당신은 주제를 찾고 있습니까 “tri roll thread gage – Tri-roll Gage: External Thread Measurements“? 다음 카테고리의 웹사이트 https://chewathai27.com/you 에서 귀하의 모든 질문에 답변해 드립니다: https://chewathai27.com/you/blog. 바로 아래에서 답을 찾을 수 있습니다. 작성자 Greenslade \u0026 Company 이(가) 작성한 기사에는 조회수 10,023회 및 좋아요 25개 개의 좋아요가 있습니다.
tri roll thread gage 주제에 대한 동영상 보기
여기에서 이 주제에 대한 비디오를 시청하십시오. 주의 깊게 살펴보고 읽고 있는 내용에 대한 피드백을 제공하세요!
d여기에서 Tri-roll Gage: External Thread Measurements – tri roll thread gage 주제에 대한 세부정보를 참조하세요
In this tutorial, Larry Borowski of Greenslade and Company demonstrates how to find external thread measurements using Greenslade’s Tri-Roll Gage.
tri roll thread gage 주제에 대한 자세한 내용은 여기를 참조하세요.
Tri-roll Thread Gage Useage Procedures 040303
Open rolls and move the part between rolls to the opposite end of the part without engaging the runnout threads. □ Rotate part slightly and observe.
Source: www.greensladeandcompany.com
Date Published: 3/10/2022
View: 7895
주제와 관련된 이미지 tri roll thread gage
주제와 관련된 더 많은 사진을 참조하십시오 Tri-roll Gage: External Thread Measurements. 댓글에서 더 많은 관련 이미지를 보거나 필요한 경우 더 많은 관련 기사를 볼 수 있습니다.
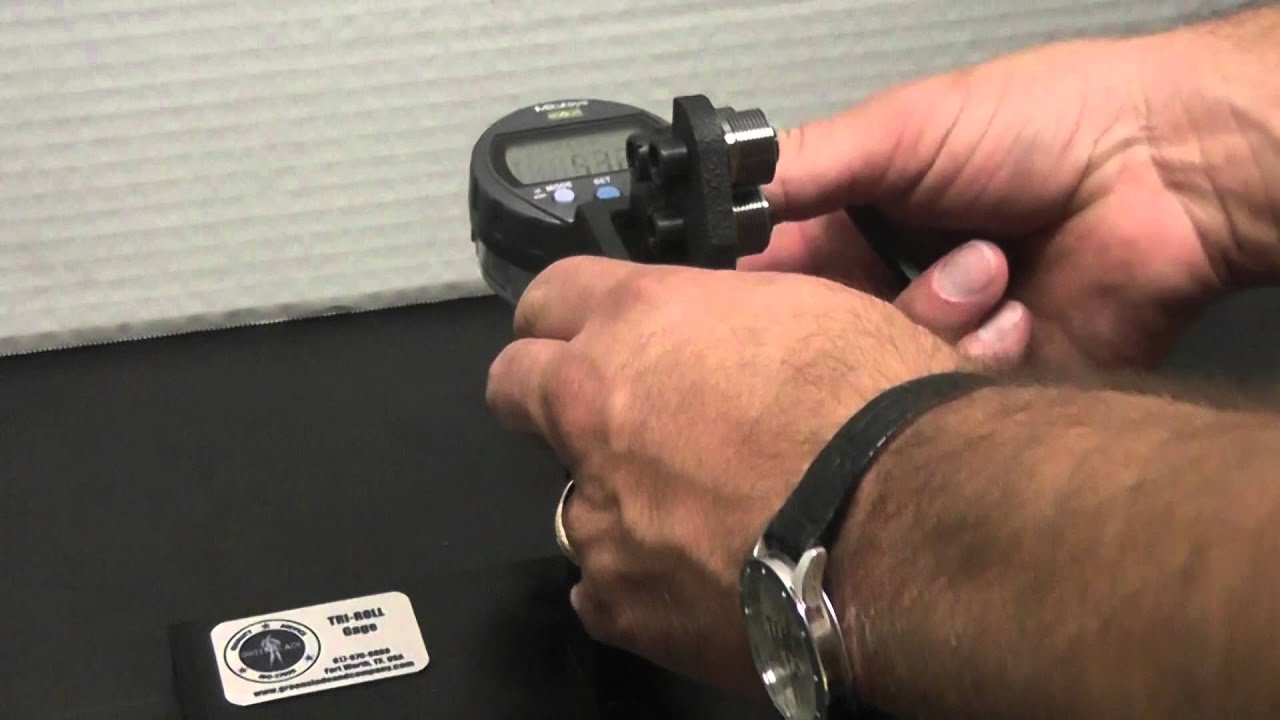
주제에 대한 기사 평가 tri roll thread gage
- Author: Greenslade \u0026 Company
- Views: 조회수 10,023회
- Likes: 좋아요 25개
- Date Published: 2013. 10. 19.
- Video Url link: https://www.youtube.com/watch?v=VbyRqUdt-GE
How do you set a tri roll?
Setting the Tri-roll System for Measuring.
Rotate the setting plug approximately 1/4 turn counterclockwise to assure that the setting plug is properly seated between the rolls. The top roll should apply firm pressure on the setting plug to press it snugly between all three rolls.
What is a tri roll?
The Tri Roll System measures the exact position of the pitch diameter within the tolerance range. It also checks size and out of roundness of plain cylindrical parts. The Tri Roll reduces gaging time over thread ring gages.
How do you inspect threads?
To inspect an internal thread, both ends of the thread plug are inserted into the threaded component. The Go end of the plug is supposed to thread in; the No-Go end is not. If this test checks out, the part can pass inspection.
What does a Johnson Gage measure?
By incorporating both Functional and Pitch Diameter Size measurements into its basic design, Johnson Gage Thread Inspection Systems not only assure assembly and dimensional conformance, but also add a measure of confidence and integrity to both the inspection process and your product.
What is a pitch diameter?
Pitch diameter, denoted by dm or d2, is the imaginary diameter for which the widths of the threads and the grooves are equal.
How do you measure internal threads?
To identify an inside thread (such as a filter ring on a lens), first take your best guess from age and origin to determine if its a metric thread then measure the diameter of the female (inside) thread. Take (The “Minor Diameter”) then add the pitch number to the measurement.
What is used for the inspection of external thread in a job?
Micrometer Measuring Wires
Another common thread measurement method is a hand-held 3-wire measuring system, which works by placing three wires of known thickness into the screw heads, and a micrometer measures the protruding wires.
Which of the following is a thread ring gage used to check?
A thread plug gage is designed to check the pitch diameter (to the given pitch / Threads per inch). In order for the part to pass inspection and be accepted, the GO gage should pass through the entire length of the nut, without requiring the use of too much rotational force.
What is thread execution?
In computer science, a thread of execution is the smallest sequence of programmed instructions that can be managed independently by a scheduler, which is typically a part of the operating system.
Which type of inspection device can check the pitch diameter of an external thread?
The ball pitch diameter gages or “GO/NO GO” gages indicate the pitch diameter size of the product’s external thread. The gages are adjustable within a size range and use interchangeable contact points to measure different pitch threads.
Tri-Roll Thread Comparator Systems
Tri-Roll Thread Comparator Systems provide variable thread measurement as well as indicating whether a threaded part is within the specified limits. Rigid construction and constant gage pressure assure consistent and precise readings Both the Tri-Roll and ITC thread comparators are able to inspect a wide range of parts with a single frame.
Tri Roll Thread Comparators
Thread Check, Inc. offers an extensive range of Tri Roll Thread Comparators. Tri Roll Thread Comparators provide actual thread measurements of dimensional characteristics for quicker machine adjustments during thread production. The Tri Roll System measures the exact position of the pitch diameter within the tolerance range. It also checks size and out of roundness of plain cylindrical parts. The Tri Roll reduces gaging time over thread ring gages. One single gage can be used to inspect pre-plate, after- plate, class 1, 1A, 2, 2A, 3, and 3A eliminating the need for multiple fixed limit thread ring gages. The rigid construction and constant measuring pressure of our tri-roll thread comparators provide consistent and accurate readings. Fixed mounting of the lower rolls assures a solid support for the work piece. Only the upper roll actuates the indicator thereby providing repeatable readings. The instrument is easy to set as no adjustment of the lower rolls is required when changing from one thread size to another. The variable gaging system provides longer life of the tooling and thus reduces costs. Thread Check’s Tri Roll Thread Comparators comply with system 21, system 21A, and system 22. Click here for Tri Roll Thread Comparator Instructions.
ITC – Internal Thread Comparator
Thread Check, Inc. offers the ITC – Internal Thread Comparators to provide actual thread measurement of dimensional characteristics for quicker machine adjustments and reduced gaging time over thread plug gages. One single gage can be used to check pre-plate, after-plate, class 2, 2B, 3, and 3B eliminating the need for multiple fixed limit thread plug gages. A single frame covers a size range from #10 through 2 ½ in diameter. Larger frames are available up to 8.0″. The rigid construction and constant measuring pressure of our ITC comparators provide consistent and accurate readings. Thread Check’s Internal Thread Comparators comply with system 21, system 21A, and system 22. Click here for Internal Thread Comparator Instructions.
Master Setting Plugs For Tri Roll Thread Comparators
Class “W” Full Form Master Setting Plugs gages are used to set Tri Roll Thread Comparators. Master Thread Setting plugs are manufactured to a go basic pitch diameter size. PITCH DIAMETER is the theoretical diametrical plane which passes through a thread at the point where the width of the thread tooth and groove are equal. The pitch diameter is measured by means of the universally recognized three wire method.
Master Setting Rings For ITC-Internal Thread Comparators
Class W tolerance master setting ring gages are used to set ITC – Internal Thread Comparators. Class W tolerance master setting ring gages are manufactured to a go basic functional diameter. FUNCTIONAL DIAMETER is the actual (measured) pitch diameter of a thread adjusted by the cumulative effects of lead error and angle error, which is always added to external threads and subtracted from internal threads.
Thread Inspection 101 Part I – Thread Gage Basics
This is Part I of our Thread Inspection 101 series.
Let’s all take a moment to be honest with ourselves. How many of you, just like myself, assumed (or still do) that a bolt is just a bolt? Or a screw is just a screw? Or a nut is just a nut? I mean, it’s pretty easy stuff, right? After all, you can buy a pack of 10 for a buck at your local hardware store. Who knew that there was an entire world of tooling out there dedicated to measuring these mundane pieces of metal? However, when you start to drill down into it, you will find thread measurement is actually a highly complex (and fascinating) world.
In fact, it is safe to say, that threads are the nuts and bolts of the manufacturing world…(sorry, I had to).
In all seriousness, threading is what holds together (quite literally) the entire industry. A significant majority of machined components that must be fastened to other machined components are done so via threading.
As such, it goes without stating that the importance of having accurately produced threads is incredibly high. In order to live up to the designed specifications, it is important that each thread bears an equal amount of the load. If there is an imperfection in the manufacture of either the male or female component’s threads, the load of this system will be imbalanced, causing a particular portion of the threads to bear more than its fair share of weight. As you can imagine, this can have catastrophic results.
As this relates to inspection and quality, you can see that accurately measuring threaded components is integral to the acceptance of a product.
Threading Inspection Basics
It is important to first understand the two basic types of threaded components out there:
Internal threads External threads
In general, if you are joining two parts via threading, there are going to be two types of threads. The first is the male end which will of course screw into the female end. In an obvious example of a nut and a bolt, the bolt is the male end and the nut is the female end. As such, the nut contains threads on the inside, making it an internal thread and the bolt has the threads on the outside, making it an external thread. Of course, this example extends well past nuts and bolts, but you get the idea.
Obviously, in order for that nut and bolt to fit together they must be machined to the exact same size. The problem is this is much more complex than just drilling a hole and making sure a rod is small enough to go through it. The overall diameter of the external threads must match the smallest diameter of the internal threads, the quantity of threads in a given length must match, the pitch of the threads must match, and the list goes on and on and on (we will get into a discussion of thread attributes in a later post).
As you can see, the geometrical measurements required to inspect a threaded part would take hours to measure just one piece. This is just not a practical solution to inspecting these parts.
The good news is, there is a very easy solution that delivers excellent results. Thread gaging.
Thread Gaging Basics
Since, as we discussed above, there are two main types of threading (internal and external), it makes logical sense that we would need one type of thread gage to measure each part. As such, there are two main types of thread gaging:
Thread plugs Thread rings
Thread Plugs
Thread plugs are exactly as they sound. They are plugs that contain external threading on them and are used for checking internal threaded components (i.e. nuts).
Thread Rings
Thread rings are, of course the exact opposite of that. They are the rings that contain internal thread on them and are used for checking external threaded components (i.e. bolts).
Both thread plugs and thread rings are typically machined from aged gage steel that offers exceptional resistance to common wear.
But how do they actually measure a threaded component?
Thread Gaging Inspection Basics
All thread gages are classified as an attribute gage, meaning they do not provide feedback on what the exact size of the dimension is. This is in stark contrast to a quantitative measurement that, say, a caliper would give in which it reads out the exact dimension you are measuring.
Thread gages accomplish this in what is called a Go/No-Go measurement.
To better understand this, let’s look at a typical thread plug. A common thread plug assembly (more on this later) will contain a handle with two ends, one on either side.
To inspect an internal thread, both ends of the thread plug are inserted into the threaded component. The Go end of the plug is supposed to thread in; the No-Go end is not. If this test checks out, the part can pass inspection. However, if the Go end does not go in, it can be deduced that the threaded component was machined too small. Subsequently, if the No-Go end does thread into the part, the threaded component was machined too large.
A thread ring works on the exact same principle, just in reverse. The rings are manufactured in a set, where the Go ring is machined to a slightly smaller size than the nominal and the No-Go ring is machined to a slightly larger size than the nominal. As such, the Go ring should thread onto the machined component and the No-Go ring should not.
It really is that simple.
You can see the logical advantage this type of measurement over having to find an exact dimension of every attribute. This Go/No-Go measurement is incredibly quick (a matter of seconds) and still very accurate.
It is because of this incredibly speedy check that thread plugs and thread rings are some of the most common gages in the entire manufacturing industry. They can be found at nearly every machining center where threaded components are being produced.
This is Part I of our Thread Inspection 101 Series. In our subsequent posts, we will dive into the sizing of thread gages as well as explore the intricacies of the thread gaging world.
Interested in purchasing a thread gage? Please submit a request today.
Tri Roll Comparators & Thread Gage
SYSTEM 21
System 21 provides for interchangeable assembly with respect to functional size only. Functional size must be measured at the maximum material limit within the length of standard gaging elements. The characteristic known as NO GO functional diameter must also be verified. This can be accomplished by using fixed limit gaging or variable gaging with functional elements.
SYSTEM 21A (FOR METRIC THREADS IN ACCORDANCE WITH ANSI B1.18M)
System 21A provides for interchangeable assembly with functional size verified at the maximum material limit using standard length gaging elements. This can be accomplished using fixed limit gaging or variable gaging with functional elements. System 21A also states that the minimum material limit (minimum pitch diameter) must be verified by inspecting two thread flank locations over the length of the thread. This can be accomplished by using variable gaging or thread roll snap gages with pitch diameter elements.
SYSTEM 22
System 22 provides for the interchangeable assembly with functional size verified at the maximum material limit using standard length gaging elements. This can be accomplished using fixed limit gaging or variable gaging with functional diameter elements. System 22 also states that the minimum material limit (minimum pitch diameter) must be verified over the full length of the thread. This can be accomplished using variable gaging with pitch diameter elements.
SYSTEM 23
Glastonbury Southern Gage Tri-Roll Thread Comparator Variable Thread Gages – Willrich
SYSTEM 21
System 21 provides for interchangeable assembly with respect to functional size only. Functional size must be measured at the maximum material limit within the length of standard gaging elements. The characteristic known as NO GO functional diameter must also be verified. This can be accomplished by using fixed limit gaging or variable gaging with functional elements.
SYSTEM 21A (FOR METRIC THREADS IN ACCORDANCE WITH ANSI B1.18M)
System 21A provides for interchangeable assembly with functional size verified at the maximum material limit using standard length gaging elements. This can be accomplished using fixed limit gaging or variable gaging with functional elements. System 21A also states that the minimum material limit (minimum pitch diameter) must be verified by inspecting two thread flank locations over the length of the thread. This can be accomplished by using variable gaging or thread roll snap gages with pitch diameter elements.
SYSTEM 22
System 22 provides for the interchangeable assembly with functional size verified at the maximum material limit using standard length gaging elements. This can be accomplished using fixed limit gaging or variable gaging with functional diameter elements. System 22 also states that the minimum material limit (minimum pitch diameter) must be verified over the full length of the thread. This can be accomplished using variable gaging with pitch diameter elements.
SYSTEM 23
System 23 provides for interchangeable assembly with functional size verified at the maximum material limit using standard length gaging elements and minimum material limit (minimum pitch diameter) must be verified over the full length of the thread. The gaging requirements for SYSTEM 22 would also apply here but in SYSTEM 23 other thread characteristics such as lead, flank angles, taper and roundness must have to be independently verified. Only thread characteristics, which are specified, will have to be inspected for SYSTEM 23 compliance.
Tri-Roll Comparator Bases & Accessories
SYSTEM 21
This system provides for interchangeable assembly with respect to functional size only. The functional size must be measured at the maximum material limit within the length of standard gaging elements. The characteristic known as NO GO functional diameter must also be verified. This is accomplished by using fixed limit gaging or variable gaging with functional elements.
SYSTEM 21A (FOR METRIC THREADS IN ACCORDANCE WITH ANSI B1.18M)
This system provides for interchangeable assembly with functional size verified at the maximum material limit using standard length gaging elements. This can be accomplished by using fixed limit gaging or variable gaging with functional elements. System 21A also states that the minimum material limit (minimum pitch diameter) must be verified by inspecting two thread flank locations over the length of the thread. This can be accomplished by using variable gaging or thread roll snap gages with pitch diameter elements.
SYSTEM 22
This system provides for the interchangeable assembly with functional size verified at the maximum material limit using standard length gaging elements. This can be accomplished using fixed limit gaging or variable gaging with functional diameter elements. System 22 also states that the minimum material limit (minimum pitch diameter) must be verified over the full length of the thread. This can be accomplished using variable gaging with pitch diameter elements.
This system provides for interchangeable assembly with functional size verified at the maximum material limit using standard length gaging elements and minimum material limit (minimum pitch diameter) must be verified over the full length of the thread. The gaging requirements for SYSTEM 22 would also apply here but in SYSTEM 23 other thread characteristics such as lead, flank angles, taper and roundness must have to be independently verified. Only thread characteristics, which are specified, will have to be inspected for SYSTEM 23 compliance.
Universal Concentricity Gage » Universal External Tri-Roll Gages
Tri-Roll Variable Reading Thread Gages
ADJUSTABLE 3-POINT GAGE FRAME – Has a self-contained alignment system that eliminates the need for setting templates or micrometers to achieve perfect 120° spacing. The frame design re-duces the inspection space and additional expense normally required by other systems using numerous gage frames for different sizes.
GAGE RANGE – The 3-POINT™ Thread System covers a size range from #4 (3mm) to 1-1/2” (40mm) with two adjustable frames.
GAGE PERFORMANCE – The gage roll sets are easily changed from one size to another. The lower rolls are mounted in a fixed position to support the workpiece. The upper roll arm assembly exerts a consistent force and actuates the indicator providing ac-curate readings.
GAGE DURABILITY – Thread rolls are designed to revolve with the workpiece, distributing wear evenly. (OptionaL) TITANIUM-NI-TRIDE (TiN) coatings protects the gage roll surface and provides additional hardness that extends gage roll life.
SPC COMPATIBLE – Universal gages provide the ideal system for data collection. Adjustments can be made at the machine before scrap is created, resulting in improved productivity and quality.
External Tri-Rolls
BEST WIRE ROLLS- Pitch Diameter (Minimum Material condition) FULL FORM ROLLS- Functional Diameter (Maximum Material condition) PLAIN ROLLS- Major Diameter (Multi lobe out-of- roundness) CONE & VEE ROLLS- Single Element Pitch Diameter Flank contact limited MINOR DIAMETER ROLLS- (55° included angle) Two full profile “vee” rolls and one full profile cone roll
GAGE TRI-ROLLS There are interchangeable gage rolls available for standard thread gaging
applications. Each set of 3 rolls corresponds to one particular thread size. For measuring Pitch Diameter
use best wire rolls. For measuring Functional Size use full form rolls. For measuring Major Diameter use
plain rolls. For measuring Minor Diameter (not shown) use included angle rolls. Special thread rolls are
priced on request.
External 2-Point Thread Gages
2-POINT THREAD GAGE– Utilizes the most advanced precision linear bearings system. Accurate linear movement and consistent gaging force assures repeatable readings throughout the measuring range. Universal’s 180° frame design provides the best method for gaging functional size and other thread geometry. Helical path seating and 60% peripheral contact provide functional size position within the pitch diameter tolerance assigned.
GAGE RANGE – The 2-POINT gages cover a size range from #4 (3mm) to 3/4” (20mm) or 13/16” (22mm) to 1-1/2” (40mm).
GAGE PERFORMANCE – The external thread gages are easily set-up to use. With an appropriate thread setting plug gage, adjustment can be made quickly in setting the indicator to the actual size of the master, greatly reducing inspection time.
GAGE DURABILITY – The external 2-POINTTM thread gages are constructed to provide a consistent
gaging force for repeatable readings. The frame offers positive alignment that gives the flexibility to measure parts at the machine.
UNAMBIGUOUS READINGS – A consistent and precise reading eliminates opinion and operator variability. With a master thread plug gage, setting adjustments are made in seconds allowing actual size to be “seen” as opposed to the operator “feel” necessary with GO NO/GO ring gaging.
External Segments
BLADE SEGMENTS- Minor Diameter & Taper (Minimum Material Condition) FULL FORM SEGMENTS- Functional Diameter (Maximum Material Condition) FLAT SEGMENTS- Major Diameter (Multi Lobe Out-Of-Roundness)
GAGING SEGMENTS – There are various interchangeable gaging segments available for standard and special threads. Thread gage segments are (Optional) TITANIUM-NITRIDE (TiN) coated for maximum wear. This coating provides additional hardness to the surfaces and visual indication of the need for replacement. Special thread segments are priced on request.
Master Setting Thread Plug Gages
SETTING THREAD PLUG GAGES – Universal Master Setting Thread Gages provide a traceable means to set and maintain the Variable Reading Thread Gaging System. Each thread size requires a Master Setting Thread Gage to establish a calibrated position before measuring a product. These masters are certified To N.I.S.T standards.
GSG – Tri-Roll External Thread Gage Frames
Features:
• Precision
Rigid construction and constant gage Rigid construction and constant gage
pressure guarantee consistent and precise read- pressure guarantee consistent and precise readings.
• Qualitative Readings
The Tri The Tri-Roll not only indicates whether a Roll not only indicates whether a
threaded part is within assigned limits, it also threaded part is within assigned limits, it also
shows the exact position of the pitch diameter shows the exact position of the pitch diameter
within a tolerance range. In addition, the Tri within a tolerance range. In addition, the Tri-Roll
will check size and out of roundness of plain cylin- will check size and out of roundness of plain cylindrical parts. drical parts.
• Repeatability Repeatability
Fixed mounting of the lower rolls assures Fixed mounting of the lower rolls assures
a solid support for the work piece. Only the upper a solid support for the work piece. Only the upper
roll actuates the indicator, thereby providing re- roll actuates the indicator, thereby providing repeatable readings. peatable readings.
• Easy to Set Easy to Set
No adjustment required on the lower rolls No adjustment required on the lower rolls
means that no adjustment is required when change- means that no adjustment is required when changing from one thread size to another. ing from one thread size to another.
• Wide Gaging Range
Both the ITC and the Tri Both the ITC and the Tri-Roll are able to Roll are able to
inspect a wide range of parts with a single frame. inspect a wide range of parts with a single frame.
• Adaptability Adaptability
The variable thread system can be used The variable thread system can be used
to measure plain diameters and can be used with to measure plain diameters and can be used with
the “Zero Spindle “ gage system. the “Zero Spindle “ gage system.
• Economical with Long Work Life
The variable thread gage system provides The variable thread gage system provides
longer life of the tooling and thus reduces cost longer life of the tooling and thus reduces cost.
Zero System Variable Gages Zero System Variable Gages are available for external and internal thread applications. The external thread application are lications. The external thread application are covered by the segment and Tri covered by the segment and Tri-Roll units and the internal applications by the ITC unit. Roll units and the internal applications by the ITC unit.
키워드에 대한 정보 tri roll thread gage
다음은 Bing에서 tri roll thread gage 주제에 대한 검색 결과입니다. 필요한 경우 더 읽을 수 있습니다.
이 기사는 인터넷의 다양한 출처에서 편집되었습니다. 이 기사가 유용했기를 바랍니다. 이 기사가 유용하다고 생각되면 공유하십시오. 매우 감사합니다!
사람들이 주제에 대해 자주 검색하는 키워드 Tri-roll Gage: External Thread Measurements
- Larry Borowski
- Greenslade and Company
- Tri-Roll Gage
- Fastener
- External Thread Measurments
- Threads
- Measuring
- Gages
- Rolls
- Tutorial
Tri-roll #Gage: #External #Thread #Measurements
YouTube에서 tri roll thread gage 주제의 다른 동영상 보기
주제에 대한 기사를 시청해 주셔서 감사합니다 Tri-roll Gage: External Thread Measurements | tri roll thread gage, 이 기사가 유용하다고 생각되면 공유하십시오, 매우 감사합니다.