · ground fault interrupter when connecting a ground…
Page 22 22 fp5/gp5 user’s manual · surge suppressor for inductive loads (i.E. Magnetic contactors, magnetic relays, magnetic valves, solenoids, magnetic brakes, etc.) connected near the inverter, use a surge suppressor across the coils to limit the transients on the sup- ply lines. Output wiring · motor con…
Page 23 Fp5/gp5 user’s manual 23 chapter 1 – receiving & installation wiring grounding · ground resistance 230v class: 100 Ω or less, 460v class: 10 Ω or less. · never ground the fp5/gp5 in common with welding machines, motors, or other high-current electrical equipment. Run all ground wir- ing in a separat…
Page 24 24 fp5/gp5 user’s manual chapter 1 – receiving & installation wiring terminal functions 230v class terminal functions 460v class terminal functions model cimr-p5u 20p4 to 27p5 2011 to 2015 2018 to 2075 nominal motor output 0.5 to 10hp 20 to 25hp 30 to 125hp l1 main circuit input power supply main ci…
Page 25 Fp5/gp5 user’s manual 25 chapter 1 – receiving & installation wiring wire and terminal screw sizes 230v class wire size * wire sizes are based on 75°c copper wire. Note: voltage drop should be considered when determining wire size. Voltage drop can be calculated using the following equation: select …
Page 26 26 fp5/gp5 user’s manual chapter 1 – receiving & installation wiring 460v class wire size * wire sizes are based on 75°c copper wire. Circuit model cimr- terminal symbol terminal screw wire size * max. Torque lb-in (n·m) wire type awg mm 2 main p5u40p4 l1, l2, l3, , ⊕ 1, ⊕ 2, b1, b2, t1, t2, t3 m4 1…
Page 27 Fp5/gp5 user’s manual 27 chapter 1 – receiving & installation wiring jst closed loop connectors note: the use of a jst closed-loop connector (lug) is recommended to maintain proper clearances. Please contact your saftronics representative for more information. Wire size * terminal screw jst closed-l…
Page 28 28 fp5/gp5 user’s manual chapter 1 – receiving & installation wiring control circuit wiring the following table outlines the functions of the control circuit terminals. Control circuit terminals classifi- cation terminal function description signal level m ul ti- fu nc tio n in pu t s ig na l s1 for…
Page 29: – Chapter 2 – Fp5/gp5 user’s manual 29 – chapter 2 – operation section description page 2 operation precautions. . . . . . . . . . . . . . . . . . . . . . . . . . . . . . . . . . . . 30 2.1 t rial o peration . . . . . . . . . . . . . . . . . . . . . . . . . . . . . . . . 31 digital operator display at power-up . …
Page 30: Warning 30 fp5/gp5 user’s manual precautions 1) only turn on the input power supply after replacing the front cover. Do not remove the cover while the inverter is powered up. 2) when the retry function (n060) is selected, do not approach the inverter or the load, since it may restart suddenly after being st…
Page 31 Fp5/gp5 user’s manual 31 2.1 trial operation to ensure safety, prior to initial operation, disconnect the machine cou- pling so that the motor is isolated from the machine. If initial operation must be performed while the motor is still coupled to the machine, use great care to avoid potentially haz…
Page 32 32 fp5/gp5 user’s manual operation checkpoints: · motor rotates smoothly. · motor rotates in the correct direction. · motor has no abnormal vibration and is not noisy. · acceleration and deceleration are smooth. · unit is not overloaded. · status indicator leds and digital operator display are corre…
Page 33 Fp5/gp5 user’s manual 33 typical operation example by digital operator (jvop-130p) description key sequence digital operator display (1) power on · displays frequency reference value. Operation condition setting · select local mode. (2) frequency setting · change frequency reference value. (3) forwa…
Page 34 34 fp5/gp5 user’s manual operation by control circuit terminal signal the diagram below shows a typical operation pattern using the control circuit terminal signals. Typical operation example by control circuit terminal signal description key sequence digital operator display (1) power on · displays…
Page 35 Fp5/gp5 user’s manual 35 2.2 digital operator display all functions of the fp5/gp5 are accessed using the jvop-130p digi- tal operator. Below are descriptions of the display and keypad sections. Local remote enter dspl run stop reset digital operator jvop-130p prgm kwout fref fout iout f/r montr acc…
Page 36 36 fp5/gp5 user’s manual 2.3 led description simple operation of the fp5/gp5 is possible, by using the quick-start displays. Quick-start displays (example of cimr-p5u23p7) description key sequence digital operator display remarks depress [enter] key to display the monitor value. Power on frequency r…
Page 37 Fp5/gp5 user’s manual 37 2.4 operation mode selection (n002, oper mode select) the fp5/gp5 has two operation modes: local and remote (see table below for description). These two modes can be selected by the digital operator “local/remote” key only when operation is stopped. The operation mode select…
Page 38 38 fp5/gp5 user’s manual this page intentionally left blank. Efesotomasyon.Com – control techniques,emerson,saftronics -ac drive-servo motor.
Page 39: – Chapter 3 – Fp5/gp5 user’s manual 39 – chapter 3 – programming features section description page 3 programming features 3.1 fp5/gp5 p arameters (n001~n116) . . . . . . . . . . . 41 3.2 p arameter s et – up & i nitialization . . . . . . . . . . . . . . . 49 3.3 fp5/gp5 o peration . . . . . . . . . . . . . . . . …
Page 40 40 fp5/gp5 user’s manual stopping method . . . . . . . . . . . . . . . . . . . . . . . . . . . . . . . 70 torque adjustment. . . . . . . . . . . . . . . . . . . . . . . . . . . . . . 72 torque detection . . . . . . . . . . . . . . . . . . . . . . . . . . . . . . . 73 tripless operation . . . . . . ….
Page 41 Fp5/gp5 user’s manual 41 3.1 fp5/gp5 parameters (n001~n116) no. Function name (lcd operator display) description factory default user setting ref. Page n001 parameter selection/ initialization (password) 0: n001 read and set, n002~n116 read only 1: n001~n035 read and set, n036~n116 read only 2: n001…
Page 42 42 fp5/gp5 user’s manual n014 mid. Output frequency (mid frequency) unit: 0.1hz setting range: 0.1~399.9hz 3hz 76 n015 mid. Frequency voltage (mid voltage) unit: 0.1v setting range: 0.1~255.0v (510v for 460v units) 17.2v (34.4v) 76 n016 minimum output frequency (min frequency) unit: 0.1hz setting ra…
Page 43 Fp5/gp5 user’s manual 43 n034 motor thermal protection (motor ol sel) led setting lcd setting description 0 disabled protection disabled 1 std motor/8 min general-purpose motor (time constant 8 min.) 2 std motor/5 min general-purpose motor (time constant 5 min.) 3 inv motor/8 min blower-cooled motor…
Page 44 44 fp5/gp5 user’s manual n037 multi-function input 2 (terminal s3 sel) set items are same as n036. (when n036=”fwd/rev cmd (3w), “in use by other” is displayed, and setting is prohibited) ext fault (no) 78 n038 multi-function input 3 (terminal s4 sel) set items are same as n036. Fault reset 78 n039 …
Page 45 Fp5/gp5 user’s manual 45 n047 frequency reference level at loss of fref (fref [email protected] loss) unit: 1% setting range: 0~100% of setting fref 80% 82 n048 terminal fv gain (terminal fv gain) unit: 1% setting range: 0~200% 100% 59,96 n049 terminal fv bias (terminal fv bias) unit: 1% setting range: -100~100…
Page 46 46 fp5/gp5 user’s manual n065 elapsed timer selection (elapsed timer) led setting lcd setting description 0 time power is on accumulate time during power on 1 time running mtr accumulate time during running time running mtr – n066 elapsed timer 1 (elapsed time 1) unit: 1 hour range: 0~9999 * initial…
Page 47 Fp5/gp5user’s manual 47 n078 over/undertorque detection level ol3 (torq det level) unit: 1% setting range: 30~200% 100% = inverter rated current 160% 74 n079 over/undertorque detec- tion delay time ol3 (torq det time) unit: 0.1s setting range: 0.1~10.0s 0.1s 74 n080 on-delay timer (on-delay timer) u…
Page 48 48 fp5/gp5 user’s manual n096 energy saving selection (energy save sel) led setting lcd setting description 0 disabled energy saving is disabled. 1 enabled energy saving is enabled. Disabled 55,96 n097 energy saving gain k2 (energy save gain) unit: 0.01 setting range: 0.00~655.0 (0=no energy saving)…
Page 49 Fp5/gp5 user’s manual 49 3.2 parameter set-up & initialization parameter selection/initialization (n001, password) the following table describes data which can be set or read when parame- ter n001 is set. N112 low frequency ol start point (low freq ol2 start) unit: 0.1hz setting range: 0.0 ~ 10.0hz …
Page 50 50 fp5/gp5user’s manual 3.3 fp5/gp5 operation accel/decel time adjustment when any of the multi-function input terminal selections (n036, n037, n038, n039 or n040) is set to “acc/dec switch”, accel/decel times can be selected by opening or closing the appropriate terminal (s2, s3, s4, s5 or s6). At …
Page 51 Fp5/gp5 user’s manual 51 automatic fault retry (n060, num of restarts) after a fault occurs, the inverter can automatically restart. The number of retry attempts can be set up to 10 times via parameter n060. The inverter can be set to automatically restart after the following faults occur: · overcur…
Page 52 52 fp5/gp5 user’s manual current limit (stall prevention) this function automatically adjusts the output frequency in response to an increase in load current to continue operation without tripping the inverter. · stall prevention level during acceleration (n073, stallp accel lvl) the current limit l…
Page 53 Fp5/gp5 user’s manual 53 in the constant output area [output frequency ≥ base frequency (n013)], the current limit level during acceleration is changed by the following equation: · stall prevention level during running (n074, stallp run level) the stall prevention level during running can be set in …
Page 54 54 fp5/gp5 user’s manual · stall prevention during deceleration (n072, stallp decel sel) to prevent overvoltage during deceleration, the inverter automatically extends the deceleration time according to the value of main circuit dc voltage. When using an optional braking resistor for the fp5/gp5, se…
Page 55 Fp5/gp5 user’s manual 55 · dc injection braking time at start (n070) dc injection braking time at start can be set in increments of 0.1 sec- ond. When parameter n070 is set to “0”, dc injection braking at start- ing is disabled. Energy saving control to enable energy saving control, set energy savin…
Page 56 56 fp5/gp5 user’s manual limit, this lower limit value is output as the voltage reference value. The lower limit value is set in order to prevent stalling at light loads. Set voltage limits at 6hz and 60hz; a value obtained by linear interpolation should be used to set any limit values other than at…
Page 57 Fp5/gp5 user’s manual 57 frequency agree set point (n075, freq det level) when multi-function contact output selections n041 or n042 are set to “freq det 1” or “freq det 2”, frequency detection is enabled. This function is acti- vated when the output frequency is above or below the frequency agree s…
Page 58 58 fp5/gp5 user’s manual frequency meter or ammeter (n052, terminal am sel) this parameter selects whether the signal (on terminals am and ac) is proportional to output frequency, output current, output power, or dc bus voltage for external monitoring. Frequency meter or ammeter calibration (n053, t…
Page 59 Fp5/gp5 user’s manual 59 chapter 3 – programming features fp5/gp5 operation · terminal fv gain (n048, terminal fv gain) the analog input voltage value for the maximum output frequency (n011) can be set in units of 1%, from 0 to 200%. Factory setting: 100% · terminal fv bias (n049, terminal fv bias) …
Page 60 60 fp5/gp5 user’s manual to operate the inverter with a frequency reference of 50% to 100% at a 0 to 10v input: gain: parameter n048 = “100” bias: parameter n049 = “50” jog operation multi-function inputs (terminals s2 to s6) can be programmed to func- tion as a jog reference selection. Operation ca…
Page 61 Fp5/gp5 user’s manual 61 chapter 3 – programming features fp5/gp5 operation modbus communication the fp5/gp5 can perform serial transmission by using a program- mable controller (plc) and modbus communication. Modbus is composed of one master plc and 1 to 31 (maximum) slave inverters. In signal tran…
Page 62 62 fp5/gp5 user’s manual chapter 3 – programming features fp5/gp5 operation · modbus frequency reference unit (n103, modbus fref unit) the frequency reference units from the plc and in the frequency refer- ence and output frequency monitors (by communication) are set with parameter n103. The output …
Page 63 Fp5/gp5 user’s manual 63 chapter 3 – programming features fp5/gp5 operation · general-purpose and blower-cooled motors induction motors are classified as general-purpose or blower-cooled motors, based on their cooling capabilities. Hence, the motor overload detection function operates differently fo…
Page 64 64 fp5/gp5 user’s manual chapter 3 – programming features fp5/gp5 operation multi-step speed selection this function allows the programming of up to 4 preset speeds, through multi-function contact input selections. 4-step speed selection n002 = “seq=x ref=opr”, where “x” can be trm, opr, or com n024…
Page 65 Fp5/gp5 user’s manual 65 chapter 3 – programming features fp5/gp5 operation phase loss protection · input phase loss detection (n083, in ph loss lvl) the input phase loss detection circuit monitors the dc bus current ripple and activates when one of the input phases are lost. The detection circuit c…
Page 66 66 fp5/gp5 user’s manual chapter 3 – programming features fp5/gp5 operation pid control to enable pid control, set pid selection (n084) to “enabled”, according to the description below. Then select the pid control setpoint value and detected feedback value setpoint as follows: · setpoint value selec…
Page 67 Fp5/gp5 user’s manual 67 chapter 3 – programming features fp5/gp5 operation notes: 1) value i is reset to”0” in the following cases: · when operation stops · when the integral value reset signal is input by multi-function contact input selection (any of parameters n036 to n040 are set to “pid i rese…
Page 68 68 fp5/gp5 user’s manual chapter 3 – programming features fp5/gp5 operation reverse run prohibit (n006, reverse oper) a “reverse run disabled” setting does not accept a reverse run command from the control circuit terminal or the digital operator. This setting is used in applications where a reverse…
Page 69 Fp5/gp5 user’s manual 69 chapter 3 – programming features fp5/gp5 operation the following figure shows fwd/rev run switching during deceleration to stop. Speed limit adjustment · frequency reference upper limit (n031, ref upper limit) the upper limit of the frequency reference can be set in incremen…
Page 70 70 fp5/gp5 user’s manual chapter 3 – programming features fp5/gp5 operation stopping method (n004, stopping method) this function selects the stopping method suitable for the particular application. · deceleration to stop (n004 = “ramp to stop”) upon removal of the fwd (rev) run command, the motor d…
Page 71 Fp5/gp5 user’s manual 71 chapter 3 – programming features fp5/gp5 operation · coast to stop with timer 1 (n004 = “coast w/timer 1”) upon removal of the run command, the inverter output is immediately removed, allowing the motor to coast. If the run command is re-applied before the minimum baseblock …
Page 72 72 fp5/gp5user’s manual chapter 3 – programming features fp5/gp5 operation torque adjustment (n071, torq comp gain) motor torque can be adjusted by changing the v/f pattern (n010) or by adjusting the torque compensation gain (n071). For details on setting the v/f pattern, see “v/f pattern adjustment…
Page 73 Fp5/gp5 user’s manual 73 chapter 3 – programming features fp5/gp5 operation torque detection the over/undertorque detection circuit will activate when the motor load causes the motor current to go above or below torque detection level (n078) respectively. When the over/undertorque condition is detec…
Page 74 74 fp5/gp5 user’s manual chapter 3 – programming features fp5/gp5 operation · over/undertorque detection level (n078, torq det level) sets the torque detection current level in units of 1% inverter rated current: 100% factory default: 160% · over/undertorque detection time (n079, torq det time) the …
Page 75 Fp5/gp5 user’s manual 75 chapter 3 – programming features fp5/gp5 operation · dc injection braking at start (n068, dcinj current; n070, dcinj [email protected]) this function restarts a coasting motor after first applying it with dc injection braking. Dc injection braking time at start (n070) is set in uni…
Page 76 76 fp5/gp5 user’s manual chapter 3 – programming features inputs & outputs * for 460v class units, the value is twice that of 230v class units. Increasing the voltage in the v/f pattern increases motor torque, how- ever, an excessive increase may cause: · inverter fault trips as a result of motor ov…
Page 77 Fp5/gp5 user’s manual 77 chapter 3 – programming features inputs & outputs slip compensation the slip compensation feature allows better speed regulation to be obtained by adjusting the output frequency according to the changing load. This feature compensates for the slip of the motor. Slip compensa…
Page 78 78 fp5/gp5 user’s manual chapter 3 – programming features inputs & outputs 3.4 inputs & outputs multi-function input signals (n036 to n040) multi-function contact input terminal s2 to s6 functions can be changed when necessary by setting parameters n036 to n040, respectively. None of these parameter…
Page 79 Fp5/gp5 user’s manual 79 chapter 3 – programming features inputs & outputs · local/remote selection (setting: “local/remote sel”) selects whether the run command is received from the digital operator or the control circuit terminal. Local/remote selection is available only while the inverter is stop…
Page 80 80 fp5/gp5 user’s manual chapter 3 – programming features inputs & outputs example: set n002 to “seq=trm ref=trm”. Open: frequency reference from control circuit terminals fv & fi, and run command from control circuit terminals s1 and s2. Closed: frequency reference and run command from serial commu…
Page 81 Fp5/gp5user’s manual 81 chapter 3 – programming features inputs & outputs · up/down command (setting: n040 = “up/down control”) with the fwd (rev) run command entered, a change in frequency is performed by inputting the up or down commands to control circuit terminals s5 and s6, so that operation ca…
Page 82 82 fp5/gp5user’s manual chapter 3 – programming features inputs & outputs analog input signals · master analog input selection (n043, analog input sel) to input the master frequency reference from the control circuit terminal, use terminal fv (0 to 10v) or terminal fi (4 to 20ma), by setting paramet…
Page 83 Fp5/gp5 user’s manual 83 multi-function output signals (n041, terminal ma sel; n042, terminal m1 sel) multi-function output terminal ma, mb and m1 functions can be changed when necessary by setting parameters n041 and n042. · terminal ma and mb functions: set via n041 · terminal m1 functions: set vi…
Page 84 84 fp5/gp5 user’s manual chapter 3 – programming features frequency agree (setting: “at speed”) see figure 51 below for an example of selecting the frequency agree sig- nal as the function of output terminals ma, mb or m1. Desired frequency agree (setting: “at desired speed”) see figure 52 below for…
Page 85: – Chapter 4 – Fp5/gp5 user’s manual 85 – chapter 4 – diagnostics section description page 4 diagnostics precautions. . . . . . . . . . . . . . . . . . . . . . . . . . . . . . . . . . . . 86 4.1 m aintenance & i nspection . . . . . . . . . . . . . . . . . . . . . . 87 periodic inspection . . . . . . . . . . . . . …
Page 86: Warning 86 fp5/gp5 user’s manual precautions 1) never touch high voltage terminals in the inverter. 2) replace all protective covers before powering up the inverter. When removing the cover, be sure to shut off the power supply to the inverter. 3) perform maintenance or inspection only after verifying that …
Page 87 Fp5/gp5 user’s manual 87 4.1 maintenance & inspection this section describes basic maintenance and inspection procedures for the fp5/gp5. Periodic inspection the fp5/gp5 will function longer if it is kept clean, cool and dry, and if all precautions highlighted in this manual are observed. Periodi- c…
Page 88 88 fp5/gp5 user’s manual 4.2 alarm & fault displays this section describes the alarm and fault displays, explanations for fault condi- tions, and corrective actions to be taken if the fp5/gp5 malfunctions. Alarm display unlike faults, alarms do not activate fault contact outputs. After the cause of …
Page 89 Fp5/gp5 user’s manual 89 fault display when the fp5/gp5 detects a fault, the fault is displayed on the digital operator and a fault contact output is activated after which the motor coasts to a stop. Check the causes listed in the table below and take the corre- sponding corrective actions. To reset…
Page 90 90 fp5/gp5 user’s manual * o h1 overheat 1 heatsink overheat (oh1) the transistor heatsink temperature exceeded the allowable value (fin temperature > oh1 detection level). Check the fan and ambient temperature. O h2 overheat 2 heatsink overheat (oh2) the transistor heatsink temperature exceeded the…
Page 91 Fp5/gp5 user’s manual 91 * stopping method selection is available for these faults. * ce modbus com err modbus transmission fault control data cannot be received nor- mally. Check the transmission devices or signals. Cpf0 com-err (op +inv) control circuit fault 1 (cpfo) digital operator transmission…
Page 92 92 fp5/gp5 user’s manual motor faults if a motor fault occurs, follow the checkpoints listed in the table below and take the corresponding corrective actions. If taking the corrective actions described does not solve the problem, contact your saftronics representative immediately. Motor faults and c…
Page 93: Appendix Fp5/gp5 user’s manual 93 appendix section description page a appendix a-1 b raking c onnection d iagrams . . . . . . . . . . . . . . . . . . 94 a-2 d igital o perator m onitor d isplay . . . . . . . . . . . . . . 95 a-3 ce c onformance . . . . . . . . . . . . . . . . . . . . . . . . . . . . . . . 97…
Page 94 94 fp5/gp5 user’s manual a-1 braking connection diagrams braking resistor unit 230v: 5~25hp 460v: 5~25hp p b 1 2 overload relay trip contact braking resistor unit overload relay trip contact of braking resistor unit 1 2 mc fault contact trx sa trx thrx sa sa mc mc thrx on off ma mc vs-616pc5 l1 l2 l…
Page 95 Fp5/gp5 user’s manual 95 a-2 digital operator monitor display the following table describes the contents of the digital operator monitor display. Digital operator monitor display name (lcd operator display) description frequency reference (frequency ref) · frequency reference can be monitored/set. ·…
Page 96 Fp5/gp5 user’s manual 96 monitor (monitor u-xx) u-09 last 4 faults are displayed. U-10 last 4 digits of software revision number are displayed. U-11 u-12 elapsed time is displayed as follows: u-13 pid feedback is displayed in units of 0.1hz. U-15 kilowatt-hour meter (4 least significant digits) u-16…
Page 97 Fp5/gp5 user’s manual 97 appendix a-3 ce conformance a-3 ce conformance (applicable to 460v models only) ce conformance – low voltage directive (lvd) compliance digital rs-232 serial port analog inputs (250 Ω ) operator input fi selectable 4~20ma or 0~10v (10-pin) im ⊕ 1 ⊕ 2 b1 b2 s1 – fixed s2 s3 s…
Page 98 Fp5/gp5 user’s manual 98 ce conformance – electro-magnetic compatibility (emc) compliance in order to conform to emc standards, exclusive-use methods are required for line filter application, cable shielding and inverter installation. An outline of the methods follows. The line filter and the invert…
Page 99 Fp5/gp5 user’s manual 99 appendix a-3 ce conformance l2 l1 l3 gnd ground bonds (remove any paint) power line filter load inverter w l1l2 uv l3 ground bonds (remove any paint) im cable length: max. 40cm metal plate motor cable: max. 20m fig. 12 installation of line filter and inverter (models fp5/gp5…
Page 100 Fp5/gp5 user’s manual 100 safety warnings and operating information for inverters introduction depending on their protection rating configuration, parts of inverters can have live, unin- sulated and hot surfaces during operation. If housing components, the control unit or ter- minal covers are remov…
Saftronics FP5 Series Inverter Operation & user’s manual PDF View
Saftronics FP5 Series User Manual
Download Operation & user’s manual of Saftronics FP5 Series Inverter for Free or View it Online on All-Guides.com.
1 2 3 4 5 6 7 8 9 10 11 12 13 14 15 16 17 18 19 20 21 22 23 24 25 26 27 28 29 30 31 32 33 34 35 36 37 38 39 40 41 42 43 44 45 46 47 48 49 50 51 52 53 54 55 56 57 58 59 60 61 62 63 64 65 66 67 68 69 70 71 72 73 74 75 76 77 78 79 80 81 82 83 84 85 86 87 88 89 90 91 92 93 94 95 96 97 98 99 100 101
FP5/GP5 TECHNICAL MANUAL
Transcription
1 FP5/GP5 TECHNICAL MANUAL
2
3 PREFACE Saftronics FP5/GP5 is the world s first optimized Inverter specifically designed for general-purpose applications. This manual describes installation, maintenance and inspection, troubleshooting, and specifications of the FP5/GP5. Read this manual thoroughly before operation. General Precautions Some drawings in this manual are shown with the protective cover or shields removed, in order to describe detail with more clarity. Make sure all covers and shields are replaced before operating this product. This manual may be modified when necessary because of improvement of the product, modification, or changes in specifications. Such modifications are denoted by a revision number. To order a copy of this manual, contact your Saftronics representative. Saftronics is not responsible for any modification of the product made by the user, since that will void your warranty.
4 PREFACE Notes for Safe Operation Read this manual thoroughly before installation, operation, maintenance or inspection of the FP5/GP5. In this manual, notes for safe operation are classified as followed: WARNING Indicates a potentially hazardous situation which, if not avoided, could result in death or serious injury to personnel. CAUTION Indicates a potentially hazardous situation which, if not avoided, may result in minor or moderate injury to personnel and damage to equipment. It may also be used to alert against unsafe practices. Even items described in CAUTION may result in a fatal accident in some situations. In either case, follow these important notes. Take the following steps to ensure proper operation. Receiving CAUTION Do not install or operate any Inverter that is damaged or has missing parts. Failure to observe this may result in personal injury or equipment damage. Page 2 Installation CAUTION When moving the unit, lift the cabinet by the base, never lift by the front cover. Otherwise, the main unit may be dropped causing damage to the unit. 6 Mount the Inverter on nonflammable material (i.e., metal). Failure to observe this can result in a fire. 6 When mounting units in an enclosure, install a fan or other cooling device to keep the intake air temperature below 45 C. Overheating may cause a fire or damage the unit. 6 Wiring Page WARNING Only commence wiring after verifying that the power supply is turned OFF. Failure to observe this warning can result in an electrical shock or fire. Wiring should be performed only by qualified personnel. Failure to observe this warning can result in an electrical shock or fire. When wiring the emergency stop circuit, check the wiring thoroughly before operation. Failure to observe this warning can result in personal injury. Make sure to ground the ground terminal ( ). (Ground resistance 200V class: 100Ω or less, 400V class: 10Ω or less.) Failure to observe this warning can result in an electrical shock or fire. Page Revision: 1 (9/98) ii Saftronics, Inc.
5 PREFACE CAUTION Verify that the Inverter rated voltage coincides with the AC power supply voltage. Failure to observe this can result in personal injury or fire. Do not perform a withstand voltage test on the Inverter. It may cause semi-conductor elements to be damaged. To connect a Braking Resistor, Braking Resistor Unit or Braking Unit, follow the procedures described in Chapter 11. Improper connection may cause a fire. 10 Tighten terminal screws to the specified tightening torque. Failure to observe this can result in a fire. 10 Never connect the AC main circuit power supply to output Terminals T1, T2, and T3 (U, V, and W). The Inverter will be damaged and invalidate the warranty. Operation Page WARNING Only turn ON the input power supply after replacing the front cover. Do not remove the cover while current is flowing. Failure to observe this can result in an electrical shock. When the retry function (n057) is selected, do not approach the Inverter or the load, since it may restart suddenly after being stopped. (Construct machine system, so as to assure safety for personnel, even if the Inverter should restart.) Failure to observe this can result in personal injury. Since the stop button can be disabled by a function setting, install a separate emergency stop switch. Failure to observe this can result in personal injury. Page CAUTION Never touch the heatsink or discharging resistor since the temperature is very high. Failure to observe this can result in harmful burns to the body. Since it is easy to change operation speed from low to high speed, verify the safe working range of the motor and machine before operation. Failure to observe this can result in personal injury and machine damage. Install a holding brake separately, if necessary. Failure to observe this can result in personal injury. 24 Do not change signals during operation. The machine or the Inverter may be damaged. 24 All the constants of the Inverter have been preset at the factory. Do not change the settings unnecessarily. The Inverter may be damaged. For supply voltage, follow Paragraph 4.3 of Chapter 4. Page Revision: 1 (9/98) iii Saftronics, Inc.
6 PREFACE Maintenance and Inspection WARNING Never touch high-voltage terminals in the Inverter. Failure to observe this can result in an electrical shock. Replace all protective covers before powering up the Inverter. To remove the cover, make sure to shut OFF the Molded Case Circuit Breaker. Failure to observe this can result in an electrical shock. Perform maintenance or inspection only after verifying that the CHARGE LED goes OFF, after main circuit power supply is turned OFF. The capacitors are still charged and can be dangerous. Only authorized personnel should be permitted to perform maintenance, inspections or parts replacement. (Remove all metal objects (watches, bracelets, etc.) before operation. Use tools that are insulated against electrical shock.) Failure to observe this can result in an electrical shock. Page CAUTION The control PC board employs CMOS ICs. Do not touch the CMOS elements. They are easily damaged by static electricity. Do not connect or disconnect wires or connectors while power is applied to the circuit. Failure to observe this can result in personal injury. Page Others WARNING Never modify the product. Failure to observe this can result in an electrical shock or personal injury and will invalidate the warranty. Revision: 1 (9/98) iv Saftronics, Inc.
7 Table of Contents 1 Receiving Inspection Checkpoints Receiving Checkpoints Checking the Nameplate Data Identifying the Parts Installation Removing and Replacing the Digital Operator Removing the Digital Operator Replacing the Digital Operator Removing and Replacing the Front Cover Choosing a Location to Mount the Inverter Clearances Wiring Connection Diagram Wiring the Main Circuit Wiring Precautions for Main Circuit Point Wiring Precautions for Main Circuit Output Grounding Functions of Main Circuit Terminals Main Circuit Configuration Parts Required for Wiring Wiring the Control Circuit Functions of Control Circuit Terminals Wiring the Control Circuit Terminals Precautions on Control Circuit Wiring Wiring Inspection Operation Operation Mode Selection Test Run Checkpoints Setting the Line Voltage Using Jumper (For 400V Class 18.5kW and Above) Test Run Digital Operator Display at Power-Up Operation Check Points Example of Basic Operation Simple Data Setting Digital Operator Key Description LED Description Programming Features Constant Set-Up and Initialization Constant Selection/Initialization (n001) V/f Pattern Setting Preset V/f Pattern Custom V/f Pattern Setting Operation Conditions Reverse Run Prohibit (n006) Multi-Step Speed Selection Operation at Low Speed Adjusting Frequency Setting Signal Adjusting Frequency Upper and Lower Limits Revision: 1 (9/98) v Saftronics, Inc.
8 6.3.6 Using Two Accel/Decel Times Automatic Restart after Momentary Power Loss (n051) Soft-Start Characteristics (n023) Torque Detection Frequency Detection (n073) Jump Frequencies (n058 to n060) Continuing Operation by Automatic Fault Reset (n056) Operating Coasting Motor without Trip Using Frequency Meter of Ammeter (n048) Calibrating Frequency Meter of Ammeter (n049) Reducing Motor Noise or Leakage Current (n050) Selecting Stopping Method Selecting Stopping Method (n004) Coast to Stop with Timer 1 (n004=2) Applying DC Injection Braking Current (n064) Building Interface Circuits with External Devices Using Sequence Input Signals (n035 to n039) Using Analog Input Signals (n042 to n045) Using Output Signals (n040, n041) Setting Operation Conditions Torque Compensation Gain (n067) Motor Protection Motor Overload Detection PID Control Intended Value Setting Detected Value Setting Energy Saving Control Energy Saving Gain K2 (n096) Energy Saving Tuning MEMOBUS Control Communication Specifications Data to be Sent/Received by Communication Maintenance and Inspection Periodic Inspector Parts Replacement Schedule (Guidelines) Troubleshooting Fault Diagnosis and Corrective Actions Alarm Display and Explanation Motor Faults and Corrective Actions Specifications Standard Specifications Dimensions Dimensions Typical Connection Diagram Braking Resistor Unit Braking Unit and Braking Resistor Unit Constant List Constant List Digital Operator Monitor Display Digital Operator Monitor Display INDEX Revision: 1 (9/98) vi Saftronics, Inc.
9 This chapter describes how to inspect the inverter after delivery to the user. 1 Receiving 1.1 Inspection Checkpoints Receiving Checkpoints Checking the Nameplate Data Identifying the Parts… 2
10 Chapter 1: Receiving CAUTION Do not install or operate any Inverter which is damaged or has missing parts. Failure to observe this may result in personal injury or equipment damage. 1.1 Inspections Checkpoints Receiving Checkpoints Table 1 Checkpoints Does the Inverter model number correspond with the purchase order? Are any parts damaged? Is hardware properly seated and securely tightened? Was an instruction manual received? Checkpoints If any of the above checkpoints are not satisfactory, contact your Saftronics representative Checking the Nameplate Data Nameplate Data Description Check the model number on the nameplate on the side of the FP5/GP5. (See below.) Visually check the exterior and verify that there was no damage during transport. Remove Inverter front cover. Check all visible hardware with appropriate tools. FP5/GP5 Instruction Manual Figure 1 Nameplate Data Model Designation U FP5/GP5 Figure 2 Model Designation Revision: 1 (9/98) 2 Saftronics, Inc.
11 Chapter 1: Receiving Specification Designation For special specifications, a spec sheet number appears on the nameplate. 1.2 Identifying the Parts Figure 3 Specification Designation Figure 4 Configuration of FP5/GP5 Revision: 1 (9/98) 3 Saftronics, Inc.
12 Chapter 1: Receiving NOTES: Revision: 1 (9/98) 4 Saftronics, Inc.
13 2 Installation This chapter describes configuration, location and clearances when mounting the FP5/GP Removing and Replacing the Digital Operator Removing the Digital Operator Replacing the Digital Operator Removing and Replacing the Front Cover Choosing a Location to Mount the Inverter Clearances… 8
14 Chapter 2: Installation CAUTION When moving the unit, lift the cabinet by the base, never lift by the front cover. Otherwise, the main unit may be dropped causing damage to the unit. Mount the Inverter on nonflammable material, (i.e., metal). Failure to observe this can result in a fire. When mounting units in an enclosure, install a fan or other cooling device to keep the intake air temperature below 45 C. Overheating may cause a fire or damage to the unit. 2.1 Removing and Replacing the Digital Operator Remove and replace the Digital Operator as follows: Removing the Digital Operator To remove the Digital Operator from the front cover, push the Digital Operator lever in the direction shown by arrow 1 and lift the Digital Operator in the direction shown by arrow Replacing the Digital Operator Figure 5 Removing the Digital Operator Engage the Digital Operator on claws A in the direction shown by arrow 1 and then on claws B in the direction shown by arrow 2 to lock the Digital Operator. Figure 6 Replacing the Digital Operator NOTE: Never fit the Digital Operator in any other direction or by any other method. The Digital Operator will not be connected to the Inverter. Revision: 1 (9/98) 6 Saftronics, Inc.
15 Chapter 2: Installation 2.2 Removing and Replacing the Front Cover To remove the front cover, first move the Digital Operator in the direction shown by arrow 1. (Figure 5). Then squeeze the cover in the direction shown by arrows 2 on both sides and lift in the direction shown by arrow 3. Figure 7 Removing and Replacing the Front Cover NOTE: Do not replace the front cover with the Digital Operator connected. The Digital Operator will not be connected to the Inverter. Replace the front cover first and then install the Digital Operator on the cover. See Figure 6 for replacing the Digital Operator. 2.3 Choosing a Location to Mount the Inverter To ensure proper performance and long operating life, follow the recommendations below when choosing a location for installing the FP5/GP5. Make sure the Inverter is protected from the following conditions: Extreme cold and heat. Use only within ambient temperature range: 10 C to + 40 C. Rain, moisture. (For enclosed wall-mounted type.) Oil sprays, splashes. Salt spray. Direct sunlight. (Avoid using outdoors.) Corrosive gases or liquids. Dust or metallic particles in the air. (For enclosed wall-mounted type.) Physical shock, vibration. Magnetic noise. (Example: welding machines, power devices, etc.) High humidity. Radioactive materials. Combustibles: thinners, solvents, etc. Revision: 1 (9/98) 7 Saftronics, Inc.
16 Chapter 2: Installation 2.4 Clearances Install the FP5/GP5 vertically and allow sufficient clearances for effective cooling as shown below. Figure 8 Clearances NOTE: 1. The clearances required at the top and bottom and both sides are common in open chassis type (IP00) and enclosed wall-mounted type (NEMA1/IP20). 2. Remove the top and bottom covers to use the open chassis type of 200V/400V 15kW or less. 3. When installing the models of 200V/400V 30kW or more equipped with eyebolts, extra spacing will be required on either side. For detailed dimensions, contact your Saftronics representative. 4. For the external dimensions and mounting dimensions, refer to Chapter 10 Dimensions. 5. Allowable intake air temperature to the Inverter: Open chassis type (IP00) : – 10 C to 45 C Enclosed wall-mounted type : – 10 C to 40 C (NEMA 1/IP20) 6. Ensure sufficient space for the sections at the upper and lower parts marked with in order to permit the flow of intake/exhaust air to/from the Inverter. Revision: 1 (9/98) 8 Saftronics, Inc.
17 This chapter describes the main circuit wiring and the control circuit wiring of the FP5/GP5. 3 Wiring 3.1 Connection Diagram Wiring the Main Circuit Wiring Precautions for Main Circuit Input Wiring Precautions for Main Circuit Output Grounding Functions of Main Circuit Terminals Main Circuit Configuration Parts Required for Wiring Wiring the Control Circuit Functions of Control Circuit Terminals Wiring the Control Circuit Terminals Precautions on Control Circuit Wiring Wiring Inspection… 22
18 Chapter 3: Wiring WARNING Only commence wiring after verifying that the power supply is turned OFF. Failure to observe this can result in an electrical shock or fire. Wiring should be performed only by qualified personnel. Failure to observe this can result in an electrical shock or fire. When wiring the emergency stop circuit, check the wiring thoroughly before operation. Failure to observe this can result in personal injury. CAUTION Verify that the Inverter rated voltage coincides with the AC power supply voltage. Failure to observe this can result in personal injury or fire. Do not perform a withstand voltage test of the Inverter. It may cause semi-conductor elements to be damaged. To connect a Braking Resistor, Braking Resistor Unit or Braking Unit, follow the procedures described in Chapter 11. Improper connection may cause fire. Tighten terminal screws to the specified tightening torque. Failure to observe this can result in a fire. 3.1 Connection Diagram Below is a connection diagram of the main circuit and control circuit. Using the Digital Operator, the motor can be operated by wiring the main circuit only. FP5/GP5 Figure 9 FP5/GP5 Connection Diagram Revision: 1 (9/98) 10 Saftronics, Inc.
19 Chapter 3: Wiring NOTE: 1. indicates shielded wires and P indicates twisted-pair shielded wires. 2. Voltage or current input for the master frequency reference can be selected by constant n042. Voltage reference input is preset at the factory (FV). 3. Control circuit Terminal FS of + 15V has a maximum output current capacity of 20 ma. 4. Multi-function analog output should be used for monitoring meters (e.g., output frequency meter) and should not be used for feedback control system. 3.2 Wiring the Main Circuit WARNING Make sure to ground the ground terminal ( ). (Ground resistance 200V class: 100Ω or less, 400V class: 10 or less.) Failure to observe this can result in an electrical shock or a fire. CAUTION Never connect the AC main circuit power supply to output Terminals T1, T2, and T3 (U, V and W). The Inverter will be damaged and invalidate the warranty Wiring Precautions for Main Circuit Input Installation of Molded Case Circuit Breaker (MCCB) Make sure to connect Molded Case Circuit Breakers (MCCB) or fuses between AC main circuit power supply and FP5/GP5 input Terminals L1, L2 and L3 (R, S, and T) to protect wiring. Installation of Ground Fault Interrupter When connecting a ground fault interrupter to input Terminals L1, L2 and L3 (R, S, and T), select one that is not affected by high frequency. Examples: NV series by Mitsubishi Electric Co., Ltd. (manufactured in or after 1988), EG, SG series by Fuji Electric Co., Ltd. (manufactured in or after 1984). Installation of Magnetic Contactor Inverters can be used without a Magnetic Contactor (MC) installed at the power supply side. When the main circuit power supply is shut OFF in the sequence, a MC can be used instead of a MCCB. However, when a MC is switched OFF at the primary side, regenerative braking does not function and the motor coasts to a stop. The load can be operated/stopped by opening/closing the MC at the primary side. However, frequent switching may cause the Inverter to malfunction. When using a Braking Resistor Unit, use a sequencer to break power supply side on overload relay trip contact. If the Inverter malfunctions, the Braking Resistor Unit may be damaged. Terminal Block Connection Sequence Input power supply phases can be connected to any terminal regardless of the order of L1, L2 and L3 (R, S, and T) on the terminal block. Installation of AC Reactor When connecting an Inverter (200V/400V 15kW or less) to a large capacity power supply transformer (600k VA or more), or when switching a phase advancing capacitor, excessive peak current flows in the input power supply circuit, which may damage the converter section. In such cases, install a DC Reactor (optional) between Inverter ¾ 1 and ¾ 2 terminals or an AC Reactor (optional) on the input side. Installation of a reactor is effective for improvement of power factor on the power supply side. Revision: 1 (9/98) 11 Saftronics, Inc.
20 Chapter 3: Wiring Installation of Surge Suppressor For inductive loads (magnetic contactors, magnetic relays, magnetic valves, solenoids, magnetic brakes, etc.) connected near the Inverter, use a surge suppressor simultaneously. Prohibition of Installation of Phase Advancing Capacitor If a Phase Advancing Capacitor or Surge Suppressor is connected in order to improve the power factor, it may become overheated and damaged by Inverter high harmonic components. Also, the Inverter may malfunction because of overcurrent Wiring Precautions for Main Circuit Output Connection of Terminal Block and Load Connect output Terminals T1, T2, and T3 (U, V, and W) to motor lead wires T1, T2, and T3 (U, V, and W). Verify that the motor rotates in the forward direction (CCW: counterclockwise when viewed from the motor load side) with the forward RUN command. If the motor rotation is incorrect, exchange any two of output Terminals T1, T2, and T3 (U, V, and W). Strict Prohibition of Connection of Input Power Supply to Output Terminals Never connect the input power supply to output Terminals T1, T2, and T3 (U, V, and W). Strict Prohibition of Short Circuiting or Grounding of Output Circuit Never touch the output circuit directly or put the output line in contact with the Inverter case. Otherwise, it may cause an electrical shock or grounding. In addition, never short-circuit the output line. Prohibition of Connection of Phase Advancing Capacitor or LC/RC Noise Filter Never connect a Phase Advancing Capacitor or LC/RC noise filter to the output circuit. Avoidance of Installation of Magnetic Starter Do not connect a Magnetic Starter or MC to the output circuit. If the load is connected while the Inverter is running, the Inverter overcurrent protective circuit operates because of inrush current. Installation of Thermal Overload Relay An electronic overload protective function is incorporated into the Inverter. However, connect a Thermal Overload Relay when driving several motors with one Inverter or when using a multi-pole motor. When using a Thermal Overload Relay, set Inverter constant n033 to 0 (motor overload protection selection: no protection). Additionally, for Thermal Overload Relay at 50Hz, set the same rated current value as that described on the motor nameplate, or at 60Hz 1.1 times larger than the rated current value described on the motor nameplate. Wiring Distance between Inverter and Motor If the total wiring distance between Inverter and motor is excessively long and the Inverter carrier frequency (main transistor switching frequency) is high, harmonic leakage current from the cable will adversely affect the Inverter and peripheral devices. If the wiring distance between Inverter and motor is long, reduce the Inverter carrier frequency as described below. Carrier frequency can be set by constant n050. Table 2 Wiring Distance between Inverter and Motor Wiring Distance between Inverter and Motor Up to 164ft (50m) Up to 328ft (100m) More than 328ft (100m) Carrier Frequency (Set value of constant n050) 15kHz or less (6) 10kHz or less (4) 5kHz or less (2) Grounding Ground resistance 200 V class: 100 Ω or less, 400 V class: 10 Ω or less Never ground the Inverter in common with welding machines, motors, or other large-current electrical equipment. Run all the ground wires in a conduit separate from wires for large-current electrical equipment. Revision: 1 (9/98) 12 Saftronics, Inc.
21 Chapter 3: Wiring Use the ground wires described in Tables 5 or 6 and keep the length as short as possible. When using several Inverter units side by side, ground the units as shown in Figure 10, (a) or (b). Do not loop the ground wires as shown in (c) Functions of Main Circuit Terminals Figure 10 Grounding of Three Inverter Units The following table outlines the functions of the main circuit terminals. Wire according to each terminal function. Table V Class Terminal Functions Models FP5/GP5 Max Applicable Motor Output L1 (R) L2 (S) L3 (T) L11 (R1) L21 (S1) L31 (T1) T1 (U) T2 (V) T3 (W) B1 B2 23P7 to 27P to to to 7.5 kw 11 to 15 kw 18.5 to 75 kw Braking Resistor Unit Main circuit input power supply Inverter output Main circuit input power supply Ö ¾ 1 ¾ 2 ¾ 3 DC Reactor (¾1 ¾2) DC Reactor (¾1 ¾2) DC bus terminals (¾1 ¾2 DC bus terminals (¾1 ¾2 Braking Unit (¾3 Ö) Ground terminal (Ground resistance: 100 Ω or less) Revision: 1 (9/98) 13 Saftronics, Inc.
22 Chapter 3: Wiring Table V Class Terminal Functions Models FP5/GP5 40P4 to to to to 4300 Max Applicable Motor Output L1 (R) L2 (S) L3 (T) L11 (R1) L21 (S1) L31 (T1) T1 (U) T2 (V) T3 (W) B1 B2 Ö ¾ 1 ¾ 2 ¾ 3 r (l 1) s 200 (l 2 200) s 400 (l 2 400) 0.4 to 15 kw 18.5 to 45 kw 55 to 160 kw 185 to 300 kw Main circuit input power supply Braking Resistor Unit DC Reactor (¾1 ¾2 DC bus terminals (¾1 Ö) Main circuit input power supply Inverter output Main circuit input power supply Braking Unit (¾ 3 Ö) Braking Unit (¾ 3 Ö) Cooling fan power supply (Control power supply r (l 1) s 200 (l 2 200): 200 to 230 VAC input r (l 1) s 400 (l 2 400): 380 to 460 VAC input Ground terminal (Ground resistance: 10Ω or less) Revision: 1 (9/98) 14 Saftronics, Inc.
23 Chapter 3: Wiring Main Circuit Configuration 200V Class FP5/GP523P7 to FP5/GP527P5 FP5/GP52011 to FP5/GP52015 FP5/GP52018 to FP5/GP52022 FP5/GP52030 to FP5/GP52075 The wiring has been completed at the factory prior to shipping. When installing a DC Reactor (option) on models of 15kW or below, remove the short-circuit bar between ¾ 1 and ¾2 terminals and connect a DC Reactor with the terminals. Revision: 1 (9/98) 15 Saftronics, Inc.
24 Chapter 3: Wiring 400V Class FP5/GP540P4 to FP5/GP541P5 FP5/GP542P2 to FP5/GP54015 FP5/GP54018 to FP5/GP54045 FP5/GP54055 to FP5/GP54160 FP5/GP54185 to FP5/GP54300 The wiring has been completed at the factory prior to shipping. When installing a DC Reactor (option) on models of 15kW or below, remove the short-circuit bar between ¾ 1 and ¾ 2 terminals and connect a DC Reactor with the terminals. Revision: 1 (9/98) 16 Saftronics, Inc.
25 Chapter 3: Wiring Parts Required for Wiring Select wires or Closed-Loop Connectors to be used for wiring from Tables 5, 6 and 7. Table V Class Wire Size Circuit Model FP5/GP5 Terminal Symbol Terminal Wire Size Wire Type Screw AWG mm 2 L1, L2, L3, (R, S, T) Ö, ¾ 1, ¾ 2, B1, B2, T1, T2, T3 23P7 (U, V, W) M P5 L1, L2, L3, (R, S, T) Ö, ¾ 1, ¾ 2, B1, B2, T1, T2, T3 (U, V, W) M P5 L1, L2, L3, (R, S, T) Ö, ¾ 1, ¾ 2, B1, B2, T1, T2, T3 (U, V, W) M L1, L2, L3, (R, S, T) Ö, ¾ 1, ¾ 2, ¾ 3, T1, T2, T3 (U, 2011 V, W) M Main Control 2015 L1, L2, L3, (R, S, T) Ö, ¾ 1, ¾ 2, ¾ 3, T1, T2, T3 (U, V, W) L1,L2, L3, (R, S, T) L11, L21, L31, (R1, S1, T1), T1, 2018 T2, (U, V, W) M8 L1,L2, L3, (R, S, T), L11, L21, L31, (R1, S1, T1), T1, 2022 T2, T3 (U, V, W) M Common to all models L1,L2, L3, (R, S, T), L11, L21, L31, T1, T2, T3, (U, V, W) L1,L2, L3, (R, S, T), L11, L21, L31, T1, T2, T3, (U, V, W) L1,L2, L3, (R, S, T), L11, L21, L31, T1, T2, T3, (U, V, W) L1,L2, L3, (R, S, T), L11, L21, L31, T1, T2, T3, (U, V, W) L1,L2, L3, (R, S, T), L11, L21, L31, T1, T2, T3, (U, V, W) S1, S2, S3, S4, S5, S6, SC, FV, FI, FS, FC, AM, AC, M1, M2, MA, MB, MC M M M10 4/0 100 M M10 1/0 x 2P 60 2P M M10 1/0 x 2P 60 2P M M10 1/0 x 2P 60 2P M M12 4/0 x 2P 100 2P M Stranded Solid G M Power cable: 600V vinyl sheathed wire or equivalent Twisted shielded wire Where size is determined using 75 C temperature-rated copper wire. Revision: 1 (9/98) 17 Saftronics, Inc.
26 Chapter 3: Wiring Table V Class Wire Size Circuit Model FP5/GP5 Terminal Symbol Terminal Wire Size Wire Type Screw AWG mm 2 L1, L2, L3, (R, S, T), Ö, ¾ 1, ¾ 2, B1, B2, T1, T2, T3 40P4 (U, V, W) M L1, L2, L3 (R, S, T), Ö, ¾ 1, ¾ 2, B1, B2, T1, T2, T3 40P7 (U, V, W) M L1, L2, L3, (R, S, T), Ö, ¾ 1, ¾ 2, B1, B2, T1, T2, T3 41P5 (U, V, W) M L1, L2, L3 (R, S, T), Ö, ¾ 1, ¾ 2, B1, B2, T1, T2, T3 42P2 (U, V, W) M P7 L1, L2, L3 (R, S, T), Ö, ¾ 1, ¾ 2, B1, B2, T1, T2, T3 (U, V, W) M Main L1, L2, L3 (R, S, T), Ö, ¾ 1, ¾ 2, B1, B2, T1, T2, T3 44P0 (U, V, W) M L1, L2, L3 (R, S, T), Ö, ¾ 1, ¾ 2, B1, B2, T1, T2, T3 45P5 (U, V, W) M Power cable: 600V vinyl sheathed wire or equivalent L1, L2, L3 (R, S, T), Ö, ¾ 1, ¾ 2, B1, B2, T1, T2, T3 47P5 (U, V, W) M L1, L2, L3, (R, S, T), Ö, ¾ 1, ¾ 2, B1, B2, T1, T2, T3 (U, V, W) M M L1, L2, L3 (R, S, T), Ö, ¾ 1, ¾ 2, B1, B2, T1, T2, T3 (U, V, W) L1, L2, L3 (R, S, T), L11, L21, L31 (R1, S1, T11), T1, T2, T3 (U, V, W) L1, L2, L3 (R, S, T), L11, L21, L31 (R1, S1, T11), T1, T2, T3 (U, V, W) L1, L2, L3 (R, S, T), L11, L21, L31 (R1, S1, T11), T1, 4030 T2, T3 (U, V, W) M8 M M6 8 8 M M8 8 8 M M Where size is determined using 75 C temperature-rated copper wire. Revision: 1 (9/98) 18 Saftronics, Inc.
27 Chapter 3: Wiring Table V Class Wire Size (Continued) Circuit Main Model FP5/GP5 Terminal Symbol L1, L2, L3 (R, S, T), L11, L21, L31 (R1, S1, T11), T1, 4037 T2, T3 (U, V, W) M8 L1, L2, L3 (R, S, T), L11, L21, L31 (R1, S1, T11), T1, 4045 T2, T3 (U, V, W) M L1, L2, L3 (R, S, T), L11, L21, L31 (R1, S1, T11), T1, T2, T3 (U, V, W) L1, L2, L3 (R, S, T), L11, L21, L31 (R1, S1, T11), T1, T2, T3 (U, V, W) L1, L2, L3 (R, S, T), L11, L21, L31 (R1, S1, T11), T1, T2, T3 (U, V, W) L1, L2, L3 (R, S, T), L11, L21, L31 (R1, S1, T11), T1, T2, T3 (U, V, W) L1, L2, L3 (R, S, T), Ö, ¾ 1, ¾ 3, T1, T2, T3 (U, V, W) Terminal Wire Size Wire Type Screw AWG mm M10 4/0 100 M M10 1/0 x 2P 60 x 2P M M10 1/0 x 2P 60 x 2P M M12 4/0 x 2P 100 x 2P M M16 650MCM x 2P 325 x 2P M r (l 1), s 200 (l 2 200), s 400 (l 2 400) M L1, L2, L3 (R, S, T), Ö, ¾ 1, ¾ 3, T1, T2, T3 (U, V, W) M16 650MCM x 2P 325 x 2P M8 1/0 60 Power cable: 600V vinyl sheathed wire or equivalent 4300 r (l 1), s 200 (l 2 200), s 400 (l 2 400) M L1, L2, L3 (R, S, T), Ö, ¾ 1, ¾ 3, T1, T2, T3 (U, V, W) M16 650MCM x 2P 325 x 2P M8 1/0 60 Control Common to all models r (l 1), s 200 (l 2 200), s 400 (l 2 400) M S1, S2, S3, S4, S5, S6, SC, FV, FI, FS, FC, AM, AC, M1, M2, MA, MB, MC Stranded Solid G M Twisted shielded wire Where size is determined using 75 C temperature-rated copper wire. Revision: 1 (9/98) 19 Saftronics, Inc.
28 Chapter 3: Wiring NOTE: Table 7 Closed-Loop Connectors AWG Size Wire Size mm 2 Terminal Screw Closed-Loop Connectors M M M M M M M M M5 2 5 M6 2 6 M8 2 8 M / 5.5 M M M M M6 8 6 M M M M M / 38 M /0 50 / 60 M M / M10 4/ / MCM 150 M MCM MCM 325 M12 x M When determining wire size, consider voltage drop. Select a wire size so that voltage drop will be less than 2% of the normal rated voltage. Voltage drop is calculated by the following equation: Phase-to-phase voltage drop (V) = /3 wire resistance (Ω/km) wiring distance (m) current (A) 10 3 Revision: 1 (9/98) 20 Saftronics, Inc.
29 Chapter 3: Wiring 3.3 Wiring the Control Circuit The following table outlines the functions of the control circuit terminals. Wire according to each terminal function Functions of Control Circuit Terminals Table 8 Control Circuit Terminals Classification Terminal Signal Function Description Signal Level S1 Forward run/stop Forward run when closed, stop when open Sequence Input Signal S2 S3 Reverse run/stop External fault input Reverse run when closed, stop when open Fault when closed, normal state when open S4 Fault reset input Reset when closed S5 Multi-step speed reference 1 Effective when closed S6 Multi-step speed reference 2 Effective when closed Multi-function contact inputs (n035 to n039) Photo-coupler insulation Input: + 24 VDC 8 ma Analog Input Signal SC FS FV FI FC G Sequence control input common terminal + 15 V Power supply output Frequency reference input (voltage) Frequency reference input (current) Common terminal for control circuit Connection to shield sheath of signal lead For analog command + 15 V power supply + 15 V (Allowable current 20 ma maximum) 0 to + 10 V/100% n042 = 0 : FV effective 0 to + 10 V (20 kω) 4 to 20 ma/100% n042 = 1 : FI effective 4 to 20mA (250Ω) 0 V Sequence Output Signal M1 M2 MA MB MC During running (NO contact) Fault contact output (NO/NC contact) Closed when running Fault when closed between Terminals MA and MC. Fault when open between Terminals MB and MC. Multi-function contact output (n041) Multi-function contact output (n040) Dry contact Contact capacity: 250 VAC 1 A or less 30 VDC 1 A or less Dry contact Contact capacity: 250 VAC 1 A or less 30 VDC 1 A or less Analog Output Signal AM AC Frequency meter output Common 0 to + 10 V/100% frequency Multi-function analog monitor 1 (n048) 0 to + 10 V 2 ma or less G S1 S2 S3 SC SC S4 S5 S6 FV FI FS FC AM AC M1 M2 MA MB MC Figure 11 Control Circuit Terminal Arrangement Revision: 1 (9/98) 21 Saftronics, Inc.
30 Chapter 3: Wiring Wiring the Control Circuit Terminals Insert the wire into the lower part of the terminal block and connect it tightly with a screwdriver. Wire sheath strip length must be 7 mm (approximately ¼ inch) Precautions on Control Circuit Wiring Separate control circuit wires from main circuit wires and other power cables to prevent erroneous operation caused by noise interference. Use twisted shielded or twisted-pair shielded wire for the control circuit line and connect the shielded sheath to the Inverter Terminal G. See Figure Wiring Inspection Figure 12 Shielded Wire Termination After completing installation and wiring, check for the following items. Never use control circuit megger check. Wiring is proper. Wire clippings or screws are not left in the unit. Screws are securely tightened. Bare wire in the terminal does not contact other terminals. Revision: 1 (9/98) 22 Saftronics, Inc.
31 This chapter describes the basic operation procedures of the FP5/GP5. 4 Operation 4.1 Operation Mode Selection Test Run Checkpoints Setting the Line Voltage Using Jumper (For 400V Class 18.5kW and Above) Test Run Digital Operator Display at Power-Up Operation Check Points… 2/ Example of Basic Operation… 28
32 Chapter 4: Operation WARNING Only turn ON the input power supply after replacing the front cover. Do not remove the cover while current is flowing. Failure to observe this can result in an electrical shock. When the retry function (n057) is selected, do not approach the Inverter or the load, since it may restart suddenly after being stopped. (Construct machine system, so as to assure safety for personnel, even if the Inverter should restart.) Failure to observe this can result in personal injury. Since the stop button can be disabled by a function setting, install a separate emergency stop switch. Failure to observe this can result in personal injury. CAUTION Never touch the heatsink or discharging resistor since the temperature is very high. Failure to observe this can result in harmful burns to the body. Since it is easy to change operation speed from low to high speed, verify the safe working range of the motor and machine before operation. Failure to observe this can result in personal injury and machine damage. Install a holding brake separately if necessary. Failure to observe this caution can result in personal injury. Do not change signals during operation. The machine or the Inverter may be damaged. All the constants of the Inverter have been preset at the factory. Do not change the settings unnecessarily. The Inverter may be damaged. For supply voltage, follow Paragraph 4.3 of Chapter 4. Revision: 1 (9/98) 24 Saftronics, Inc.
33 Chapter 4: Operation 4.1 Operation Mode Selection The FP5/GP5 has two operation modes, LOCAL and REMOTE, as described in Table 9. These two modes can be selected by the Digital Operator LOCAL/REMOTE key only while the operation is stopped. The selected Operation mode can be verified by observing the Digital Operator SEQ and REF LED s as shown below. The Operation mode is set to REMOTE (run by control circuit Terminals FV and FI frequency reference and RUN command from a control circuit terminal) prior to shipment. Multifunction contact inputs from control circuit Terminals S3 to S6 are enabled in both Operation modes LOCAL/REMOTE. LOCAL : Both frequency reference and RUN command are set by the Digital Operator. SEQ and REF LED s go OFF. REMOTE : Master frequency reference and RUN command can be selected as described in Table 9. Table 9 Reference Selection in REMOTE Mode (n002: Operation Method Selection) Setting Operation Method Selection SEQ LED Reference Selection REF LED 0 Operation by RUN command from Digital Operator OFF Master frequency reference from Digital Operator OFF 1 Operation by RUN command from control circuit terminal 2 Operation by RUN command from Digital Operator OFF 3 Operation by RUN command from control circuit terminal ON Master frequency reference from Digital Operator OFF ON 4 Operation by RUN command from Digital Operator OFF Operation by RUN command from control circuit terminal Operation by RUN command from serial communication Operation by RUN command from serial communication Operation by RUN command from serial communication ON ON Master frequency reference from control circuit Terminals FV and FI Master frequency reference from control circuit Terminals FV and FI Master frequency reference set by serial communication Master frequency reference set by serial communication Master frequency reference set by serial communication ON Master frequency reference from Digital Operator OFF ON Master frequency reference from control circuit Terminals FV and FI ON ON ON ON ON ON Revision: 1 (9/98) 25 Saftronics, Inc.
34 Chapter 4: Operation 4.2 Test Run Checkpoints To assure safety, prior to initial operation, disconnect the machine coupling so that the motor is isolated from the machine. If initial operation must be performed while the motor is still coupled to the machine, use great care to avoid potentially hazardous conditions. Check the following items before a test run. Wiring and terminal connections are correct. No short-circuit caused by wire clippings. Screw-type terminals are securely tightened. Motor is securely mounted All items are correctly earthed (grounded). 4.3 Setting the Line Voltage Using Jumper (For 400V Class 18.5kW and Above) Set the line voltage jumper according to the main circuit power supply. (See Figure 13.) Insert the jumper at the appropriate location corresponding to the input line voltage. It has been preset at the factory to 440V. Figure 13 Line Voltage Jumper (For 400V Class 18.5kW to 45kW) Revision: 1 (9/98) 26 Saftronics, Inc.
35 Chapter 4: Operation 4.4 Test Run Digital Operator Display at Power-up When the system is ready for operation, turn ON the power supply. Verify that the Inverter powers up properly. If any problems are found, turn OFF the power supply immediately. The Digital Operator display illuminates as shown below when turning the power supply ON. Figure 14 Digital Operator Display at Power-Up Revision: 1 (9/98) 27 Saftronics, Inc.
36 Chapter 4: Operation Operation Check Points Check the following items during operation. Motor rotates smoothly. Motor rotates in the correct direction. Motor does not have abnormal vibration or noise. Acceleration and deceleration are smooth. Current matches the load flow. Status indicator LED s and Digital Operator display are correct Example of Basic Operation. Operation by Digital Operator The diagram below shows a typical operation pattern using the Digital Operator. Figure 15 Operation Sequence by Digital Operator Table 10 Typical Operation by Digital Operator 1 Description Key Sequence Digital Operator Display LED Display Power ON Fref Display frequency reference value. 0.0 Operation Condition Setting Select LOCAL mode. REMOTE LED (SEQ. REF) OFF \ / 2 Frequency Setting Change the value Change reference value. by pressing 15.0 Fref / \ Write-in set value Fref Select output frequency monitor display. 0.0 Fout 3 Forward Run Forward run (15 Hz) 15.0 Fout RUN LED ON Revision: 1 (9/98) 28 Saftronics, Inc.
37 Chapter 4: Operation 4 Frequency Reference Value Change (15 Hz to 60 Hz) Select frequency reference value display. Table 10 Typical Operation by Digital Operator (continued) Press 7 times 15.0 Fref Change set value. Change the value by pressing \ / 60.0 Fref / \ Write-in set value Fref Select output frequency monitor display Fref 5 Reverse Run Select reverse run. Press 3 times fo F/R Switch to rev \ / by pressing eu / \ F/R Write-in set value. eu F/R Select output frequency monitor display. Press 5 times 60.0 Fout 6 Stop Decelerates to a stop. 0.0 Fout RUN LED OFF STOP LED ON Operation by Control Circuit Terminal Signal The diagram below shows a typical operation pattern using the control circuit terminal signals. Figure 16 Operation Sequence by Control Circuit Terminal Signal Revision: 1 (9/98) 29 Saftronics, Inc.
38 Chapter 4: Operation Table 11 Typical Operation by Control Circuit Terminal Signal 1 Description Key Sequence Digital Operator Display LED Display Power ON Fref Display frequency reference value. 0.0 REMOTE mode is preset at the factory REMOTE LED (SEQ, REF) ON 2 Frequency Setting Input frequency reference voltage 60.0 Fref (current) by control circuit Terminal FV or FI and verify the input value by the Digital Operator. Output Frequency Display For reference voltage 10V Select output frequency monitor display. 0.0 Fout 3 Forward Run Fout Close between control circuit Terminals 60.0 SI and SC to perform forward run. RUN LED ON 4 Stop Open between control circuit Terminals SI and SC to stop operation. 0.0 Fout STOP LED ON (RUN LED blinking during deceleration) Revision: 1 (9/98) 30 Saftronics, Inc.
39 This chapter describes simple data setting. 5 Simple Data Setting 5.1 Digital Operator Key Description LED Description… 32
40 Chapter 5: Simple Data Setting 5.1 Digital Operator Key Description Mode Indicator LED s (Remote Mode) Lights when selecting Input mode from the control circuit terminal or serial communication. SEQ: Lights when selecting RUN command from control circuit terminal or serial communication. REF: Lights when selecting frequency reference from control circuit Terminals FV and FI or serial communication. Display Displays set values of each function or monitoring values such as frequency and output current. (4 Digits) Quick-Start LED s LED Description Set/Read During Run Fref Frequency reference setting/monitoring Enable Fout Output frequency monitor Enable Iout Output current monitor Enable kwout Output power monitor Enable F/R FWD/REV RUN command selection Enable Montr Monitor selection Enable Accel Acceleration time Enable Decel Deceleration time Enable Vmtr Motor rated voltage Disable V/F V/f pattern selection Disable Fgain Frequency reference gain Disable Fbias Frequency reference bias Disable FLA Motor rated current Disable PID PID selection Disable kwsav Energy Saving selection Disable PRGM Constant number/data Disable Enter Key Displays each constant set value. By pressing this key again, the set value is written in. Number Change Keys Changes set values or constant numbers. : Increment key : Decrement key Operation Command Keys Operation command keys operate the Inverter. *STOP/RESET : Red LED lights by pressing STOP. (Resets operation at faults. Reset is disabled while a RUN command is ON.) RUN : Red LED lights by pressing RUN. Operation Mode Selection Key The Operation mode is alternated between REMOTE and LOCAL (Digital Operator). Display Selection Key Selects the contents of Quick-Start LED s. (See Page 33) 5.2 LED Description Figure 17 Digital Operator Key Description By using the Quick-Start LED s on the Digital Operator, simple operation of the Inverter is possible. Each Quick-Start LED is selected each time DSPL key is pressed. Following is a table describing Quick-Start LED selection. (Example of model FP5/GP5) Revision: 1 (9/98) 32 Saftronics, Inc.
41 Chapter 5: Simple Data Setting Table 12 LED Description LED Display Description Key Sequence Digital Operator Display Remarks Power ON Fref Frequency reference setting/monitoring 0.0 Fout Output frequency monitor 0.0 Iout Output current monitor 0.0 kwout Output power monitor 0.0 Press ENTER key to display the monitor value. F/R FWD/REV RUN command selection Fo Montr Monitor selection U 01 Accel Acceleration time 10.0 Decel Deceleration time 10.0 (During run) Vmtr Motor rated voltage V/F V/f pattern selection 1 Fgain Frequency reference gain 100 Fbias Frequency reference bias 0 Set/read is enabled only during stop. FLA Motor rated current 14.0 PID PID selection 0 kwsav Energy saving selection 0 PRGM Constant number/data 002 Press ENTER key to display the data. Revision: 1 (9/98) 33 Saftronics, Inc.
42 Chapter 5: Simple Data Setting NOTES: Revision: 1 (9/98) 34 Saftronics, Inc.
43 This chapter describes programming features. 6 Programming Features 6.1 Constant Set-Up and Initialization Constant Selection/Initialization (n001) V/f Pattern Setting Preset V/f Pattern Custom V/f Pattern Setting Operation Conditions Reverse Run Prohibit (n006) Multi-Step Speed Selection Operation at Low Speed Adjusting Frequency Setting Signal Adjusting Frequency Upper and Lower Limits Using Two Accel/Decel Times Automatic Restart after Momentary Power Loss (n051) Soft-Start Characteristics (n023) Torque Detection Frequency Detection (n073) Jump Frequencies (n058 to n060) Continuing Operation by Automatic Fault Reset (n056) Operating Coasting Motor without Trip Using Frequency Meter of Ammeter (n048) Calibrating Frequency Meter of Ammeter (n049) Reducing Motor Noise or Leakage Current (n050) Selecting Stopping Method Selecting Stopping Method (n004) Coast to Stop with Timer 1 (n004=2) Applying DC Injection Braking Current (n064) Building Interface Circuits with External Devices Using Sequence Input Signals (n035 to n039) Using Analog Input Signals (n042 to n045) Using Output Signals (n040, n041) Setting Operation Conditions Torque Compensation Gain (n067) Motor Protection Motor Overload Detection PID Control Intended Value Setting Detected Value Setting Energy Saving Control Energy Saving Gain K2 (n096) Energy Saving Tuning MEMOBUS Control Communication Specifications Data to be Sent/Received by Communication… 60
44 Chapter 6: Programming Features 6.1 Constant Set-up and Initialization Constant Selection/Initialization (n001) The following table describes the data which can be set or read when n001 is selected. Setting Constant that can be set Constant that can be read 0 (Constant write disable) n001 n001 to n108 1 (Factory setting) n001 to n034 n001 to n108 2 n001 to n049 n001 to n108 3 n001 to n108 n001 to n108 4, 5 Not used (disabled) 8 Initialize: 2-wire sequence 9 Initialize: 3-wire sequence Refer to Page V/f Pattern Setting V/f pattern can be set by constant n010. Set value 0 to E: F : Preset V/f pattern can be selected. Custom V/f pattern can be set. Revision: 1 (9/98) 36 Saftronics, Inc.
45 Chapter 6: Programming Features Preset V/f Pattern The following shows the preset V/f patterns. (The voltages are for 200V class. For 400V class, the value is twice that of 200V class.) Table 13 Preset V/f Pattern (n010 = 0 to E) Specifications n010 V/f Pattern *1 Specifications n010 V/f Patterns *1 Low Starting Torque 8 General-Purpose 60 Hz 50 Hz 0 50 Hz 60 Hz Saturation 50 Hz Saturation 1 F 2 High Starting Torque *2 60 Hz High Starting Torque Low Starting Torque High Starting Torque 9 A B 72 Hz 3 90 Hz C Variable Torque Characteristics 50 Hz 60 Hz Variable Torque 1 Variable Torque 2 Variable Torque 3 Variable Torque High Speed Operation 120 Hz D 180 Hz E Consider the following items as the conditions for selecting a V/f pattern. They must be suitable for: The voltage and frequency characteristics of motor. The maximum rotation speed of motor. Select high starting torque only in the following conditions. Normally, this selection is not required. The wiring distance is long (150 meters (492 feet) and above). Voltage drop at startup is large. AC Reactor is inserted in the input or output of the Inverter. A motor smaller than the nominal output of the Inverter is used. Voltages when the models of 200V, 55kW or above, or 400V, 55kW or above are selected. Revision: 1 (9/98) 37 Saftronics, Inc.
▷ Saftronics FP5/GP5 Series User Manuals PDF Download
VOLTIMA VSP Series User Manual VOLTIMA PURE SINE POWER INVERTER VSP Series Pure Sine Wave Inverter … VSP Series Inverter Operation & user’s manual, 11
Wagan Proline-5000 3744 Item No. : 374 4 (12V DC Input)374 4 -4 (24V DC Input)374 4 -8 (48V DC Input)Proline 5000 ™ AC to DC InverterUser ’s ManualPlease visit our website for the latest information on this product.RoHScompliant … Proline-5000 3744 Inverter Operation & user’s manual, 20
Mitsubishi F700 Series INSTRUCTION MANUALINVERTERINVERTER FR-F700-EC INSTRUCTION MANUAL (Applied)HHEAD OFFICE: TOKYO BUILDING 2-7-3, MARUNOUCHI, CHIYODA-KU, TOKYO 100-8310, JAPANIB(NA)-0600193ENG-H (1204)MEE Printed in Japan Specifications subject to change without notice.3PRECAUTIONS FOR USEOF THE INVERTER4PARAMETERS5PROTECTIVE FUNCTIONS6PRECAUTIONS FORMAINTENANCE AND INSPECTION7SPECIFICATIONSWIRINGOUTLINE21FR-F740-000 … F700 Series Inverter Instruction manual, 408
Victron energy Venus GX 2020-11-10 03:10 1/5 Garmin MFD integrationVictron Energy – https://www.victronenergy.com/live/Garmin MFD integrationPreliminary manual1. IntroductionThe integration technology used is called Garmin OneHelm.2. CompatibilityOneHelm is currently available for the following models:GPSMAP® 8400/8600 MFD seriesGPSMAP® 722/922/1222 Plus MFD seriesAlso, Active Captain is supported. This screenshot show … Venus GX Conference System Preliminary manual, 5
키워드에 대한 정보 saftronics fp5 manual
다음은 Bing에서 saftronics fp5 manual 주제에 대한 검색 결과입니다. 필요한 경우 더 읽을 수 있습니다.
이 기사는 인터넷의 다양한 출처에서 편집되었습니다. 이 기사가 유용했기를 바랍니다. 이 기사가 유용하다고 생각되면 공유하십시오. 매우 감사합니다!
사람들이 주제에 대해 자주 검색하는 키워드 Repair Saftronics DG2 Plus DC Drive
- Industrial Electronics
- GTV
- G-TV
- Electrical
- Galco
- Galco TV
- repair
- saftronics
- DG2
- DG2 repair
- DC Drive
- DC drive repair
- drive repair
- repair services
- repair center
- DC current
- drives
- fix
Repair #Saftronics #DG2 #Plus #DC #Drive
YouTube에서 saftronics fp5 manual 주제의 다른 동영상 보기
주제에 대한 기사를 시청해 주셔서 감사합니다 Repair Saftronics DG2 Plus DC Drive | saftronics fp5 manual, 이 기사가 유용하다고 생각되면 공유하십시오, 매우 감사합니다.